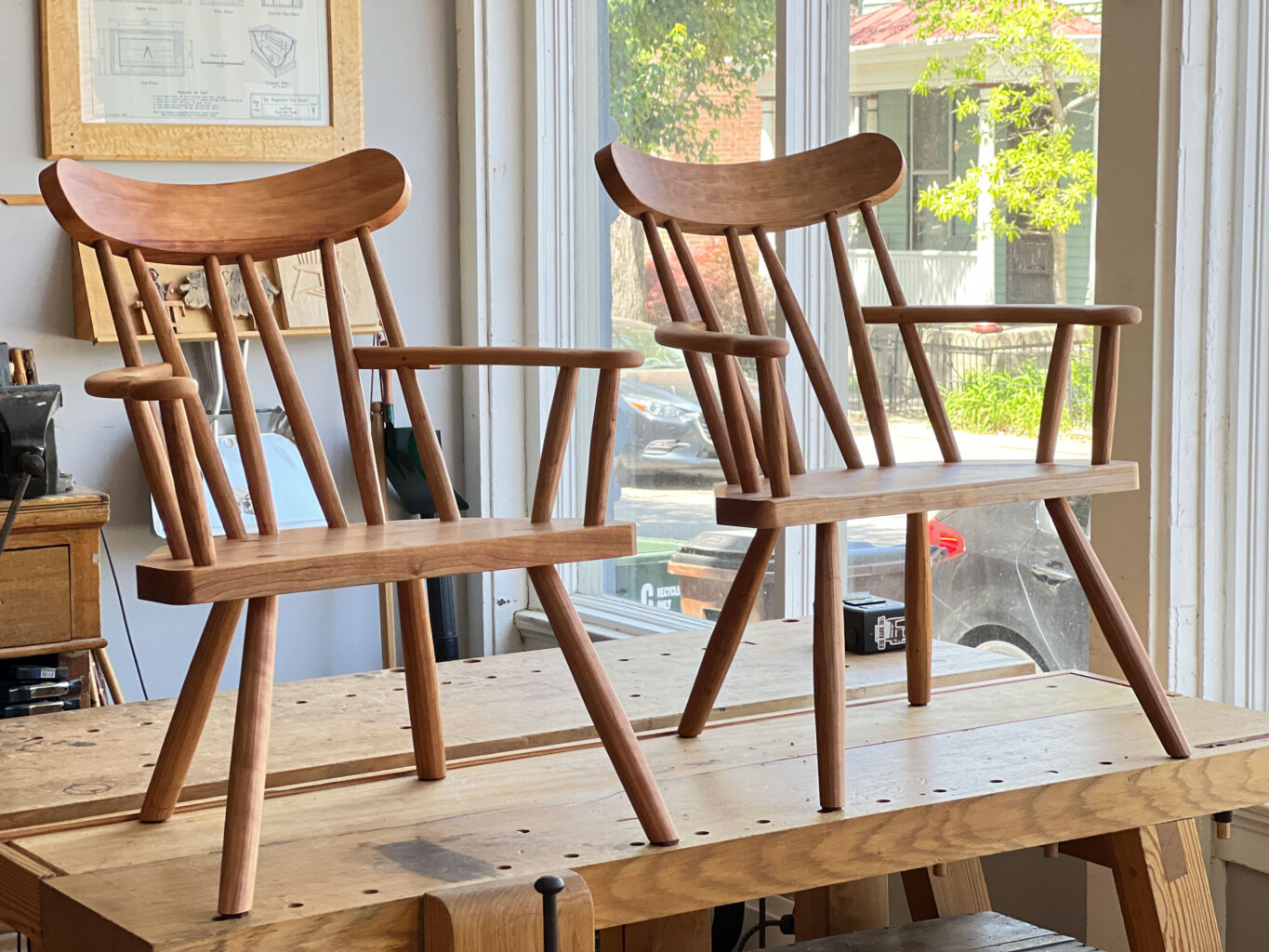
The $50 introductory price of the “Video: Make a Gibson Chair with Christopher Schwarz” ends as of June 18; on Monday, June 19, the price will be $75.
Gibsons are quite unlike the other stick chairs Chris makes. And he has devised novel ways to use cheap lasers to make your life easier when building them (meaning you don’t have to build a lot of complicated jigs).
Chris and I spent a lot of May 2023 filming the process, condensing it into a video that:
- Will not waste your time. Chris dislikes prattling on and on in a video (and in life). He tried to make this video 100 percent meat – no gristle.
- Will show you how to build the chair and avoid common pitfalls. He has made a lot of mistakes while figuring out the Gibson. He is happy to show you his scars and detours.
- Is somewhat enjoyable to watch. In our video there are cats, self-deprecating jokes, the breaking of the fourth wall and other small amusements that will, we hope, keep you awake.
- Has the information you need. The video comes with all the patterns (hand-drawn by Chris) and cutting lists and sources so you will get up to speed quickly.
This chair is a good first chair. Yes, it’s a bit angular. But you can do it. You just have to commit.
This 3-hour video includes all the videos and all the drawings and patterns. All free of DRM (Digital Rights Management) so you can put the video on your laptop, iPad, phone and desktop with no restrictions.
You can read more about it here and order it if you like. After June 18, the price will be $75 forever.
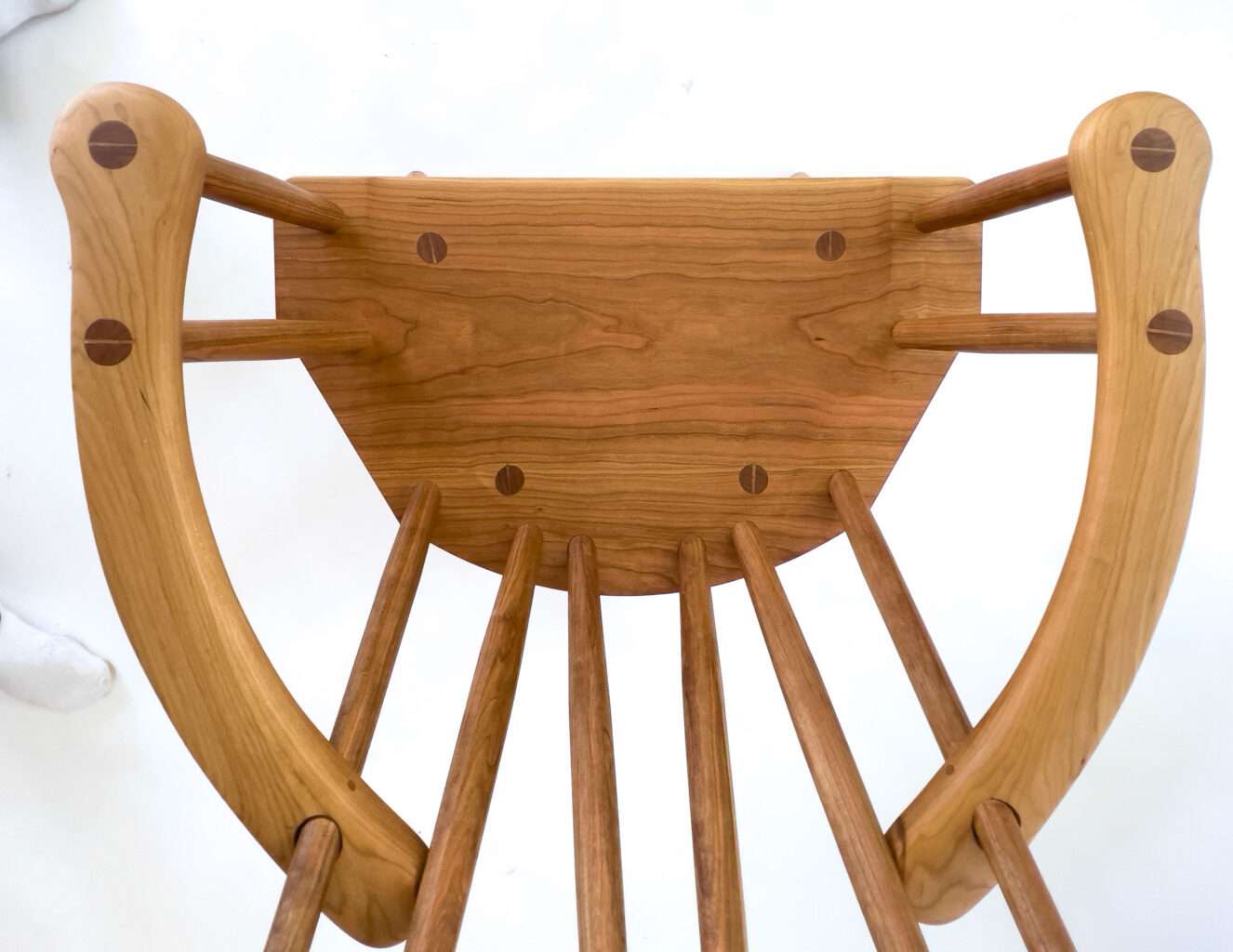