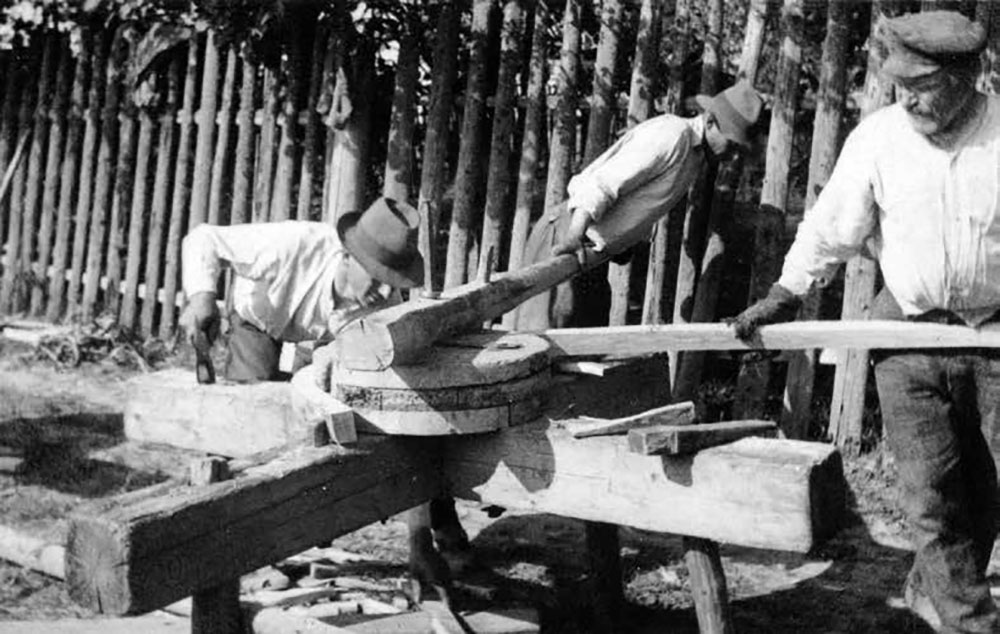
This is an excerpt from “Woodworking in Estonia” by Ants Viires; translated by Mart Aru.
Unsegmented felloes in Estonia and Latvia were always bent from ash wood. In Russia too, ash was occasionally used, although oak and elm were preferred. The Assikvere wheelright used ash also for the hub and the spokes.
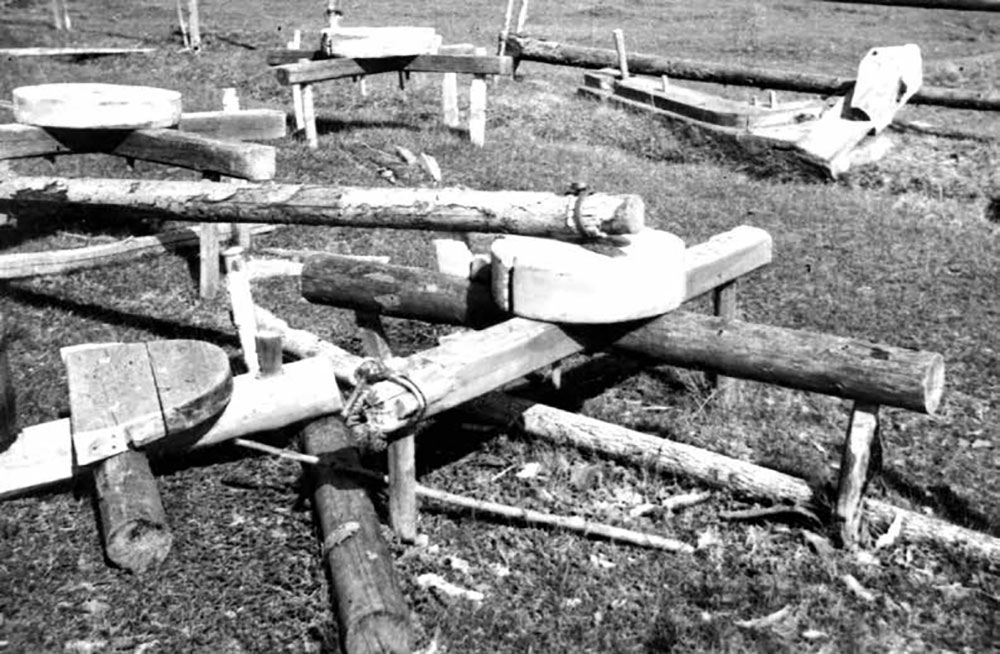
Here we will describe the process of unsegmented felloes as it was practiced until recently in Assikvere. Young ash trees had to be used for bending, the thinner ones yielding four boards and the thicker up to 12 boards. In order to make sure the suitability of a tree for felly making, a notch was cut into the trunk with an axe. If the piece of wood came out whole, the tree was no good for wheel making. When cutting wood for the front wheel, the length of the trunk had to be 8-1/2′ (2.5 m) and for the rear wheel 10-1/2′ (3.1 m). The boards were cut with an axe and wedge and then trimmed and smoothed. The width of the board before bending was about 2-1/4″ inches and it was 1-3/4″ – 2″ thick (5.7 cm x 4.4-5 cm).
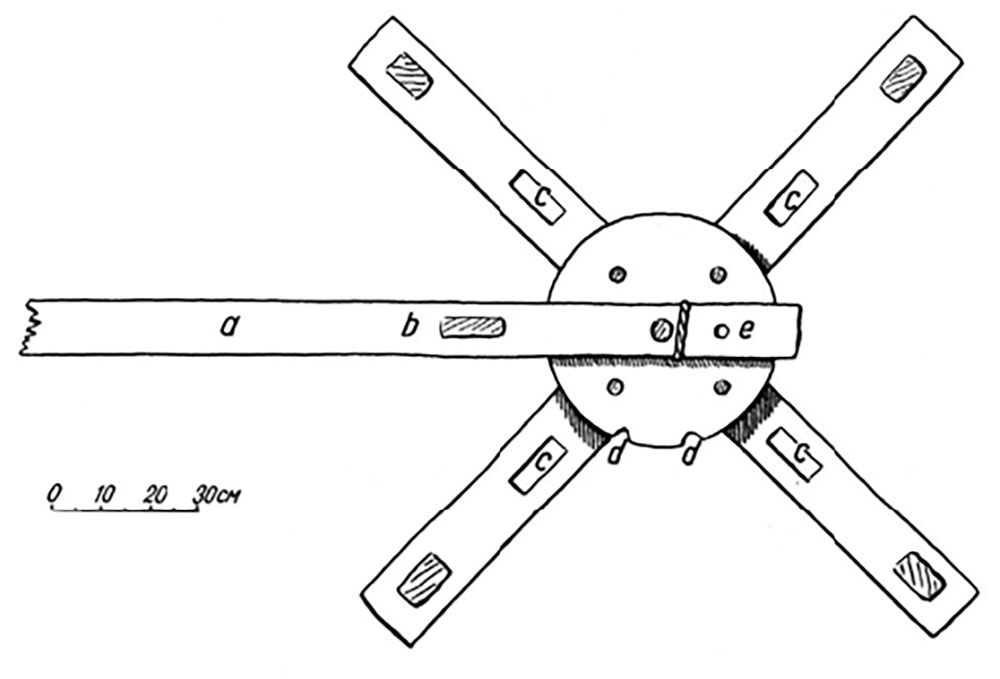
The green boards thus chosen were steamed or heated for about two hours. Bending on the wheel bench was done while the boards were still hot. A large wooden circular mold was used for the front wheels and a somewhat smaller one for the rear wheels. This circular block of wood was attached to a cross-like base (Figs. 175, 176) to which the end of the board was secured before starting. Bending was carried out by three persons (Fig. 177); they were described humorously, according to their functions as the “pushing boy, wedging boy and pulling boy.” The pushing instrument, or the bow, is a pole between 6-1/2′-9- 1/2′ (2-3 m), where it is mounted on a metal pushing pin. The latter is held in position by a strong wedge. In working the bow (or the pole), the pushing boy forces the board round the bending block with the aid of the wedge. The operation has to be performed evenly, without moving the pole up or down. The wedging boy moves the wedge as the board is bent, and inserts it into the appropriate hole in the cross-like base of the bending block. Sometimes an additional wedge is driven in for firmness. The pulling boy goes in front and guides the board, making sure of the board’s direction round the block. When the circle is completed, the pulling boy and the wedging boy join the ends with two pieces of birch. An additional board is now used to join the ends of the bent felly from the inside, it having been previously steamed or heated together with the board for the felly proper. It is a job of the wedging boy to hold the ends tightly while the pulling boy attaches the inside joining board. Only then may the pushing boy release the pressure. During the bending the ash board may often “crack with the inner ring,” i.e. , along the inside of the annual circle. If the crack is thin and the wood remains sufficiently thick it is still fit for use.
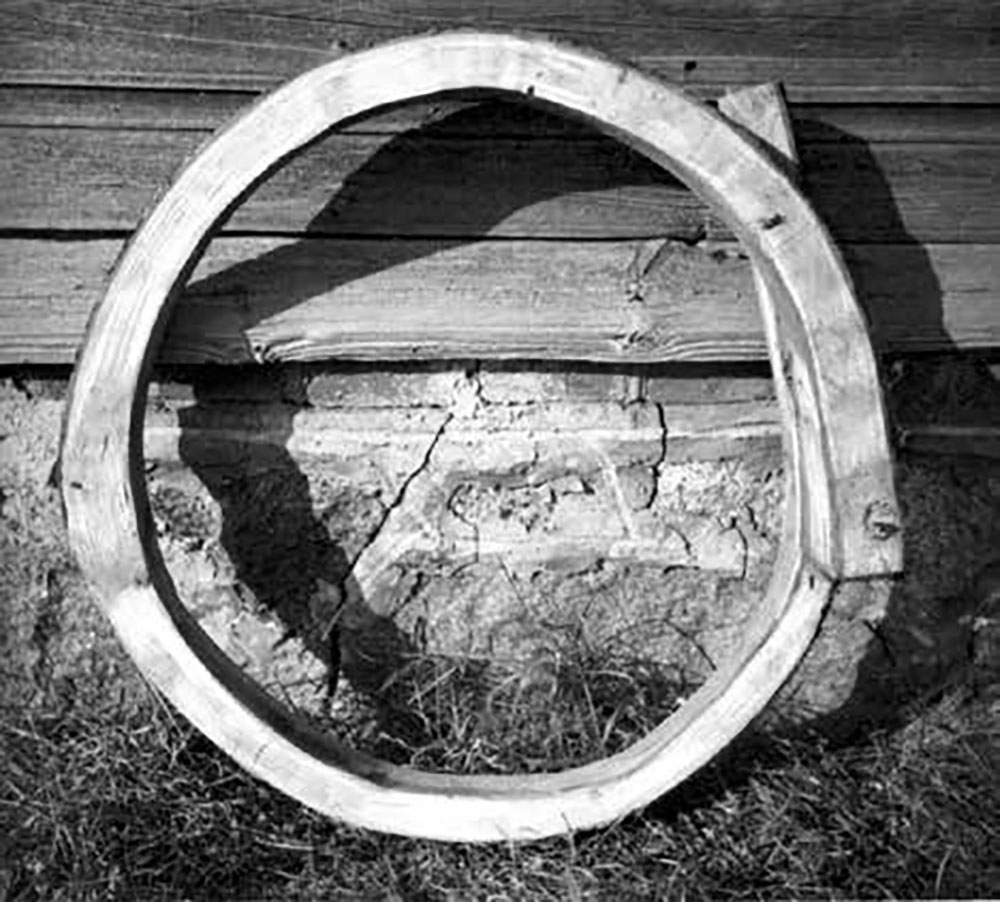
Before proceeding with processing the curved unsegmented felly (Fig. 178), it has to dry in a room for at least one week. After it has dried the ends are sawn off, so that a space of about 1/2″ (1.2 cm) is left between them. They are later pulled together by the smith with an iron band.
— Meghan B.