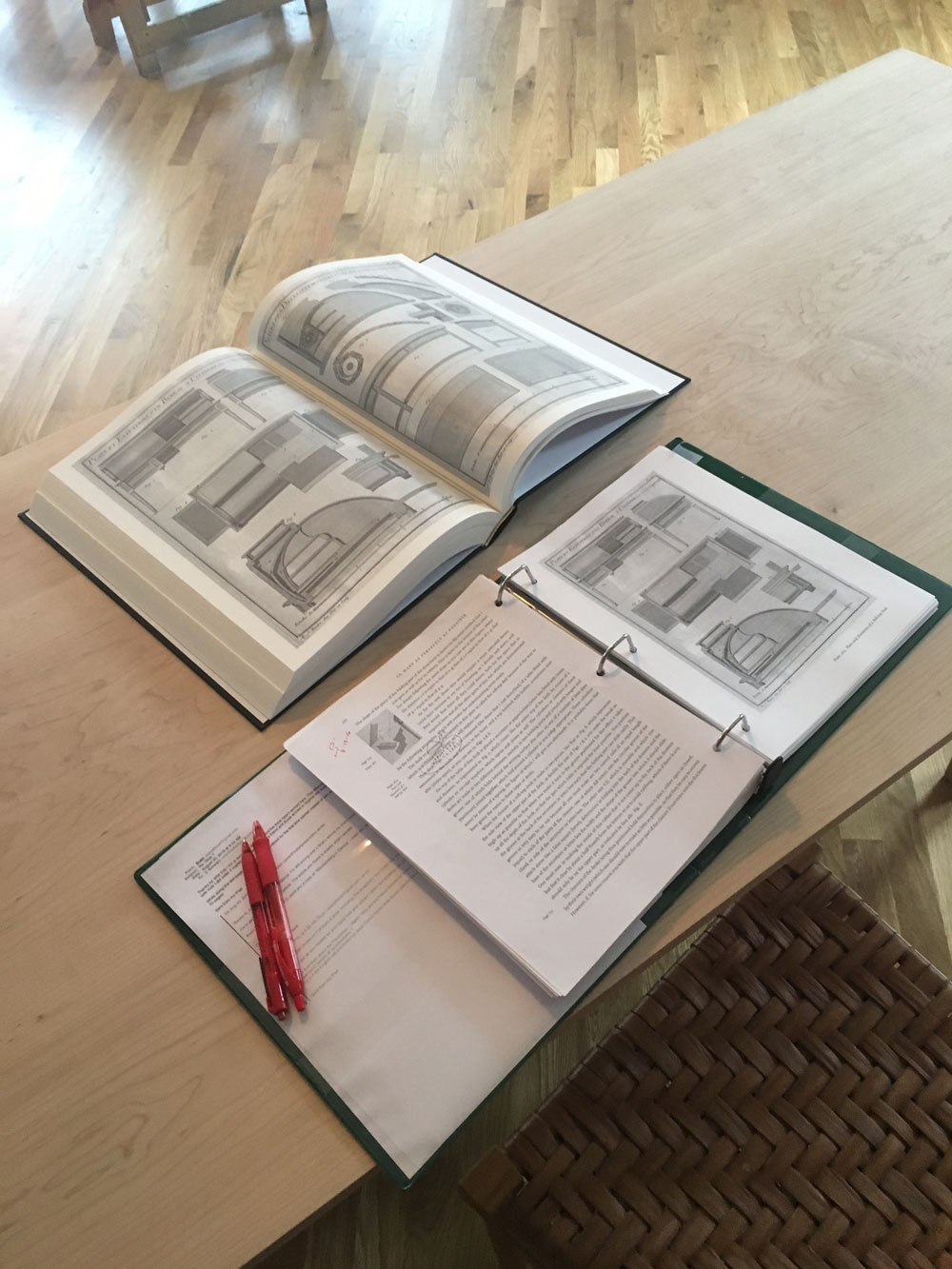
The vast majority of the headaches I’ve suffered in my life have been caused by one thing: editing.
Though it might seem like fun – sitting down and reading hundreds of pages of writing about woodworking – I assure you it’s a lot like working. So I am grateful to the men and women who showed up last Saturday to help us edit “To Make as Perfectly as Possible: Roubo on Furniture.”
The amateur editors found lots of typos and even a few mistakes made by Monsieur Roubo in the original text. We ate donuts, drank cream soda (thanks Eric!), ate pizza and drank beer. All these things help the editing process, but they still can’t mask the fact that it’s a slog.
As a result of their efforts we are on time with getting this book to the printer in September and in your hands in November.
We asked everyone who helped out to write down his or her name. Some people did; some people are clearly hiding something from the authorities. Here are the editors:
Jared Wilcox
David Pruett
Greg Jones
Rick Stillwater
“Handsome” Chris Decker
Scott Stahl
Mike Hamilton
Rosalie Haas Pruett
Mike Ham: Hon
Matthew Conrad
Jen Neiland
Ryan Fee
Brad Daubenmire
Charles Thomas
Megan Fitzpatrick
John Hoffman
If I’ve misspelled your name, it’s only because your handwriting sucks eggs. Mine is, of course, even worse.
Thanks again everyone. I think we will do this again with future books. It really helped.
— Christopher Schwarz
Like this:
Like Loading...