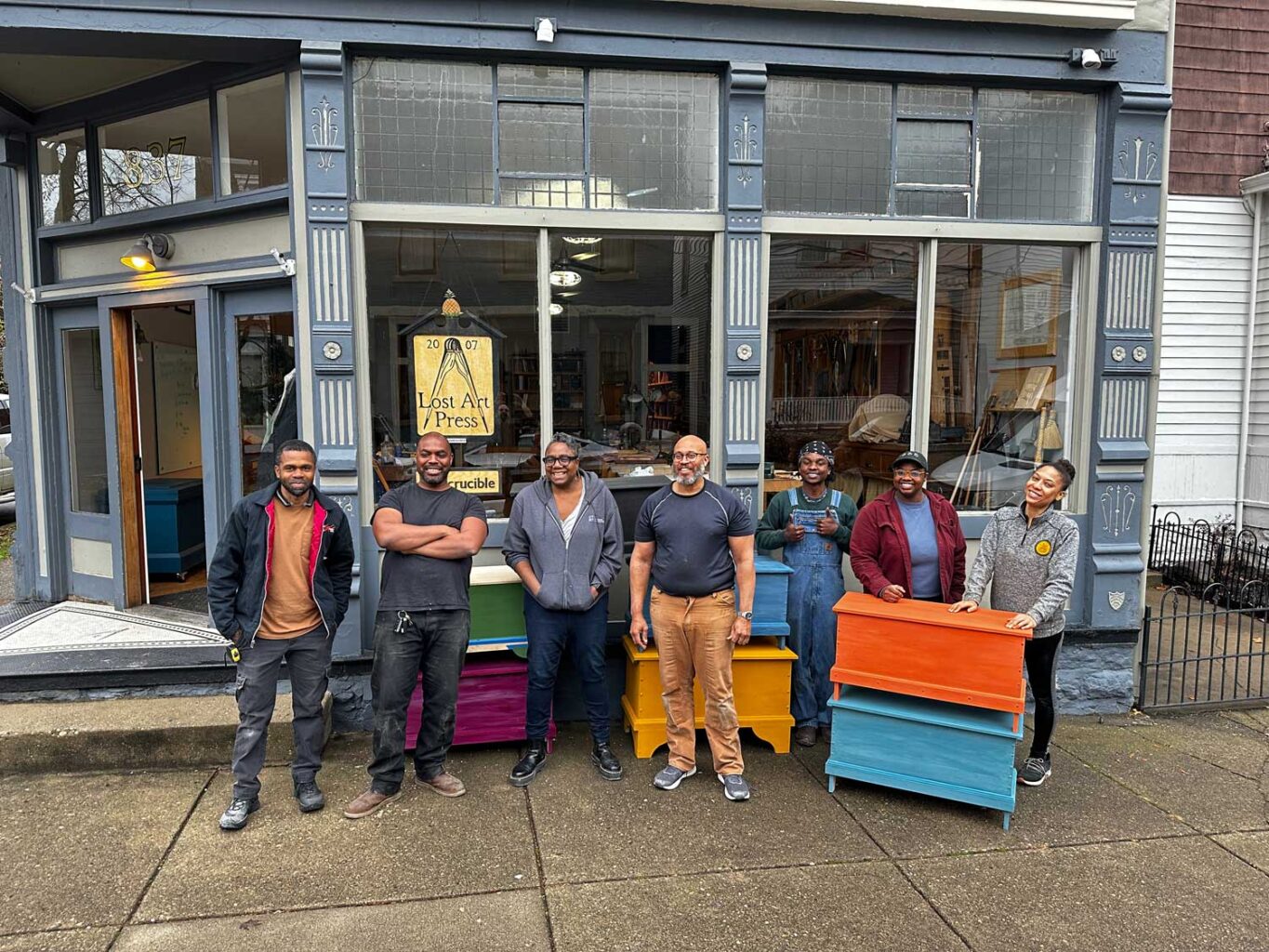
Last week, Jerome Bias led a woodworking class of six black woodworkers as they built a six-board chest by hand in our workshop. It was one of the more memorable and enjoyable classes here at our storefront.
In addition to woodworking, every day of class was filled with explorations of the past led by Jerome, who worked as a tradesman at Old Salem Museum & Gardens and now explores African-American foodways by preparing open-hearth historical meals at plantation.
The chests were made entirely by hand, and each student personalized their chest with the decorative cutouts, the mouldings and the milk paint they applied on the last day.
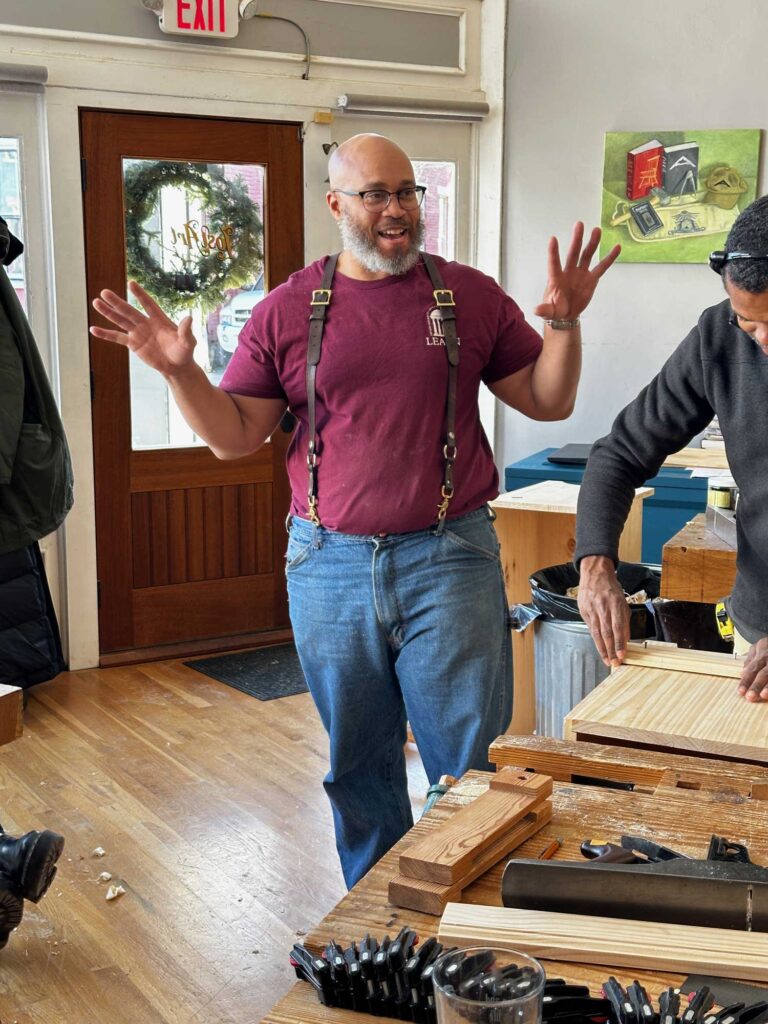
This remarkable class was possible because of Jerome’s fearlessness and desire to encourage young black woodworkers. And it was possible because of your donations of cash and tools. Thanks to your help, the wood, the food and the kits of tools we prepared for the class (which they took home) were all covered, gratis.
I feel certain you are going to see these faces again, both here at Lost Art Press and in the world at large. The enthusiasm and drive of these students was infectious.
Thanks to everyone who helped. We hope we can do this again. First we all have to rest, but not for too long. Tomorrow at 10 a.m., Megan and I begin a new project that we hope will plant a seed for future generations. More details to come.
— Christopher Schwarz
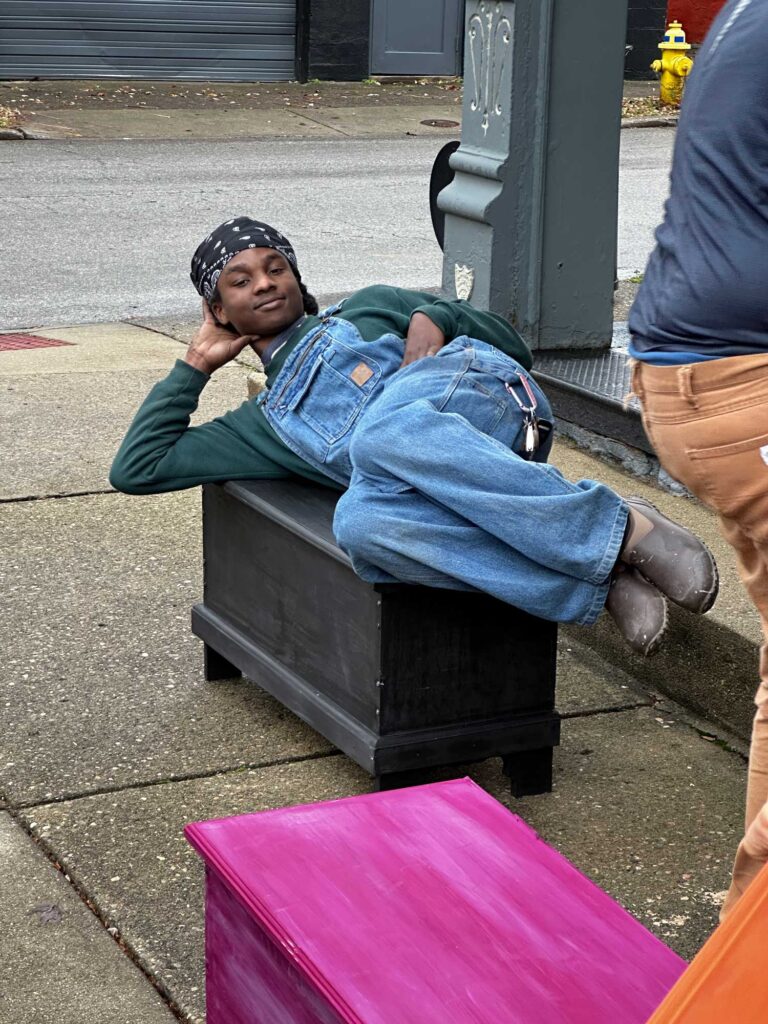