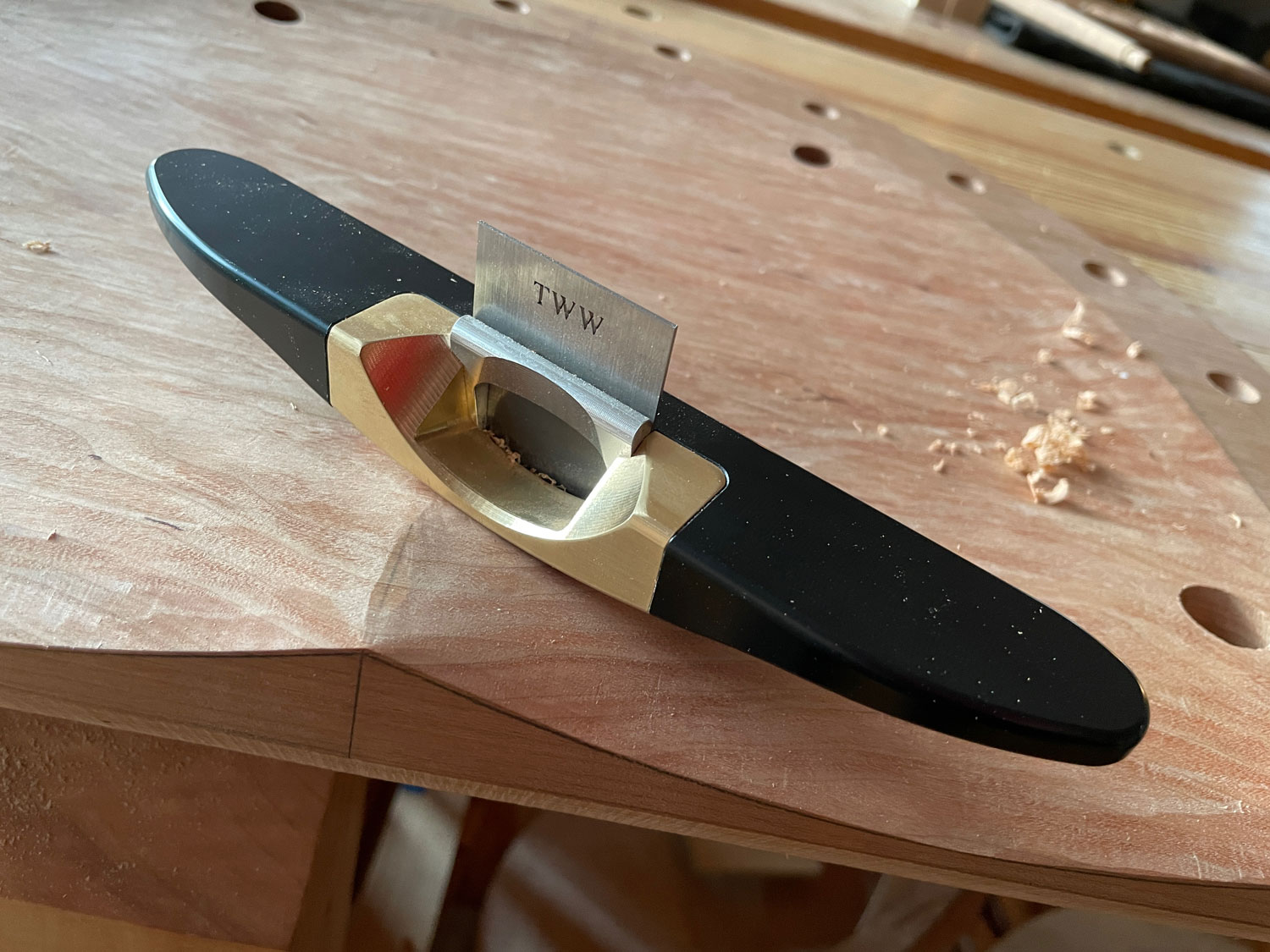
James Mursell at The Windsor Workshop has always made tools that work very well but look different than traditional tools. His travisher, for example, is a great worker, but it looks far more organic than a traditional travisher. Mursell’s travisher is all about rounded edges.
Mursell’s new Traviscraper, is in the same vein. Or is it? What the heck is a “traviscraper?”
Here in the States, most Windsor (aka Forest) chairs are made with seats in soft white pine and tulip poplar. Americans have little need to scrape their seats much at all. But in the U.K., seats are typically elm, ash or oak. So finishing a seat in these woods can be a lot of work with a travisher alone.
I build stick chairs, which have hardwood seats. So I struggle at times to finish them with only a travisher and a curved card scraper. The Traviscraper is the answer to a lot of my problems. It is like a scraper plane for concave hardwood seats. Like any scraping tool, it can work in almost any direction on the seat’s saddle. And the curved sole of the Traviscraper lets you make clean cuts in places that a travisher would struggle.
In fact, I wonder why this tool didn’t already exist. (Perhaps it did and I’ve never encountered it.)
In any case, the Traviscraper is a thoroughly modern tool. It’s made from Delrin and brass, so it has a real heft to it. Every surface of the tool is curved, except for two sharp corners of the blade (ease these over with a file or sander as they are sharp).
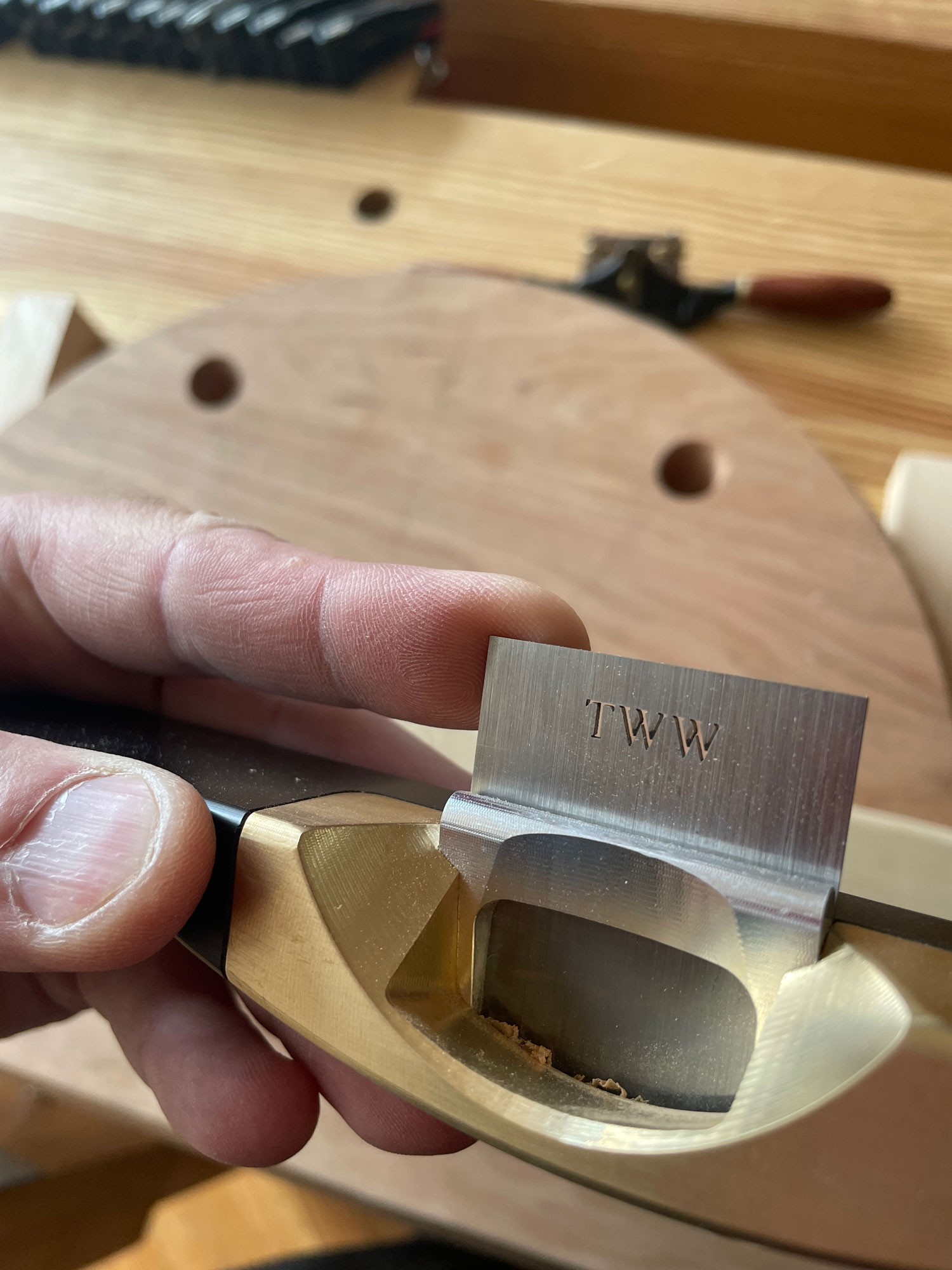
If you’ve used a travisher, you already know how to use the Traviscraper. You pinch it between your index fingers and thumbs and push it forward. I needed to use a bit more downward pressure with the Traviscraper than a travisher to keep it in the cut – you’ll figure it out. It’s pretty intuitive.
All in all, I really like the Traviscraper. It cleaned up the tear-out left by my travisher, but the tool’s sole continued to refine the seat’s saddle. After scraping my seat with the tool, it needed only some minor sanding to be ready for finish.
The tool is easy to set and resharpen – Mursell’s website has videos that demonstrate the process.
If you make chairs with hardwood seats, the Traviscraper will make your life much easier. If you make chairs with soft seats, I don’t think you’ll find it very useful.
The Traviscraper is available for sale directly through The Windsor Workshop website.
— Christopher Schwarz
P.S. As always, I paid full retail (plus shipping) for this tool and received nothing in return for my comments.
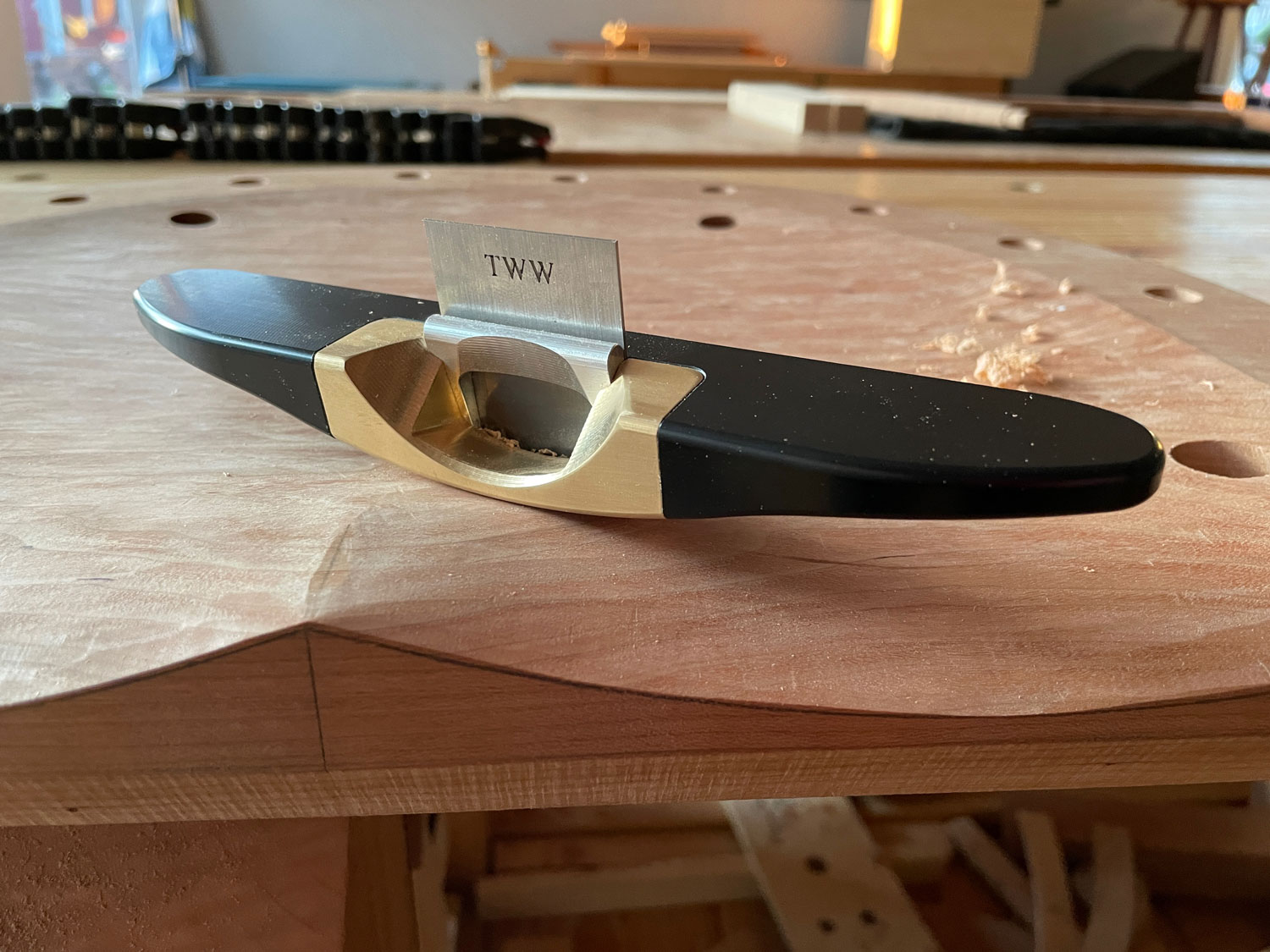