
Dan Phillips doesn’t advertise or have a website, so when Christopher Schwarz suggested he’d make a good subject for a profile, adding “he has a great eye,” I looked him up on Instagram. Here’s a guy who doesn’t give a fig for the accepted wisdom about social media, I thought; Daniel’s feed is a colorful mix of drawings, paintings, home interiors, music, kids and woodworking tools, all with a good dose of irony. Scattered among the variety you’ll find images of dovetails, other joinery details and finished furniture pieces. Not for Dan the segregation of woodworking from “life” or any of the other interests that characterize it, a different Instagram account for every one. How refreshing.
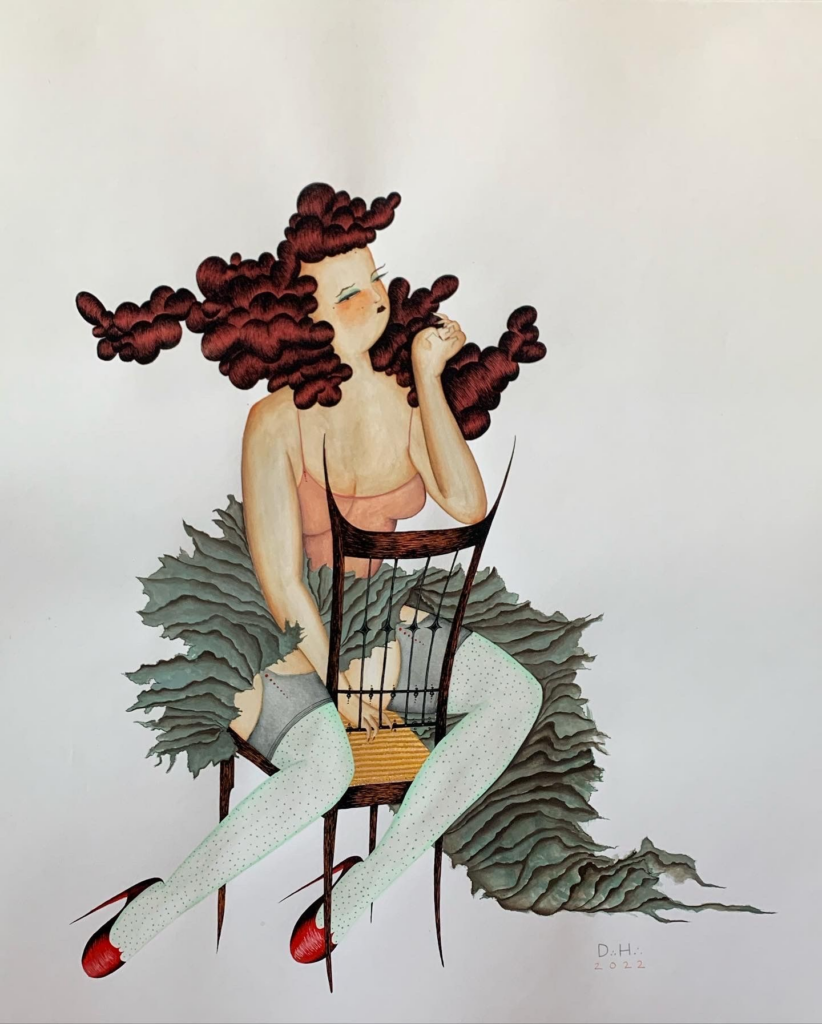
Given what I saw, I wasn’t surprised to learn that Dan, who goes by D.H. Phillips, is the son of artist parents. Born in Dallas in 1976, he’s the middle of three children. His father, Harvey Phillips, shifted from visual art to architecture early in Dan’s life. “For as long as I can remember that’s what he did, and still does,” Dan says. His mother, Susie Phillips, remains a practicing artist in paint.
Dan’s dad was also a professional carpenter who always had a woodshop of one kind or another. “As soon as I was old enough to work a bit, he would take me, first, to demolition sites,” says Dan. “Then I learned to frame houses and sheetrock and all that stuff. I really liked being in the shop more than at somebody’s house.” As he grew more interested in design, H.C. Westermann, a sculptor and two-dimensional artist, became a strong influence. “I wanted to learn that more fancy woodworking stuff, and that wasn’t really in my dad’s [wheelhouse].” Ambitious, he made a dovetailed box on the bandsaw “with lots of wood putty.”
Dan’s former wife is a paper conservator. One of her grad school teachers had trained in the book-binding program at North Bennett Street School. He looked the place up, took a two-week class in fundamentals of fine woodworking and says “That was it.” He applied to the full-time program. He was still motivated by two-dimensional artistic interests, “but once I was there, furniture making totally took over.”
Dan attended NBSS from 2005 to 2007. “I loved finding out about the early American decorative arts. We’d go on museum trips, and I loved the furniture. But all the other stuff – the quilts, paintings, folk art – that whole classical early American thing really did something for me,” he says.
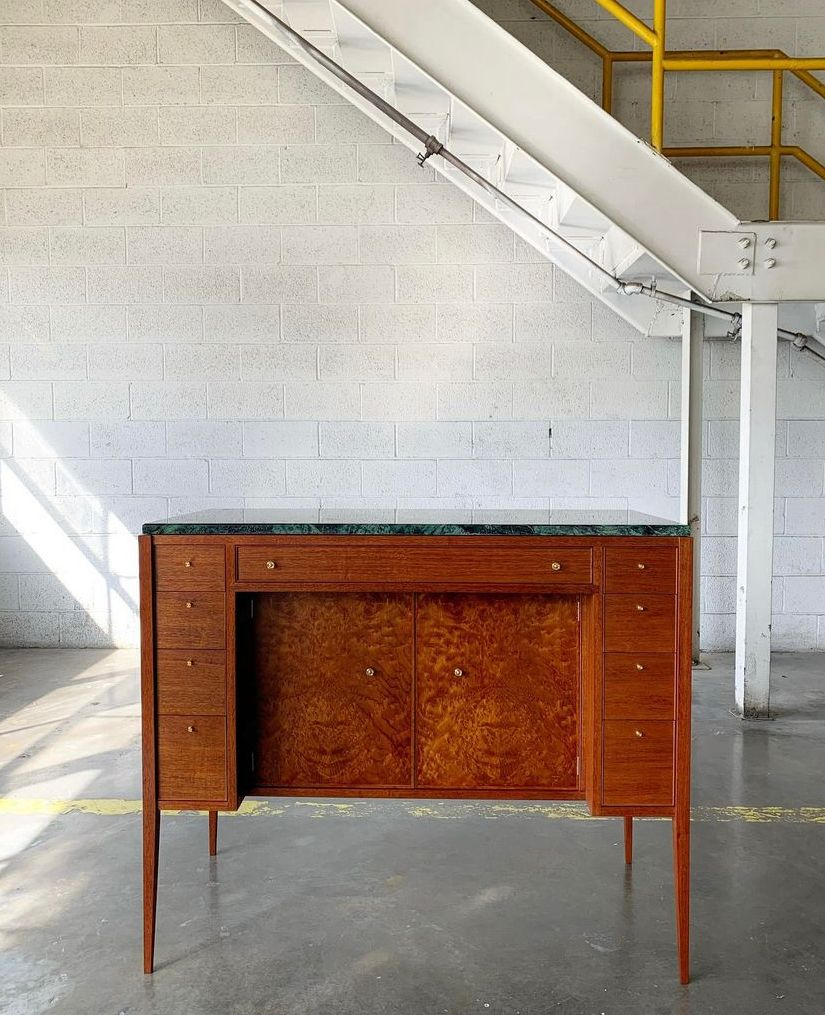

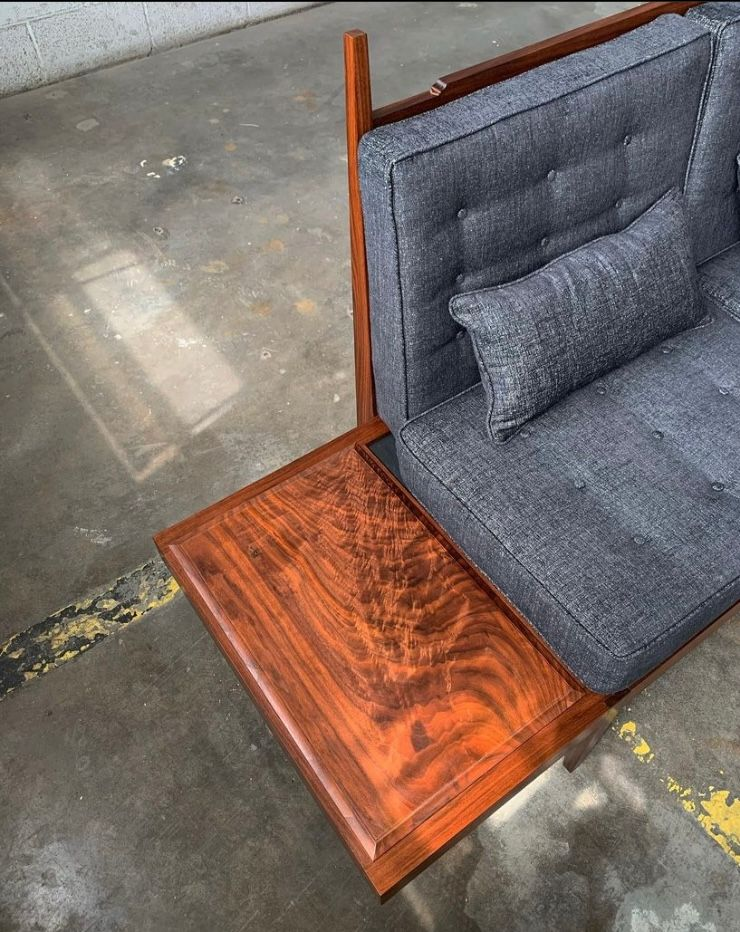

“There’s an aesthetic that carries through the periods,” he continues. “A piece of scrimshaw looks just as awesome to me as a federal secretary. That pre-industrial stuff…. You can see the hand in everything. I love to draw – I don’t use computers for drawing – so maybe there’s something there…a tactile thing, a certain crudeness, no matter how fancy something might look. You can tell it’s handmade, and I love seeing the transition through the periods and the details that stick, the things that change.”
After his time in Boston Dan moved back to Dallas in 2007 and set up in his dad’s shop. Slowly, at first, he began to get commissions; the first was a coffee table for his mom. Then, he says, “It just kind of snowballed. It’s been pretty steady.” There are times he’s overwhelmed and others when “my fingers are crossed that something’s going to pop up. I just sort of made furniture making my reality, whether commissioned work was actually happening or not.”


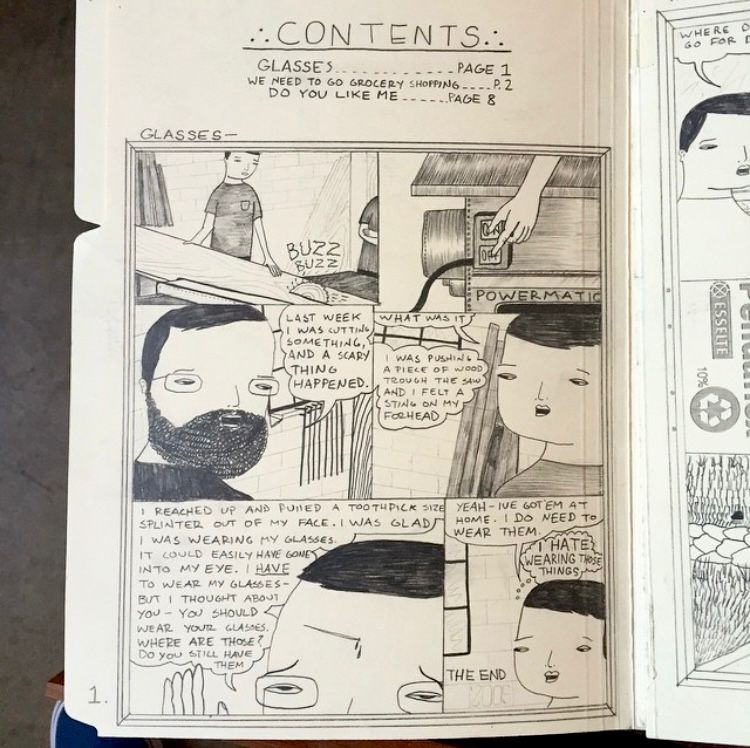
Dan’s work comes mostly through word of mouth. Although he posts work on Instagram, he says “I’m not sure how much business I get from it.” He always asks people how they found him. It’s usually from a friend, or they saw something he’d made.
Today he makes mostly residential stuff – desks, sideboards, wall units, beds, chairs but mostly “loungey” chairs. “I don’t know that I’ve ever made any dining chairs.” There are dining tables…some work for offices, such as desks, about which he remarks, “you can have some fun with all the drawers and hidden compartments.” At present his favorite thing is case pieces.
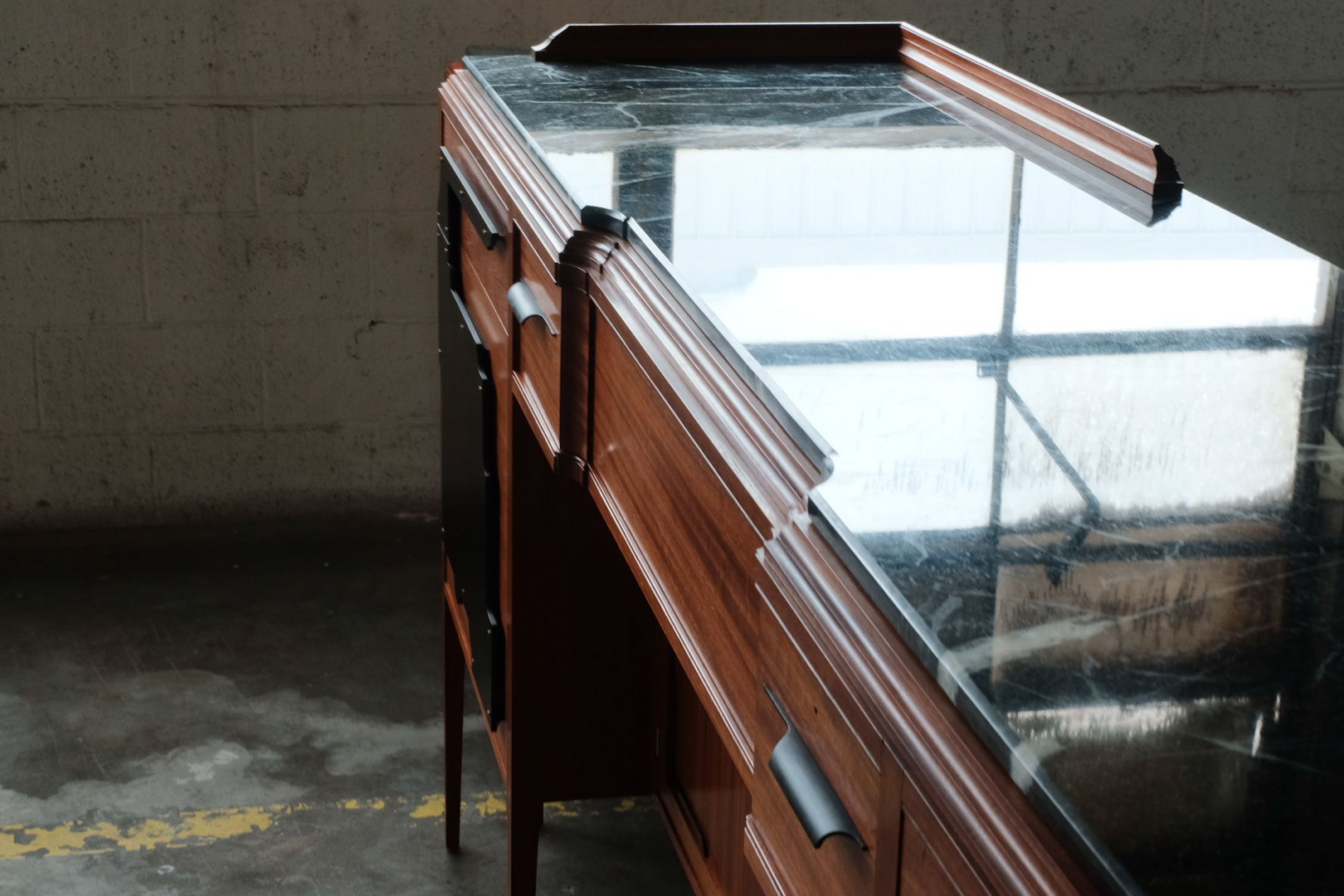
He works in mahogany and walnut, primarily darker woods and says, “I draw the piece and it will become obvious what wood to use.”

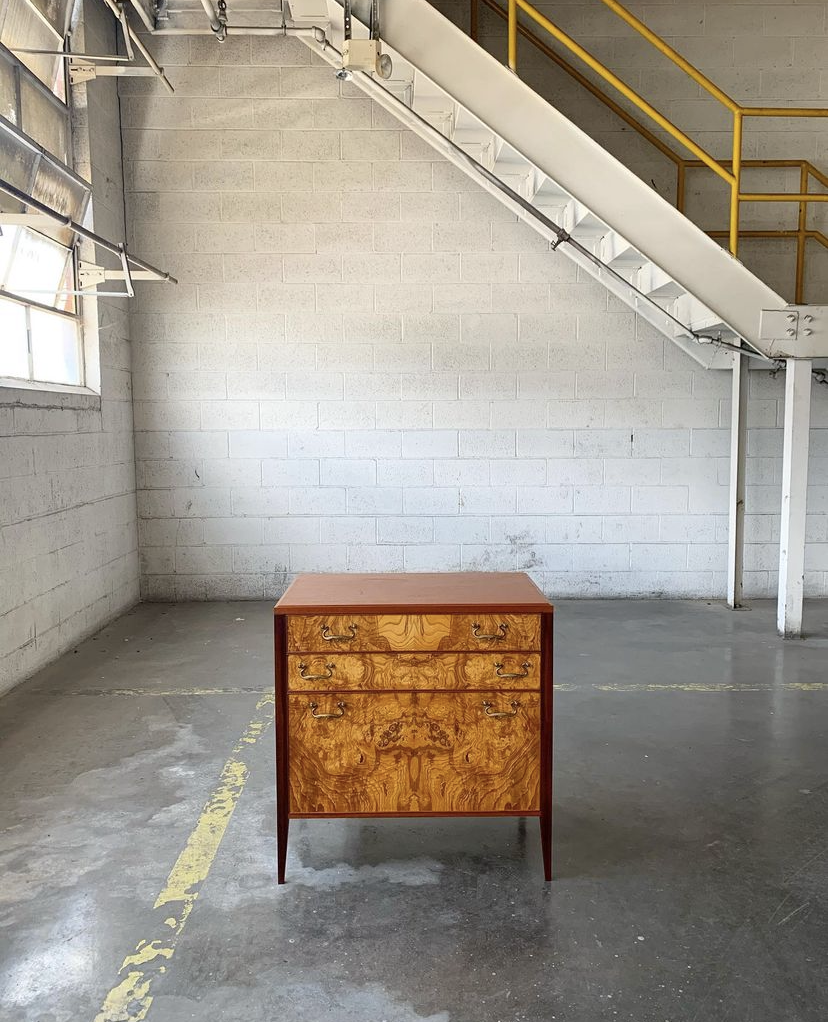

He’s still a very active painter, too. His paintings, he says, “have evolved over time. I first did them as train graffiti tags, then moved to paper.” He paints in watercolors and washes but sometimes reverts to colored pencil and watercolors. Most are gouache on paper.

He sells in a gallery, though recent work has been commissioned. “I never just ‘make art.’ I’ve got to have a reason. There’s someone who’s commissioned a piece, or I have a show coming up. The furniture scratches so many of those itches. I do a ton of drawing, so I never miss out on drawing stuff,” he says.
Dan’s shop is in a former Ford Motor Company manufacturing plant, a huge building near Fair Park in Dallas. He’s been there about 10 years. Before that, he worked in a Quonset hut. “That was not good! Whatever the weather was outside, that’s what it was in there. I couldn’t make fancy furniture.” He moved into a friend’s jewelry studio, but it became too cramped. He currently has about 5,000 square feet in the whole shop, but that includes a couple of office/bench rooms, a storage room, a machine room and more. A Plexiglas fabricator uses half the space; Dan and his dad use the other.
Home is near the shop. In fact, Dan says, most of his existence takes place within about a 7-minute-drive circle. Even his kids’ school is within that radius.
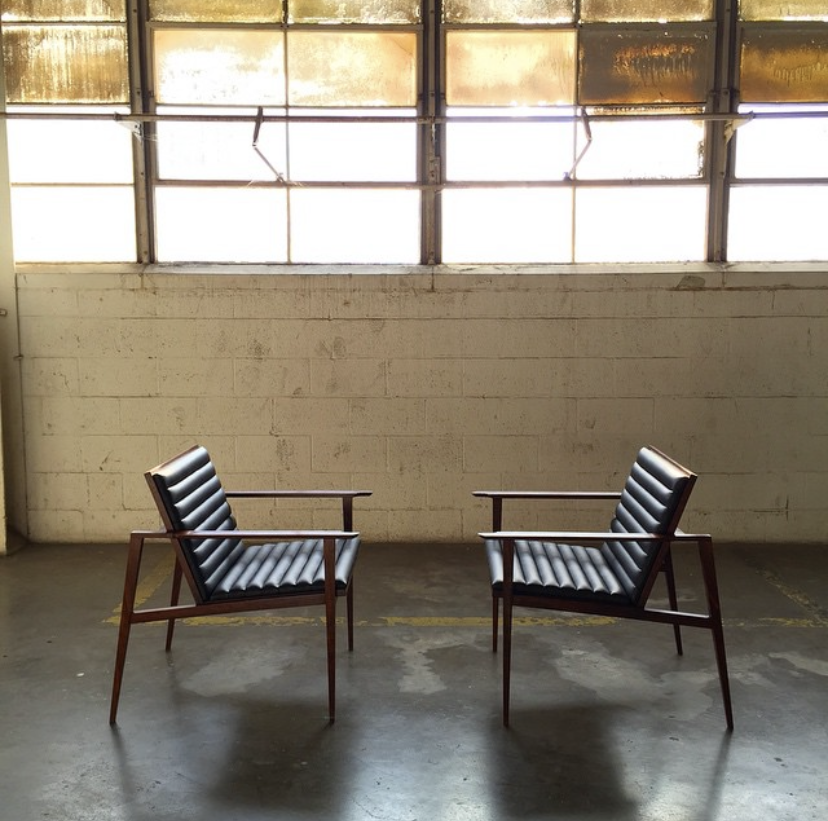
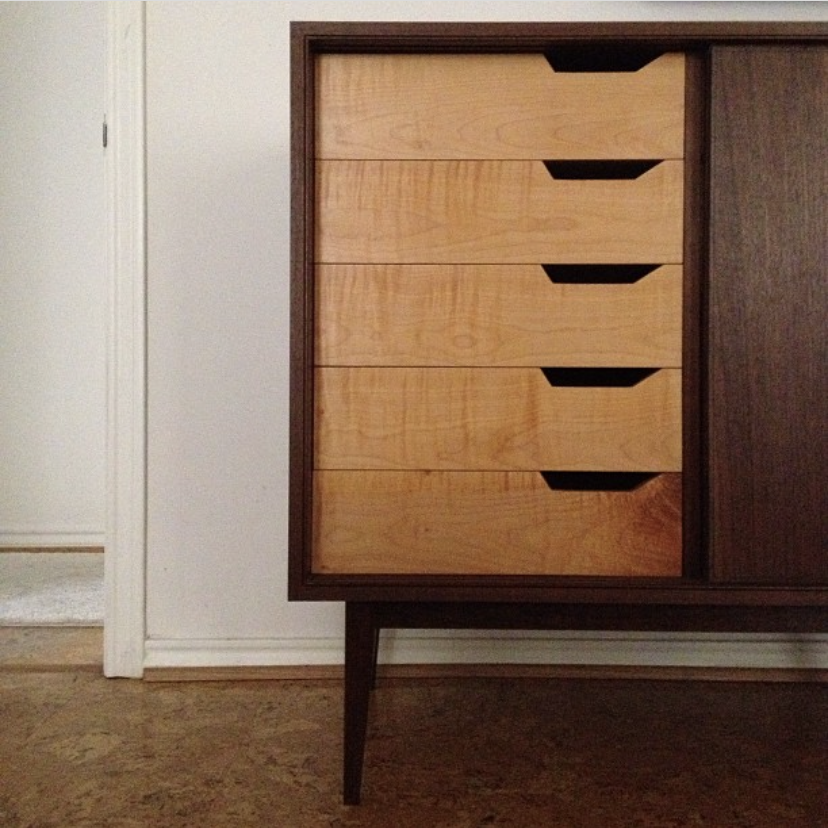
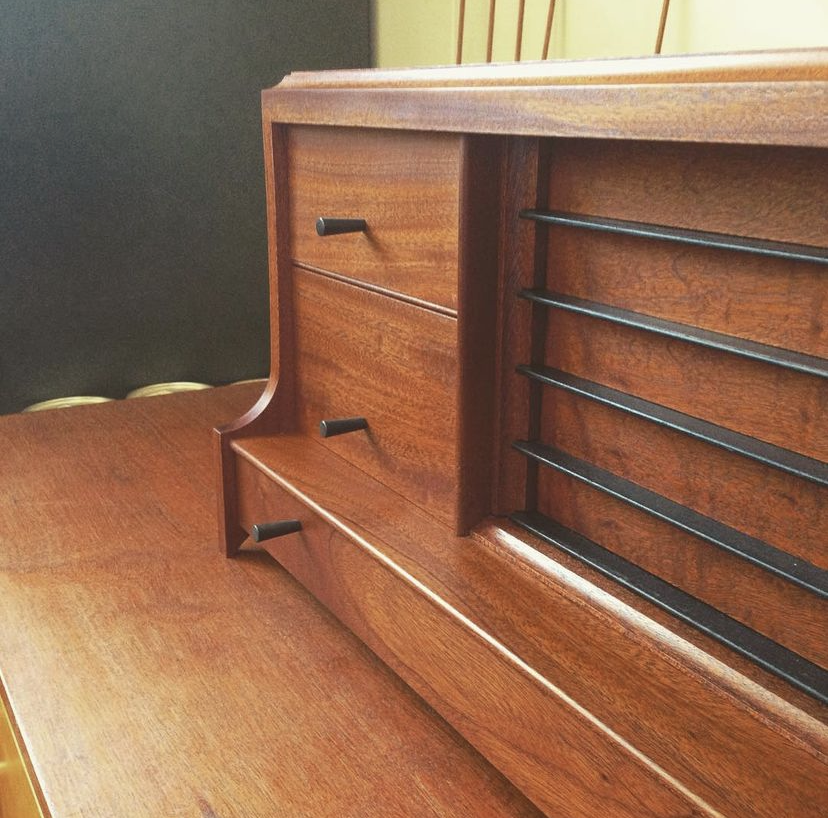
Drawing on the Past
Dan looks to antiques as a starting point. He has no interest in making period furniture as such but incorporates details he likes in his own work. “It’s an opportunity to participate [in furniture making] the same way the old guys did. You get these pattern books from Sheraton or Hepplewhite and use them as a starting point. The proportions…they worked it out! [Master those proportions, and your piece] already looks good. There’s no need to reinvent the wheel,” he says. Dan draws in pencil on printer paper and keeps refining designs, then makes a scale drawing and adjusts accordingly; for example, seat height is important when he’s making one of those “loungey” chairs, so he’ll base it on that.
He refines his drawings, which he calls doodles, until he’s satisfied. Then the challenge is “trying to get things to look like my ‘doodle.’ Sometimes things in the doodle are totally unrealistic, so I’m just trying to figure out how to get the same visual effect in the drawing. I like to draw stuff, and draw a lot of it. I’ve just developed a certain style from doing that. I probably have 8,000 drawings of furniture.”
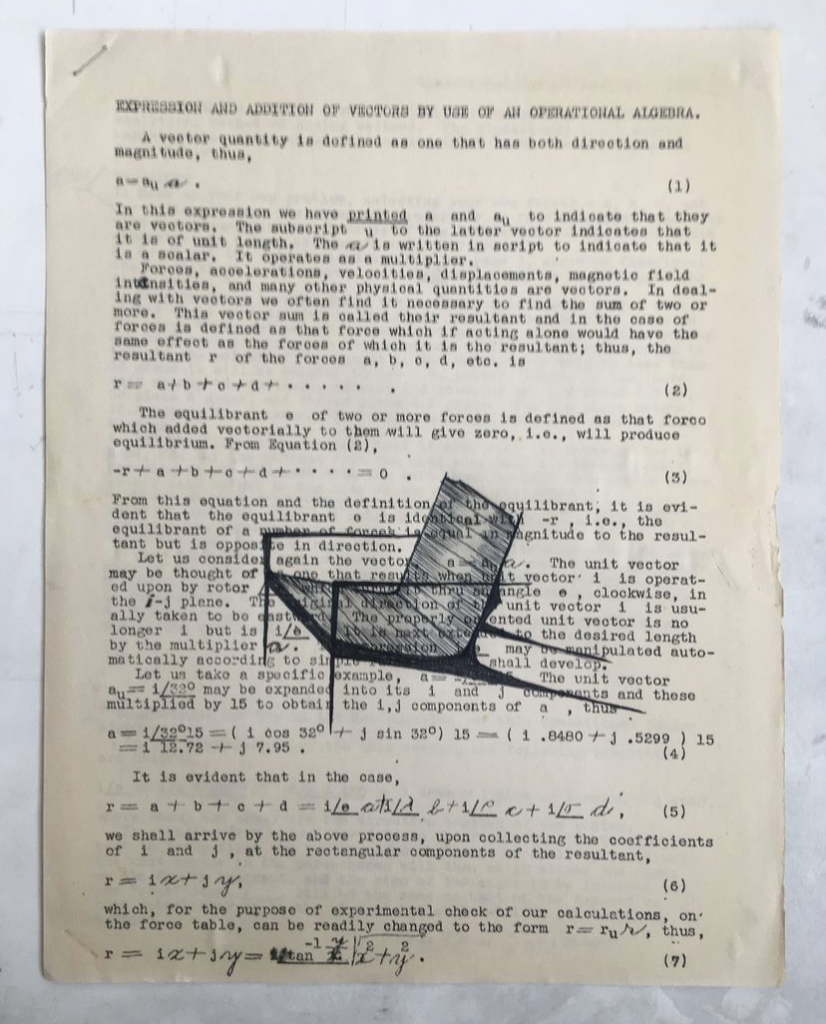
Home & Family

Dan lives with Jackie Dunn Smith, an artist who paints and does tattoos, devoting about half her work time to each. They have two children; their daughter, Velena Phillips, is 10. Their son, Mugsy Smith, is 14.
Dan’s mother’s family moved to north Texas from Pennsylvania via Oklahoma. His father’s side came from Kansas, where they were asparagus farmers; then, in a turn of events worthy of his arch Instagram feed, his paternal grandfather won a contest held on the radio that came with flying lessons as the prize. After training, that grandpa became a pilot, flew in the Second World War and went on to a career as a pilot for now-defunct Braniff International Airways. That’s what brought his father’s family to Dallas when his dad was in high school.
Their home is furnished with all sorts of things, many of Dan’s own making. For one show he built a 12’x 18′ cabin and furnished it with a bed, blanket chest and lounge chair. The installation was for sale, but it didn’t sell, so he ended up with the three furniture pieces. He also has furniture he made in training. As for the family dining table, he got that back from a client who moved and couldn’t use it; the client thought that Dan might be able to sell it, but there were no takers. He wanted to keep it, and in the end, they said he could. The rest of their home is furnished with a mix of antiques and IKEA.
When asked to sum up his work as a furniture maker, Dan says,
Simply, it’s what I do. If I had to analyze it I’d say that I like the place I’m in, where people are aware of my thing and that they are choosing me for the thing they want. There is no shortage of available furniture. It’s almost ridiculous to be making more. But I’m glad to be doing it. I love the art form. I love hearing what the client wants and the spark that goes off in my brain and the subsequent pencil to paper to hash out the general idea. I love the first impression and the miles of yellow tracing paper refining the design. I love making a presentation drawing for the client to look at. Once they say yes, I love getting out the big paper and using the drafting table. I love the problem solving of turning the doodle into a set of working drawings. I love figuring out how much wood I need and looking at the available wood that will work.
I loathe figuring out how much something will cost. But then they say yes and the wood shows up and you agonize about how to break it down and then you break it down and then it’s a mad fever of strategy and efficient work flow until you don’t have anything else to do but get some photographs made and deliver it. Pretty damn fun. Glad to be able to participate in a centuries old way to make your way.
– Nancy Hiller, author of “Shop Tails,” “Kitchen Think” and “Making Things Work.”