This is an excerpt from “The Woodworker: The Charles H. Hayward Years: Volume III” published by Lost Art Press.
Although framed panelling is not employed as much as formerly, it still plays a part in woodworking. Many homeworkers will use the method for a good class cupboard or wardrobe back, while the ever popular oak linen chest is, to most of us, unthinkable unless panelled.
There are a few points regarding panels and their grooves which are well worth thinking about. In the first place, see that the grooves in all the members of a frame are of uniform depth. The panels should be taken to size so that they are 1/16 in. less each way than the measurements taken between the groove bottoms. Thus, assuming that the grooves are 1/4 in. deep, the panels should be cut 7/16 in. more in length and width than the sight size of the opening. This allows 1/16 in. clearance, which ensures that when the frame is cramped up there shall be no pressure on the panels. If the depth of the grooves varies so that here and there the panels are without clearance, they will come in for some pressure when the joints are cramped up, and so may show hollow or round on the face.
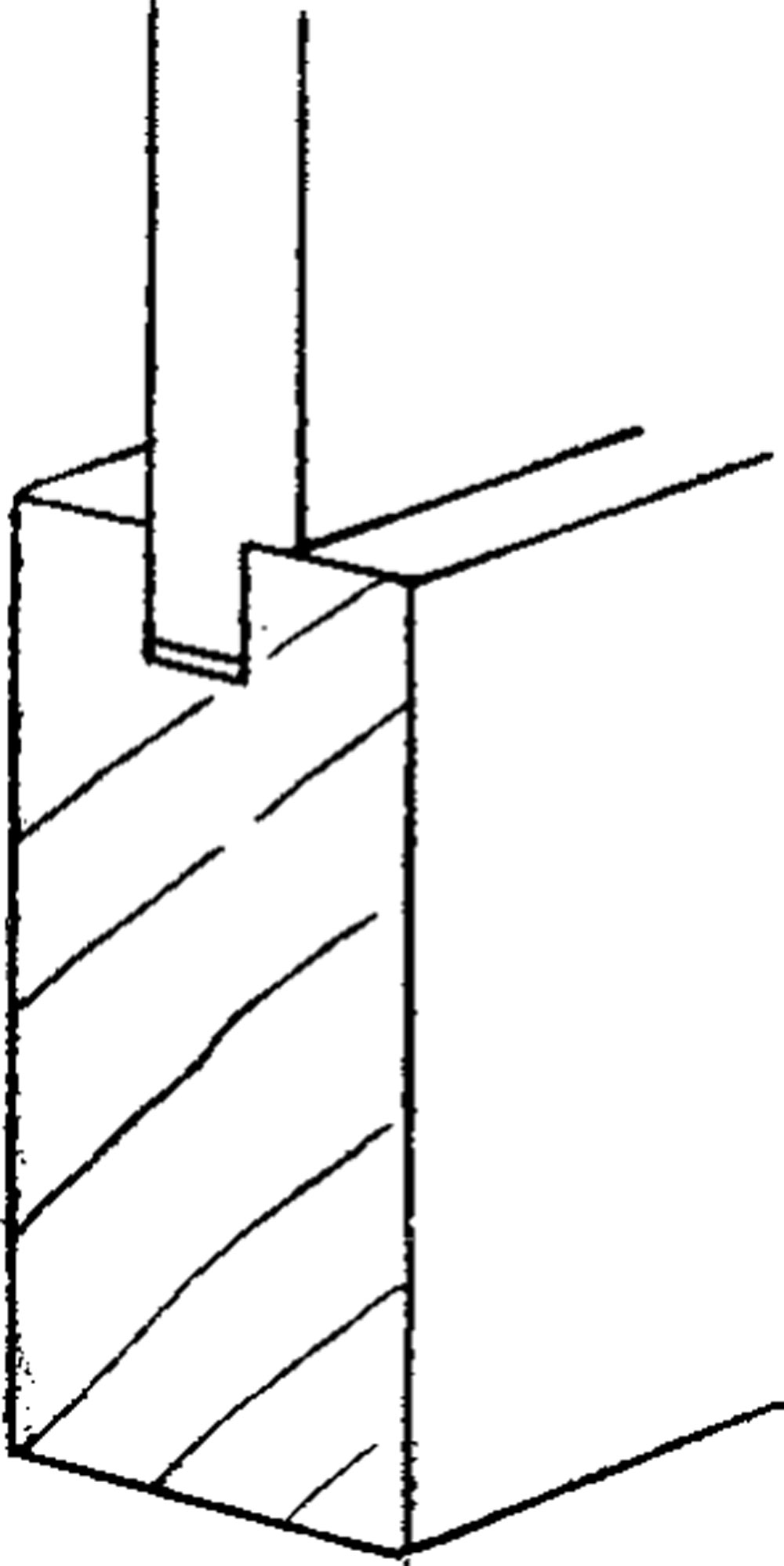
Mulleting
Then there is the matter of the width of the grooves in relation to the thickness of the panels. A panel should be a push fit in its grooves, no tighter and certainly no looser. Panels too tight often make it difficult to squeeze the joints up well; loose ones, with their movement and rattle, are an abomination.
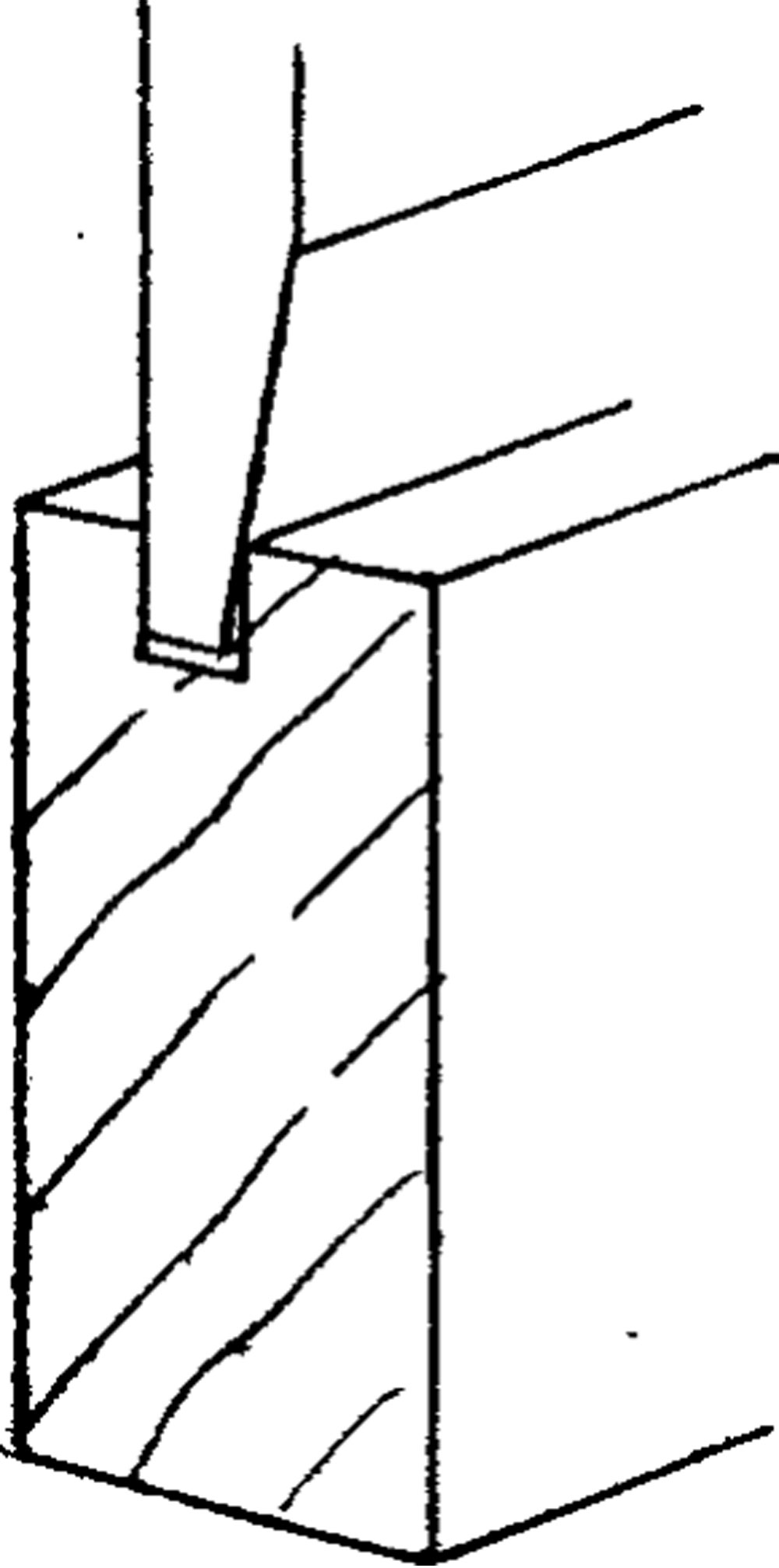
It sometimes happens that panels have to be fitted into grooves too narrow to receive them in their entire thickness. Thus they must be thinned at the edges. This thinning is called mulleting. A common method of mulleting a panel which does not need much thinning is shown at Fig. 1. It will be seen that the panel can hardly be said to fit into the grooves, since at the back it touches only the groove edge. Many workers dislike this method. But it must be admitted that, in the case of plywood panels (which do not shrink), it serves quite well. Solid panels, however, because of shrinkage across the width, would be likely to become slack in the grooves at their edges if mulleted in this way. Even so, if the stuff used for the panels can be relied upon to shrink but little, this may not amount to much.
A sounder job is illustrated at Fig. 2, where the panel is shown rebated. Here the panel does fit the groove and shrinkage cannot cause looseness. It takes a fair amount of time, however, to get an accurate fit of the rebates against the framing at the back. So, in the case of panels not seen at the back, it is a common practice to work the rebates well on, giving, say, 1/8 in. clearance between rebate and frame.
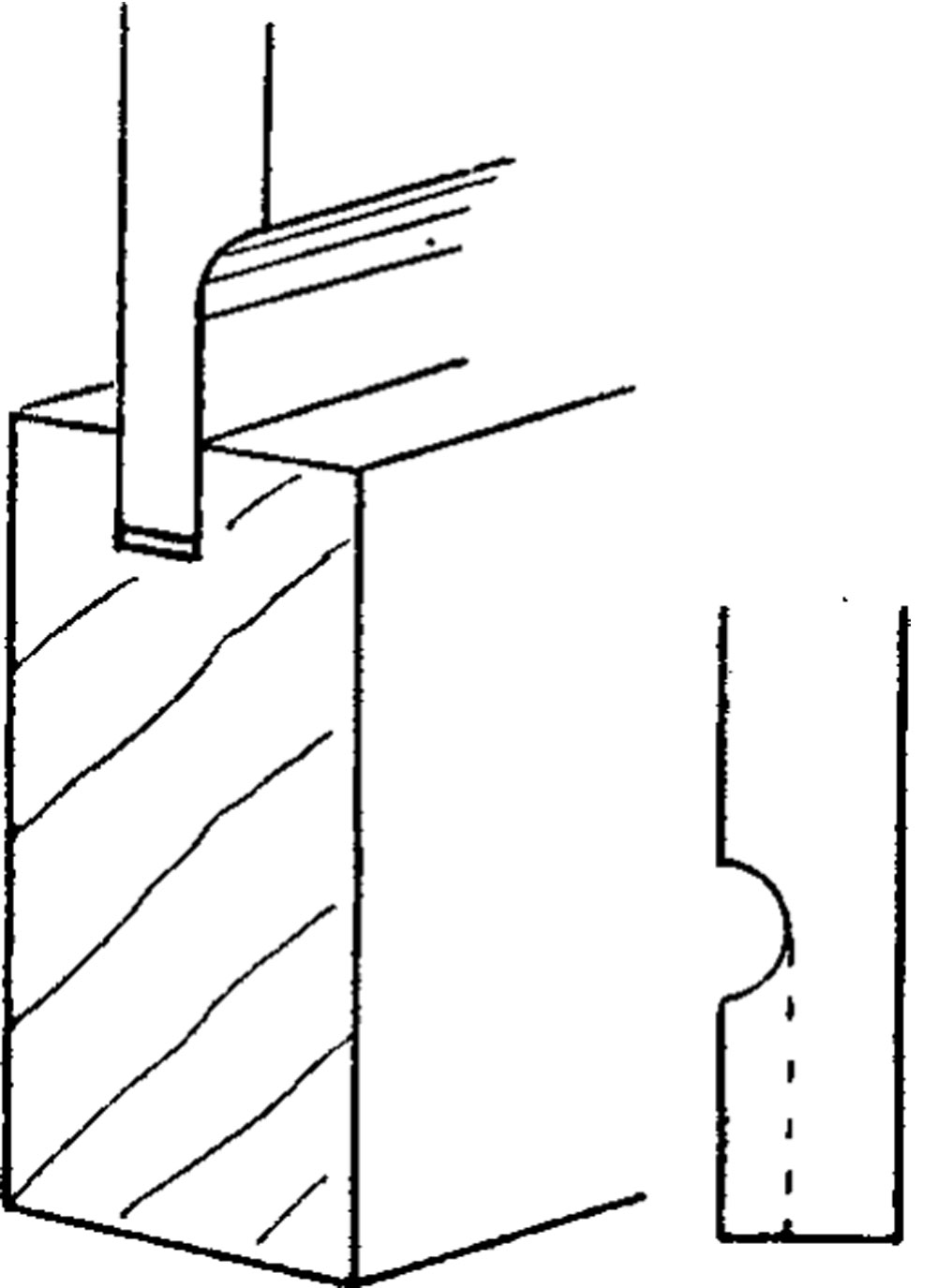
Fig. 3 shows the commonest machine-worked mullet. It is essentially the same as the rebated mullet, but the appearance is better. In fact, it is often employed on the face of panels, usually in conjunction with an ovolo moulding worked on the edges of the framing. To work this by hand, a plane that will make a small hollow (called a “round”) and a rebate plane are needed. Gauge on the edges the thickness to which the mullet has to be worked. Then work the hollow, as shown in Fig. 3, handscrewing or pinning a strip of wood to the panel to form a guide for the plane. It is also advisable to fasten another light strip to the left hand side of the plane to act as a depth gauge. After working the hollow, remove the waste down to the line (dotted in Fig. 3) with the rebate plane. If the mullet is on the face of the panel, take special care not to let the corner of the rebate plane iron dig into the hollowed part.
Never glue panels in their grooves. The idea of framing is to provide for shrinkage of panels. If this movement is prevented by glueing, the panels will probably split or, when jointed, crack along the joints.
— MB