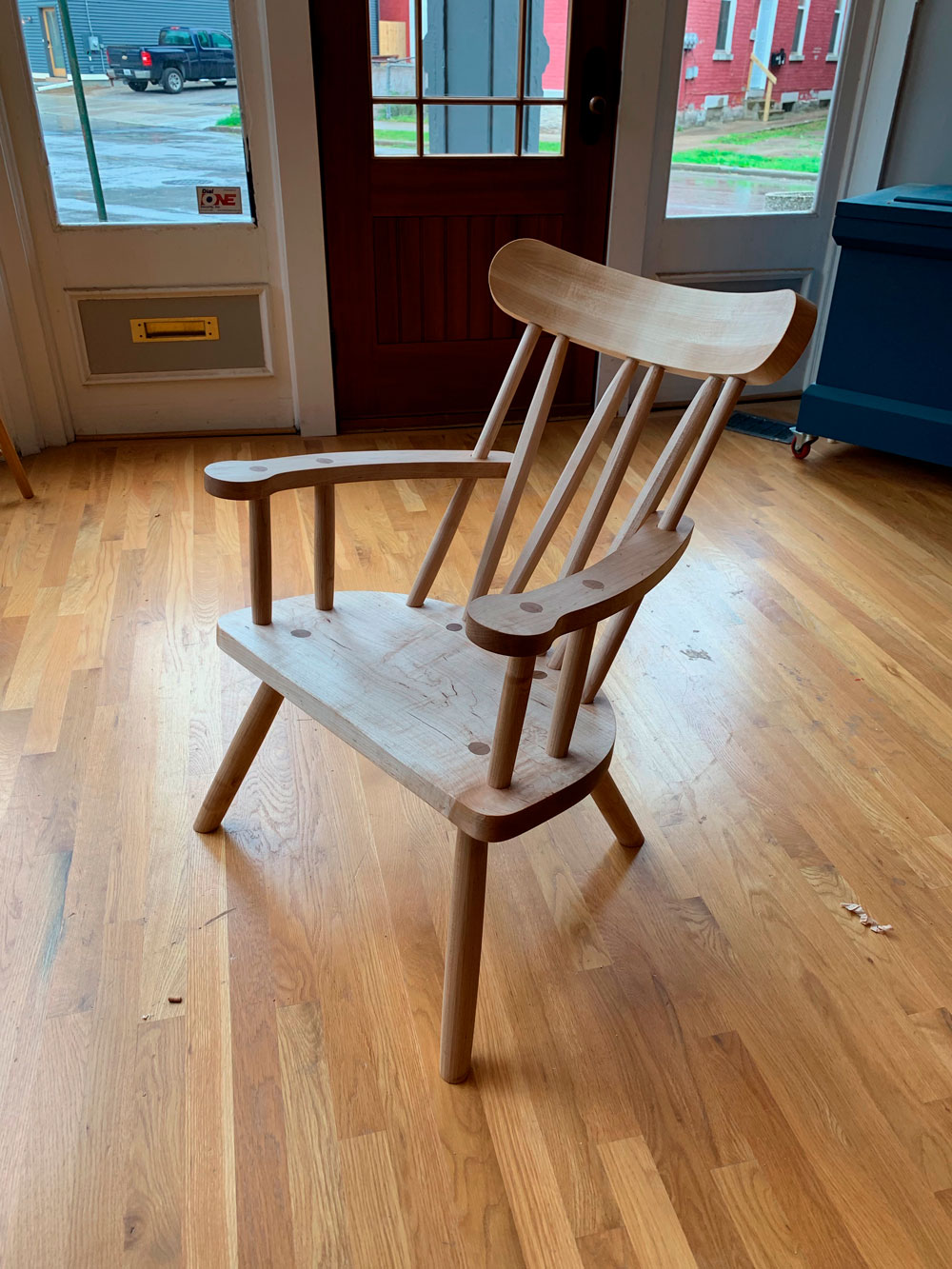
When I make things for sale – chairs, hammers, tool chests, workbenches, whatever – I struggle with when to let the things go out of my hands and into the world.
Sometimes I think I have two choices:
- Perfection first. I first need to get all the details perfect no matter how long it takes. Then I’m going to get faster and faster at it.
- Speed first. I need to get this project done so it makes money and is acceptable to a customer. Then I’ll achieve perfection as I get better and better at it.
I’ve found the truth is something entirely different. When I make an object for the first time or the 10th time, getting it “just right” is impossible because I have no conception of how good the thing can become in the end.
For example, when I started making lump hammers in our shop, I made them slowly and to what I thought was a high standard. The problem was that my eyes couldn’t conceive of what a really good hammer looked like. So my first hammers were made slowly and weren’t anything like they look like today – to my eye. (Note: Even my early ones were good. I’m not asking to be swamped with returns.)
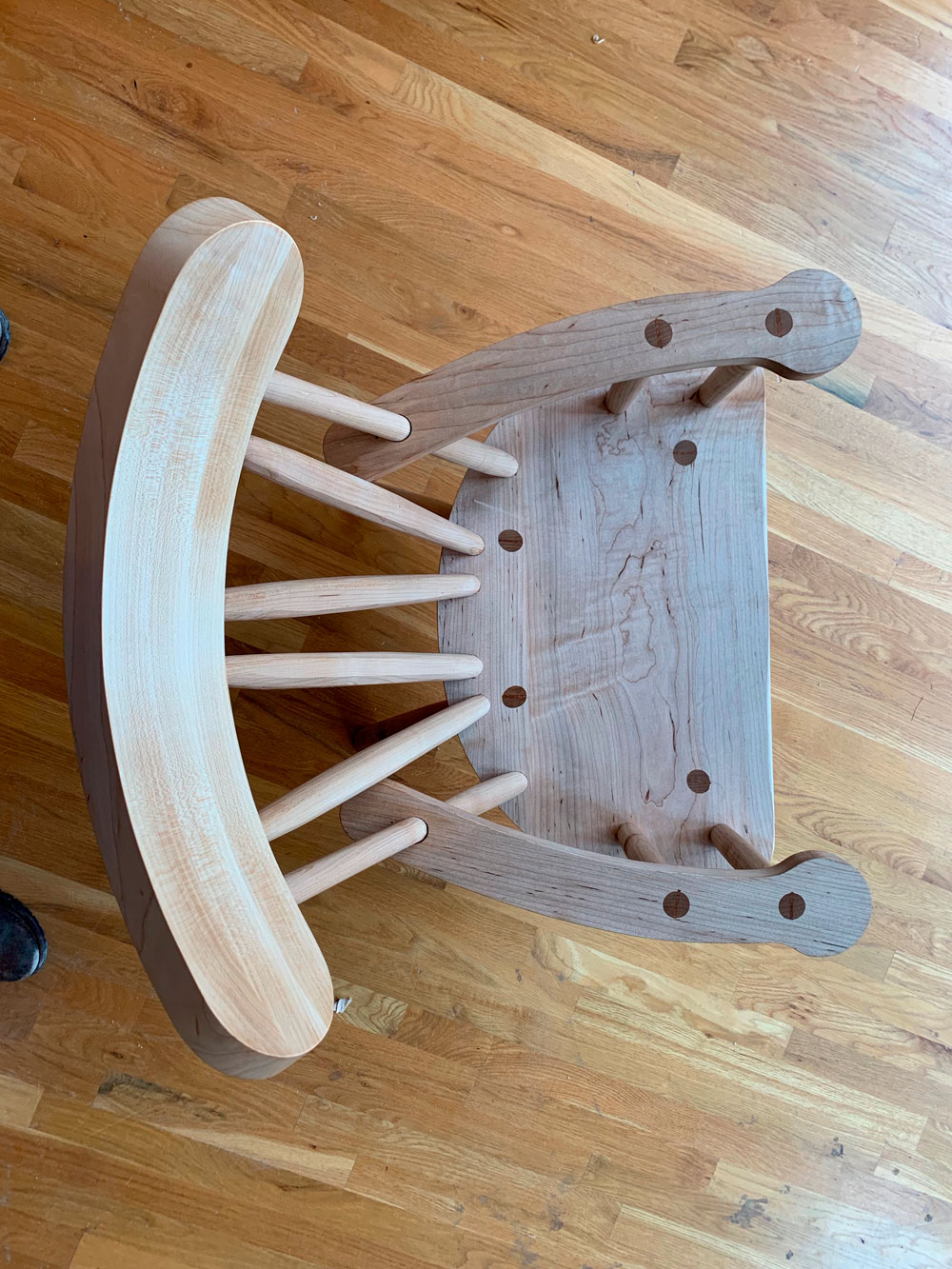
Same with chairs. When I invited Peter Galbert over for dinner one night I had to look him in the eye and say: I can afford to own only my early and prototype chairs. These things horrify me. Please don’t judge me by them. He smiled broadly and nodded. (I know in my heart he was judging me.)
I’ve concluded that speed and quality are not mutually exclusive. You don’t have to choose one over the other. Instead, I start with neither and end up with both. It just takes time at the bench, the lathe or the belt grinder.
This week I have this Irish chair prototype (above) sitting around the shop while Chris Williams teaches two classes stocked with experienced chairmakers. I honestly wanted to hide the chair somewhere. It’s a mess. But Lucy and I are moving house right now and there is no place to stash it.
Though it pains me to look at the chair, its presence also forces me to see it and develop an eye for what it can become. And that’s the first step to getting it right.
— Christopher Schwarz
Like this:
Like Loading...