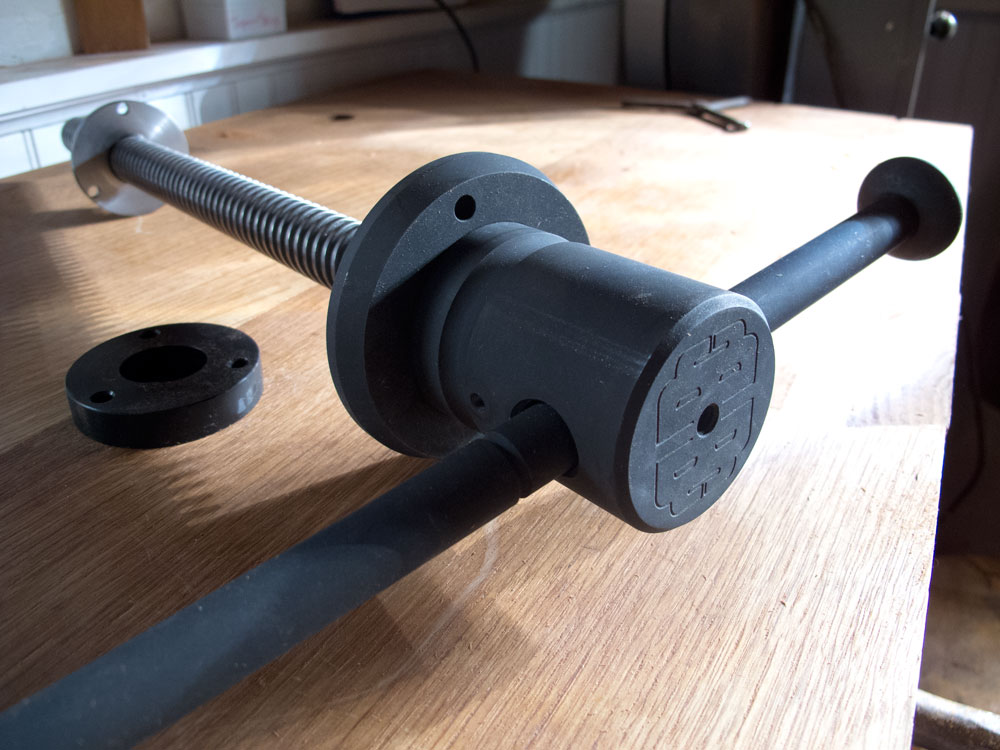
This week I will install a leg vise on my Holtzapffel workbench in our sunroom, which is my shop on the first floor. I’ve had a twin-screw vise on Holtzapffel since I built it six years ago; when I’m done with this leg vise, I’ll be able to switch between leg vise and twin-screw with ease.
I’ve wanted to add a leg vise to the Holtzapffel for a long time, but I waited for one single reason: I wanted to use a Benchcrafted Classic metal screw on the bench. Jameel and Father John Abraham have been developing this vise for a long time, and I finally received my hardware while I was away in either Alaska or Maryland.
I’m going to install the Classic screw in tandem with Benchcrafted’s Crisscross Retro, a piece of hardware I’ve been sitting on impatiently for many months now.
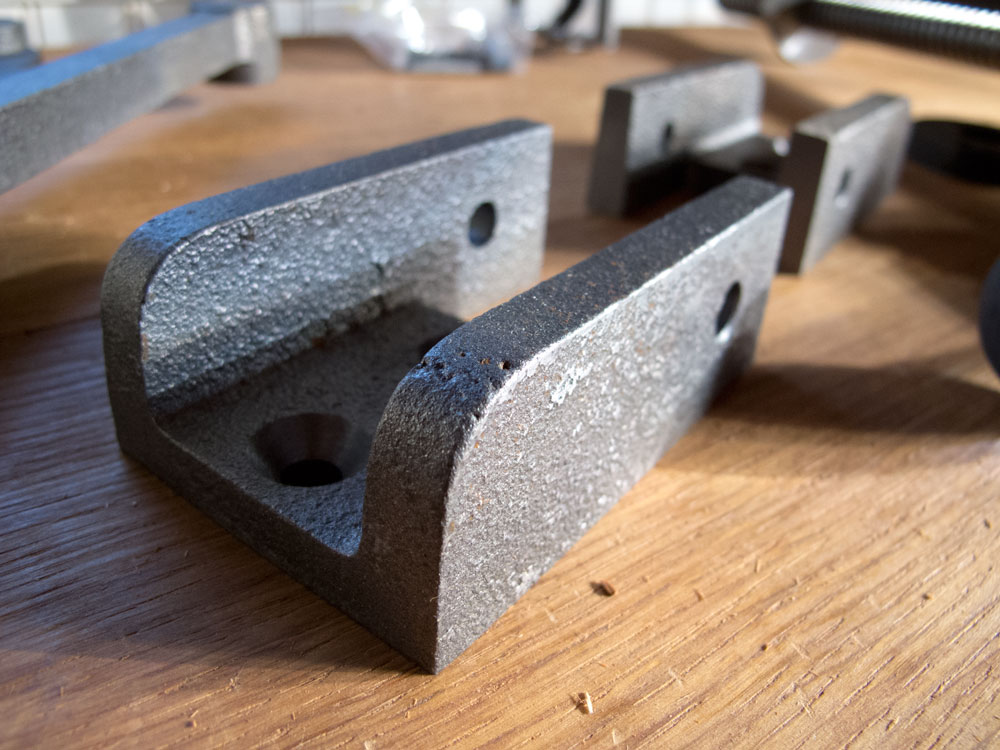
My hope is this will be the most highly evolved form of metallic leg vise yet.
This morning I pulled out all the bits and pieces of the vise so I could plan out the maple vise chop. Handling Benchcrafted hardware is like holding jewelry, and the Classic is equal parts “space age” and “bad-ass.” The screw has a double-lead acme thread, which moves smoothly and quickly (1/2” per rotation). That’s very fast (check out the video on the Benchcrafted site). The machining on the screw and nut are fantastically smooth.
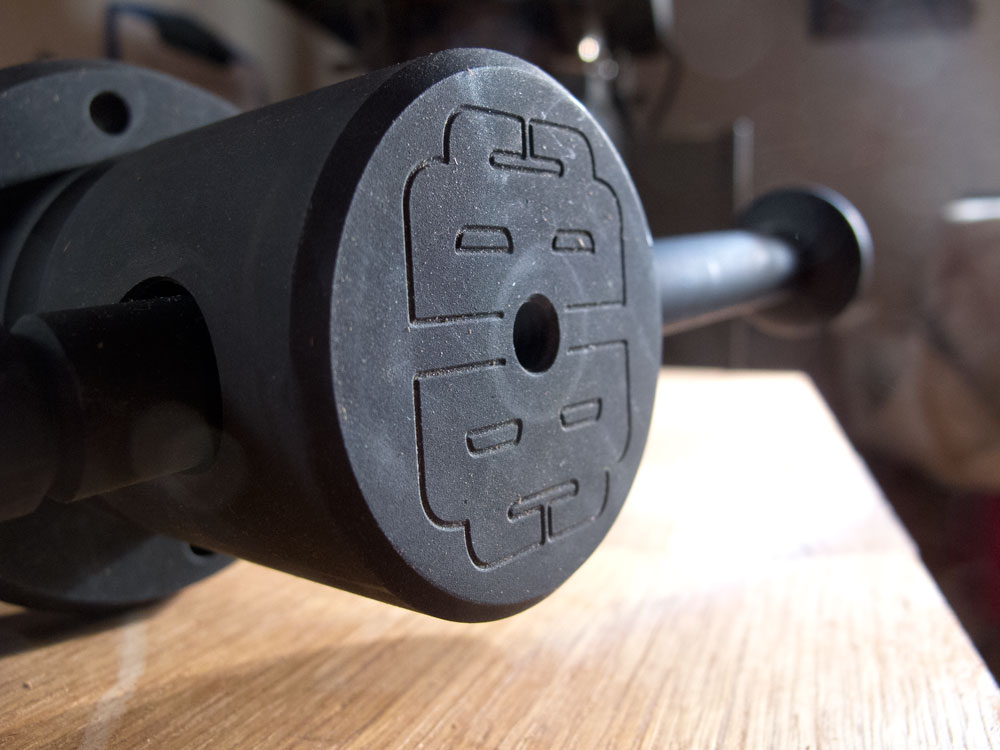
On the other hand, the hub, Tommy bar and flange are “Parkerized” like a firearm, which protects the surface from rust and is way cooler than paint.
The Tommy bar is also thoughtfully designed. The metal ends unscrew. And the way the Tommy bar interacts with the hub is quite cool. There is a detent in the Tommy bar that intersects with a spring-loaded plunger in the hub. This allows you to lock the Tommy bar in the middle of its length for coarse adjustments. Or you can let it swing free for maximum leverage.
It’s almost like magic.
I haven’t been this excited about vise hardware in a long time. If you are considering adding a leg vise or are building a new bench this year, I recommend you take a hard look at the Benchcrafted Classic and Crisscross combination.
— Christopher Schwarz
P.S. I know commenters are going to ask me to compare this to a wooden screw. Save your breath. It’s an aesthetic choice more than a functional one in my opinion. Wooden screws like those from Lake Erie are on par with the quality of the Benchcrafted stuff. So it’s like handplane bodies. Which do you prefer: metallic or wooden? They both work great.
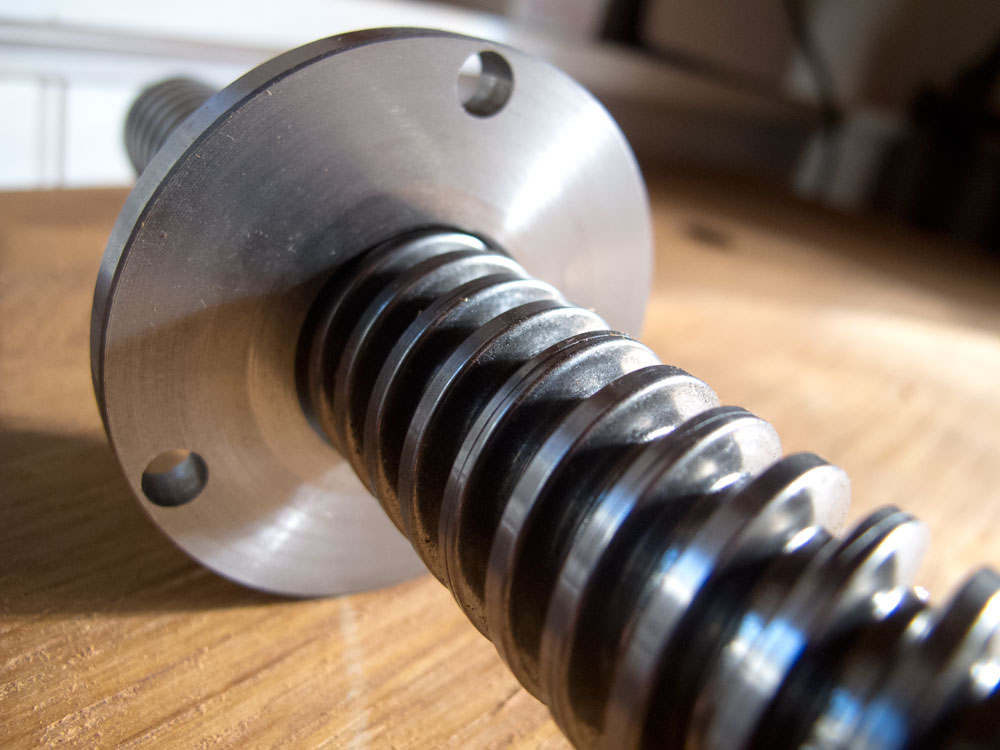
Like this:
Like Loading...