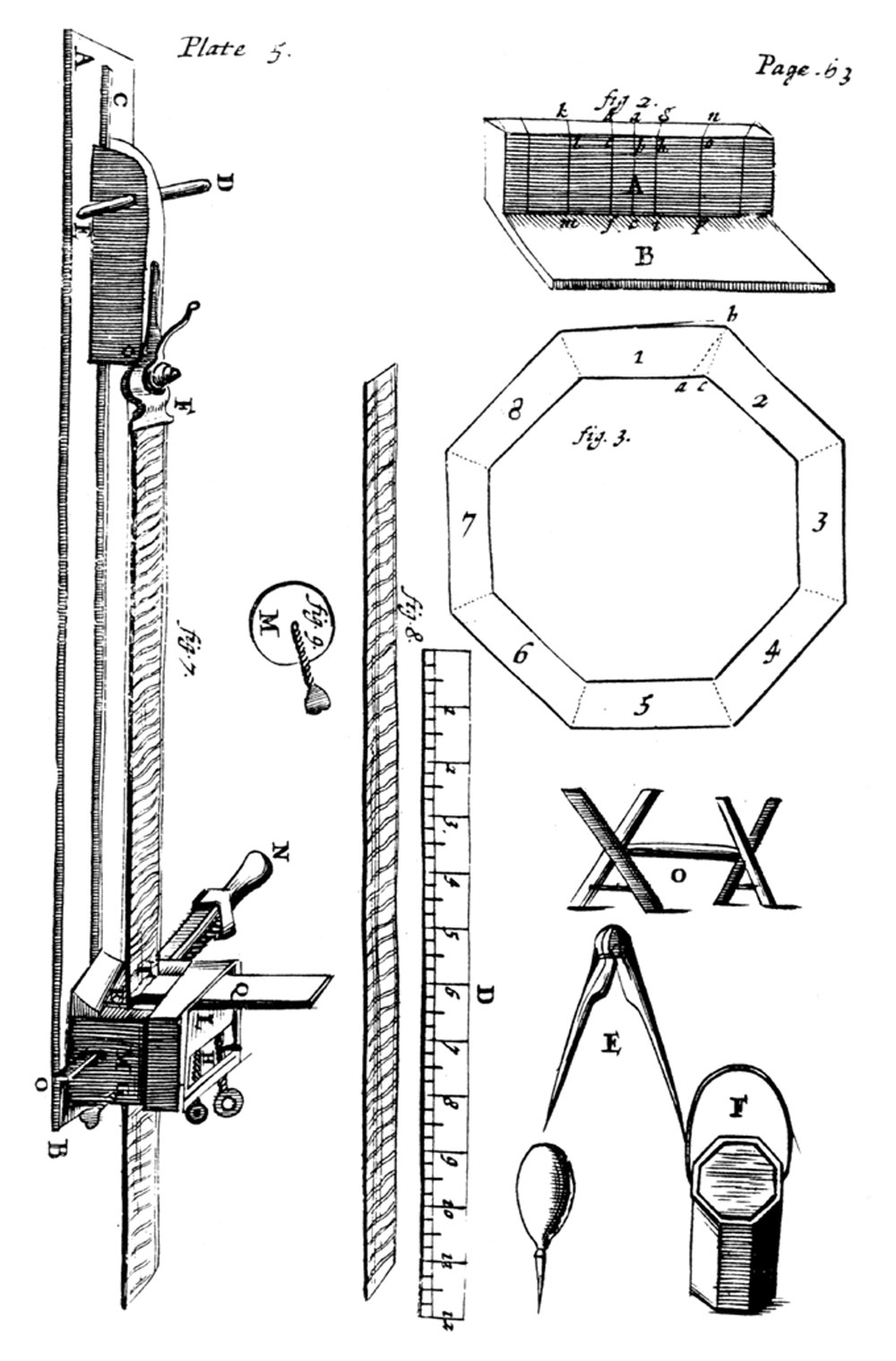
This is an excerpt from “The Art of Joinery” by Joseph Moxon; commentary by Christopher Schwarz.
The waving engine described in plate 5. fig. 7, hath A B, a long square plank of about seven inches broad, five foot long, and an inch and a half thick. All along the length of this plank on the middle between the two sides runs a rabbet [a raised track], as part of it is seen at C. Upon this rabbet rides a block with a groove in its underside. This block is about three inches square and ten inches long, having near the hinder end of it a wooden handle going through it [that is] about one inch diameter, as D E. At the fore-end of this block is fastened a vise, [that is] somewhat larger than a great hand-vise, as at F. The groove in the block is made to receive the rabbet on the plank.
At the farther end of the plank is erected a square strong piece of wood, about six inches high, and five inches square, as G. This square piece has a square wide mortise in it on the top, as at H. Upon the top of this square piece is a strong square flat iron collar, somewhat loosely fitted on, having two male screws fitted into two female screws, to screw against that part of the wooden piece un-mortised at the top, marked L, that it may draw the iron collar hard against the iron [that cuts the moulding], marked Q , and keep it stiff against the fore-side of the un-mortised piece, marked L, when the piece Q is set to its convenient height. And on the other side the square wooden piece is fitted another iron screw, having to the end of its shank fastened a round iron plate which lies within the hollow of this wooden piece, and therefore cannot in draft be seen in its proper place. But I have described it apart, as at M. {Fig. 9.} Its nut is placed at M on the wooden piece. On the farther side of the wooden piece is fitted a wooden screw called a knob, as at N. Through the farther and hither side of the square wooden piece is fitted a flat piece of iron, about three quarters of an inch broad and one quarter of an inch thick, standing on edge upon the plank; but its upper edge is filed round {the reason you will find by and by}. Its hither end comes through the wooden piece, as at O, and its farther end on the opposite side of the wooden piece.
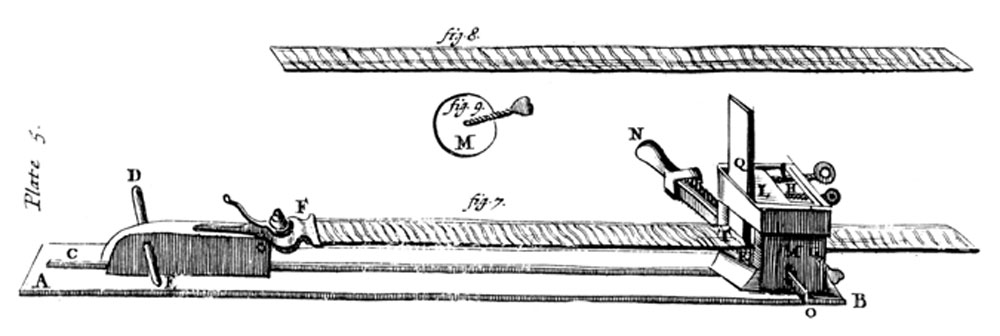
Upright in the hollow square of the wooden piece stands an iron, as at Q , whose lower end is cut into the form of the moulding you intend your work shall have.
In the fore side of this wooden piece is [a] square hole, as at R, called the mouth.
To this engine belongs a thin at piece of hard wood, about an inch and a quarter broad and as long as the rabbet. It is disjunct [distinct, unconnected] from the engine, and in fig. 8. is marked S S, called the rack. It hath its under[side] flat cut into those fashioned waves you intend your work shall have. The hollow of these waves are made to comply with the round edge of [the] flat plate of iron marked O {described before}. For when one end of the riglet [workpiece] you wave is, with the vise, screwed to the plain side of the rack, and the other end put through the mouth of the wooden piece, as at T T, so as the hollow of the wave on the underside of the rack may lie upon the round edge of the flat iron plate set on edge, as at O, and the iron Q , is strong fitted down upon the reglet [sic]. Then if you lay hold of the handles of the block D E and strongly draw them, the rack and the riglet will both together slide through the mouth of the wooden piece. And as the rounds of [the] rack ride over the round edge of the at iron, the rack and reglet will mount up to the iron Q , and as the rounds of the waves on the underside of the rack slides off the iron on edge, the rack and reglet will sink, and so in a progression (or more) the riglet will on its upper side receive the form of the several waves on the underside of the rack, and also the form or moulding that is on the edge of the bottom of the iron. And so at once the riglet will be both moulded and waved.
But before you draw the rack through the engine, you must consider the office of the knob N, and the office of the iron screw M. For by them the rack is screwed evenly under the iron Q. And you must be careful that the groove of the block flip not off the rabbet on the plank. For by these screws, and the rabbet and groove, your work will be evenly gauged all the way (as I said before) under the edge of the iron Q , and keep it from sliding either to the right or left hand, as you draw it through the engine.
Analysis
Of course, the No. 1 question you have to have about the “waving engine” entry is what the heck the thing actually does. Is it a planer? A moulding machine? Well, yes. It works like both a planer and a moulding machine to produce what are called rippled or waveform mouldings, which were all the rage during Cromwell’s reign in England.
Wave mouldings show up in many picture frames of the era and reflect light in a most unusual way – thanks to their undulations or ripples.
Moxon’s device seems complex from the description because he is writing about a thing that doesn’t exist in this exact form today. In essence, the waving engine produces rippled mouldings much like a duplicator lathe or a pattern-cutting bit in a router. A flat piece of iron follows a block with the desired pattern cut into it. This moves the stock against a fixed cutter, which gradually (very gradually) cuts away the waste to reveal the final wave shape in the workpiece.
The workpiece, by the way, is pulled through the waving engine by hand. If you are interested in this fascinating machine, I recommend you check out a 2002 article by Jonathan Thornton, who built a close reproduction of Moxon’s waving engine and shows how it developed into a fancier machine that worked with a crank. It’s easily available in pdf format from Stanford University’s web site for the Wooden Artifacts Group (http://aic.stanford.edu/sg/wag/authorindex.html).
— by MB