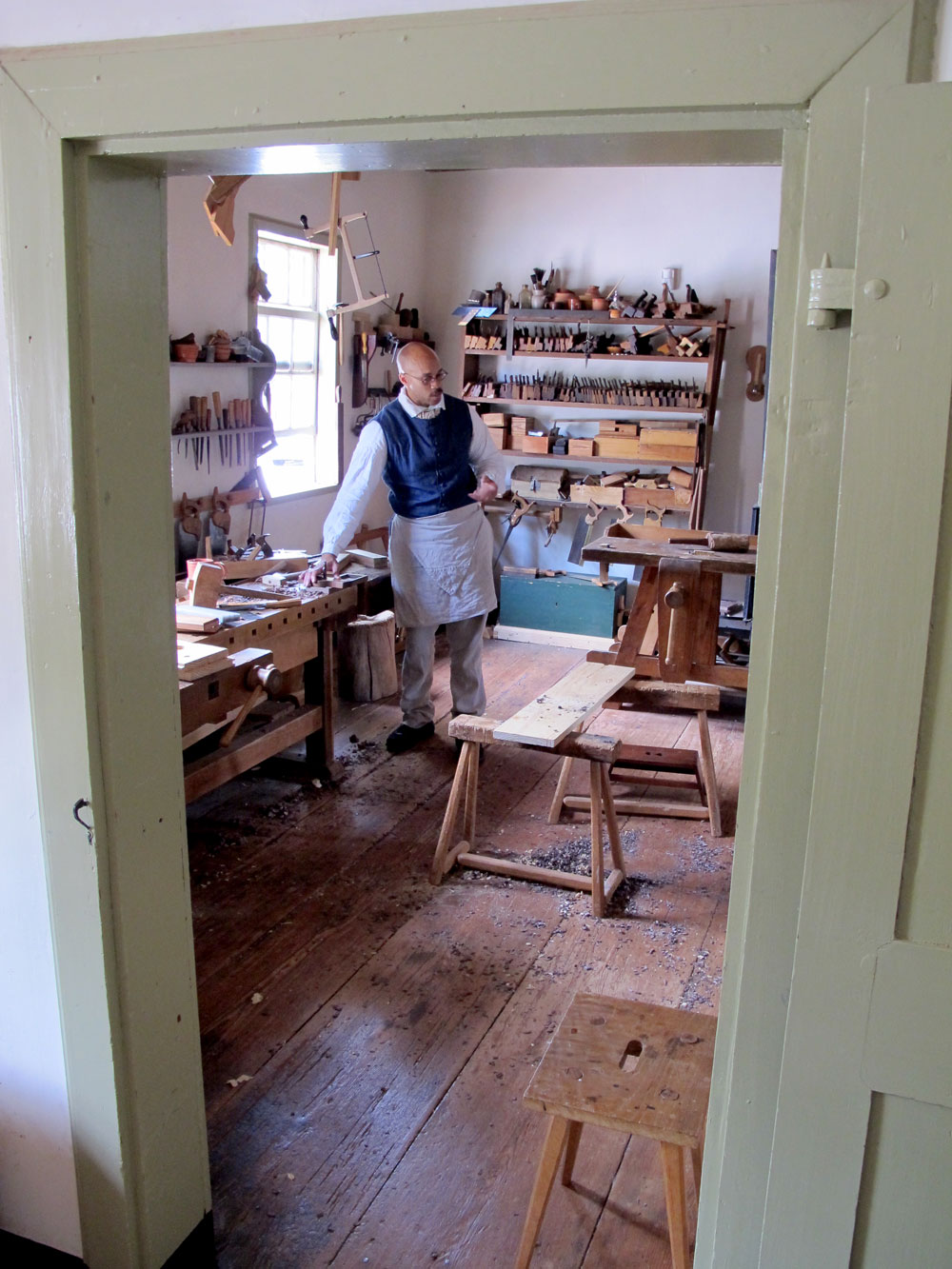
I spent today at the research center of the Museum of Early Southern Decorative Arts (MESDA) on a scouting trip for my upcoming book “The Furniture of Necessity.” MESDA’s research center in Winston Salem, N.C., is an irresistible magnet for this book because of the museum’s “object database.”
This database has 20,000 objects of furniture, metalwork, textiles etc. in it. And you can browse through it to your heart’s content – the research center is free and open to the public (true Southern hospitality).
I pored over the furniture archives today until the research center closed, and I scanned more than 150 photos and datasheets about pieces of furniture that were produced for the middle-class (whatever that is) – or people with austere tastes.
I got some amazing stuff, including some Moravian chairs that are shockingly contemporary. Plus some great stretcher tables, six-board chests, drop-leaf tables and chests of drawers. I’m afraid I can’t show you my scans because they are protected by copyright, but I will attempt to divert your scorn by writing about something else – Jerome Bias!
I got to have lunch with Jerome, a furniture maker and interpreter at Old Salem. Jerome wrote the great story in Popular Woodworking Magazine about Thomas Day and was the guy who introduced me to the research center at MESDA.
When I visited Jerome’s shop at Old Salem he was cleaning out the bottom of an oilstone box he was building using an old woman’s tooth router plane. We had lunch at the local shop of Martin O’Brien, a cabinetmaker, finisher and stone carver.
The barbeque was terrific, of course, but the conversation was even better. Martin does a lot of work on MESDA pieces and had some great insights into traditional finishing that made me stop chewing my food.
So that’s what I did on my summer vacation. And now I have earned a can of Fat Tire.
— Christopher Schwarz
P.S. I did change the title of this blog. Some readers pointed out that using “chicken” in the headline could be misconstrued. Not my intent. Ever. So I just changed it. This is not worth of comment please.
Like this:
Like Loading...