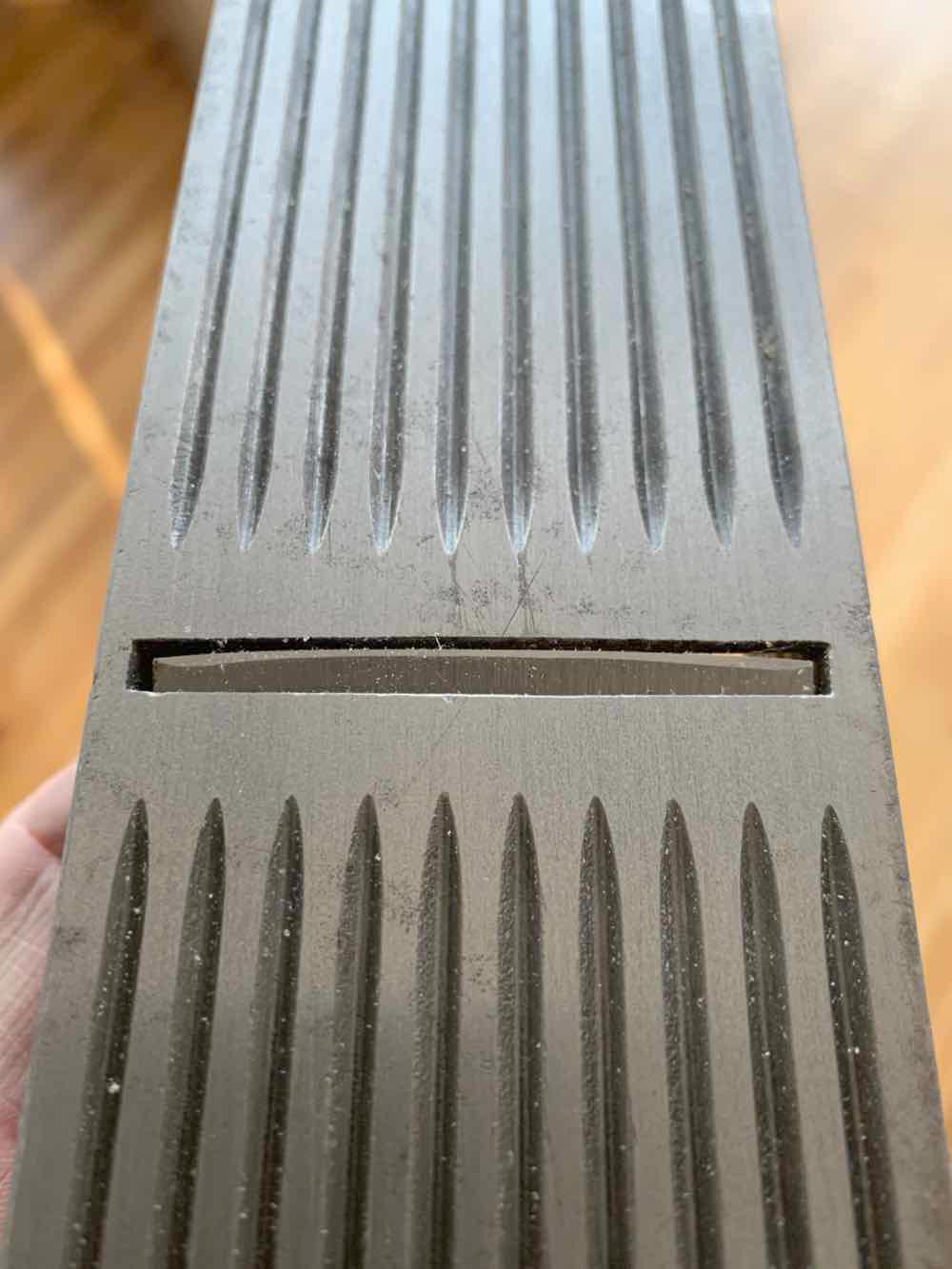
When I fixed up my first jack plane in the 1990s, I took the advice of every decent person around me: I replaced its old iron with a new Hock blade.
The replacement blade cost almost three times what I paid for the plane, but I didn’t think I had a choice. That’s just what I was told to do.
The Hock blade worked brilliantly, and it’s still at work in a jack plane in Florida. But now I know a little better. Replacement irons and chipbreakers are best for planes that are regularly pushed to the absolute limits of their performance – mostly smoothing planes and block planes.
The jack plane, on the other hand, works just fine with a stock blade – as long as the blade hasn’t been abused too badly by rust or softened by aggressive grinding. Stanley Works (and its competitors) knew how to make good steel. So an old iron that hasn’t been mistreated will take a fine edge and keep it for a good long while.
Even if you do intend to replace the blade in your jack plane to help support modern toolmakers (and I salute you), I encourage you to practice the grinding and lapping steps on your old iron. You’ll learn a lot, you won’t trash your new blade and you’ll have a backup blade for a rainy day.
Dressing the Flat Back
Based on the archaeological evidence, most of our ancestors didn’t care much about flattening and polishing the flat back of the blade. Many old tools show little or no attention to the back of the blade.
Despite this strong evidence, I still flatten the back. But I don’t go nuts. For the most part, I am trying to get rid of the grime, surface corrosion and small rust pits that are common on garage-dwelling planes.
I do this operation with the same setup I use to dress the sole of my planes: a 36” section of granite threshold with some #80-grit belt sander paper stuck to it. Dress the back of the blade until you see clean metal up at the cutting edge. Keep the blade flat against the paper (attaching a magnetic base to the iron is a good idea) and clean the metal filings off the paper after every 30 seconds of work.
This process shouldn’t take long. The goal is to get the blade clean enough and flat enough so that you can polish a small back bevel on the flat face (for this I will use David Charlesworth’s “Ruler Trick” and will cover the technique later in this entry).
After you clean the back with #80 grit, repeat the process with #100, #120 or whatever you have. Just try to make it flat, clean and a little more polished than it was during your earlier steps. I usually end this work on a coarse diamond plate. Some people end it on a #1,000 waterstone. It’s your call.
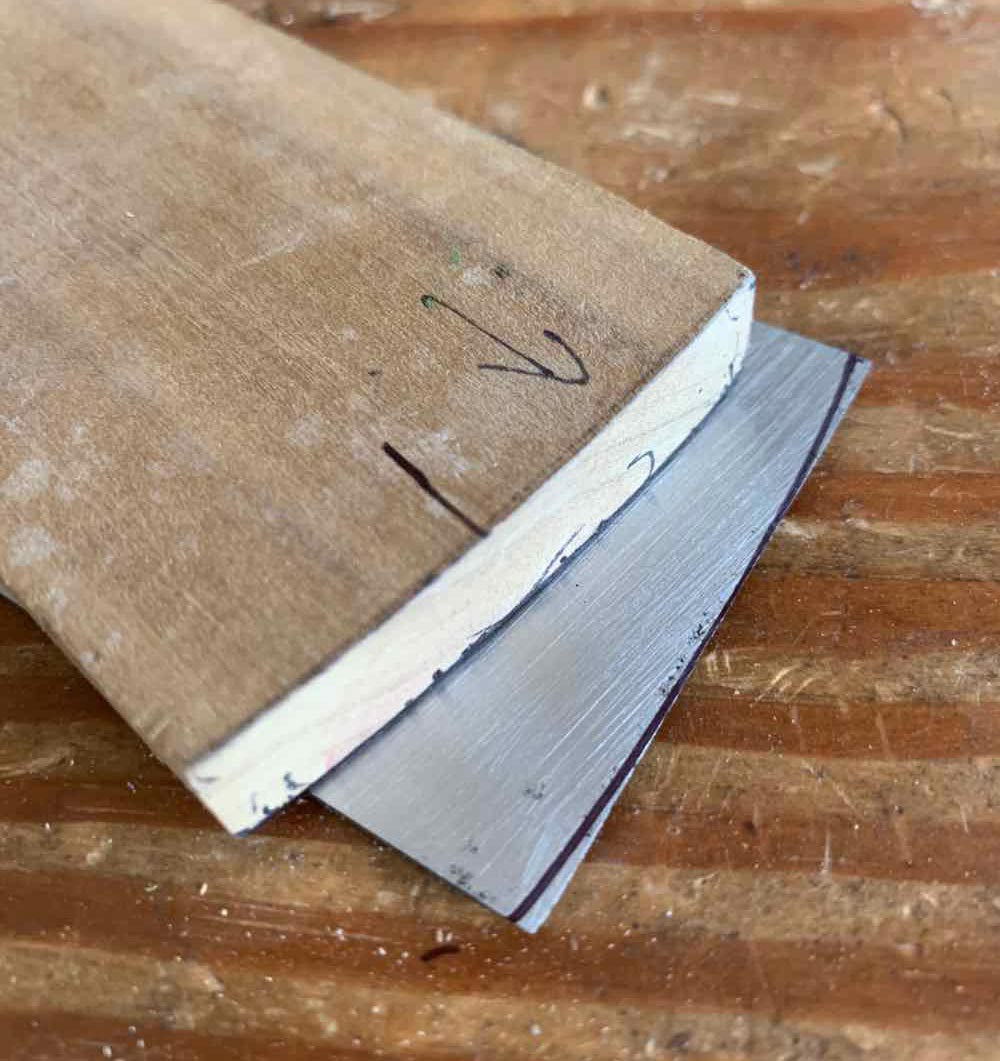
Shape the Bevel
The cutting edge of a jack plane should be curved across its width. This is a historical approach that goes back to the very first English-language writing on woodworking in the 17th century. And it’s an approach that holds up today.
How much curve? Of course, it depends. I like a curve that is somewhere between an 8” and 10” radius. The 8” radius is more aggressive, but can be tricky to sharpen in some honing guides (if you use a honing guide as I do).
The 10” radius is easy to do and works with most honing guides. If you want to play it safe, use 10”. If you want to take a small gamble (which is easily undone) then use 8”. Either way, take a scrap of plywood or scrap wood and rip it to 2”, which is the typical width of a jack plane’s blade.
Use your compass to strike an 8” or 10” arc across the end of the wooden bit. Saw, rasp, sand or otherwise shape the end to that line. Then use your template to mark the arc on the end of your plane iron. Use a fine fine fine Sharpie to make this mark. And make it as close as you can to the tip of the iron. Now it’s time to grind it.
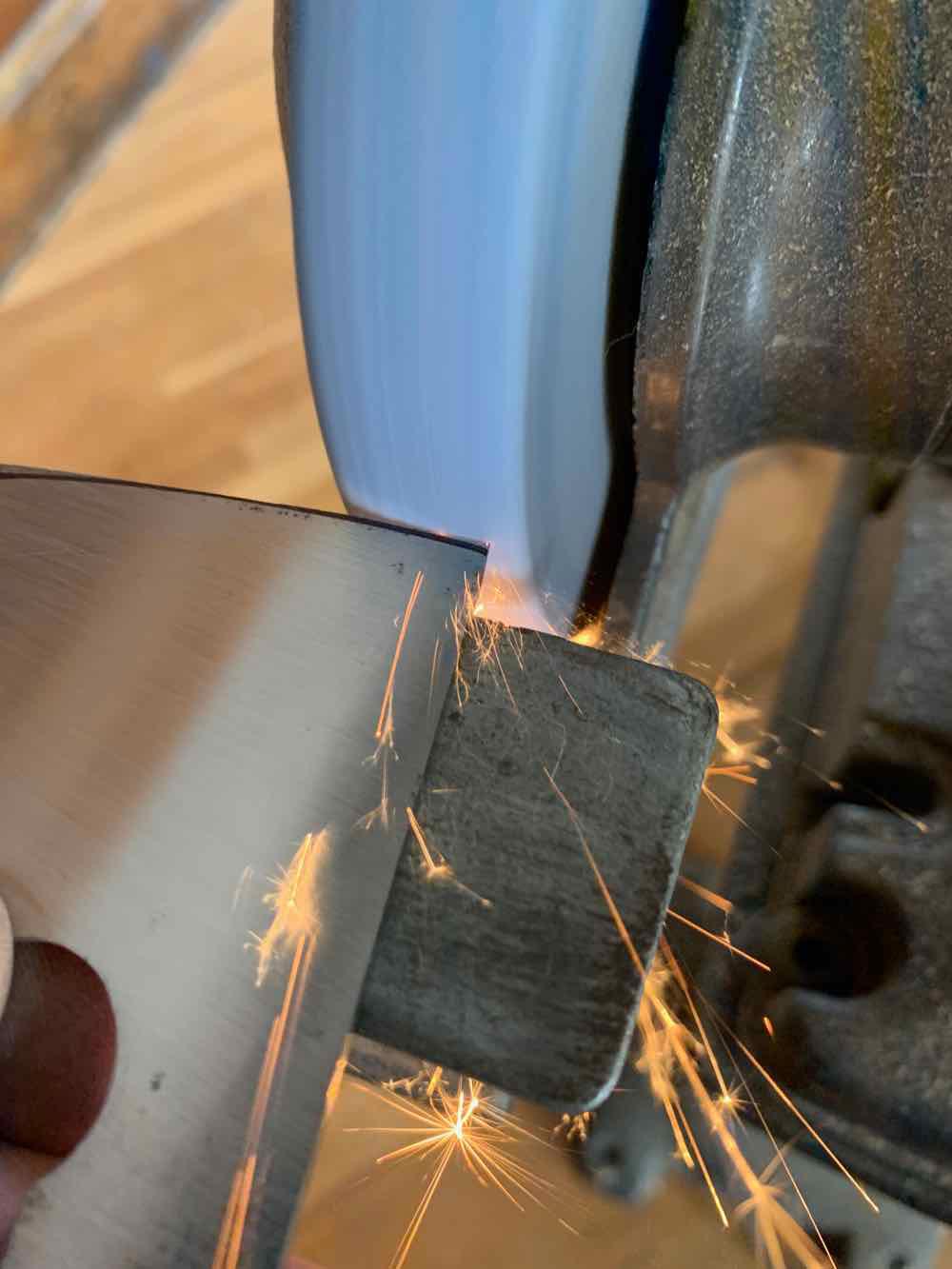
Grind the Bevel
Grinding is not hard. The idea of grinding is what’s hard. Get a grinder – fast speed, slow speed, hand-cranked, whatever (I have a fast electric one). Put a coarse wheel on it, like an #80 wheel. I use Norton 3X wheels because they seem to cut cool and fast. But I’ve worked on wheels of all colors. Coarse wheels that are friable (meaning they break down easily) are way better than dense wheels that don’t break down.
You can do a lot of research on grinding wheels. Or you can skip all that and just work with what came on your grinder and adjust from there. One important detail, however, is to dress the wheel so it has a slight convex camber. This camber makes it easy to maneuver the tool you are grinding.
So here’s what actually is important: the tool rest. Not the type of tool rest – whatever you got is fine – but how it’s set. Set it so it’s 90° to the grinding wheel. Yup, the goal is to grind the tip of your blade at 90°. Grinding the blade this way gets the curve to shape quickly, doesn’t heat up the blade much and gives you some flats at the tip of your blade to gauge your progress when grinding the bevel.
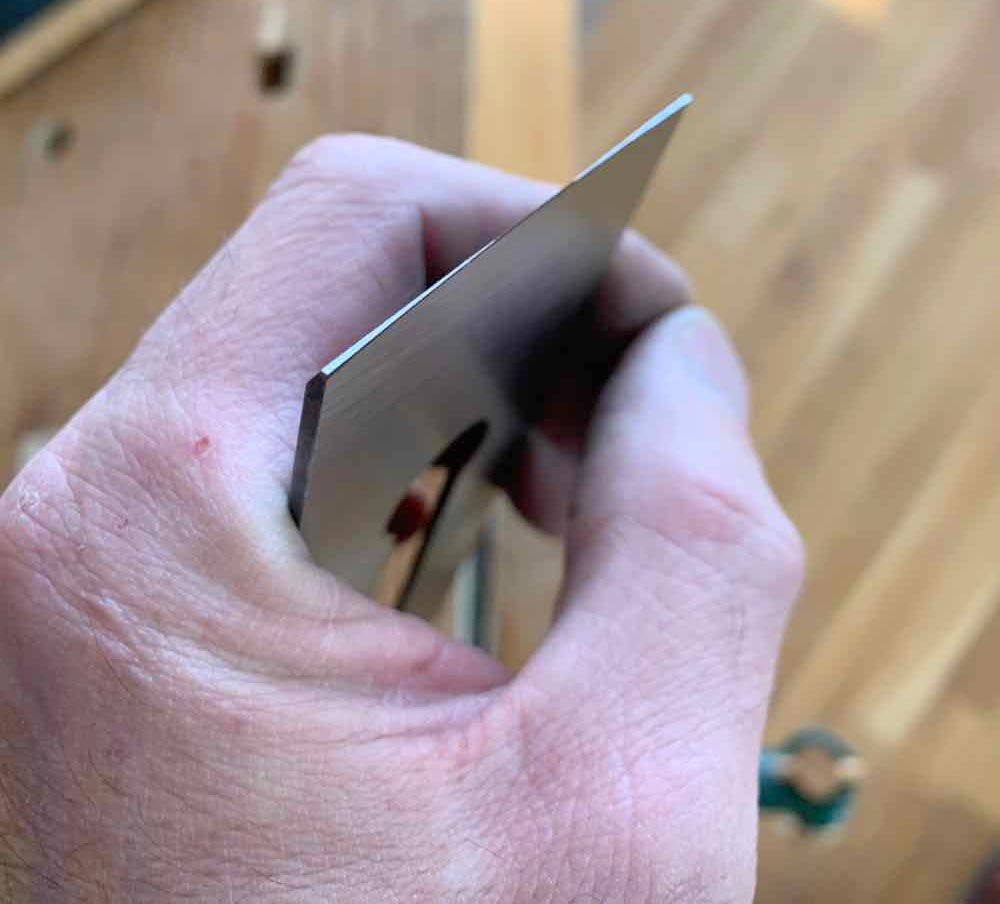
So grind the tip of the blade flat at 90° and down to your Sharpie line. The blade shouldn’t heat up much during this operation. But let’s talk about heat and steel.
Keep it Cool
When I grind steel, I pause after 5-10 seconds of hard grinding and check the temperature of the blade by pinching it with my fingers. If my fingers involuntarily recoil, the blade needs to be cooled before grinding it more. Dunk it in a cup of water until it cools. Note: This is not quenching (quenching is something else). This simply cools the blade.
If, however, you can grasp the tip of the work and continue on, then continue on. (Side note: If you do overheat the blade and it turns a little blue, it’s not the end of the world. Try using the blade anyway and see if you even notice that the edge degrades too quickly. Grinding away that blued area is usually an invitation to make the problem worse.)
When you get to your Sharpie line, pause to examine the flats on the tip of the blade. They should be the same on either side of the apex of the blade. Fix them if they aren’t equal – tiny equal flats is the first goal.
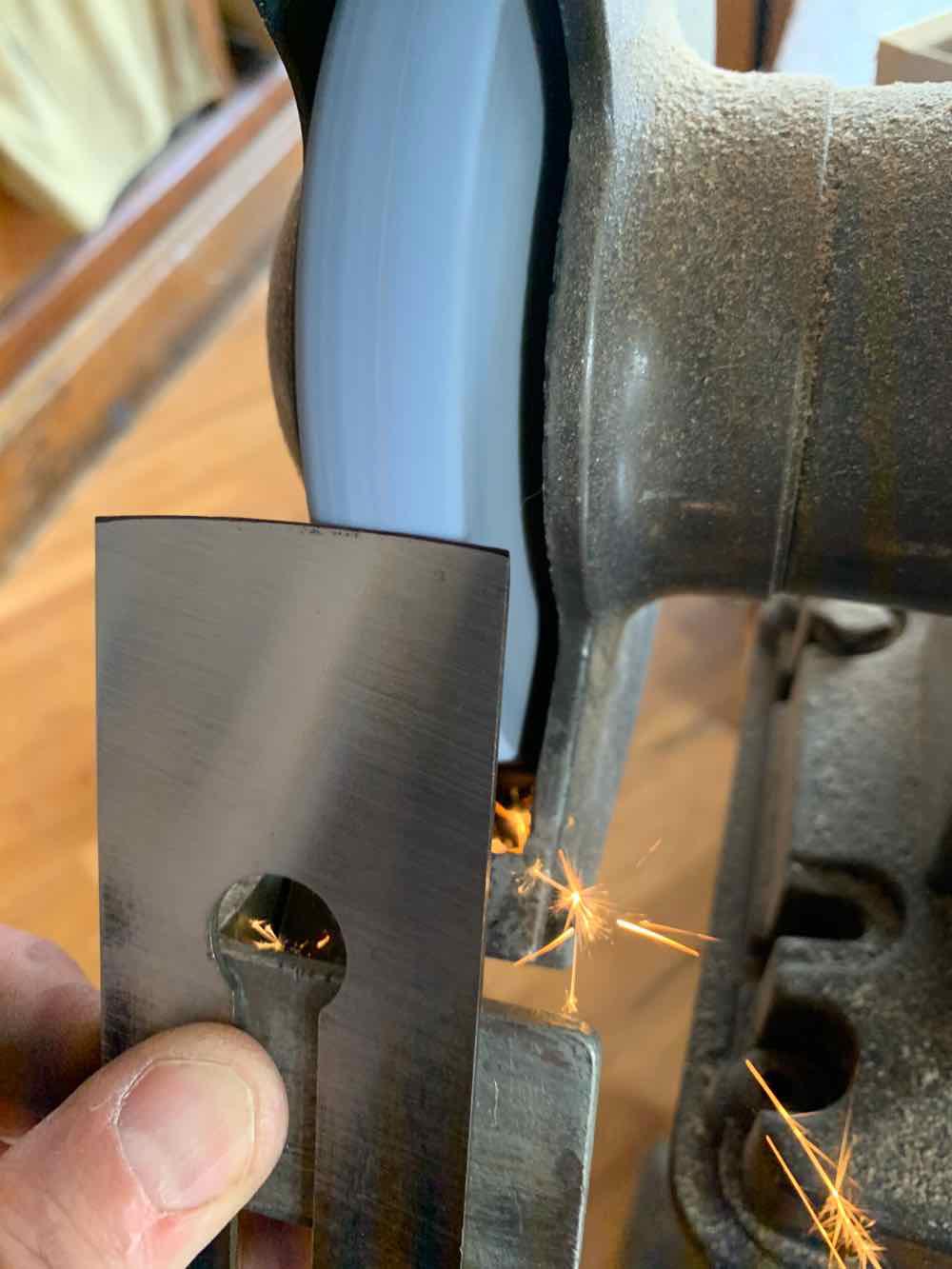
Grind the Bevel
Set the tool rest so it grinds at 25°. There are lots of gizmos that will do this. I use a popsicle stick with 25° cut on the end. When I grind the bevel on a jack plane, my first goal is to create a smooth 25° arc on the bevel that acts like a path I can then follow to complete the grinding.
I create this “path” by first touching the center of the iron to the wheel lightly. Then I move the iron right while increasing the pressure against the wheel. I repeat this operation while moving the iron left. I do this a couple times and look at the results. When the arc across the bevel looks even, I can work on removing lots of metal.
This is the part that is “the grind.” It can take a bit of time depending on how messed up the iron is.
During this operation, the motion is like the windshield wipers in your car. Touch the iron lightly to the wheel and shift it left and right – adding some forward pressure at the corners. Do this a couple times and pause to check the temperature of the iron and to see if the tiny flats at the corners are disappearing at the same rate.
If they are, congrats. Carry on. If not, you’ll need to add more pressure on the corner that needs to play catch-up.
Cool the iron in the water when it gets too hot.
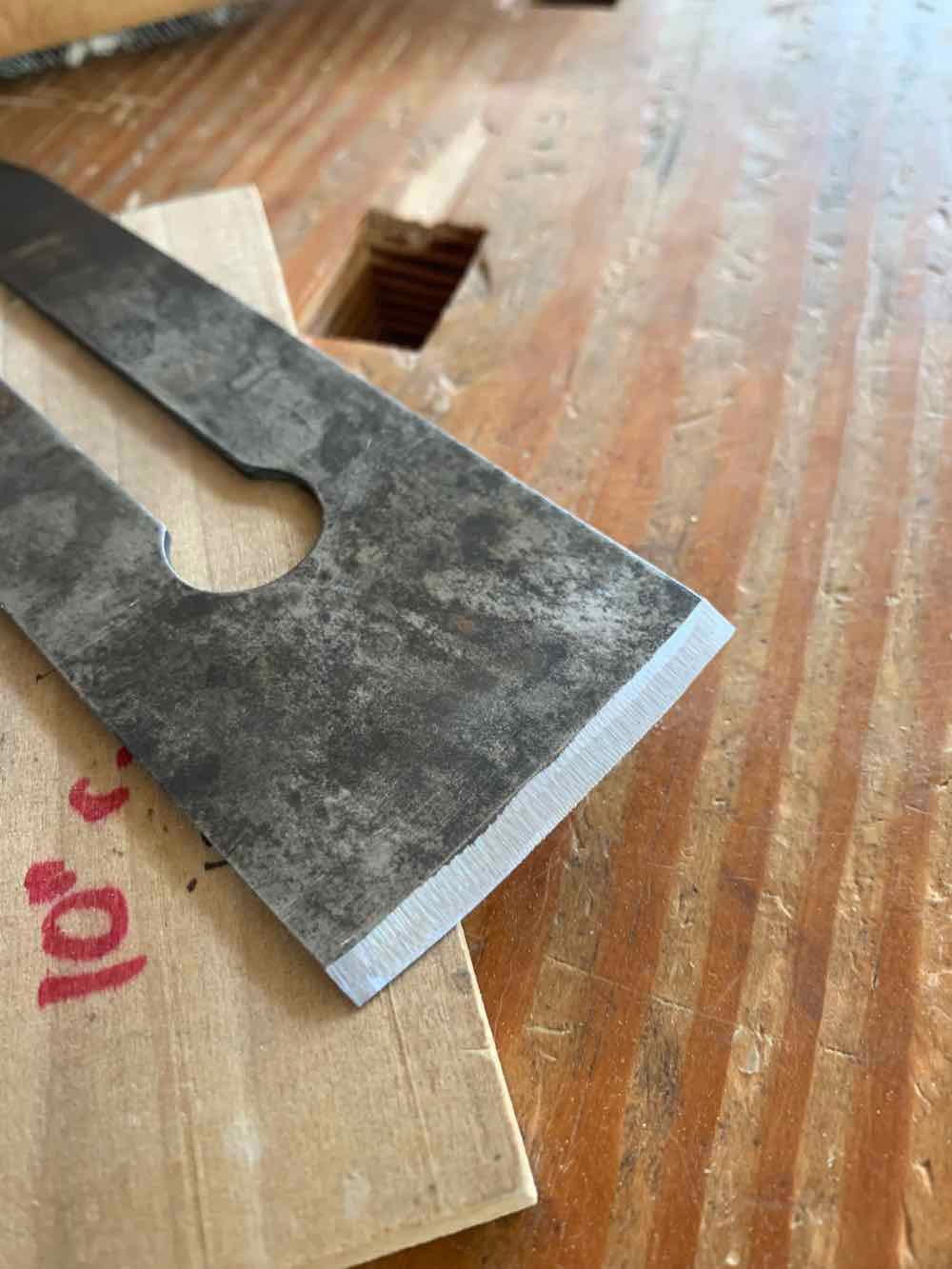
When the flats become tiny – about the width of a hair – you are ready to hone the iron. Try not to remove the flats on the grinder if you can. After the flats are gone, the tip of the iron will heat up rapidly.
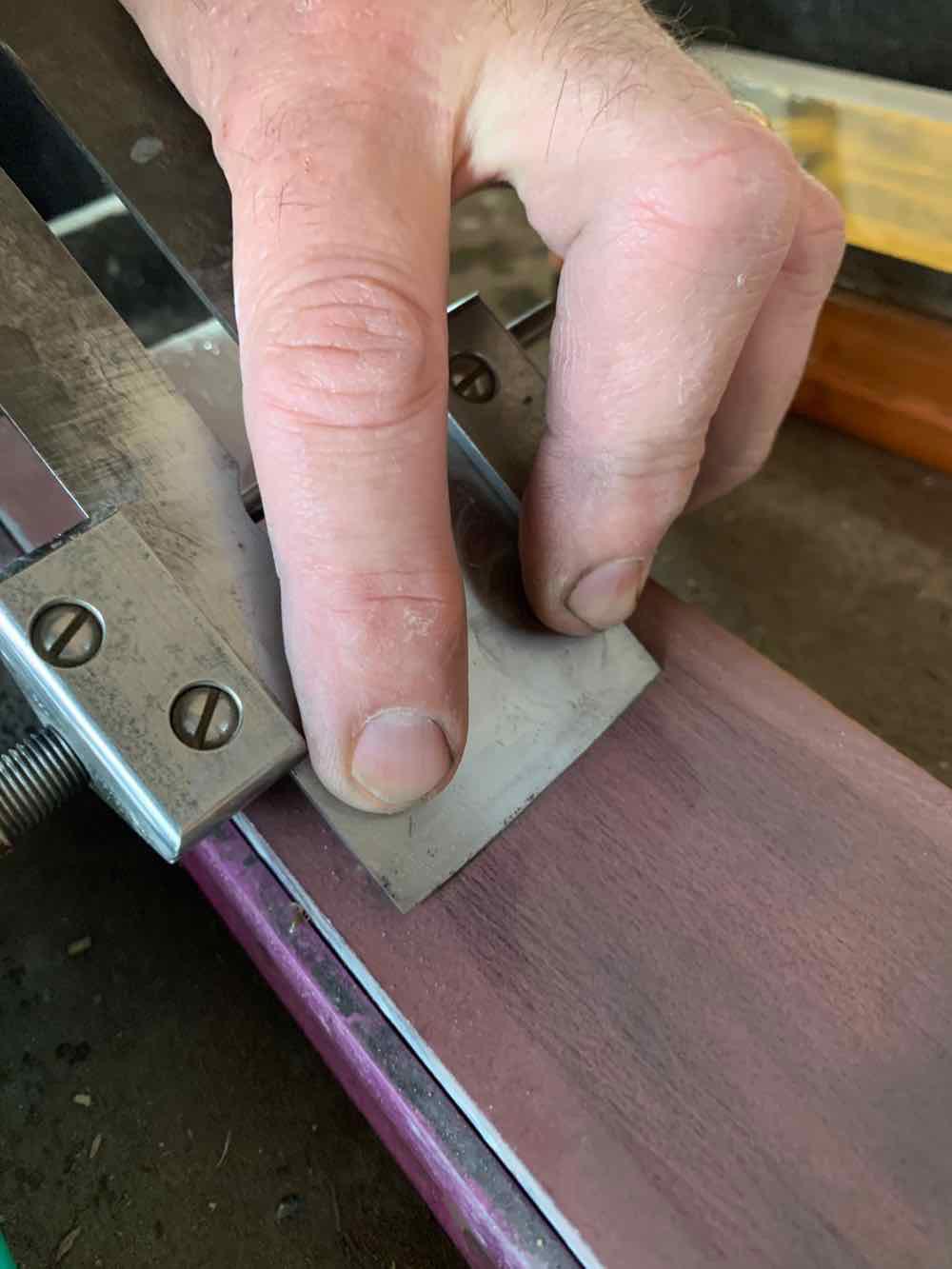
Honing
Hone the iron using the same media you use for your chisels and plane irons. I use a honing guide, which makes the process a snap. Secure the iron in the jaws of the guide and set it for 30° or 35°. I use 35°. This is where you might encounter problems with an 8” radius. On some guides you won’t be able to hone the corners of the iron because the body of the honing guide will hit the stone, denying you access to the corners of the blade. Switch to a 10” radius or sharpen the iron freehand.
Start on your coarse-grit stone (I use a #1,000-grit waterstone). Rock the iron left and right as you roll up and down the stone. Proceed until the flats are gone and you have created a burr on the backside of the iron. Then proceed up the polishing grits (I use #5,000 and then #8,000) to finish the bevel.
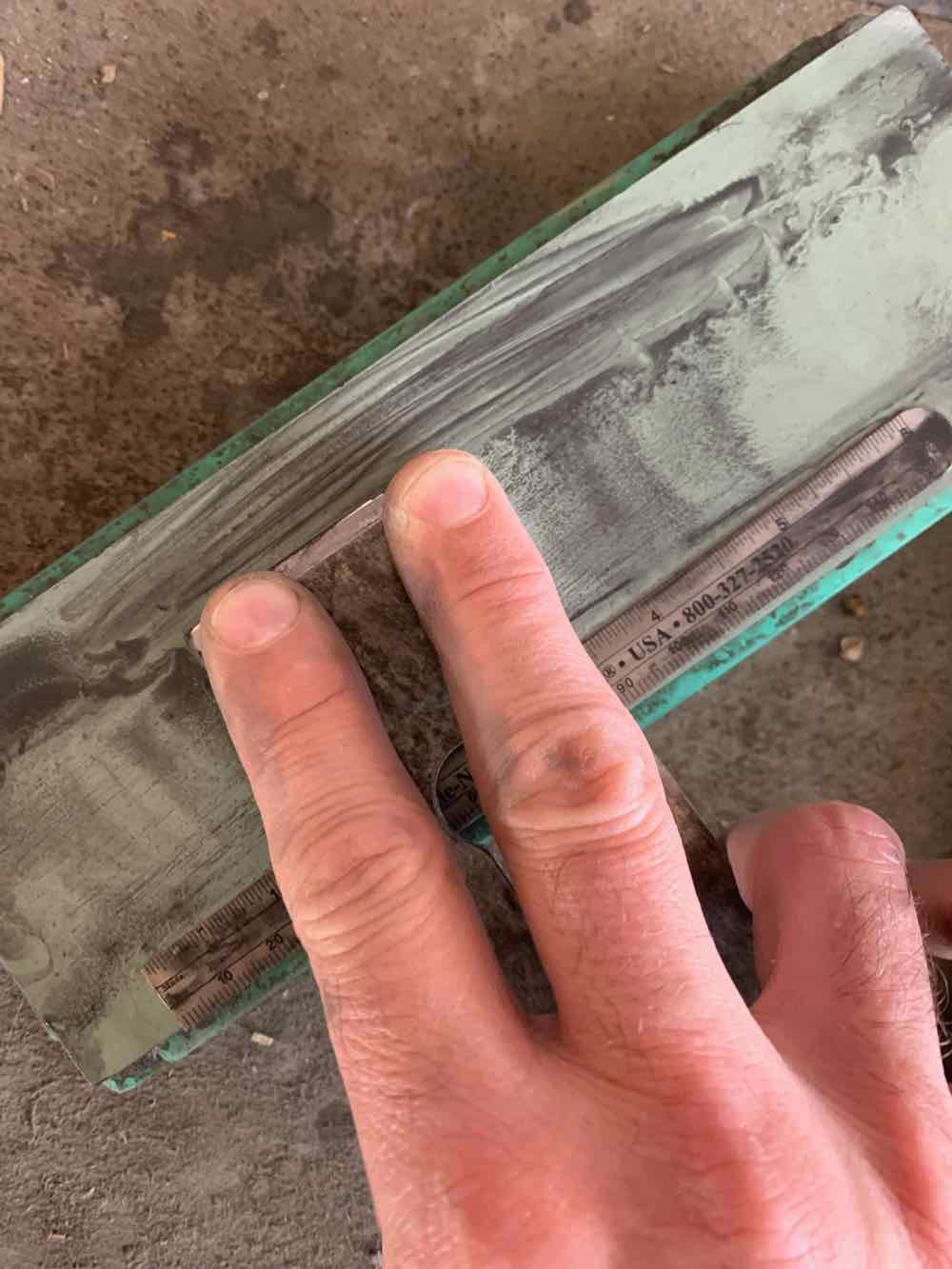
Remove the burr and polish the backside of the iron. I prop up the iron on a thin steel ruler (thanks David Charlesworth) so I only have to polish a tiny bit of metal at the tip. The first time you do this on an iron, it might take a minute or so, but that beats the heck out of the hours it would take if you had to polish the entire backside.
The Chipbreaker (aka Cap Iron)
Luckily the chipbreaker isn’t as critical to a jack plane as it is to a smoothing plane. It’s primary job in a jack plane is to attach the iron to the blade-adjustment mechanism in the frog. Plus, the hump of the chipbreaker helps deflect shavings up and out.
Still, you need to make sure that you don’t create a “shavings trap.” That happens when there’s a gap between the iron and breaker that is big enough for shavings to get into. Stone or file the underside of the breaker until you get a good light-tight fit between the breaker and iron.
One of the most common problems with old breakers is that they have flattened out a bit during the last 100 years and you need to restore their “spring.” To do this, clamp one-third of one end of the breaker in a vise and press gently but firmly against the un-clamped portion. You only need a tiny tiny bit of bend to fix the problem. It’s easy to over-do it. It’s also easy to undo it.
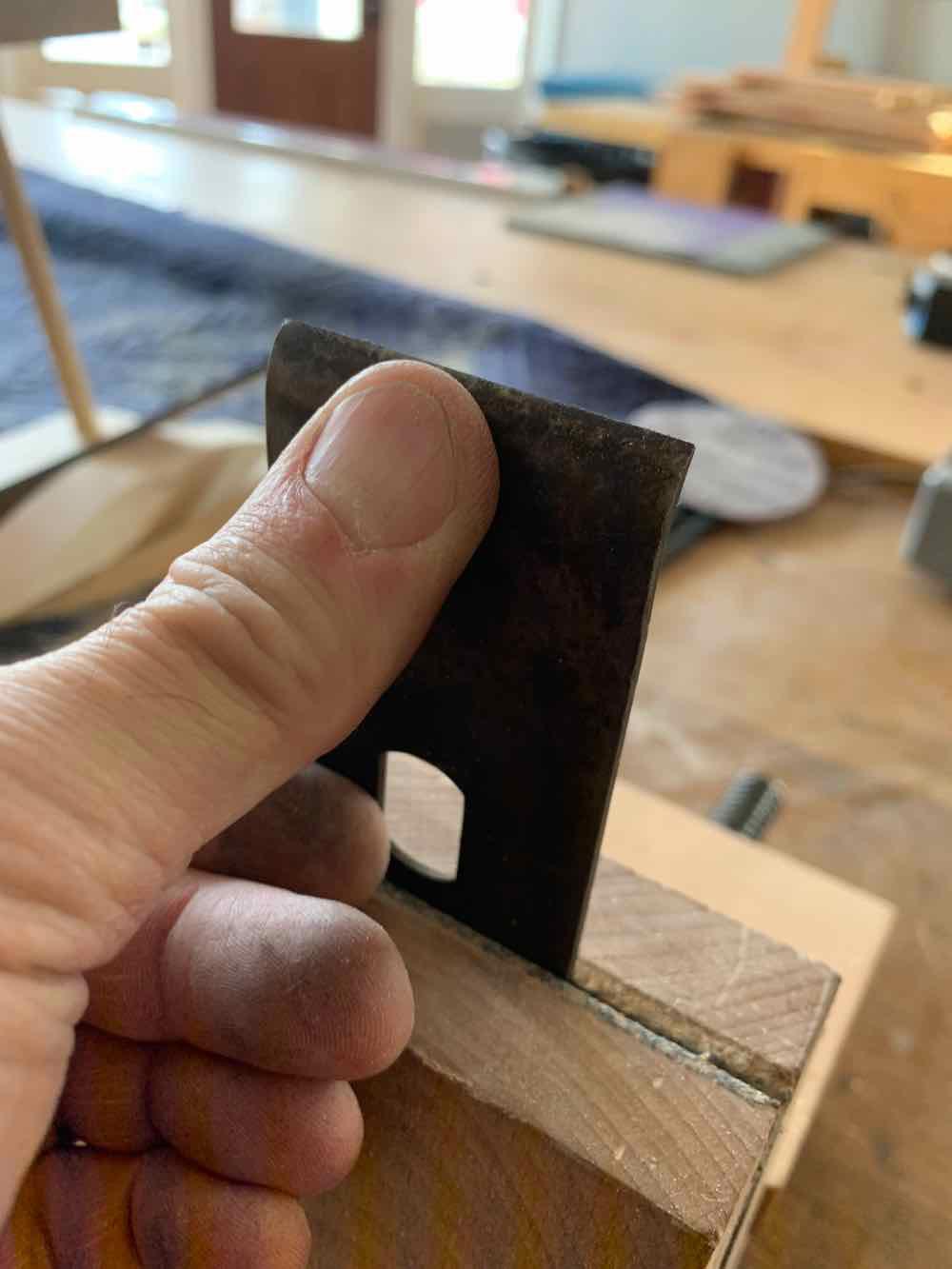
If you can’t get the breaker working no matter what you do, consider buying an aftermarket one from Hock Tools or Lee Valley. That will fix your wagon.
Now you can assemble the whole plane and make some shavings. Attach the chipbreaker so it is behind the curve of the iron, but don’t position it too far back – that can give you troubles. You can make it so that you cannot retract the iron into the mouth of the tool. Tighten the breaker snugly. Check the frog screws again to make sure they aren’t loose (I’ve done this).
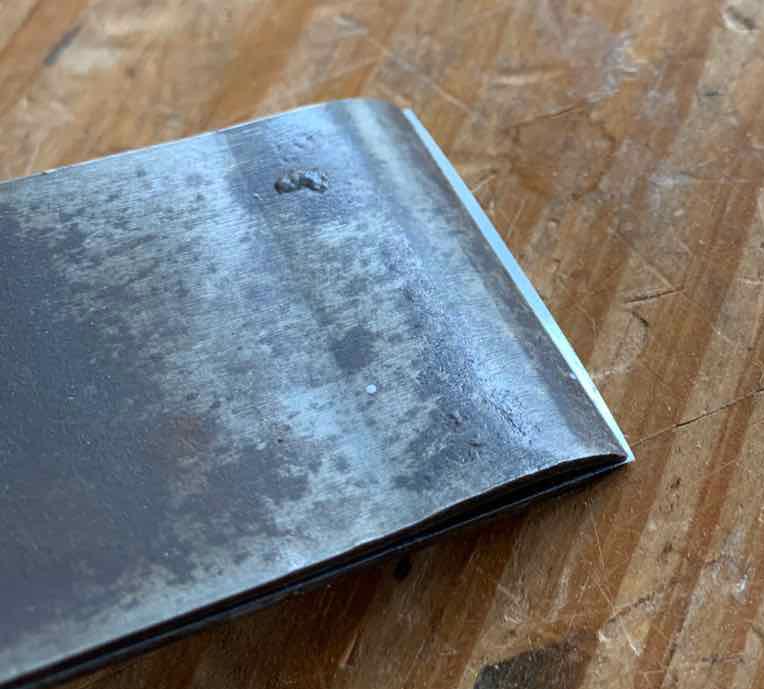
And assemble the plane. Yay.
In the next entry, I’ll show you how to make a board flat with a jack plane.
— Christopher Schwarz
The Jack Plane Series
The Jack Plane You Really Need: Part 1
Clean & True Critical Surfaces: Part 2
Grind the Iron & Fit the Chipbreaker: Part 3
Set Up & Use: Part 4
Like this:
Like Loading...