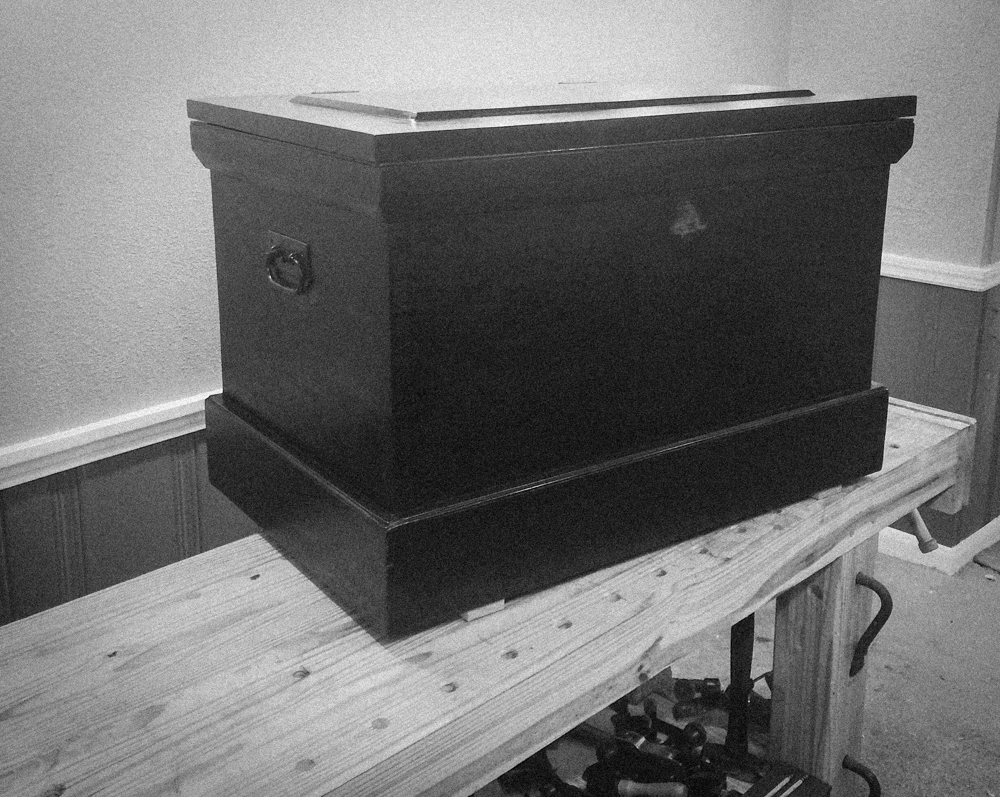
This fall, Lost Art Press will add a discussion forum. The “digital pub” will be a space for readers to converse, share photographs of LAP-inspired builds and ask questions related to hand-tool skills, books and life in the craft.
When I joined Chris a few weeks ago for the Anarchist’s Tool Chest class at Phil Lowe’s Furniture Institute of Massachusetts, I mentioned my plans to launch a “fan site.” I wasn’t sure what domain name to use, but when Chris showed up at happy hour in his “Death to the Pixies” t-shirt, it was obvious: “Fu**ostArtPress.com,” I blurted out. Sometime between that outburst and the next round of beers, Chris decided to let me give it a shot.
But the forum is also an idea that John and Chris have been thinking about for a while. Over the years, they’ve received a steady stream of questions, along with suggestions for what they “NEED” to add to the web site. When Chris decided to give up e-mail, pesky readers like myself lost the capacity to ask those questions. And Chris lost one of the most treasured aspects of being an author – the pleasure of receiving feedback from engaged readers.
So the forum fills gaps on both sides. For readers, it will be a virtual pub. For authors, it revives a digital means of receiving feedback, questions and criticisms.
At this point, I bet you’re asking two questions: (1) “Who is this guy?” and (2) “What’s he got to do with the blog?” Although I hate writing about myself, here are some quick answers.
(1) I’m a woodworking nerd. I have more experience reading about wood than building furniture. But that is about to change. For the past decade, I’ve been a professional professor and a hobby woodworker. This fall, I’m reversing those roles. While being an adjunct professor of American religious history has been a fulfilling vocation, it hasn’t paid the bills. I’ve yet to find that coveted tenure-track job, and I’m fed up with the corporatization of higher education. Inspired by authors like Chris, Robert Pirsig, and Matt Crawford – and encouraged by my wife and many of our university colleagues – I’m taking the plunge into anarchy. I’m building my own furniture designs. Valuating my own labor. Refusing to accept the Ikea-fication of our world. And narrowing the gap between what I do and what I love.
(2) I’m going to moderate the forum. While I encourage constructive criticism, this won’t be a space for hate. (And I will have a really low threshold for any posts derogatory of other readers.) We want this to be a friendly pub where the whole family can enjoy bratwurst and beers, not that bar down the street where every Saturday night someone gets their head bashed in with a cue ball. (I actually love those bars – this just isn’t going to be one of them.) In addition to moderating posts, its my job to keep other blog readers and LAP authors up to date. Each Monday, I’ll write about what’s trending in the forum, including links to conversations and photographs. As the discussions build, I’ll solicit comments and responses from LAP authors.
We anticipate we’ll be ready to launch the forum by mid-September. Until then, you’ll have to keep using the lame “comments” function to tell us what you think!
— Brian Clites, your new moderator and author of TheWoodProf.com blog
Like this:
Like Loading...