People gripe about traveling abroad, especially for work. I don’t get it. Here is how it’s done.
1. Take yourself on a “date.” Jet lag is easy to conquer with modern chemistry. I tell people that I give myself a “roofie” before I fly across the globe. First I take myself out for a nice dinner – in this case an overheated Mexican craphole in a New Jersey airport. And I order extra salsa – in this case they brought ketchup.
Then I get myself a nice girlie drink, the ones that come with either a paper umbrella or a glittery tube top. And, after telling myself how irresistible I am, I slip myself a few pills while I’m not looking. Two ibuprofen and two Benadryl.
With the help of this concoction I can sleep all the way across the Atlantic while a 6-year-old ninja goes all Donatello on the back of my seat.
2. Don’t nap. When I land I behave like I’m on local time. I stay up as late as I can the first day I am there and crash hard. After that, the trick is to never stop swimming.
3. Embrace everything. When I teach, I always round up the students to go out in the evenings to get dinner and a couple of drinks. We usually enlist a local to help us find a cheap dive with good food, good beer and a goodly amount of patience with loud-mouthed woodworkers. Tell bad jokes. Stay up too late. Crash hard. Repeat.
And never say “no” when you are invited to do something with the locals. The best way to see a new place is through the eyes of a resident. The worst way to see it is from the seat of a tour bus.
The week I’ve been at Warwickshire College, teaching a class in building “The Anarchist’s Tool Chest” for the New English Workshop. We’re in a nice little town called Leamington Spa outside Birmingham. The place is awash in Georgian architecture, quaint little shops and just enough pubs to get us into trouble.
It has been a remarkable week for many reasons.
This is my first course in England and the first course for New English Workshop. It’s a great little company run by Derek Jones and Paul Mayon that seeks to really honestly and truly prop up the craft.
Here’s one example: The tool chest I’ve built for the course will be auctioned off by David Stanley Auctions while it is full of incredible tools donated by toolmakers all over the world (Karl Holtey, Veritas, Bad Axe Toolworks and many others – a complete list to come). All the proceeds from that auction will go back to Warwickshire College to support its furniture-making program.
I’ll have more details on the auction as we get closer to the date.
As a nice gesture, I had all 18 students sign the underside of the tool chest. That should confuse some future tool collector.
The other great thing about the course has been getting to know the students, many of whom I’ve corresponded with via e-mail. One of the highest of the highlights was getting to meet Kieran Binnie, a luthier, woodworker, music lover and history nut.
Kieran runs the Over the Wireless blog, where he discusses woodworking, building guitars and martial arts and somehow blends them all into a very interesting and readable mix. Oh, and his guitars are gorgeous. Do subscribe to his blog. And read more about Kieran on Chris Hughes’ blog at Artifact Bag. And check out this Telecaster he built. Must. Resist.
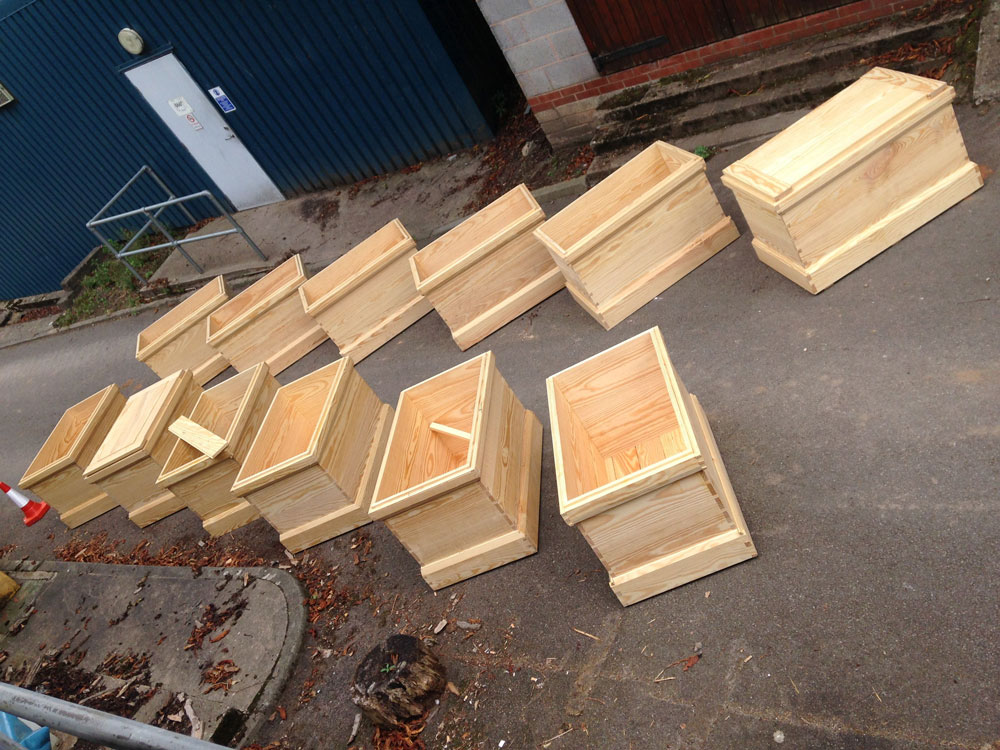
As we loaded up the 18 students’ chests today, I marveled that we got so much work done in only five days (and without a single stomach pumping and only one instance of barfing). When woodworkers build a serious tool chest it is usually the point where they give themselves over to the craft. You can see that after five hard (nay, brutal) days of dovetailing under extreme time pressure, that each person has become a little different. And it’s not just the odd smell.
Building such a difficult piece in a short period of time gives them the confidence they can do a lot of other things in the craft. And it can be done quickly and precisely.
So this blog entry has gone on far too long. I’ve got another date tonight. This time with a pillow and an unplugged alarm clock.
— Christopher Schwarz