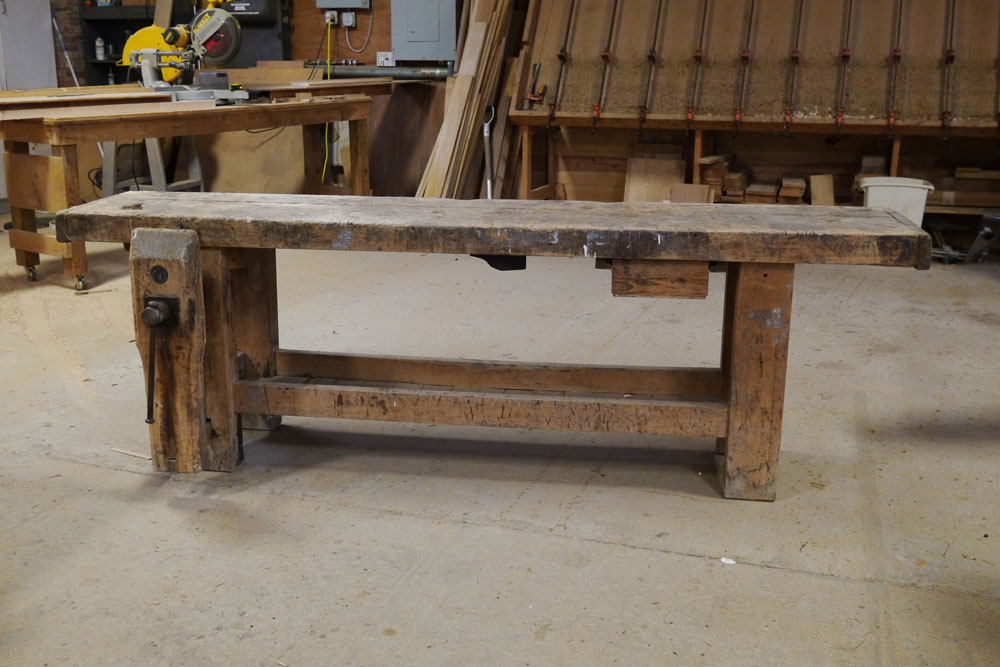
Jameel Abraham at Benchcrafted has been scouting in Georgia to see if there’s enough massive old French oak to put on another French Oak Roubo Project (aka FORP) in fall 2015.
Jameel’s account of his visit to Georgia with photos of big oak can be found here.
If Jameel and Bo Childs do manage to organize a second French Oak Roubo Project, you can bet I will be there to take another chance to work with this amazing material. It is more akin to timber-framing and is both exhausting and exhilarating. The size of the material makes every construction step a challenge.
After last year’s event, I have come up with some techniques to make construction easier and the joinery more precise. So I want another wack.
Stay tuned to this blog and the Benchcrafted blog for details on this event.
While Jameel was in Georgia, he also got to inspect a Féron & Cieworkbench that Childs imported from France. Féron, which branded its products “a la La Forge Royale,” produced tools and workbenches in France.
You can download an early 20th-century Féron & Cie catalog here:
Forge Royale Compressed
This workbench has some interesting details to consider if you have a workbench on the drawing board.
1. No flush surfaces. One of the most striking things about the bench is that the stretchers, front legs and benchtop are not in the same plane (a feature common on earlier French benches). The benches in the catalog are drawn similarly, so I don’t think this one is a fluke.
Make what you will of it. I suspect the non-flush surfaces made the bench easier to manufacture. Personally, I want all those surfaces in the same plane to make clamping doors and long boards a lot easier.
2. A splined or tenoned slab benchtop. One of the details from Jameel’s photos is that the slab benchtop is in (at least) two pieces. Along the seam there are pegs. My suspicion (and Jameel’s) is that there is a spline or loose-tenon in there, and the pegs keep everything together and aligned.
English benchbuilder Richard Maguire uses a similar detail on his benchtops, and he drawbores the loose tenon to keep the seam shut. After talking to maguire and seeing the detail on this Féron bench, I am itching to try it on a future workbench.
3. It’s a knockdown design. The top can be removed from the Féron bench. The top sits on tenons on the legs and is secured with a threaded wooden post.
After looking at the joinery in Jameel’s other photos, I am wondering (but am not convinced yet) if the bench was sent to the customer in pieces and the customer glued up the bits to the base and then attached the top. That is how I’d do it. And it’s how Plate 11 Bench Co. does it. But this is speculation only.
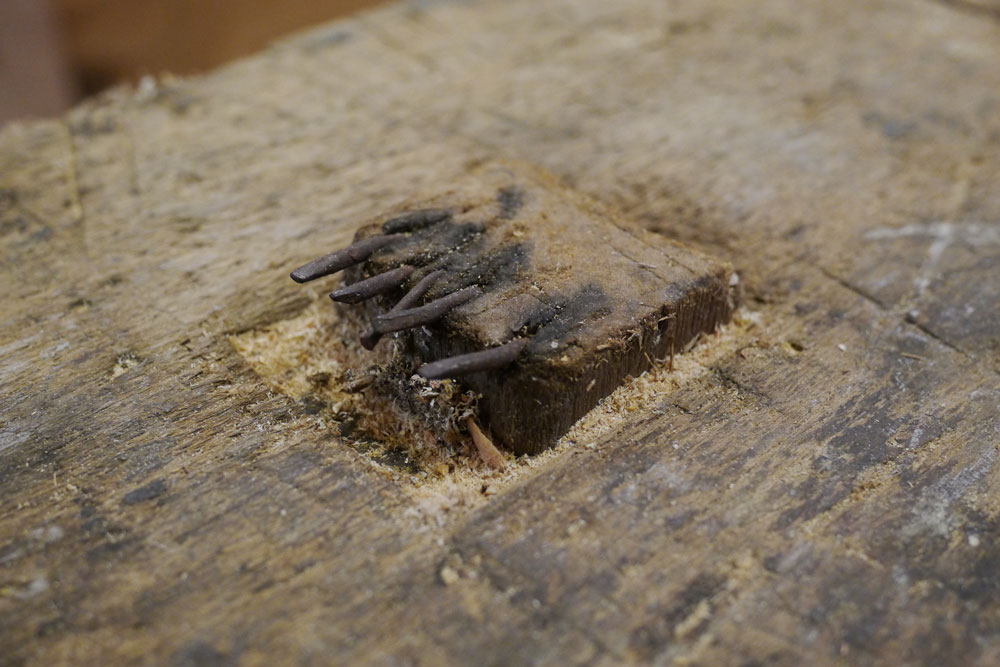
4. Nails in the planing stop. This feature shows up on old benches in place of an iron toothed stop. The benches in the Féron catalog show a planing stop that is just a shaft of wood. No nails. No toothed stop as best I can tell.
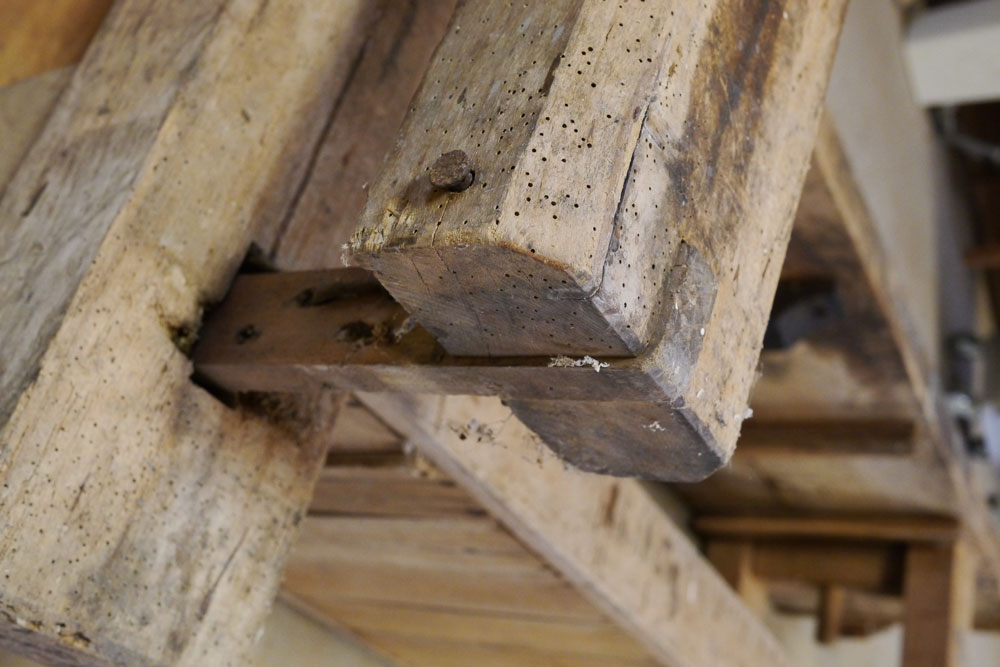
5. A simple parallel guide. The parallel guide in the leg vise is held in the chop with an open notch. This is a time-saving feature for the builder.
Thanks to Jameel for the photos and background information on this important bit of bench-building history.
— Christopher Schwarz
Like this:
Like Loading...