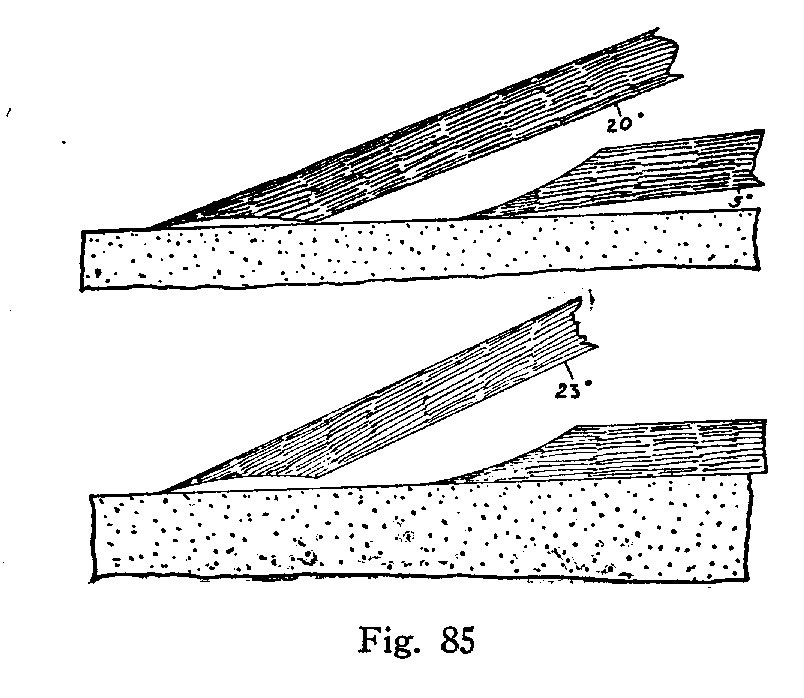
Some people use back bevels on bevel-down planes to increase the cutting angle up from the standard 45°. This reduces tear-out. However, some sources recommend these back bevels for block planes only.
Huh?
Yesterday evening I read “Carpenters’ Tools” by H.H. Siegele (Frederick J. Drake, 1950), which is a fascinating little book filled with surprises. In the chapter on block planes, Siegele recommends honing the tool’s bevel at a very low 20°. Then he says you can either sharpen the back flat or raise the back 5° off the stone.
Siegele says this 5° back bevel is more common than sharpening the back flat. Why is it useful? He doesn’t say exactly, but he states the back bevel is an improvement when the bevel has been hollow-ground on a grinder with a small-diameter wheel.
To me, that says Siegele is trying to improve the edge life of his block plane – especially because he is honing at 20° to 23°. But there’s more at stake than edge life alone when you look at all of Siegele’s advice.
In the book’s section on bench planes, Siegele recommends again a low 20° hone for easy woods, but he says you always sharpen the back flat. No back bevel.
So why use a back bevel on a block plane but not a bench plane?
Easy. The wear bevel. When you use any handplane, the part of the blade that gets the most wear is the little bit of metal that faces down against the work. On a bench plane, that means the primary bevel takes the most abuse. That’s not a big deal because the primary bevel also receives most of the work when you hone it.
But with block planes, it’s the back of the blade that gets beat up and worn away. So a back bevel on a block plane is a very good thing. Yes, the back bevel will improve edge life, but it also ensures that your edge will actually be sharp by getting you to hone away the wear bevel.
— Christopher Schwarz
Like this:
Like Loading...