This is an excerpt from “By Hand and Eye” by Geo. R. Walker and Jim Tolpin.
“[Architectural ornamentation] liberates us from the tyranny of the useful and satisfies our need for harmony.” — Roger Scruton
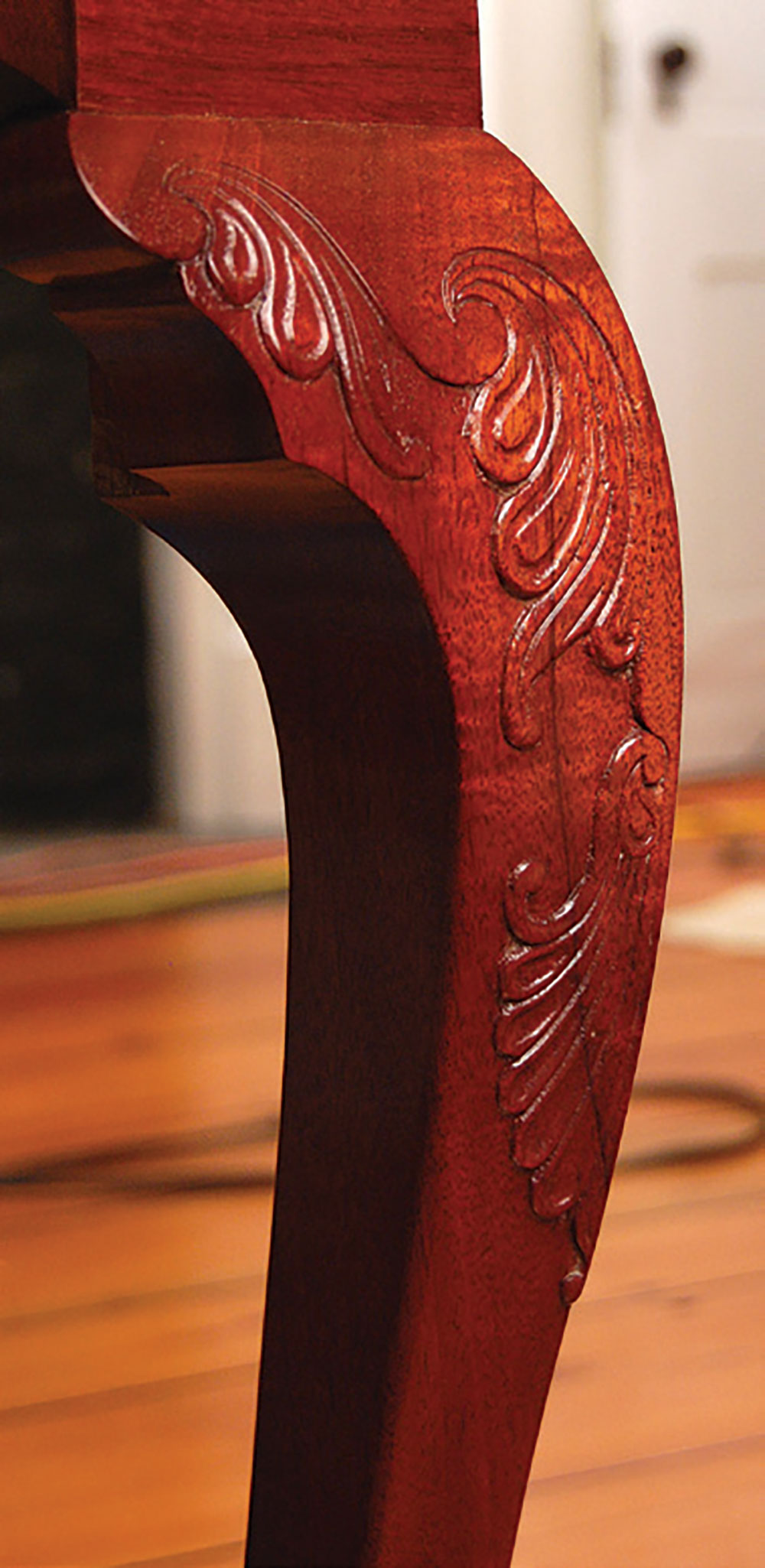
carving on this table
leg accomplishes
several things at once.
It highlights the form,
provides interest for a
close view and emphasizes
this object’s
place of importance in
the life of a home.
Traditionally, ornament and mouldings were employed to punctuate and emphasize a form. Even though they’ve been overdone, it doesn’t mean they don’t have a valid place. Our woodworking design tradition has seen wide swings in taste concerning ornament, embellishment and mouldings. Some periods drip with overcooked gingerbread, some scrape clean down to the bone. A few contemporary designers even abhor figured wood, and some modernist designers dictated that ornament should be allowed only if it looked machine made – no hints of man’s hand. It’s difficult today, with the pendulum swung away from traditional ornament, to see how it was originally viewed, especially when bursts of excess litter our furniture history. It might be helpful to understand the original craft intent and not simply write off traditional ornament and mouldings as a relic of another era. Ornament must complete a design – similar to the effect of leaves on a tree or feathers on a bird. It’s not an add-on, it’s not a strategy to rescue an inferior design. Abraham Swan (circa 1757) wrote, “If the original design be bad, superadded ornaments will make the whole appear like a clown in a laced waistcoat.”
The bones underneath must be good or ornament will only make the whole design worse. That’s the reason so much mass-produced 20th-century Colonial-style furniture fails so pointedly.
Ornament and mouldings must have a function. While we think today of function as primarily a structural element (a way to meet a physical requirement), the craft idea of function was much broader, because the definition of function included visual appearance. Mouldings or other ornaments were used to emphasize a form, create a visual border, transition one part to the next or to create layers of interest on different scales (such as a close view). Another function of ornament is to set something apart. As reflected in Swan’s quotation above, this human need to embellish what we value is the reason that even our ancestors of modest means felt compelled to use ornament to decorate a powder horn, dowry chest or quilt. The question to ask is not whether the ornament or moulding adds to the design, but whether the design lacks something without it.
— Meghan B.