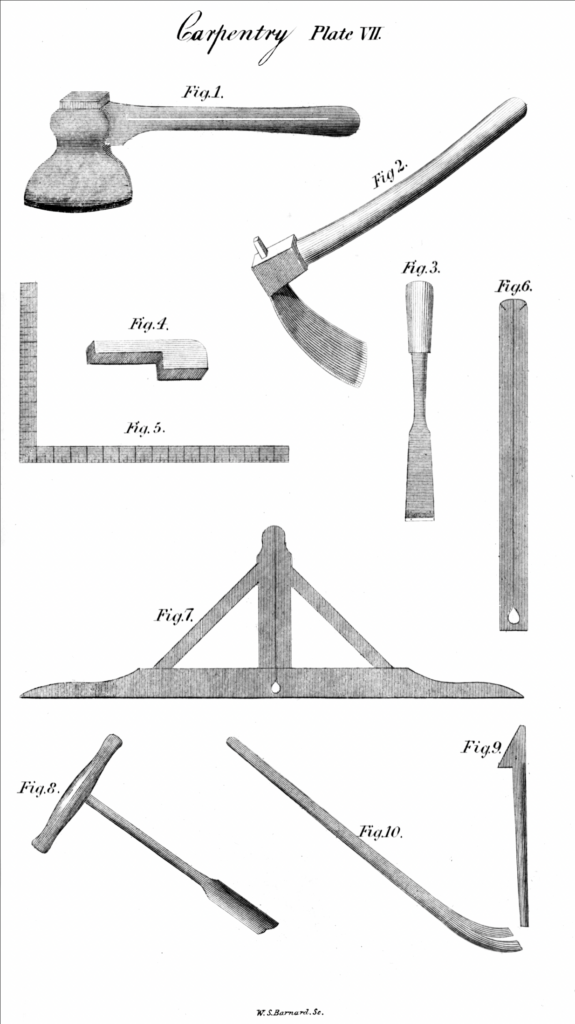
The following is excerpted from “Mechanic’s Companion,” by Peter Nicholson. It is one of the foundational English-language texts in woodworking and the building trades. First published in 1812, “Mechanic’s Companion” is an invaluable and thorough treatment of techniques, with 40 plates that provide an excellent and detailed look at the tools of the time, along with a straightforward chapter on the geometry instruction necessary to the building trades.
If you work with hand tools, you will find useful primary-source information on how to use the tools at the bench. That’s because Nicholson – unlike other technical writers of the time – was a trained cabinetmaker, who later became an architect, prolific author and teacher. So he writes (and writes well) with the authority of experience and clarity on all things carpentry and joinery. For the other trades covered – bricklaying, masonry, slating, plastering, painting, smithing and turning – he relies on masters for solid information and relays it in easy-to-understand prose.
PLATE VII.
Fig. 1 the axe used in chopping timber by a reciprocal circular motion, generally in a vertical plane, and with the cutting edge in that plane.
Fig. 2 the adze used also in chopping timber by a reciprocal motion, generally in a vertical plane, but with the cutting edge perpendicular to the plane, and thereby forming a horizontal surface.
Fig. 3 the socket chisel used in mortising; it must be observed, that the socket chisel is not always the breadth of the mortise, but generally less, particularly when the mortise is very wide.
Fig. 4 mortise and tenon guage.
Fig. 5 the carpenters’ square.
Fig. 6 the plumb rule.
Fig. 7 the level.
Fig. 8 the auger.
Fig. 9 a hook pin for drawboring.
Fig. 10 the crow.
§ 1. CARPENTRY in civil architecture, is the art of employing timber in the construction of buildings.
The first operation of dividing a piece of timber into scantlings, or boards, by means of the pit saw, belongs to sawing, and is previous to any thing done in carpentry.
§ 2. The tools employed by the carpenter are a, ripping saw, a hand saw, an axe, an adze, a socket chisel, a firmer chisel, a ripping chisel, an augur, a gimlet, a hammer, a mallet, a pair of pincers, and sometimes planes, but as these are not necessarily used, they are described under the head of joinery, to which they are absolutely necessary.
§ 3 OF SAWS.
A saw is a thin plate of steel, indented on the edge, so as to form a series of wedges, with acute angles, and for the conveniency of handling, a perforated piece of wood is fixed to one end, by means of which the utmost power of the workman may be exerted in using it.
Saws have various names, according to their use. It is obvious in order that the saw should clear its way in the wood, that the plate should decrease in thickness from the cutting edge towards the back, and for this purpose also, besides this additional thickness, most saws have their teeth bent towards the alternate sides of the plate, this must always be the case where the plate is broad: in very narrow plates the cutting edge is made thicker than usual. Such saws as are not intended to cut into the wood their whole breadth, have strong iron or brass backs, in order to stiffen them, and keep them from buckling or bending ; both external and internal angles of the teeth of saws are made to contain sixty degrees, and the magnitude of the teeth is proportioned to the size of the saw, and accommodated to its use.
Some saws are used for dividing the wood in the direction of the fibre, and to any extent of distance exceeding the breadth of the plate, at pleasure; others are only employed in cutting in a direction perpendicular to the fibres, to any breadth or thickness; the former case requires the front edges of their teeth to stand almost perpendicular to the line passing through their angles, in order to cut through, or make a way through in less time than if set backwards, which is better adapted to the latter case: for otherwise, the points of the teeth would run so deep into the wood, as to prevent the workmen from pushing the saw forward without breaking it. The saws commonly used by the carpenter, are the ripping saw, and the hand saw; which are particularly described under the head of joinery, as well as other saws used in that branch.
§4. THE AXE
Is an edged tool, having a long wooden handle, for reducing timber to a given form or surface, by paring away slices of unequal thickness ; is used by a reciprocal motion in the arc of a circle, generally in a vertical plane, forming the surface always in the same plane, and has therefore its cutting edge in a longitudinal plane, passing through the handle ; the slices cut away are called chips, the operation is called chopping, and the surface reduced to its form is said to be chopped ; but among woodmen the operation is called hewing.
§ 5. THE ADZE
Is also an edge tool with a long wooden handle for reducing timber to a given form of surface, by paring away thin slices of unequal thickness, by a reciprocal motion in the arc of a circle, and in a vertical plane ; but its cutting edge is perpendicular to a longitudinal plane passing through the handle. It forms a much more regular and smooth surface than the axe. The operation is also called chopping.
The use of the adze is to chop and pare wood in a horizontal position.
§ 6. THE SOCKET CHISEL
Is used for cutting excavations ; the lower part is a prismoid, the sides of which taper in a small degree upwards, and the edges considerably downwards: one side consists of steel and the other of iron : the under end is ground into the form of a wedge, forming the basil on the iron side, and the cutting edge on the lower end of the steel face, From the upper end of the prismoidal part rises the frustum of a hollow cone, increasing in diameter upwards ; the cavity or socket contains a handle of wood of the same conic form : the axis of the handle, the hollow cone, and the middle line of the frustrum are all in the same straight line. The socket chisel, most commonly used, is about an inch and quarter or an inch and a half broad. It is chiefly used in mortising, and is the same in carpentry, as what the mortise chisel is in joinery.
§ 7. THE FIRMER CHISEL
ls formed in the lower part similar to the socket chisel ; but each of the edges above the prismoidal part falls into an equal concavity, and diminishes upwards, until the substance of the metal between the concave narrow surfaces, becomes equal in thickness to the substance of the metal between the other two sides, produced in a straight line, meet a protuberance projecting equally on each side: the upper part of the protuberance is all at, or straight surface, from the middle of which rises a pyramid, to which is fastened a piece of wood in the form of a frustrum of a pyramid, tapering downwards; this piece of wood is called the handle : the middle line of the handle, of the pyramids of the concave, and of the prismoidal parts, are all in the same straight line.
§ 8. THE RIPPING CHISEL
ls only an old socket chisel used in cutting holes in walls for inserting plugs, and for separating wood that has been nailed together, &c.
§ 9. THE GIMLET
Is a piece of steel of a cylindric form, having a transverse handle at the upper end, and at the other end a worm or screw; and a cylindric cavity called the cup above the screw ; forming in its transverse section, a crescent. Its use is to bore small holes; the screw draws it forward in the wood, in the act of boring, while it is turned round by the handle ; the angle formed by the exterior and interior cylinders, cuts the fibres across, and the cup contains the core of wood so cut: the gimlet is turned round by the application of the fingers, on alternate sides of the wooden lever at the top.
§10. THE AUGER
Is the largest of all boring tools, it has a wooden handle at the upper end at right angles, to a long shaft of iron and steel ; at the lower end is a worm or screw of a conic form, for entering the wood ; so far it is similar in construction to the gimlet: the lower part of the shaft, axis, or spindle is steel, and is of a prismoidal form, to a certain distance, from the end upwards. The edges are nearly parallel, and the sides taper in a small degree upwards; the part of the shaft above the prismoid is arbitrary; but it is obvious, that in order to pass the bore freely, its transverse dimensions must be less than the lower part. The worm has its axis in the same straight line with the axis of the shaft. The lower end is hollow, or cut into a cavity on one side of the cone, and forms a projecting edge on the narrow surface of the prism called the tooth, which is brought to a cutting edge.
The part of the lower end on the other side of the cone projects before the face of the prismoidal part in the form of a wedge, the line of concourse of the two sides of the wedge forming a cutting edge. The vertex of the cope is the greatest extremity of the lower end ; the cutting edge of the tooth is something higher or nearer to the handle, and the cutting edge of the wedge-like part stilI nearer to the handle. Any point being given as the centre of a cylindric hole on the surface of a piece of timber, the vertex of the conic screw is placed in that point; then keeping the middle line of the shaft perpendicular to, or at the inclination to be given to the surface of the timber; turn the auger round with both hands, the screw will draw it downwards into the wood, and when it has got a certain depth, the tooth will begin to cut a portion of the cylindric surface of the hole: when the part of the cylindric surface is cut half round the circumference, or perhaps a little more, the projecting wedge-like part will begin to cut out the bottom, and the core will rise in the form of a spiral shaving, by continuing to turn the handle. This construction of the auger is of very late invention, and is certainly a great improvement.
The lower part of the old form of the auger is a semi-cylinder on the outside, and the inside a less portion of a larger cylinder, the bottom of the cutting part is formed like a nose-bit : before this auger can be entered in the wood, a cavity must be first made with a gouge.
§11. THE GAUGE
Is made out of a solid piece of wood notched with an internal right angle, or consisting of two narrow planes perpendicular to each other; one of these straight surfaces forms a shoulder, the other surface has two iron teeth placed in a perpendicular to the intersection of the two surfaces, so distant from one another as to contain the thickness of the tenon, or breadth of the mortise, and the tooth next to the shoulder so far distant from the intersection, as the tenon is distant from the face. When you gauge, press the shoulder close to the wood, and the other surface of the gauge which contains the teeth, close to the other surface of the wood to be gauged; then draw and pull it backwards and forwards and the iron teeth will scratch the wood so as to make a sharp incision or cut. When carpenters have occasion to alter their gauge for other work, they either file away the old teeth and put in new ones; or, if the distance between the old ones will answer, they cut away a parallel slice from the shoulder, or put a new piece on before it.
§12. THE LEVEL
Consists of a long rule, straight on one edge, about 10 or 12 feet in length, and another piece fixed to the other edge of the rule, perpendicular to, and in the middle of the length, and the sides of this piece in the same plane as the sides of the rule ; this last piece having a straight line on one side perpendicular to the straight edge of the rule. The standing piece is generally mortised into the other, and firmly braced on each side, in order to secure it from accidents, and has its upper end kerfed in three places, one through the perpendicular line, and one on each side. The straight edge of the transverse piece has a hole or notch cut out on the under side equal on each side of the perpendicular lines. A plummet is suspended by a string from the middle kerf at the top of the standing piece, so that when hanging at length, the bottom of the plummet may not reach to the straight edge, but vibrate freely in the hole or notch. When the straight edge of the level is applied to two distant points, and the two sides placed vertically, the plummet hanging freely, and coinciding with the straight line on the standing piece, then these two points are level: but if not, let us suppose that one of the points is at the given height, the other point must be lowered or heightened according as the case may require; and the level applied each time, until the thread is brought to a coincidence with the perpendicular line. By two points, is meant two surfaces of contact, as two blocks of wood or chips, or the upper edges of two distant beams.
The use of the level in carpentry, is to lay the upper edges of joists in naked flooring horizontal, by first levelling two beams as remote from each other as the length of the level will allow ; the plummet may then be taken off, and the level may be used as a straight edge. In the levelling of joists, it is best to make two remote joists level first in themselves, that is, each throughout its own length, then the two level with each other; after this, bring one end of the intermediate joists straight with the two levelled ones, then the other end of the joists in the same manner, then try the straight edge longitudinally on each intermediate joist, and such as are found to be hollow, must be furred up straight.
§ 13. TO ADJUST THE LEVEL.
Place it in its vertical situation upon two pins or blocks of wood then, if the plummet be hanging freely, and settle upon the line on the standing piece, or if not, one end being raised, or the other end lowered, to make it do so, turn the level end for end, and if the plummet fall upon the line, the level is just ; but if not, the bottom edge must be shot straight, and as much taken off the one end as you may think necessary; then trying the level first one way and then the other as before, and if a coincidence takes place between the thread and the line, the level is adjusted; but if not, the operation must be repeated till it come true.
§ 14. THE PLUMB RULE
ls a prismatical piece of wood, with a line drawn down the middle of one of the· sides, parallel to the two adjacent arrises on the same face. Its use is to try the vertical position of posts, or other work perpendicular to the horizon, by means of a plummet suspended from the upper end of the rule, and a notch cut out at the foot, in order to allow room for the plummet to vibrate freely.
In order to put up a post perpendicular to the horizon, place the bottom of the post in its situation, and the sides as nearly vertical as the eye may direct; if the post stands insulated, it must be fixed in this position with temporary braces, at least from two adjoining sides; but if very heavy, from all the four sides; then try the plumb rule upon one side, and if the thread coincides with the line, that side of the post is already plumb, but if not, the top must be moved forwards or backwards, accordingly as it leans or hangs, as much as appears to be wanted, by previously moving the front and rear braces, and fixing them anew, while the other two remain, to stay the other sides : apply the plumb rule again as before, and if there be a coincidence between the line and the plummet thread, then that face is perpendicular, but if not, the several similar operations must be repeated till found to be so. Proceed in the same manner with the other two parallel sides of the post, until they are made plumb, and by this means the post will be set in a true vertical position.
§15. THE HAMMER
Consists of a piece of steel, through which passes a wooden handle perpendicularly; the steel is flat at one end, or in a small degree convex. The use of the hammer is for driving nails into wood by percussive force. The other end of the hammer, that is not used for driving nails, is sometimes made with claws, and sometimes with a rounded edge, like a semicylinder. The claws are for laying fast hold of the head of a nail, to be drawn out of a piece of wood; for this purpose the back of the hammer is rounded, so that the hammer, in the act of drawing the nail, may not penetrate with its other extremity into the wood; and this also lessens the distance of the force to be overcome from the fulcrum, and consequently increases the power employed. When the hammer is used, place the back of it upon the wood, and the claws so as to have the nail fast between them, lay hold of the handle and pull the contrary way to that side of it on which the nail is; then, if the force be sufficient, the nail will be drawn out of the wood, and the nail thus drawn will come out almost straight. Some people, instead of pulling the handle of the hammer the contrary way to the side on which the nail is on, (and thereby making it describe a circle in a plane, perpendicular to the surface of the wood, and through the longitudinal direction of the head,) turn the hammer sideways : the nails easier drawn by this way, but then the surface of the wood is more injured, as well as the nail, which is frequently so much bent as not to be of any more use. Claw hammers are chiefly used in the country; and those with their other extremity rounded like a cylinder, are used in town for clinching and rivetting. In driving a nail, when the hammer comes in contact with the head of the nail, if the striking surface is not perpendicular to the shank of the nail, the nail will not be driven into the wood, or only in a small degree, but will be bent sideways towards an oblique angle, and will thus frequently break the nail, unless it be well entered, and so strong as to resist the force acting thus obliquely. The reader must here observe, that no force can act with its full effect upon another, unless in a line perpendicular to the surface of contact.
§ 16. THE MALLET
Is similar in its construction to the hammer, but the head is a thick block of wood, of a structure in form of the frustum of a pyramid, the side of this frustum tending to some point in the handle continued. It is used for mortising and driving pins into wood. The object is struck by the narrow sides of the mallet.
§ 17. THE BEETLE OR MAUL
Is a large mallet to knock the corners of framed work, and to set it in its proper position, and is sometimes used for driving short piles into the ground, where it would be unnecessary to use greater power. The handle is about three feet in length, and for these heavy purposes both hands are employed. This is more used in the country than in London, where they use a sledge hammer for the same purpose.
§ 18. THE CROW
Is a large bar of iron, used as a lever to lift up the ends of heavy timber, in order to lay another piece of timber, or a roller, under it. One end of the crow has claws.
§ 19. THE TEN FOOT ROD
Is a rod about an inch square, divided in its length into feet and inches, for the purpose of setting out work. The method of raising a perpendicular by a ten foot rod, is described in the Practical Geometry, page 25. Prob. III. Instead of a ten foot rod, some use two five foot rods for the same purpose.
§ 20. HOOK PIN
Is a conical piece of iron, with a hooked head, declining upwards in the form of a wedge. The top is flat, for the purpose of driving it down; and the shoulder which rises from the cone, stands perpendicular to the axis, and is used for driving it out of a hole, when it is fixed fast. The hook pins are the same in carpentry, as what the draw bore pins are in joinery, viz. they are employed after the tenons have been entered in the mortise and bored, as shall be presently shown, in drawing the shoulders of the tenons home to their abutments in the mortise cheeks : when there are several mortises and tenons in the same frame, as many hook pins are employed. The method of boring, and using the hook pins, is thus: bore a hole first through the mortise cheeks, not very distant from the abutments; enter the tenon, and force it home to its shoulders as near as you can ; mark the tenon by the hole, and draw the tenon out of the mortise. Then pierce a hole through the tenon, about one third of its diameter nearer to the shoulder, and enter the tenon again, bringing the shoulder as near to its abutment as possible; drive in the hook pin with considerable force; the convex circumference will bear upon alternate sides of the mortise and tenon, viz. upon the farther side of the hole of the tenon, and upon the nearest side of the mortise from the joint ; the shoulder of the tenon being brought home to its abutment, the hook pin may be drawn out of the hole; for this purpose there is a hole through the upper part of it, by which it is sometimes drawn out with another hook pin; but if driven in very fast, it will require the assistance of a hammer to strike it upon the shoulder upwards, and two or three smart blows will soon loosen it ; when drawn out, enter the pin, and drive it home with force, or till it be sufficiently through and fast, so as not to be driven farther without breaking.
§ 21. THE CARPENTER’S SQUARE
Is a square of which both stock and blade consists of an iron plate of one piece ; it is in size and construction thus : one leg is eighteen inches in length, numbered from the exterior angle, the bottom of the figures are adjacent to the interior edge of the square, and consequently their tops to the exterior edge: the other leg is twelve inches in length, and numbered from the extremity towards the angle ; the figures are read from the internal angle, as in the other side ; each of the legs arc about an inch broad. This implement is not only used as a square, but it is also used as a level, and likewise as a rule : its application as a square and as a rule is so easy as not to require any example : but its use as a level, in taking angles, may be thus illustrated; suppose it were required to take the angle which the heel of a rafter makes with the back, apply the end of the short leg of the square to the heel point of the rafter, and the edge of the square, level across the plate, extend a line from the ridge to the heel point, and where this line cuts the perpendicular leg of the square, mark the inches, and this will show how far it deviates from the square in twelve inches.