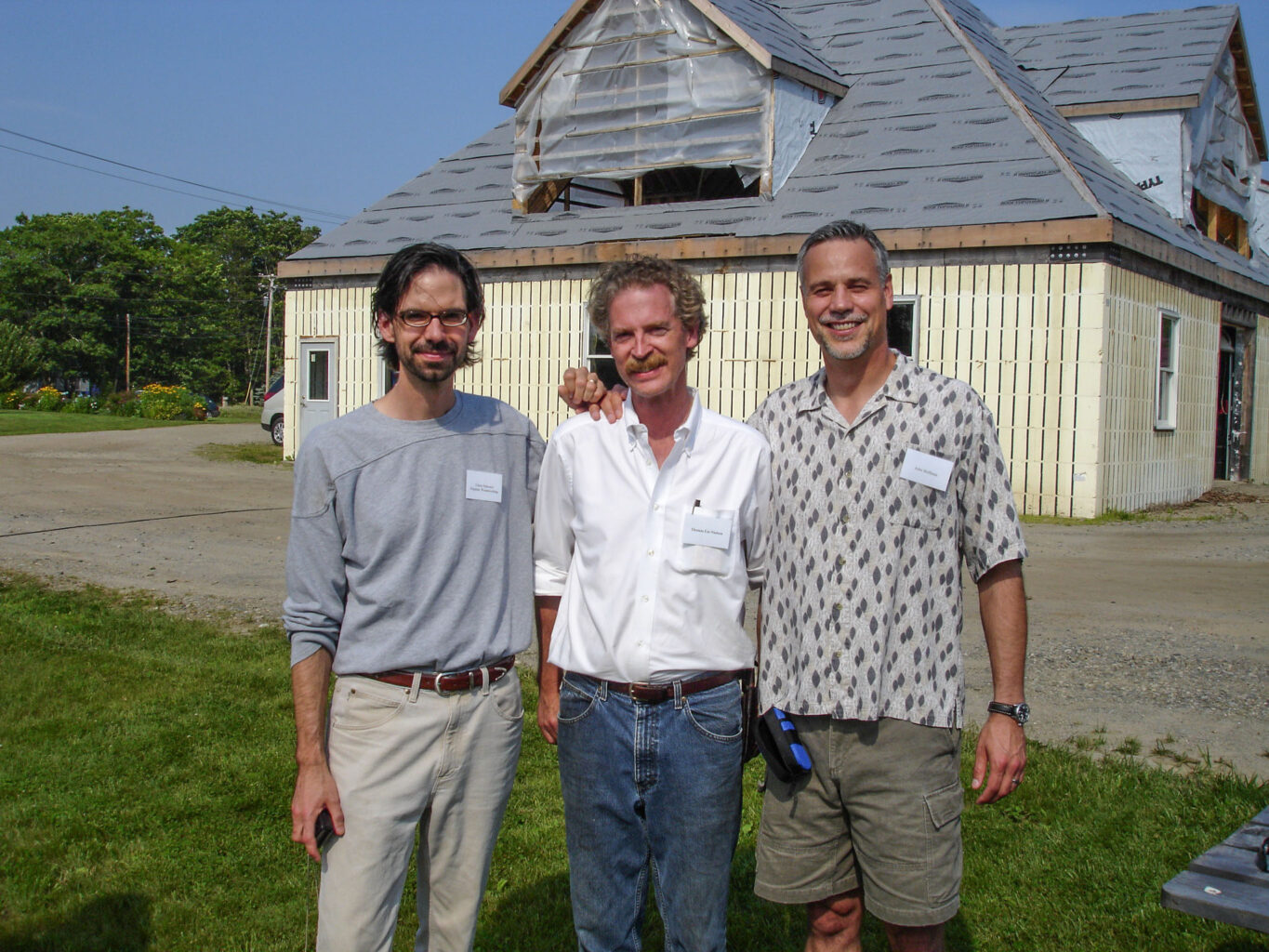
The picture above of three young friends was taken in 2006 at Lie-Nielsen’s 25th anniversary celebration in Warren, Maine. I was in awe of meeting Thomas Lie-Nielsen, and listened to everything he said about business and life. Also at the event was Christian Becksvoort who was a wealth of information. He is one of the few woodworkers who created and runs a successful woodworking business. As he said, “failure was not an option.” One thing he expressed that resonated deeply with me was he would never write another book because the publishing companies don’t play fair. As a kid in the 1970s who loved rock music, I saw documentaries about bands such as Grand Funk Railroad that had been taken advantage of by greedy management; right before a tour was supposed to start, management took all the equipment preventing the band’s tour from happening. I was hearing a similar story from Chris Becksvoort, a successful author.
On the long drive home from Maine I talked to Chris Schwarz about starting our own publishing company that would treat authors right. I thought that with current technology (this was 2006, mind you) we could enter the text into a system and hit the print button. I once heard Tom Lie-Nielsen say during a class, “I now know why tools cost so much to make.” I now understand there is a bit more to publishing than hitting a print button.
We started Lost Art Press in 2007 with “The Art of Joinery” by Joseph Moxon. Chris was still at Popular Woodworking magazine, and I had my full-time job. I had to get written permission to create a business that was not in conflict with my job and Chris had to get the OK from his employer to print the book. We published the book by offering pre-sales so that we had enough money to cover the print run. Tom let us come to his shows and sell it, and he remains a huge supporter of LAP. We are ever-grateful to him.
As business continued, I remember hitting $50K in sales and was over-the-moon happy. We created T-shirts and Chris created a thing called a “blog.” Now we use a lot of technology, and our blog continues to be the most important way to reach customers. Chris is a natural writer who actually wears out keyboards.
Our business is split between content and everything else. Guess which side I am on? I have only had two creative ideas in my life. The first was a block plane made from a concrete that would be covered in a slick poly material. Chris just looked at me. The second idea was steak-flavored soda. (Feel free to steal those ideas as LAP isn’t going down those paths.)
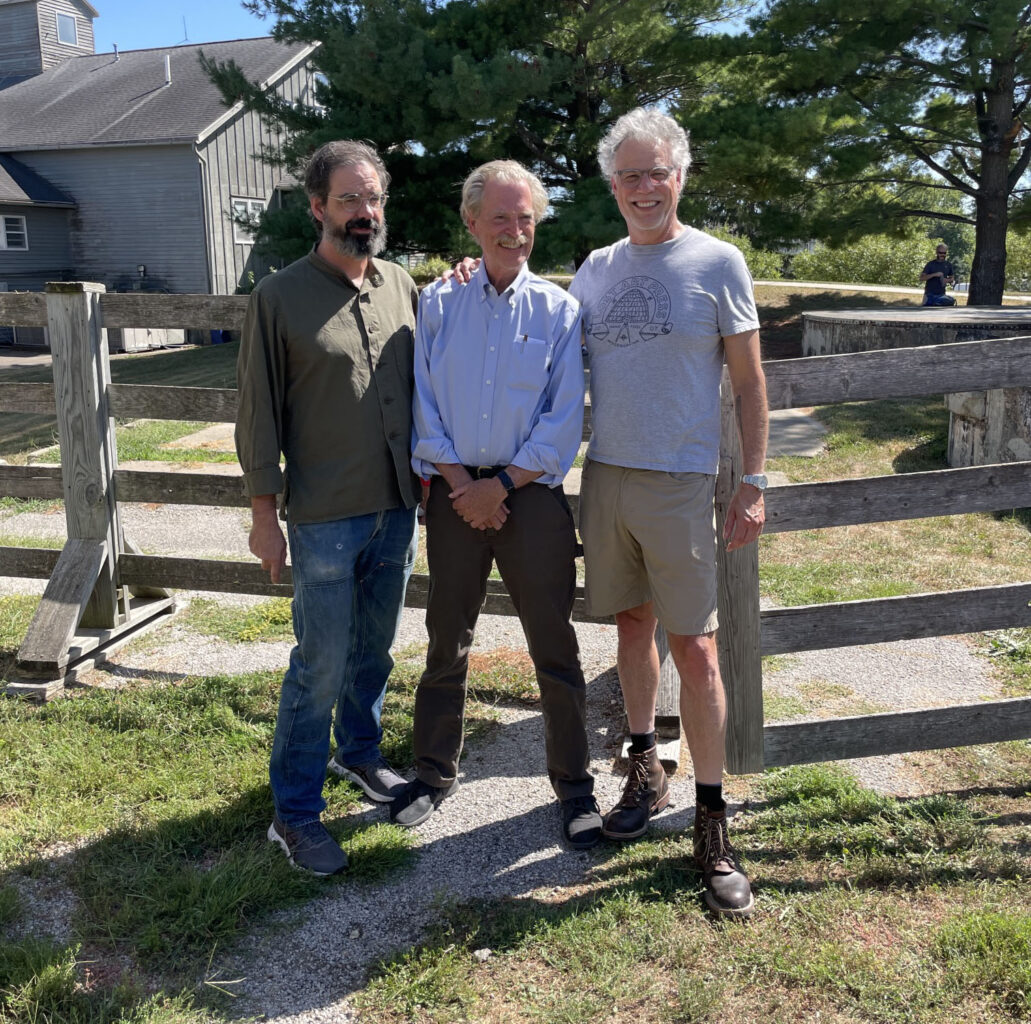
The second picture is from Handworks 2023, just a few days ago. what I am calling the “Middle” for LAP. As the picture shows I have become a model of style. My appreciation for others and this wonderful life continues to grow. It is amazing to me to see people wearing our T-shirts and buying our creations. As Chris said, “What a country where two drunks with laptops can create a business that works!”
On the drive home from Handworks 2023 I reflected on my life and how we got to where we are. I first and foremost thank you, our customers for your support. You are the best, and I think the other woodworking companies would agree; creators and makers have a wonderful quality that is sometimes lacking in “normal” society.
Special mention goes to Lucy May, Chris’s beloved wife who has held Chris up and helped me and helped LAP succeed. Thank you Madam President.
Thank you to our LAP staff: Megan Fitzpatrick, our first employee without whom we could not publish as many books; Meghan Bates my dear friend who takes care of our customers and provides a voice of reason when work and life have me needing advice; Kara Uhl for keeping contracts and other important items in line so I don’t go insane. Thanks to our newest employees, Mark Gilsdorf and Gabe Gavre, who have signed on to run the new warehouse. And thanks to Chris for being Chris, and bringing me along on this wonderful ride. He has become my other brother.
Thank you also to:
Tom Lie-Nielsen, a kindred soul, and his wife Karyn for their wonderful friendship and support when we were nothing.
Robin Lee, who is one of the kindest, visionary leaders I have met.
Chris Becksvoort for sparking us to create LAP.
All of our authors and our LAP family: Narayan Nayar, Dr. Timmy Henriksen, Dr. Sean Thomas, Justin Leib, Deneb Puchalski, FJ and Jameel Abraham and Raney Nelson.
Stay tuned. I promise to post every 10 years or so!
Much Love.
– John Hoffman