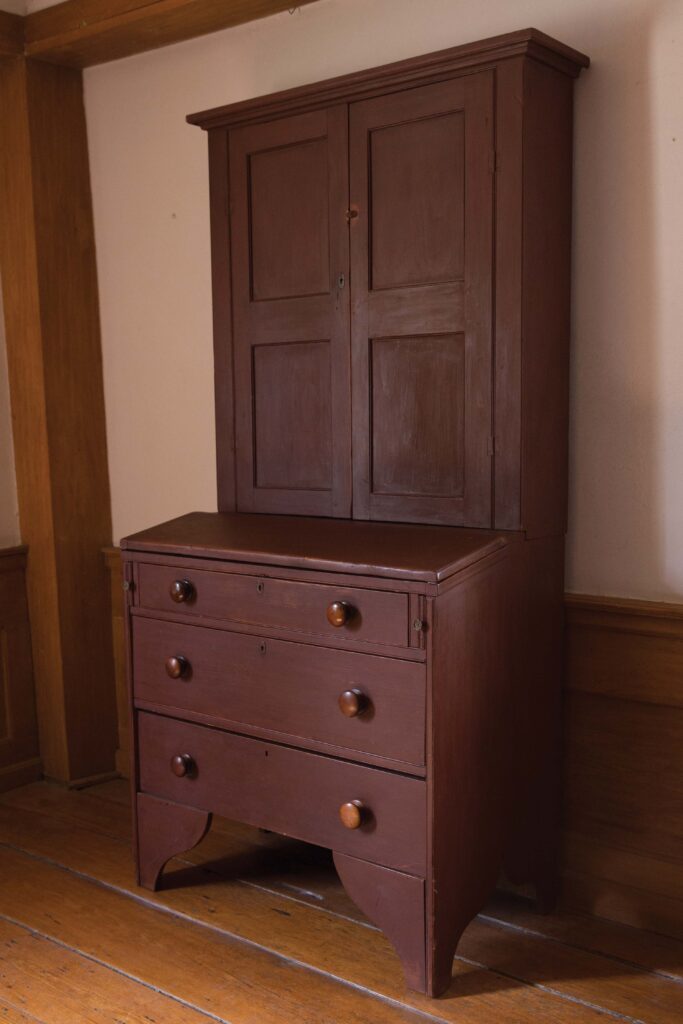
The following is excerpted from “Hands Employed Aright: The Furniture Making of Jonathan Fisher (1768-1847),” by Joshua A. Klein.
Jonathan Fisher (1768-1847) was the first settled minister of the frontier town of Blue Hill, Maine. Harvard-educated and handy with an axe, Fisher spent his adult life building furniture for his community. Fortunately for us, Fisher recorded every aspect of his life as a woodworker and minister on the frontier.
In this book, Klein, the founder of Mortise & Tenon Magazine, examines what might be the most complete record of the life of an early 19th-century American craftsman. Using Fisher’s papers, his tools and the surviving furniture, Klein paints a picture of a man of remarkable mechanical genius, seemingly boundless energy and the deepest devotion. It is a portrait that is at times both familiar and completely alien to a modern reader – and one that will likely change your view of furniture making in the early days of the United States.
The value of a minister’s library was substantial and, therefore, the fact that Fisher invested time in the construction of a desk and bookcase is not surprising. One biographer calculated that Fisher owned approximately 300 books, describing it as “not an inconsiderable store for a poor minister in a small village.” That Fisher valued reading is even seen in the plans for his house in which one of only two items of furniture depicted was a bookcase in the kitchen.
Though Fisher’s desk and bookcase is not explicitly mentioned in the surviving journal entries, attribution can be confidently made based on provenance, numerous construction features and the homemade wooden lock on the door.
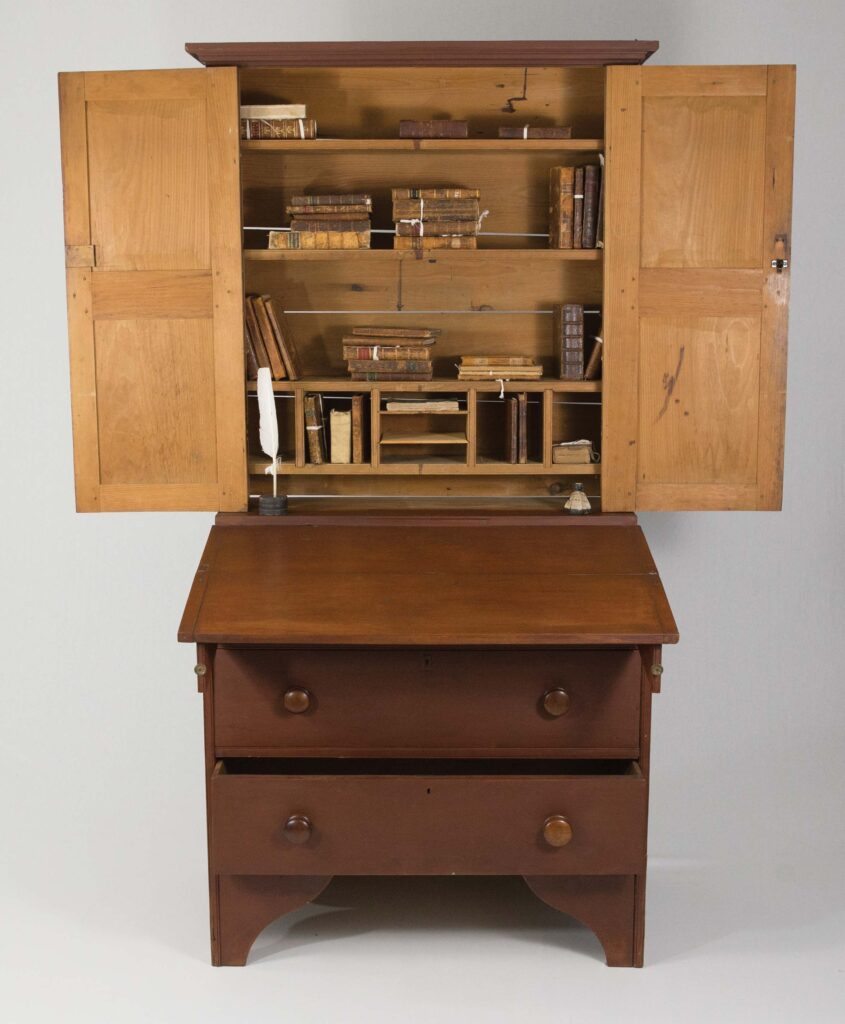
The desk is constructed of pine and was painted (although the current paint is modern). The desk has three drawers and downward-extending lopers that provide a slanted writing surface. At the top of the writing surface, there is a small secret compartment with a sliding-dovetail lid for valuables. The bookcase has both full-length shelves as well as small compartments for letters, etc. The panel doors lap with a beveled edge when closed, and a homemade wooden lock secures the minister’s library from tampering. Despite the fact that the lock operated with a key that is now missing, there is an identical lock on the door to his clock face that still functions, operating by turning a knob. Fisher made many wooden latches in his house, all of which are fascinating, but these locks are particularly delightful. They are easy to overlook by assuming that they are the same metal locks Fisher might have purchased from Mr. Witham’s store at the head of the bay, but they are clearly Fisher-made and completely made of wood. Their delicateness and smoothness of operation add a touch of sophistication to an otherwise unassuming piece of furniture.
Fisher’s work has been sometimes compared to that of the Shakers because of its simplicity and conscious restraint. While the overall association stands, it is significant to point out that the primary difference between Fisher and the Shakers is their view of ornamentation. While classic Shaker work has little to no moulding, Fisher relished elaborate profiles. The cornice of this desk (as well as that of his wardrobe) sat like a crown over Fisher as he studied. His artistic vision of furniture design, though similar to the Shakers’ in its modesty, was less inhibited. Even as a young child, his mother, Katherine, taught him to value artistic expression. Katherine, whose drawings look so much like her son’s, saw a world in which chastity and artistic beauty were not mutually exclusive. Fisher was not afraid of flourish.
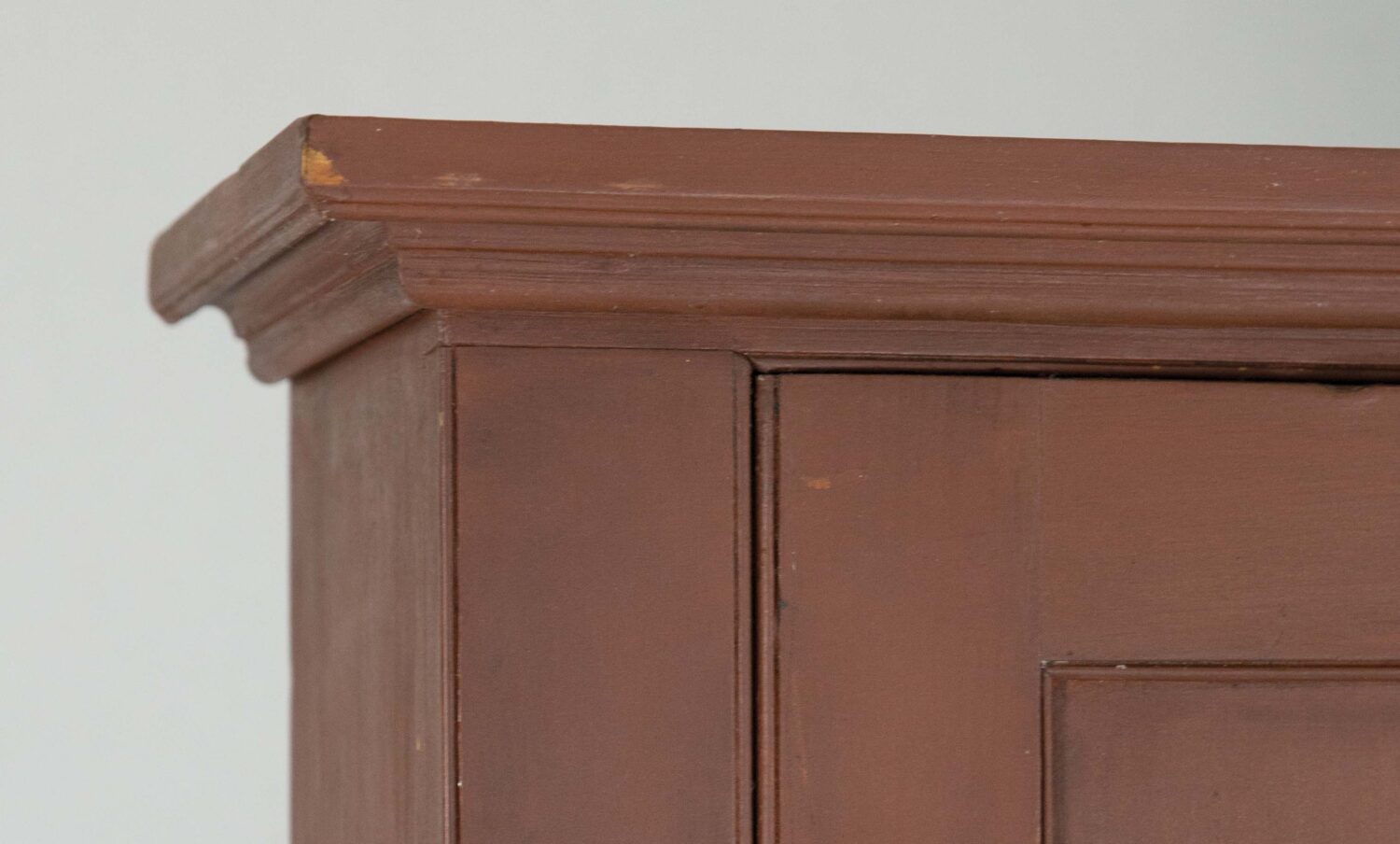
His work fits much more squarely in the Federal vernacular classification than that of the Shakers.
The desk carcase is interesting in that it is constructed like a six-board chest, with the sides extending to the floor with bootjack feet. The dados are a scant 3⁄4″ wide, matching his surviving dado plane. The backboards are unplaned, rough-sawn boards nailed into rabbets in the sides. The drawers (with the exception of the bottom one, which is a replacement) are of conventional dovetail construction – half-blind dovetails at the front, and through-dovetails at the back. The drawers’ bottoms are beveled and fitted into grooves in the sides and front, and are nailed to the drawer backs.
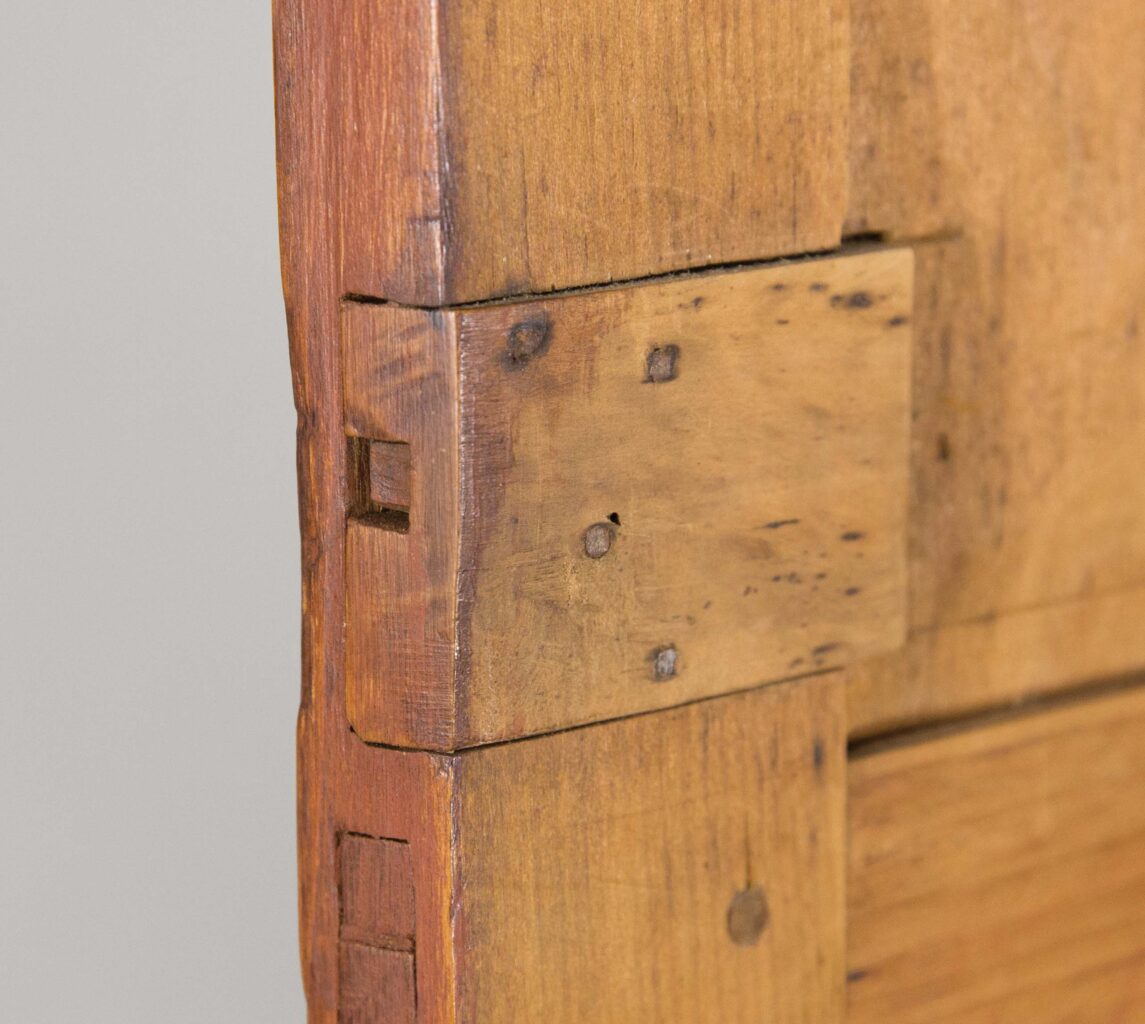
The overall composition of this piece illustrates the minister’s education. Even this simple desk was designed with classical proportions from his architectural training. Fisher’s fluency in this geometric layout is obvious from his college geometry notebooks in the archives. These notebooks are full of compass exercises to lay out complex patterns. Designing a desk was easy compared to the drawings he usually did. This “artisan’s design language” (as George Walker has called it) must have been intuitive in Fisher’s cosmos of order and mathematical rationality.
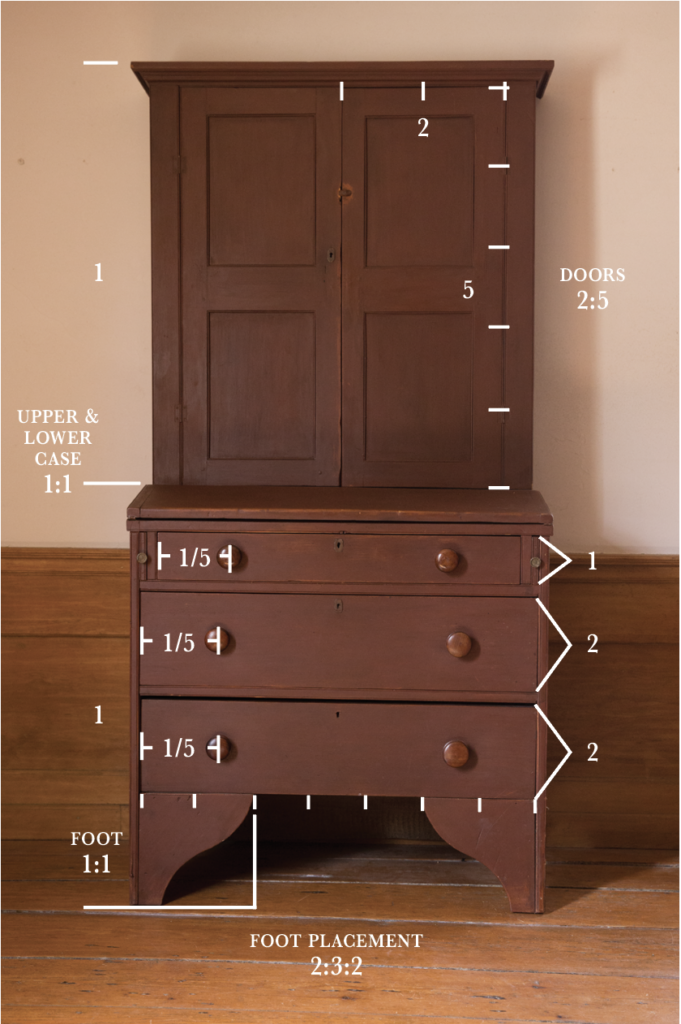
The panels in the doors are interesting in their irregularity. Their flat sides face out in the Federal style and are beveled only where needed on the inside. The insides of the panels have heavy scalloping from the fore plane, even leaving behind evidence of a nick in the iron of the plane. This tendency to continue to use a nicked iron without regrinding the bevel is consistent throughout his work and concurs with the notion of pre-industrial indifference toward secondary surface condition. For the bottom two panels, he seems to have run short on material because the panels are only barely as thick as the 5⁄16″ groove and, even at that, both retain minor, rough-sawn texture. It appears he was scraping the bottom of the barrel to get those doors finished.
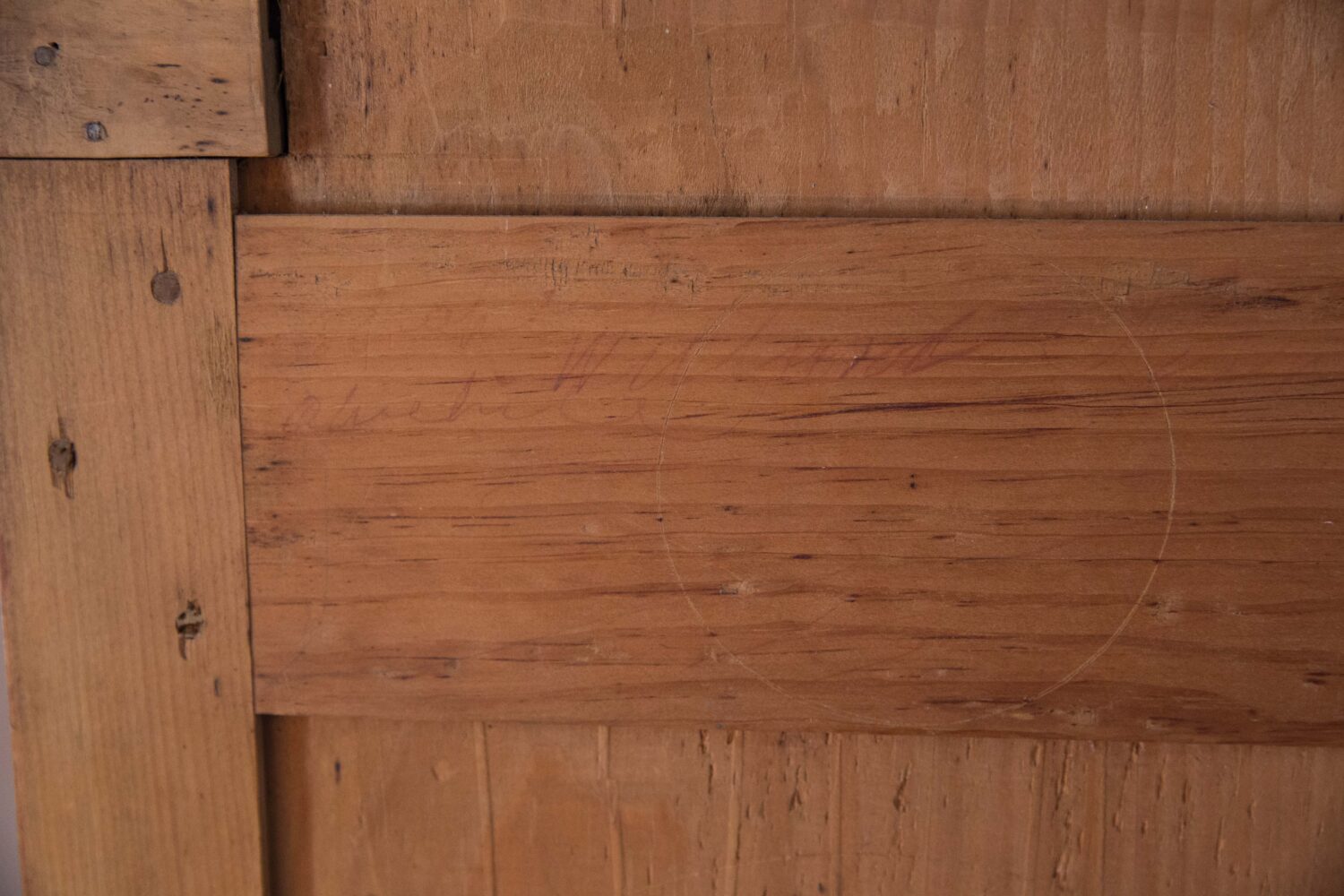
The insides of the doors have several inscriptions. “Willard” is written in red ink on one door, and “Josiah F” on the other. There are also compass-scribed circles on the inside of both doors whose randomness appears to have no significance beyond doodling. Even more perplexing, however, is the recording of “1 gallon of vinegar” on the inside of the door. This pattern of documenting purchases (and then crossing them off when paid) as well as notable life events is seen in several other pieces throughout the house. Jonathan seemed to have started the habit but Willard definitely took it far beyond his father. Willard’s name, agricultural notes and weather reports appear all over the house and his son, Fred, seems to have continued the tradition.