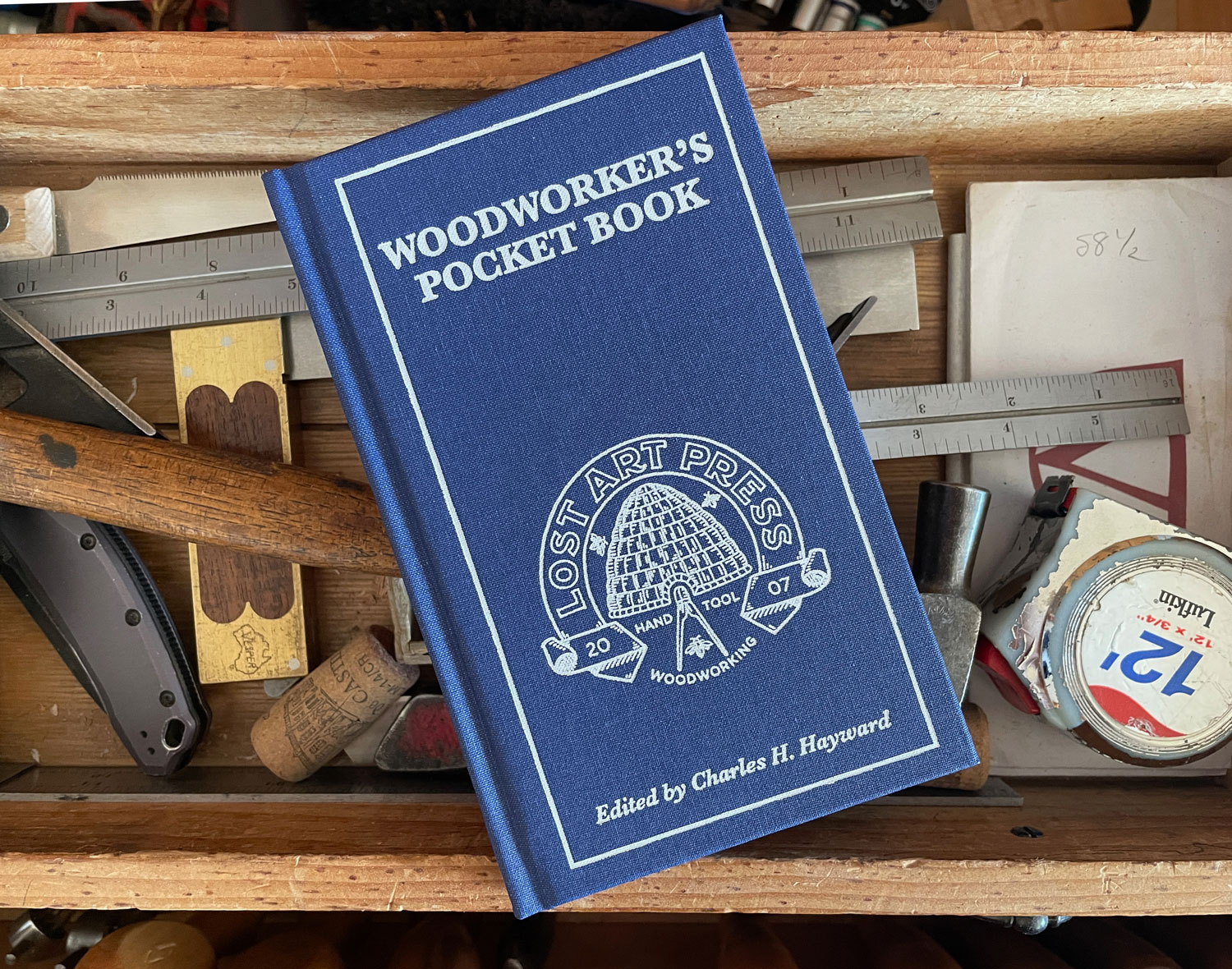
Earlier I joked that it would take a space squid invasion to again delay shipment of “The Woodworker’s Pocket Book.”
Looks like I better start brushing up on my cephalopod language skills.
The bad news: Shortages of cotton cloth for the cover made us change course in the manufacturing process three times. We were finally able to get a good supply of a new brand of cotton cloth shipped to the printing plant. And, after delay because of Southern snowfall, the books are now being packed up in Tennessee to travel to our Indiana warehouse.
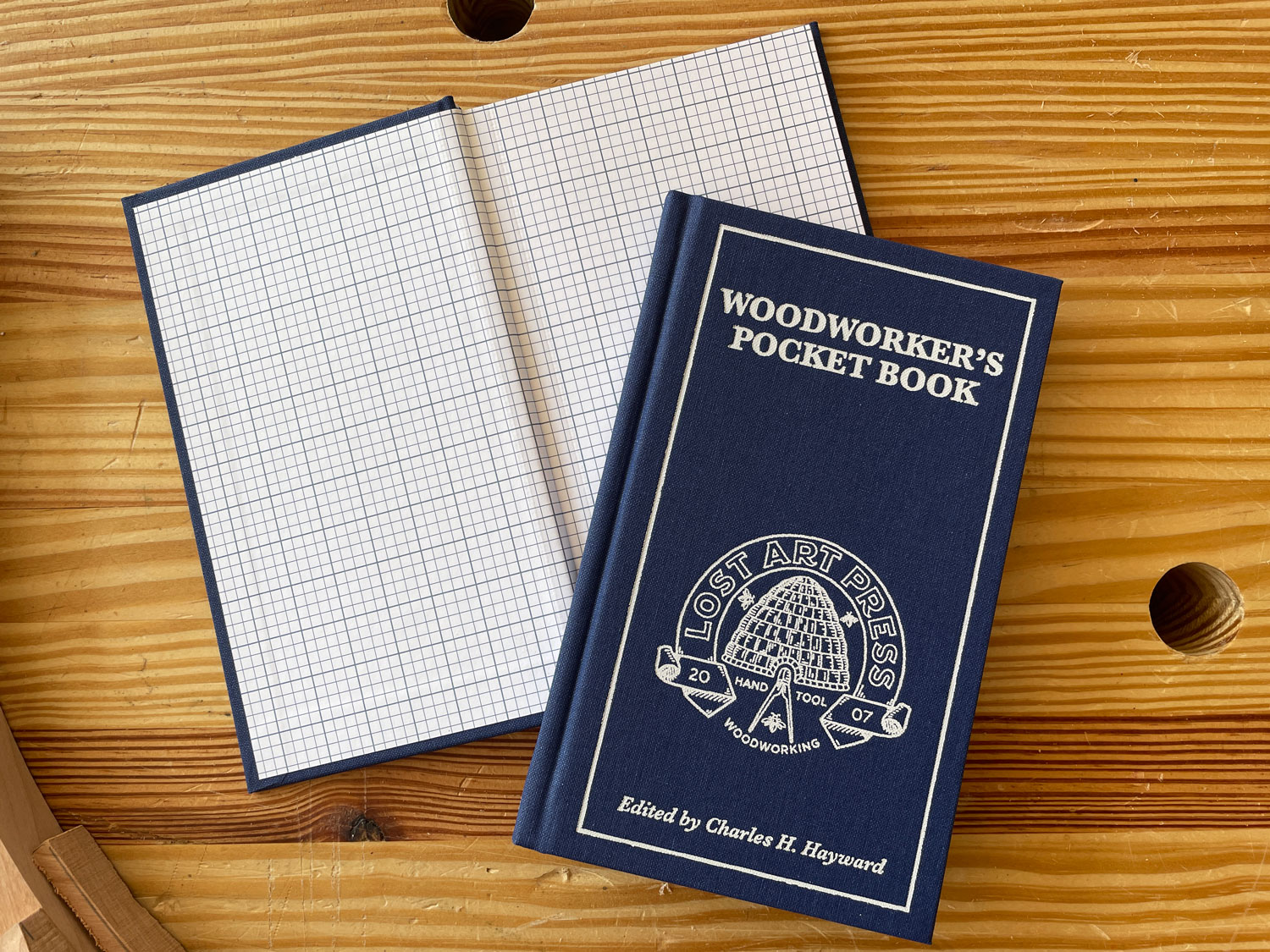
The good news: The book is gorgeous. We were able to get a couple of advance copies today to check some specs. I think you will love it when you receive it. The original book used graph paper for the book’s endsheets, which we reproduced. And we were even able to squeeze in some cute contrasting headbands on the book’s spine.
We also used stochastic printing to sharpen up the printing, plus a super-white paper to make the text easier to read. This was a stupid amount of work for a $13 book, but “stupid amount of work” was my nickname in high school.
Thank you for your patience. It won’t be long now.
— Christopher Schwarz
