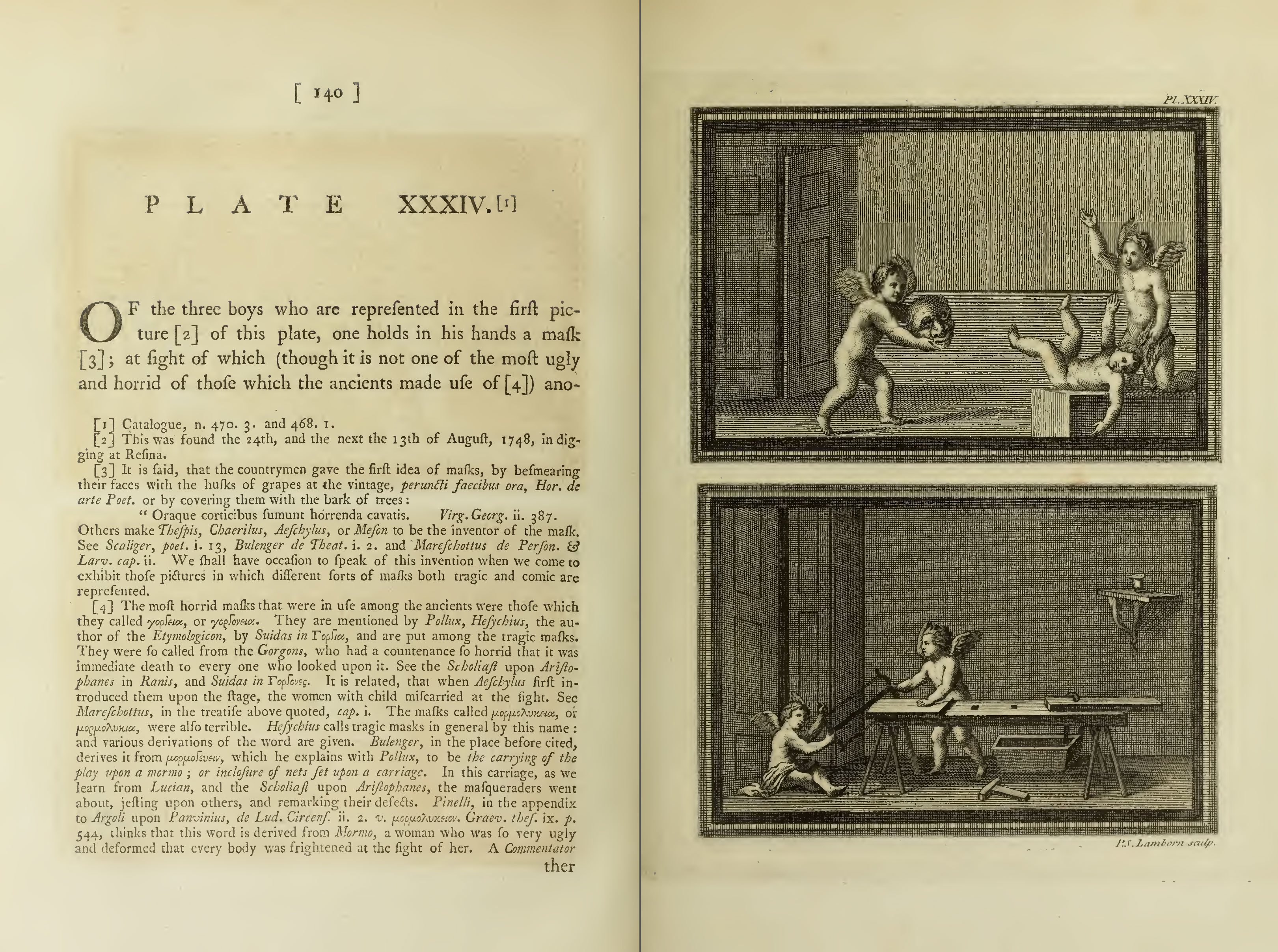
People often ask us where we find the interesting plates and images of early woodworking for our books and this blog.
Though it sounds snarky, the true answer is “on our computers.”
There isn’t some grand repository of awesome images of early woodworking images that you can visit and suddenly become Jeff Burks or Suzanne Ellison, our two hardest-working researchers for Lost Art Press.
Both researchers have taught themselves to work in other languages and comb the network of research libraries across the globe that are stitched together by the Internet. Though all three of us have been doing this a long time, I’m never surprised when one of them turns up a new database of images.
If you haven’t fallen asleep yet, here’s a brief peek into how we operate to nail down one single detail.
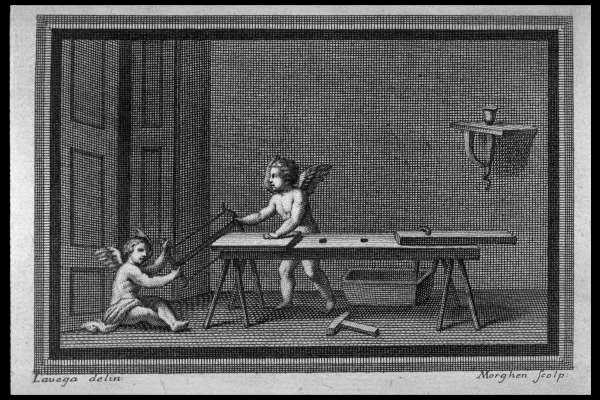
So this year I’m building a pair of Roman-style workbenches for Woodworking in America. One of them will be from a fresco at Herculaneum, which was covered in thick ash after Pompeii erupted in 79 AD and rediscovered in the early 1700s.
The fresco doesn’t exist anymore, according to Suzanne’s conversations with Italian antiquities experts (she’s a brazen one). But there are engravings that were made for royalty and (eventually) a more general public throughout the 18th and 19th centuries. Once you start looking at these engravings however, you can see that they don’t agree.
For example, in plate 34 shown above the bench has been drawn at other times without a holdfast, without holdfast holes, with four legs missing, the toolbox moved and the oil on the shelf moved. So in order to make sure it’s OK to use a holdfast on my reproduction, we have been researching this tool for about the last year.
Scholars are little help on this question. Books on Roman tools were written mostly by people who don’t know what a holdfast is. That’s not to crap on their mortar board. Many modern woodworkers don’t know what a holdfast is.
So Suzanne dug up the original royal volumes of the images shown in plate 34. Then we compared those images to frescos that survived to see how accurate they were drawn and then engraved. The answer is: The accuracy on the early royal drawings is remarkable. So it’s fair to say that the artists saw what they thought was a holdfast in the fresco.
In our research we both stumbled onto “The Antiquities of Herculaneum” by Thomas Martyn and John Lettice (1773). (Download the excerpt here.) In the section on plate 34, the authors have a footnote saying a holdfast was shown in a Gruter marble. Is Gruter a place? No. A person. Yup.
Jan Gruter compiled “Inscriptiones antiquae totius orbis romani, in corpus absolutiss” in 1603, an enormous 1,678-page compendium of Roman and Greek inscriptions.
So Suzanne and I spent hours last night scanning all the pages and pulled out the four images of woodworking tools. Did we find the holdfast?
Maybe.
Below are the four images. One of them has a snake-like thing that could be a holdfast.
The net result of all this work is that I feel fairly confident in adding a Roman-style holdfast to that bench (blacksmith Peter Ross has graciously agreed to make all the hardware for these benches).
But I will have an asterisk by my holdfast at all times.
— Christopher Schwarz
P.S. What motivates Jeff and Suzanne to do this sort of work? I don’t know. In this particular case, Suzanne’s grandfather is from San Giuseppe Vesuviano, which is near Herculaneum and Pompeii.
Like this:
Like Loading...