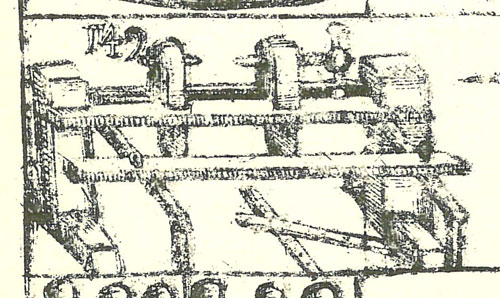
12. AS There are different Matters, and Substances to be Turned, so there is also diverse ways, & different Tooles to be used in each different Matter; As Soft wood, Hard wood, Ivory, Brass, Iron, &c. Each of which I shall successively discourse upon each of their working Tooles.
CXLIX*. The Lathe, it is the Turners or Throers Engine, by which they make all their Turned Works. This Machine Instrument is so vulgarly known, though it cannot be described in a Draught so as all its parts shall appear at one single view, yet I have set down enough of it to give you the names of its several members and their uses.
Parts of a Lathe.
The Leggs, or Stiles, are two thick Square peeces of timber about 3 Foot long, and 6 Inches broad, which are set upright, to them the other parts by mortesses are fastned; Haveing Braces at the bottom by which they are fastned to the floore.
The Cheeks, or Sides, are the two side peeces, fastned on each side the Leggs at the upper end by Tennants and so pinned; or else by a strong Iron Screw, made with a square Shank at the head, to go through the Cheeks and Stiles, and so by turning on the end of it an Iron nut, the two Cheekes will be drawn close to the tennants, or upper ends of the leggs.
The Puppets, are the square peeces of wood rounded of at the head, which have the Pikes, or Iron Pinns in, upon which the work is turned. At the lower end each hath a Tennant to slid between the two Cheeks, with a Mortess throwe them, for to put Taper wedges to keep the Puppets close to the Cheeks.
The Screw, and the Pike, are the two Irons upon the points whereof the centers of the works are fixed, & after screwed hard that the work slip not off. The Screw hath a Nut in the Puppet, and an Iron handle fited into the hinder end of the Screw by which it is turned forwards and backwards as the use of it shall require.
The Rest, is a Square peece of timber one corner of it rounded off: upon this the workman layeth his tooles in working to keep them stiddy while he is useing them.
The Stays for the Rest, are two peeces of wood fitted and fastned under the Shoulders of the Puppets, upon these the Rest is set at any distance from the Pikes, by the meanes of Wooden Screws set in wooden Nuts against the Rest.
The Side Rest, is a Rest disjunct from the Lathe, and used by Turners when they turn the flat sides of Boards, which standing athwart the Pikes they can the more conveniently rest their Tools upon it. It is a peece of Oaken plank firmely nailed on a square peece of timber standing upright, which as a tennant slideth into an Iron Collar that reacheth through the Cheeks and is wedged under as the Puppets are.
Some Turners to the square tennant set on one end of it a long round Iron Cilindrick Socket, into it is put a long round Iron Shank, on the top whereof is made the Side Rest which turneth any way in the Socket, and kept fast therein by a Screw Pin going through the side of the Socket.
The Treddle, and Cross Treddle, are peeces of Timber which are nailed to the ground with a Leather that they may rise and fall, to the other end is the String fixed which goeth to the Pole.
The Pole, is a peece of timber that will bend and go to it place againe, by this the worke is turned about in the Lathe.
The Pole Rests, are Sparrs or other timber nailed to the top of the Seiling, with an overthwart peece from them on which the Pole playeth.
The Rowler, is a round peece of wood made use of when the Rome is not high enough for a Pole to play up and down. It is moved on two Iron Pins fastned at both ends, with a Pole set either before, or behind the Lathe, with a string from it to the Rowler.
The Bow, which is an Archers Bow, and is used by some Turners that work in small, and that seldom remove the Puppets of their Lathe. It is fastned over head and from the midle of the String another hangs down & comes to the Treddle
The Great Wheel, it is used when heavy worke is to be turned, such as the Pole and Treddle will not command. The Wheel is set in a moveable Frame consisting of wooden Standards, Lying, Overthwart, & Cross peeces mortessed together. The String lyeth in the Grove of the wheel and turned cross is put into a Grove of the worke, or a Mandrile or Pulley fixed to the side of the worke, and is turned about with one or two Iron Handles.
The Treddle Wheel, is a wheel made of a Board with a grove in for a string, which goes cross to the grove in the worke. It is under the Lathe on an Iron Axis with a Crooke at one end, on it is hung the noose of a Leather thong, and the other end fastned to the Treddle, which by exact treading on, carryeth the wheel about without intermission.
The String, it is made of the Guts of Beasts as sheep &c. though the generall name of it is Cats-Guts.
The Seat of the Lathe, it is made of wooden Bearers, with an overthwart peece, with Iron pins at the ends to fasten it: against this the workman supports himselfe to stand the stiddier to his worke. In the sted of this Seat some Turners make use of a strong Gerth web, fastned to the Leggs of the Lathe, against which he stays himselfe and keep him steddy at his work.
The Horn, is the tip end of an Horn, hung on the outside the puppet, or else a round Wooden Box, pinned under the Cheek to hold, oyle or grease in, to liquour the centers of his work to make it run easie.
— From Randle Holme’s “The Academy of Armory, or, A Storehouse of Armory and Blazon” Book III, Chapter VIII, Plate 2. Why am I reading this?
Like this:
Like Loading...