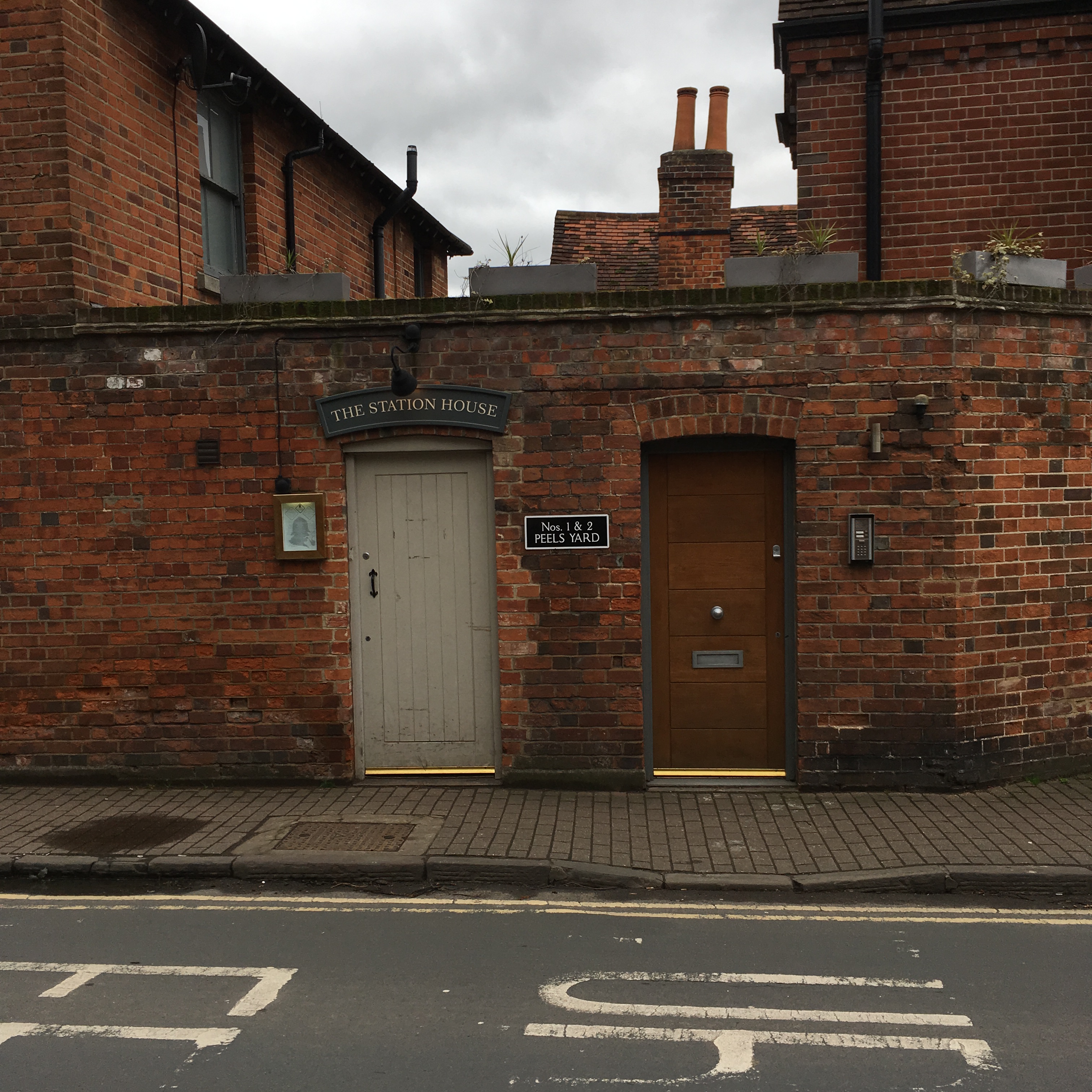
Job Centres were government-operated employment agencies intended to help people find gainful work instead of spending their days watching telly while sponging off the dole. At least, such was the image of their unemployed compatriots entertained by many supporters of Margaret Thatcher, prime minister at the time. Her cabinet ministers (well, some of them) were less dismissive regarding the plight of their jobless constituents. There were jobs out there, they insisted; you just had to put some effort into finding one. “Get on your bike” became an oft-heard exhortation after Norman Tebbit, Secretary of State for Employment, told attendees at the Conservative Party Conference in 1981 that he’d grown up in the 1930s with an unemployed father. “He didn’t riot,” Tebbit said; “he got on his bike and looked for work and he kept looking ‘til he found it.”
The Job Centre certainly made it more convenient to find employment. But I would have found a job with or without it. I was raised by parents who, despite the haziness of their hippie years, impressed on me the importance of hard work and self-reliance. At the same time, they also supported the provision of social services and safety nets, knowing that things can go wrong for anyone, despite diligent work and the best-laid plans.
My friend Beatrice, on the other hand, had graduated from Cambridge with a degree in drama. Finding herself unable to secure paid employment in her field, she didn’t hesitate to sign up for the dole. “But surely you could get a job at a sandwich shop, or cleaning houses?” I offered, shocked that this bright, resourceful, relatively well-off friend had sought government assistance.
“If I take a job unrelated to my area of expertise it will count against me the next time I apply at a theatre,” she explained over Lapsang Souchong in her cozy London flat. Seeing my stunned expression, she added that taking just any job “would suggest that I’m not serious about my profession.”–Excerpted from Making Things Work by Nancy Hiller