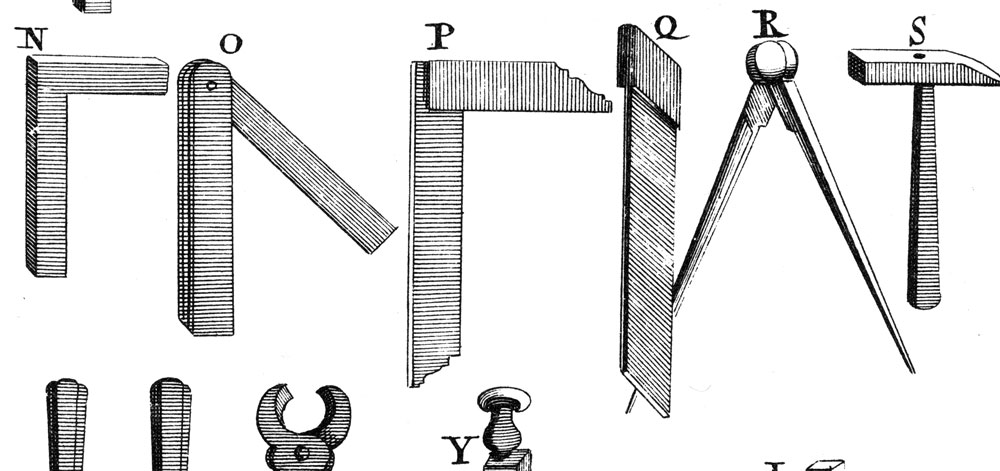
The Northern European square from Melencolia looks a lot like a tool that shows up in several early English and French texts on woodworking.
But the drawings of this tool – the miter bevel – have always bothered me. It’s really a problem of perspective (or lack of perspective). But the miter bevel, when drawn, looks like a dead ringer for the Melencolia square.
Take a look at the image above. It’s from André Félibien’s “Princips de l’architecture…,” which is where Joseph Moxon cribbed his illustrations for “Mechanick Exercises.” Félibien calls the tool (Q) the “Triangle angle,” whereas the traditional try square to its left is called a “Triangle quarré.” “Quarré” being the word for “square” in this instance.
If you look at the drawing of the Triangle angle it’s easy to be fooled that all of the lines are either parallel or 90° to one another and you are looking at it from a highly foreshortened perspective.
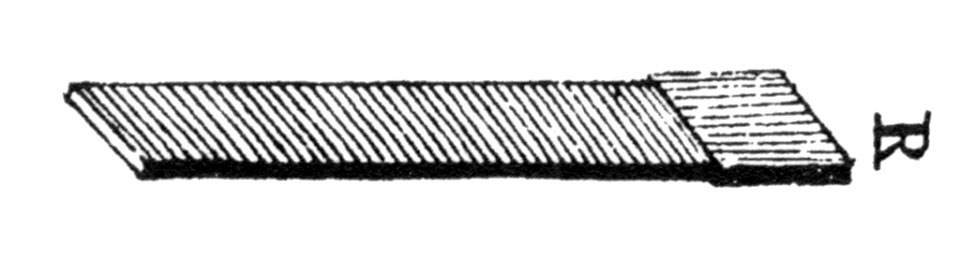
Moxon’s drawing of the same tool copies the image. And Randle Holme III’s “The Academy of Armory, or, A Storehouse of Armory and Blazon” looks even less like a bevel square to my eye.
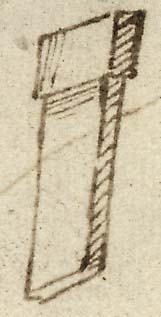
It’s only the text that really makes thing clear. (You can read the original text from both Moxon and Holme at the end of the article.)
What finally made the scales fall from my eyes was to see a real bevel square. Thanks to my good friend Bengt Nilsson, a Swedish woodworker and my sometimes-assistant when I teach in Germany, we have this image from his trip to Skokloster palace, which has a remarkable collection of 17th- to 19th -century woodworking tools. Many of them unused.
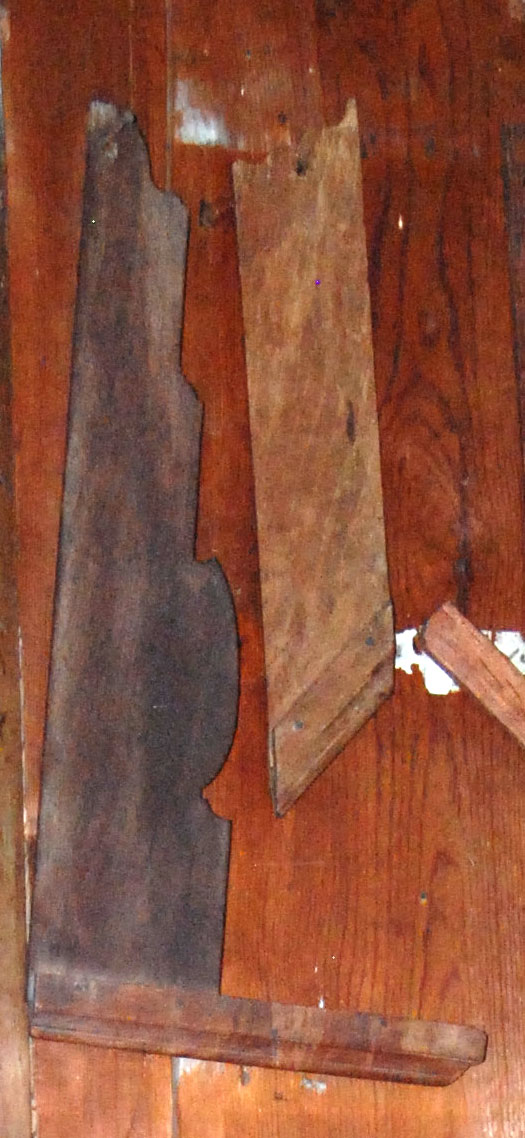
Here you can see how the thing really looks. The photograph refuses to allow our minds to trick us into seeing 90° when there is 45°. And hey, look, a Melencolia square is right next to it with a very decorative blade. Thanks Bengt!
The point of this blog entry isn’t about my trouble with perspective. Instead, it’s to show the clear structural relationship between the Melecolia square and the more-common bevel square. They both have short stocks and long blades. And both are now (almost) extinct.
Next: Other images of the Melencolia square and discussing its construction.
— Christopher Schwarz
Randle Holme III’s “The Academy of Armory, or, A Storehouse of Armory and Blazon:”
CXXXVIII. The first Tool in this square is termed a Miter square, of a contrary form to the following, mentioned chap.9. numb.17. It hath an Handle (or top part) an Inch thick, and three broad, with a Tongue of the same breadth, and for length 5, 6, or more inches, according to the breadth of the Work: it is to be Glewed into the Handle by a Mortess and Pinned.
Joseph Moxon’s “Mechanick Exercises…:”
S. 18. Of the Miter Square. And its Uſe.
The Miter Square marked E, hath {as the Square} an Handle marked a, one Inch thick, and three Inches broad, and a Tongue marked b, of about the ſame breadth: The Handle and the Tongue {as the Square} have both their Sides parallel to their own Sides. The Handle {as the Square} hath in the middle of its narroweſt Side a Morteſs in it, of an equal depth, the whole length of the Handle: Into this Morteſs is fitted one end of the Tongue, but the end of the Handle is firſt Bereld off to make an Angle of 45 Degrees with its inſide. This Tongue is {as the Square} Pin’d and Glewed into the Morteſe of the Handle.
It is uſed for ſtriking a Miter-line, as the Square is to ſtrike a Squareline, by applying the inſide of the Handle to the outſide of the Quarter, or Batten, you are to work upon; and then by ſtriking a Line by the ſide of the Tongue: For that Line ſhall be a Miter-line. And if upon two Battens you ſtrike two ſuch Lines, and Saw and Pare them juſt off in the Lines, when the flats of thoſe two ſawn ends are applied to one another, the ont and inſide of the Battens, will form themſelves into the Figure of a Square.
And, in case you missed it, here is the first part of this series:
Melencolia Square, Part 1
Like this:
Like Loading...