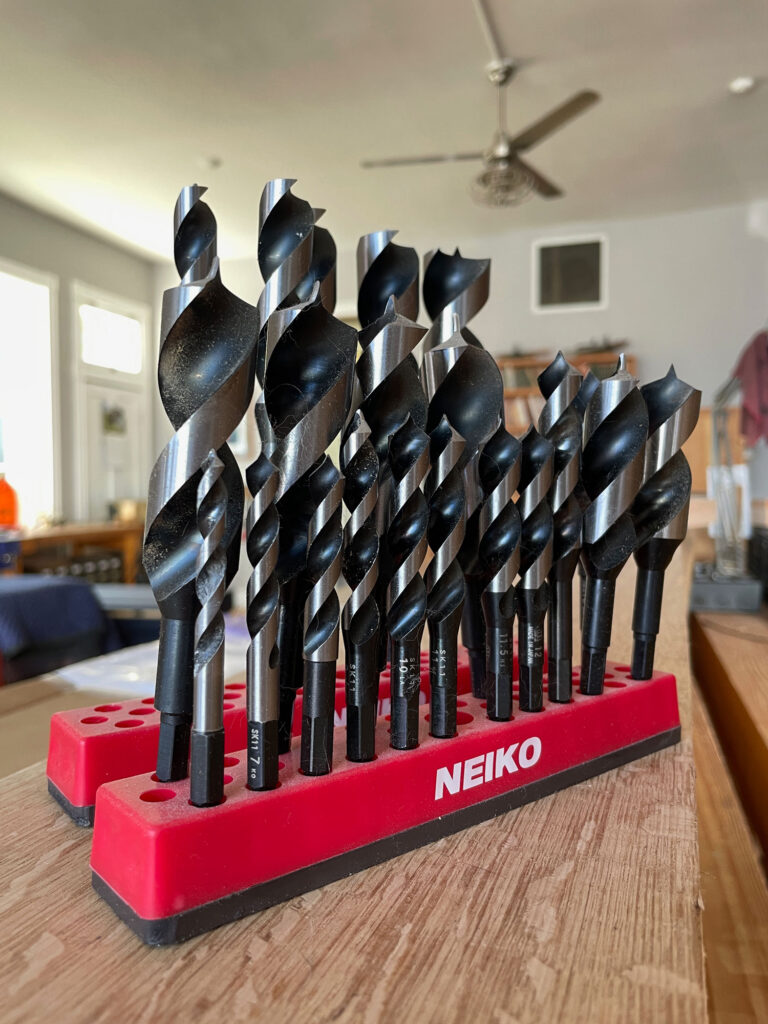
I’m always looking for better drill bits because my work involves making a lot of holes. My dream bit would make a clean hole (entry, exit and every surface in between), it wouldn’t clog and it would make a hole that is the exact dimension stamped on its shaft.
In my experience, you can only get two of those three characteristics in a drill bit.
The WoodOwl Overdrive bits are likely the best bits I’ve encountered so far. They aren’t perfect, but they come closer than any other bit I’ve encountered. Here are some details.
Hole cleanliness: The Overdrives are as good as I’ve seen. The bits cut rapidly and leave a clean hole – even if the exit hole isn’t backed up with a sacrificial board.
Bit cleanliness: The Overdrives don’t clog. They have large flutes that pull the waste away rapidly. And waste doesn’t get packed into the flutes like on some other augers.
Accuracy: Here is where the bits fail me a bit. When used in a handheld drill, the flutes of the bit can cut the round hole into an oval. This is, of course, user error – I moved the drill. But the Overdrives have very sharp flutes, and it can be difficult to avoid making the hole a little bit oval-shaped.
This isn’t a big deal in many applications. In fact, most woodworkers won’t notice it. But if you drill an oval through-mortise and have a round tenon, the error will show.
But other than that detail, I love them. The Japanese-made bits have the added benefit of having a hex shank, so they won’t spin and gall in your drill’s chuck. And they are remarkably inexpensive for what you get. They are outstanding bits for your drill press.
If you live in the U.K., get the Star-M F-Type bits (they’re made by the same manufacturer). They have a little different bit geometry, but that have all the same excellent characteristics of the Overdrives.
— Christopher Schwarz
Read other entries from The Anarchist’s Gift Guide here.