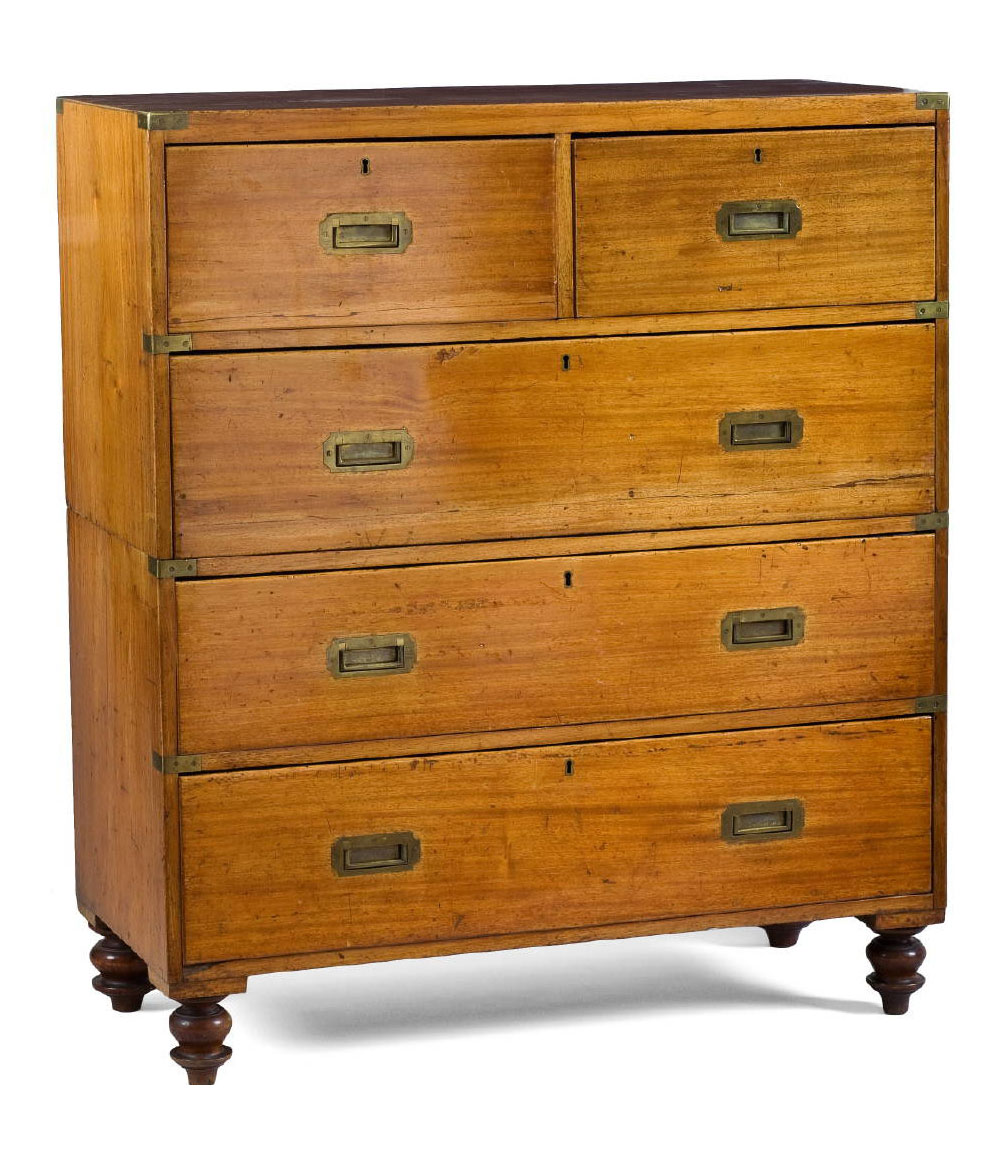
There are still some spots open in my class on building a campaign chest that I’m teaching May 6-10, 2013, at the Marc Adams School of Woodworking in Franklin, Ind.
For me, this class is the most important one I’m teaching in 2013 (yes, even more important than the workbench class with ancient oak). It’s important because it will tie together all the hand skills needed to build high-end casework. It will be a stepping stone for my forthcoming book on campaign furniture. And we, as a class, will be exploring a beautiful furniture form that has been neglected for almost 100 years.
On the casework side, this class is about hard-core hand joinery. Yes, we’ll be using machines dimensioning our stock, but most of the joinery will be handled with hand tools. Why? It’s efficient and fun.
Here are a few of the joints and processes we’ll be exploring.
• Full-blind dovetails to attach the top to the case sides.
• Half-blind dovetails to assemble the cases and drawers.
• Through-dovetails at the back of the drawers.
• Hand-cut dados for the drawer blades.
• Grooves for the back? You can cut them by hand or power.
• Web frames for the drawers? We’ll explore hand-cut mortise-and-tenon, machine-made mortise-and-tenon and the Domino.
• Turned feet (if you build a naval chest).
• Installing inset hardware with power tools or hand tools.
• Dealing with figured exotic woods with hand tools only.
In other words, this class will explore the full range of casework joinery options out there. This class is great for beginners who want to jump into classic joinery or woodworkers who have always wanted to learn to do things “the right way” with a historical approach and a handsaw.
Oh, and this class will also be about scoring some incredible wood. On the Friday before the class (May 3), we are visiting my favorite lumber paradise: Midwest Woodworking. There we’ll be picking out some world-class wide mahogany (or other species) for the chest of drawers.
So if you’ve ever wanted to step up your joinery skills to the top shelf, I think you’ll find this class is an excellent trial by fire. It’s not about one skill or one tool or one sample project. It’s about mastering the suite of skills to make a world-class piece of furniture.
I haven’t been this excited about a class since Dictum gave me the green light to teach a class based on “The Anarchist’s Tool Chest.”
For more information on the class, visit the marcadams.com web site here. If you have questions about the class, drop me a line at chris@lostartpress.com.
And for those of you who have already signed up, I hope you are looking forward to this class as much as I am.
— Christopher Schwarz
Like this:
Like Loading...