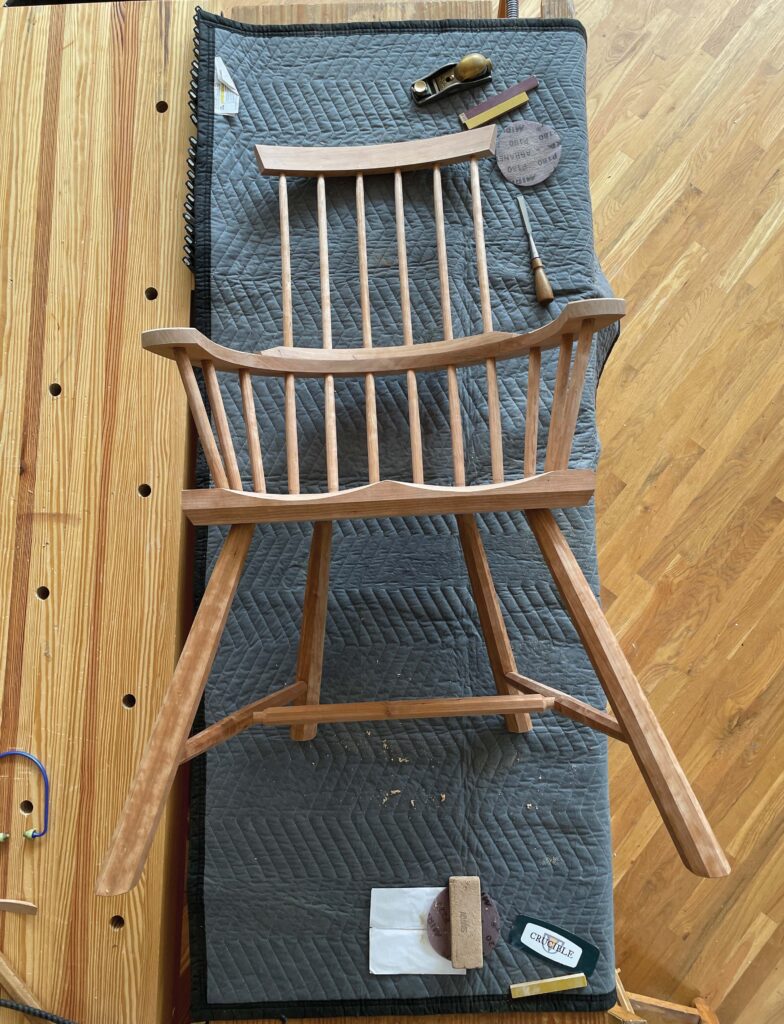
The following is excerpted from “The Stick Chair Book,” by Christopher Schwarz. (His “make pretty” process applies to all of his projects, not just chairs.)
“The Stick Chair Book” explores the craft of “hedge carpenters” or dabblers who built chairs for the everyday home. The chairs they made weren’t designed to impress the neighbors – they were designed to be comfortable, stout and (if you have a good eye) nice to look at.
After 18 years of building vernacular stick chairs and studying historical examples in the U.K., Europe and North America, Schwarz has figured out how anyone can design and build these chairs without a lot of gear.
Here are the things you don’t need to build a stick chair: a shavehorse, drawknife, steambox, green wood, axe or even a passing knowledge of geometry.
Instead, most of the work is done with saws (a band saw speeds things up), a drill or brace, a jack plane and maybe a couple specialty tools if you want to saddle the chair’s seat. You can use any kind of wood, even stuff from the home center.
At some point during my life as a woodworker I decided to add one more step to the construction process of every piece of furniture I build. Instead of stampeding from assembly into finishing, I added one day of work that I call: Make Pretty.
On this day I do nothing but try to bring every surface of a piece up a notch. I look over every inch – slowly – to find small defects that can be remedied, or details that can be made crisper. I look at bevels and mouldings to see if I can tweak their corners so they flow more smoothly. I look for tiny bits of glue or splinters (even on secondary surfaces) that I can pare away. I check curves and overhangs to see if they can be subtly altered to be more harmonious with the rest of the piece.
Make Pretty might sound like a drag. But I find it to be the most satisfying part of making a piece of furniture. For one whole day I get to look at a thing I’ve made before it heads off to a customer. So many times, I’ve looked at photos of my pieces that are now 1,000 miles away, and I can barely remember working on them.
Make Pretty is the conjugal visit before the great separation.
I have a set of tools that I use for every session of Make Pretty. Here’s the list:
• A moving blanket/furniture pad.
• A freshly sharpened cabinet scraper.
• A handful of flat sticks that are covered with #100-, #180- and #220-grit sandpaper (basically shop-made emery boards). The wood backing makes crisper lines than hand-held sandpaper.
• A sharp 1/2″ chisel.
• A cork sanding block and #220-grit abrasive.
• A small UV flashlight (which highlights smears of hide glue).
• Hot water and a toothbrush (for removing the smears of hide glue).
• My shop’s two logo stamps.
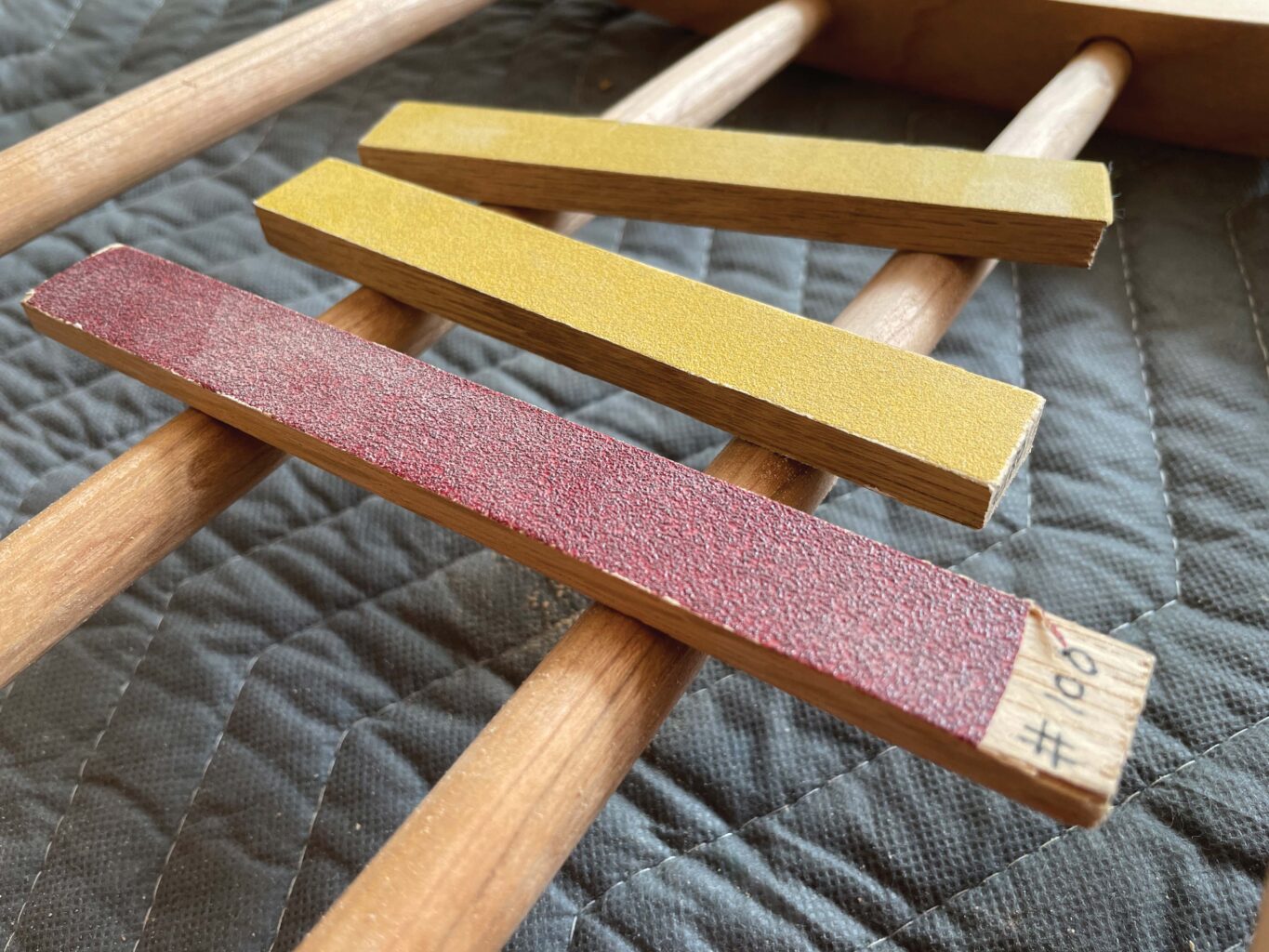
For me, Make Pretty begins with the smallest details. I put the chair on a moving blanket and look at every joint in the piece. I ask: Can I do anything to make this better? In a case piece, this might mean a little bit of glue and sanding dust to conceal a hairline gap. In a chair, it might require a sliver of a wedge to fill a void where a wedge shifted during assembly.
I look for stray splinters where tenons were driven hard into mortises. I look for tiny beads of glue that evaded my eye after assembly.
After looking at joinery, I look at individual components. I examine each stretcher to see if there are odd flats where the double-tapers meet. Is there any tear-out I can remove? Do the stretchers transition evenly into the tenons? Can they be evened up?
The same goes with the chair’s sticks. Mostly I look to see if there are small irregularities I can correct. Many times a stick’s tenon is slightly offset from the center of the stick. A little scraping on the heavy side of the stick can easily conceal this.
On legs I look for dents that occurred while moving the chair about. Can they be steamed or scraped away? On the arms and the shoe I look for tear-out, corners that aren’t crisp and bevels that don’t meet evenly.
This process continues over every single component.
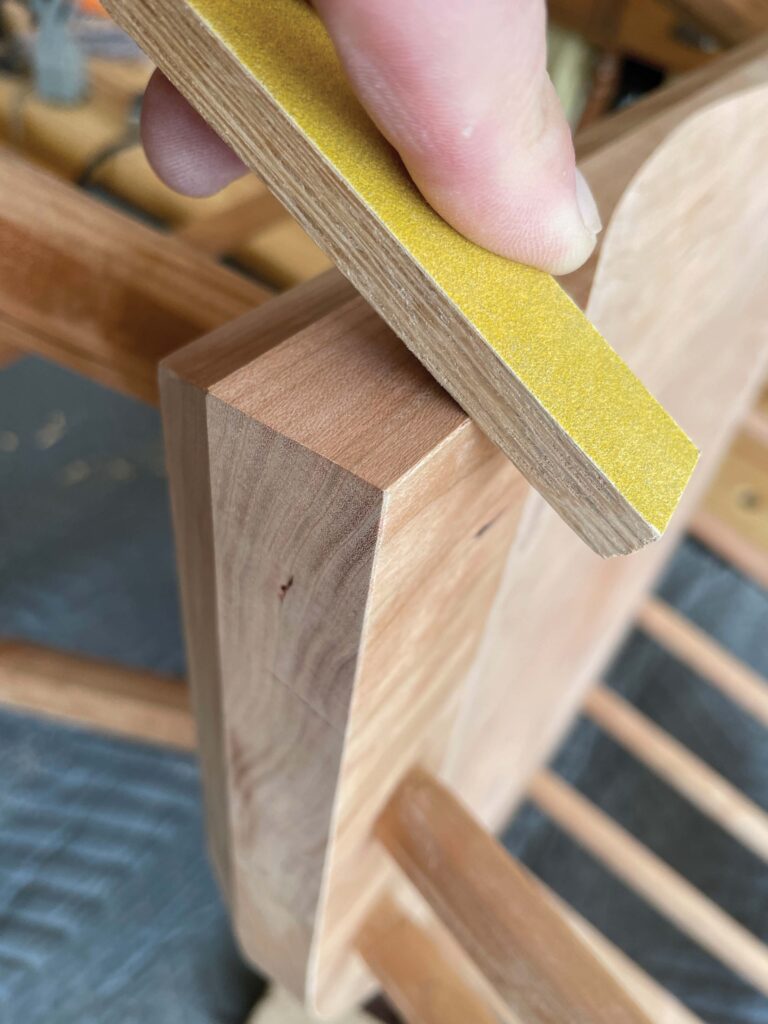
After that, I look at broad surfaces. Can I improve the line between the spindle deck and the saddle? Can I make the pommel crisper? Is the curve on the comb perfect, or can I eliminate small bumps or hollows with some sanding? Are the arms perfect to the touch? (Because they will be touched.)
I spend extra time looking at any end grain that shows in the piece. Because end grain is more difficult to work than face grain, it’s fairly common for the end grain to need some extra attention to remove scratches so it matches the finish level of the face grain.
Getting Ready for Finishing
When I have corrected every error I can find, I turn to making the arrises of the piece ready for finishing. In most commercial work, all edges get “broken” by a quick rub with fine sandpaper. Breaking the edges makes the piece pleasant to touch – and can prevent sharp arrises from cutting flesh.
But I like to go one step further. On the most visible surfaces – the crest, the hands and the seat – I’ll sand a small bevel using my sticks that are coated with adhesive-backed sandpaper. This bevel is about 1/32″ across. And it takes time to do it right. When the bevels meet at corners they need to be the same size.
Has a customer ever noticed this and brought it to my attention? No. But I do it anyway. I love to see the consistent little bevel as it catches the light on the corner of the crest or the hands.
Even if you aren’t as crazy as I am, make sure you break all the edges of the piece before you add any finish.
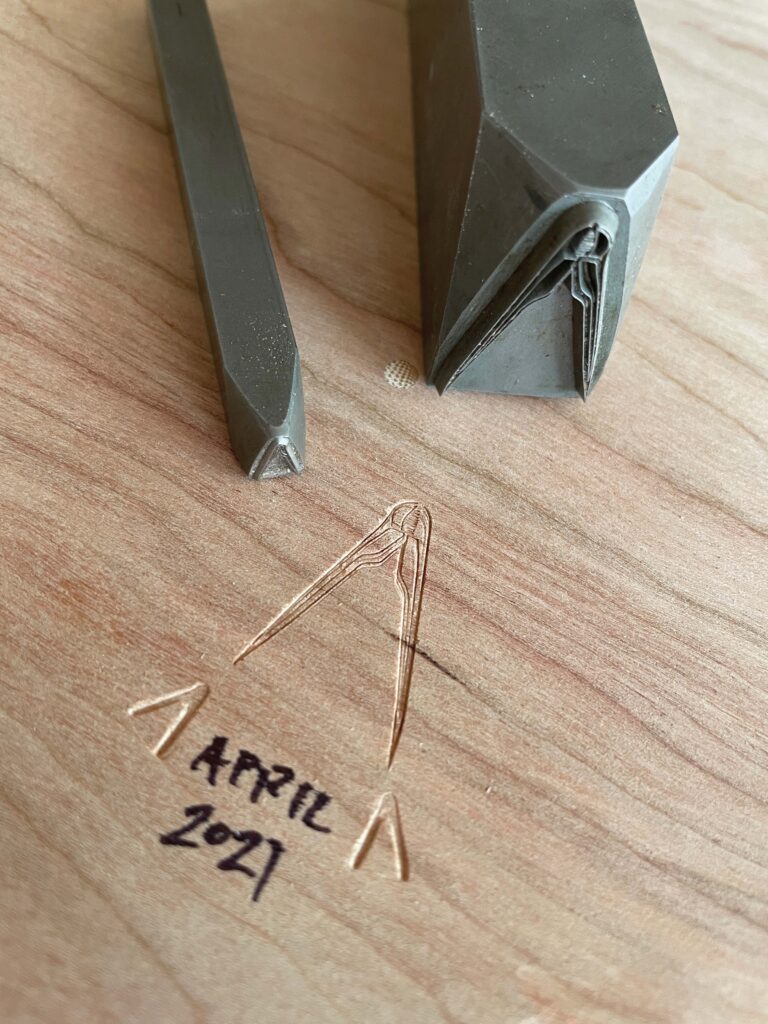
Once I complete the Make Pretty, I have to decide how I will mark the chair with my shop symbol – a pair of dividers. I have two shop marks. One large and one small. I first mark the underside of the seat with the large dividers. Then I add one mark with the small dividers for every error in the piece that nags at me. It might be one or two marks. But it is a reminder that I’m human and I acknowledge my mistakes. (And perhaps some day I’ll make a piece that doesn’t have any small marks.) I’ve never told my customers this, so keep your trap shut, OK?
Lastly, I write the month and the year below my shop mark in permanent marker. I don’t try to imitate old work, but I’d hate for some idiot to represent it to some moron as an antique.