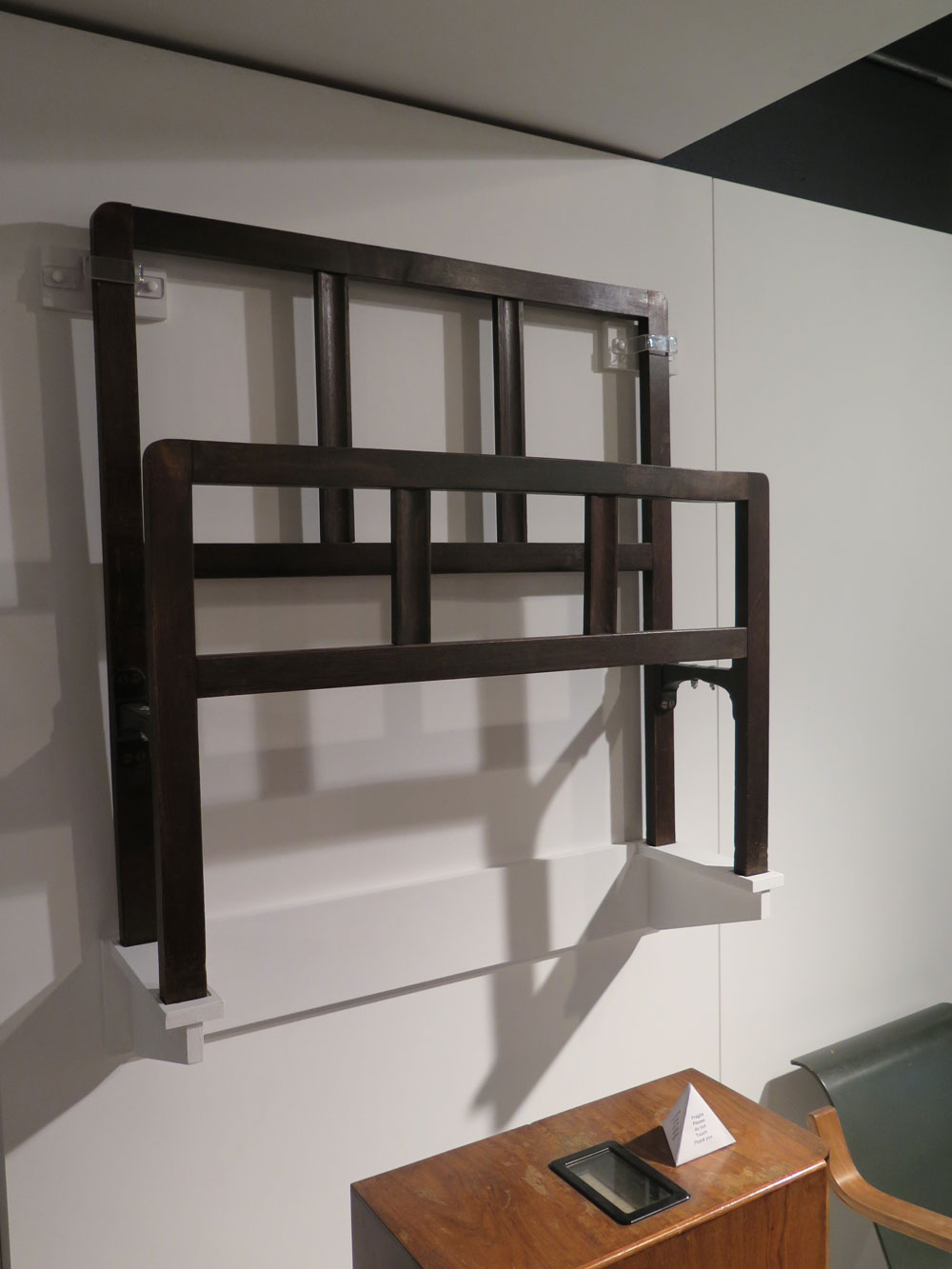
Perhaps one of the most testing times of furniture-making was that of war time and the immediately following years, when utility furniture came into being. Certain restrictions had to be placed on the methods of construction and the weight of timber used. It was realised that the items had to be reasonably durable, but the stringent requirements of the times made it necessary to keep timber sizes to the minimum. At the same time, although all unnecessary weight was avoided, there was a limit below which furniture would be unsound.
Compared with furniture of the Victorian and earlier periods, utility furniture was lightly built, but most people today have come to realise that much early furniture was unnecessarily heavy, and that in some ways lightness is a virtue providing that strength is adequate.
A problem that confronts the man in the home workshop is that of the thickness and width he should make the various parts. To the furniture designer or craftsman the decision is largely one of appearance only, because over the years a tradition has grown up in which the sections are more or less settled within certain limits.
If this sounds like blindly doing a thing for no better reason than repeating what was done before, it should be remembered that trade practice is generally founded on what experience has shown to be sound. Sometimes you can get away with slighter material, but it is often because you have to, either because the cost is too great otherwise, or because larger stuff is not available.
In any case we have to realise that, except for first-quality things, furniture today is not built for posterity as it used to be. The day when furniture was intended to be handed down to later generations has largely gone. Ask any young couple of today whether they want to start their home with things from the home of their parents, and you will invariably be told that such old-fashioned stuff does not interest them. Perhaps they are right. If the true craftsman dislikes the idea of making a thing that is not intended to last, at least the younger generation is entitled to its view of what it wants.
— Charles Hayward, from The Woodworker, February 1961