Editor’s note: Thanks to everyone who entered our True Tales of Woodworking Contest, in celebration of the release of Nancy Hiller’s new edition of “Making Things Work: Tales of a Cabinetmaker’s Life.” We enjoyed reading every one of the entries – it was difficult to choose a winner (a good problem to have!). We’re running some of our top choices here (lightly edited to match LAP editorial style), and will announce and share the winning story on Saturday, Feb. 1. Nancy will also be sharing some of the entries on her Making Things Work blog, so be sure to tune in there, too!
— Fitz
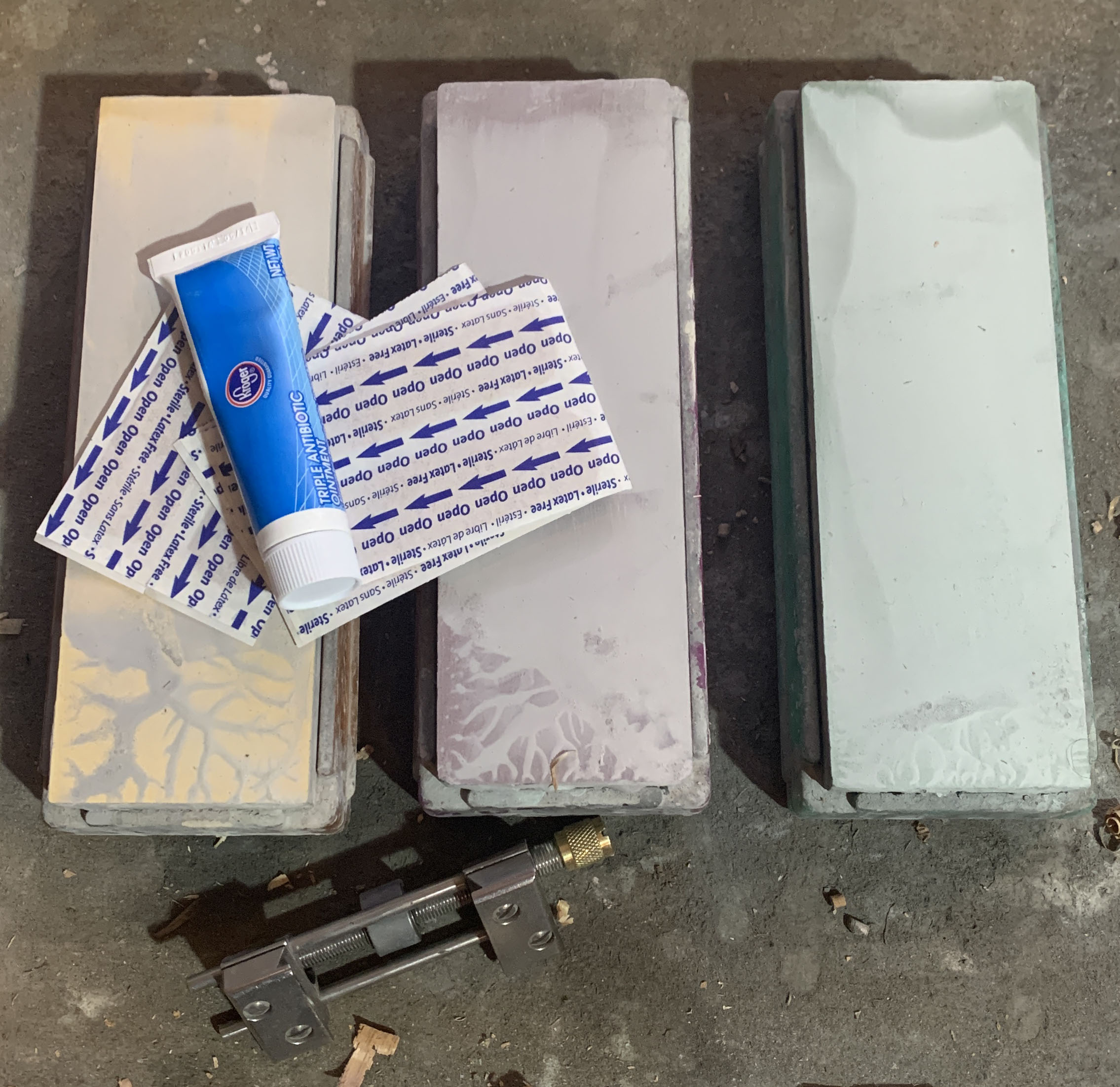
Every meaningful thing I have learned about woodworking, I have learned from mistakes. I type at a desk for a living. I sit in a high-rise commercial building, fingers on plastic chiclet keys, eyes focused on the blue light of my monitors, swiping between files on an illusory desktop. Woodworking affords me the opportunity to work with my hands. It provides a meaningful escape from the doldrums of my suburban routine. I find the discipline well worth it – even if that includes the risk of personal injury. The following litany of injuries is by no means exhaustive. It represents only a small portion of the valuable lessons I have learned in the past few years.
• Injury #1: A 10″ bruise just above my navel. Lesson: Never use a table saw’s fence in a cutting operation when the piece you are cutting is wider than it is long.
While making a decorative wall panel for a conference room build-out, I made a 4′ x 10″ strip of 1/4″ plywood, which I intended to cut into 10″ squares. “Aha!” I thought aloud. “The table saw’s already set at 10″. I’ll just rotate the strip 90 degrees, and zip through these.” I let the long end flop over the side of the saw and proceeded to push the short end against the fence. My hand must have twisted the piece slightly, for the blade and hurled a square directly into my gut like Frank Richard, who caught cannonballs with his stomach. I took a long break, and used a sled without the fence on the next cuts.
• Injury #2: Splinters; a near impalement. Lesson: Wood may have pent-up stress, which can relieve itself at inopportune times.
While attempting to make a faux shoji screen, I found myself resawing on the table saw some Douglas fir for the lattice. About halfway through the board, I heard the blade whine louder than a teenager on a bad date. Instinctively, I let go and the 6′, spear-like projectile sailed past me. The “kiln-dried” lumber from my local big-box store appeared to have a very wet center, which caused some dormant stress to be released. Suddenly free, the twisted fibers pinched the blade, et voila! I had accidentally made a modern, motor-powered atlatl.
• Injury #3: A deep cut across the tip of my index finger. Lesson: Pay close attention to your hands while sharpening.
I had bought new sharpening stones and was happily honing my first set of chisels. I pressed against the back of the chisel with my index finger and started a series of hypnotic figure-eight motions. About 90 seconds into the sharpening routine, my lapping fluid turned a rusty brown color. I thought it odd, but continued. When I lifted the chisel to feel for a burr, I noticed that my finger had found the edge of the chisel at some point in the process, getting caught between my chisel and stone. The perfectly clean wound oozed blood. I must admit, I did feel a bit of pride in spite of my throbbing finger: the chisel certainly was sharp.
• Injury #4: A hole in my fingernail. Lesson: Never rush sanding.
So I wanted to sand some half-lap joints flush. I was in a rush, and I decided to lock my hips and bring my full weight to bear against the disc sander. It worked marvelously. That is, until my workpiece tipped ever so slightly. In half a second, the grit ate through the center of my fingernail. The ensuing panic clouded my mind; I could not decide what to do next. Thus, I got blood everywhere. It dripped on my workpiece, ruined my shoes, and dribbled all over the workshop floor and equipment. I elevated my hand, waited for the blood to clot, taped up my finger, disinfected everything, and went back to work. It was the week before Christmas, and I had gifts to finish.
• Injury #5: Mysterious cuts in odd places. Lesson: I’m never going to be perfect, and that’s OK.
Where do these injuries come from? I don’t know. Currently, there’s a 1″-long gash on the back my ring finger. How did I get that? I have no idea. Why didn’t it hurt at the time? No clue. It hurts now. Usually about a half-dozen of these injuries appear on my hands and arms for the duration of a project. I’ve made my peace – with most of them.
The reason I treasure these experiences is found in their effect on the connection between my body and mind. These memories are concrete. I can still smell the mildly herbal aroma of Ipe when I first ripped it on a table saw. I can feel the subtle suction of a perfectly flat board against the cast iron top of a jointer. I remember the joy I felt when I first saw whisper-thin walnut shavings emerging from the mouth of a handplane. I can hear the subtle hiss of piston-fit drawer as it slides into place. These experiences are durable. They are worth a hand full of splinters.
— Clayton Huthwaite
Like this:
Like Loading...