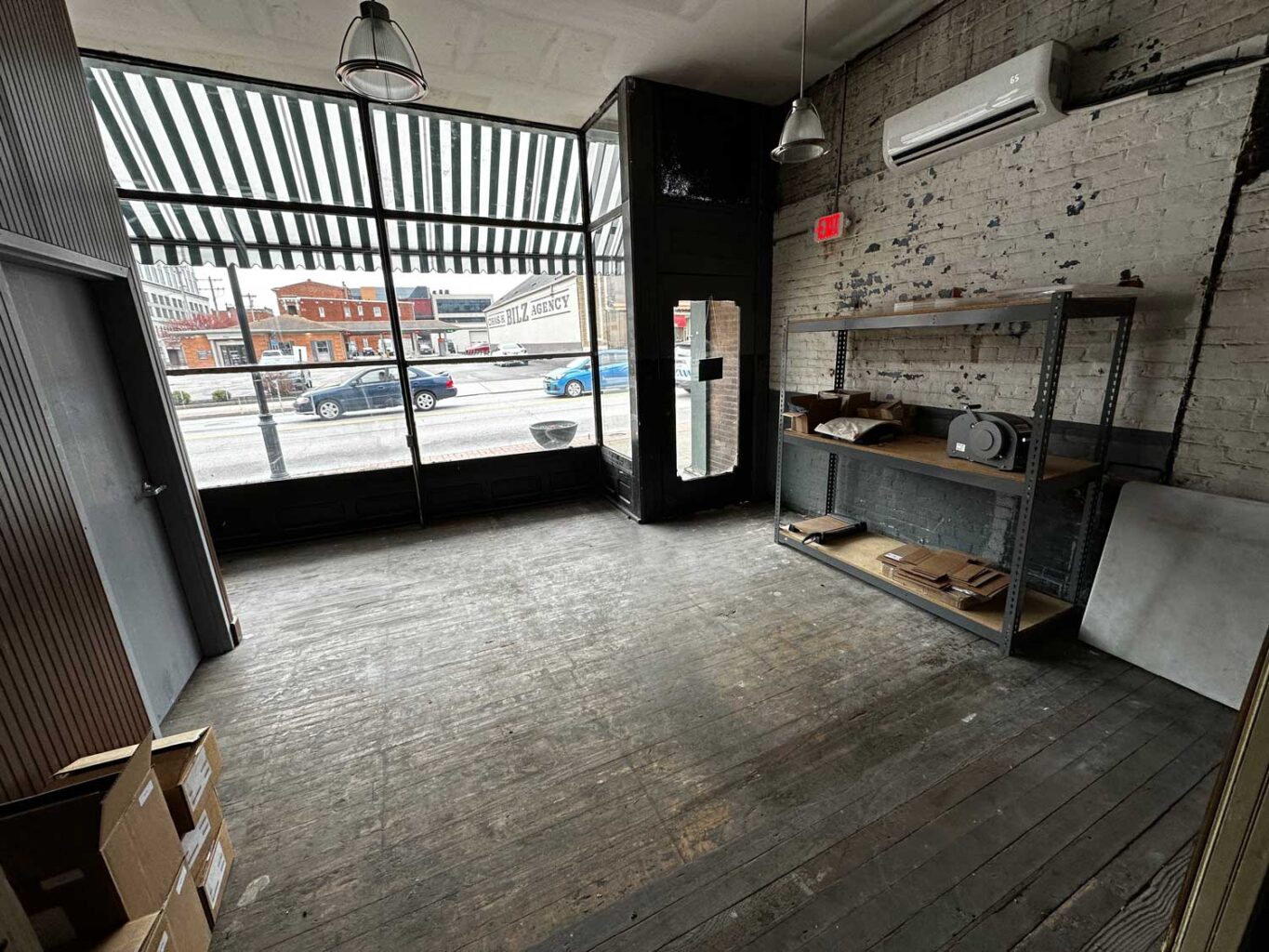
Our fulfillment center at the Anthe (pronounced Ann-thee) Building is now fully operational. The material lift has been repaired, the new roof is on, the skylight has been replaced, the back wall masonry has been rebuilt, and we have dehumidifiers on every floor – plus extra heating capacity to deal with the occasional cold snap.
The price: in$ane. Thank goodness John and I both have other ways to make money. Because Lost Art Press has primarily been paying contractors for the last 11 months.
Next month, John and his fulfillment crew will move the last of our inventory from storage units in Cincinnati and Latonia into the Anthe Building. If all goes well with that, we’ll have an opening day party for y’all (I hope you like Milwaukee’s Best and oyster crackers).
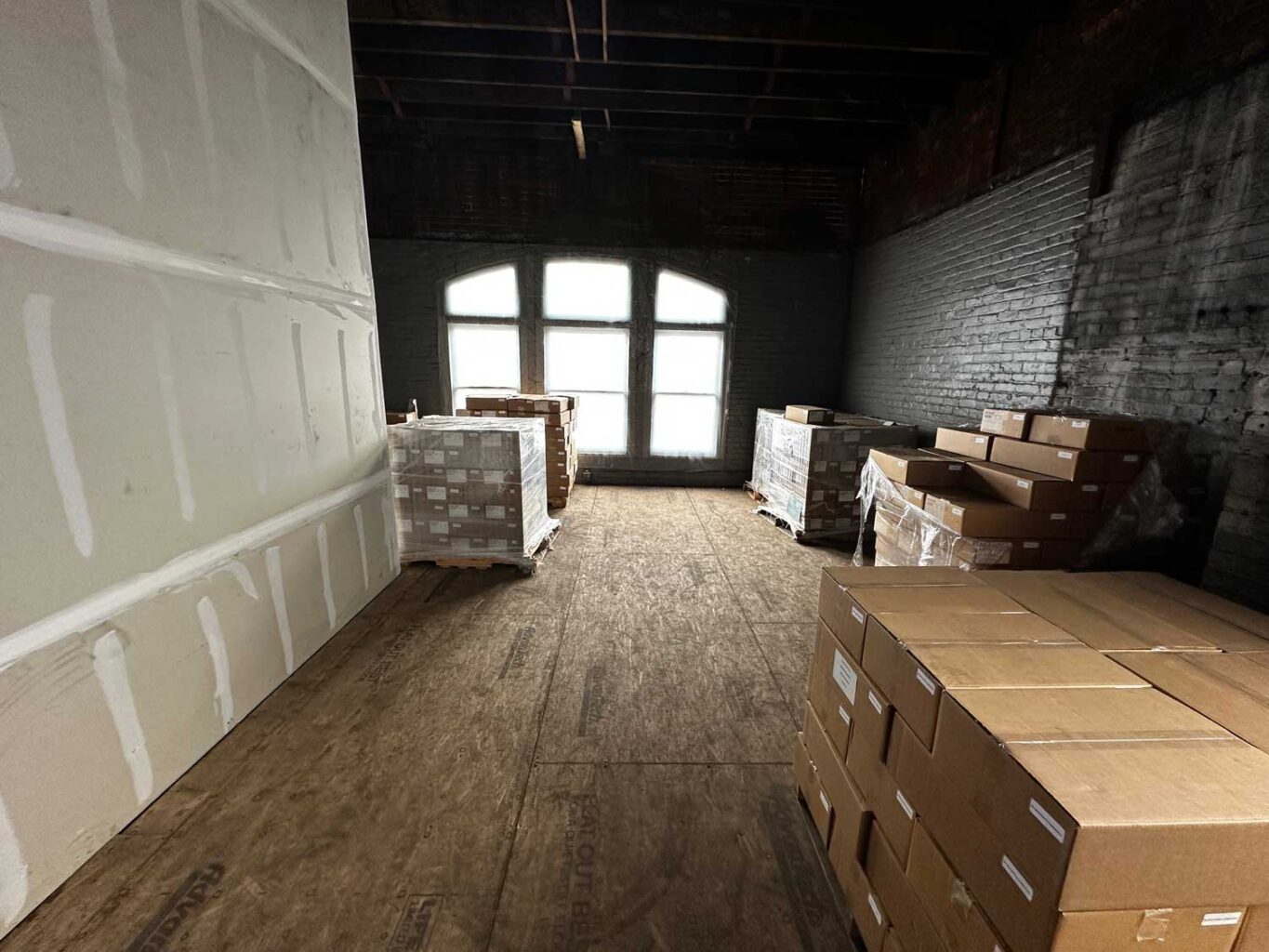
Now John and I can finally start looking ahead to what to do with the space. What is the next project? Restoring the exterior storefront? Getting a retail store up and running? Building a break room for fulfillment employees (probably this one).
This project has been the most stressful and difficult thing John and I have ever done together. If we could do it all over again, we’d probably do something different (a pole barn in unincorporated Kenton County would have been faster and cheaper). But for now, we’re just happy that the place is running and running well. John, Mark and Gabe have been getting orders out faster than our fulfillment house ever has. And we’re able to offer some signed editions and other niceties for customers that were once impossible.
So thanks to everyone who helped. Whether you bought a hammer, a class, a book or a bandana. Every penny helped.
— Christopher Schwarz