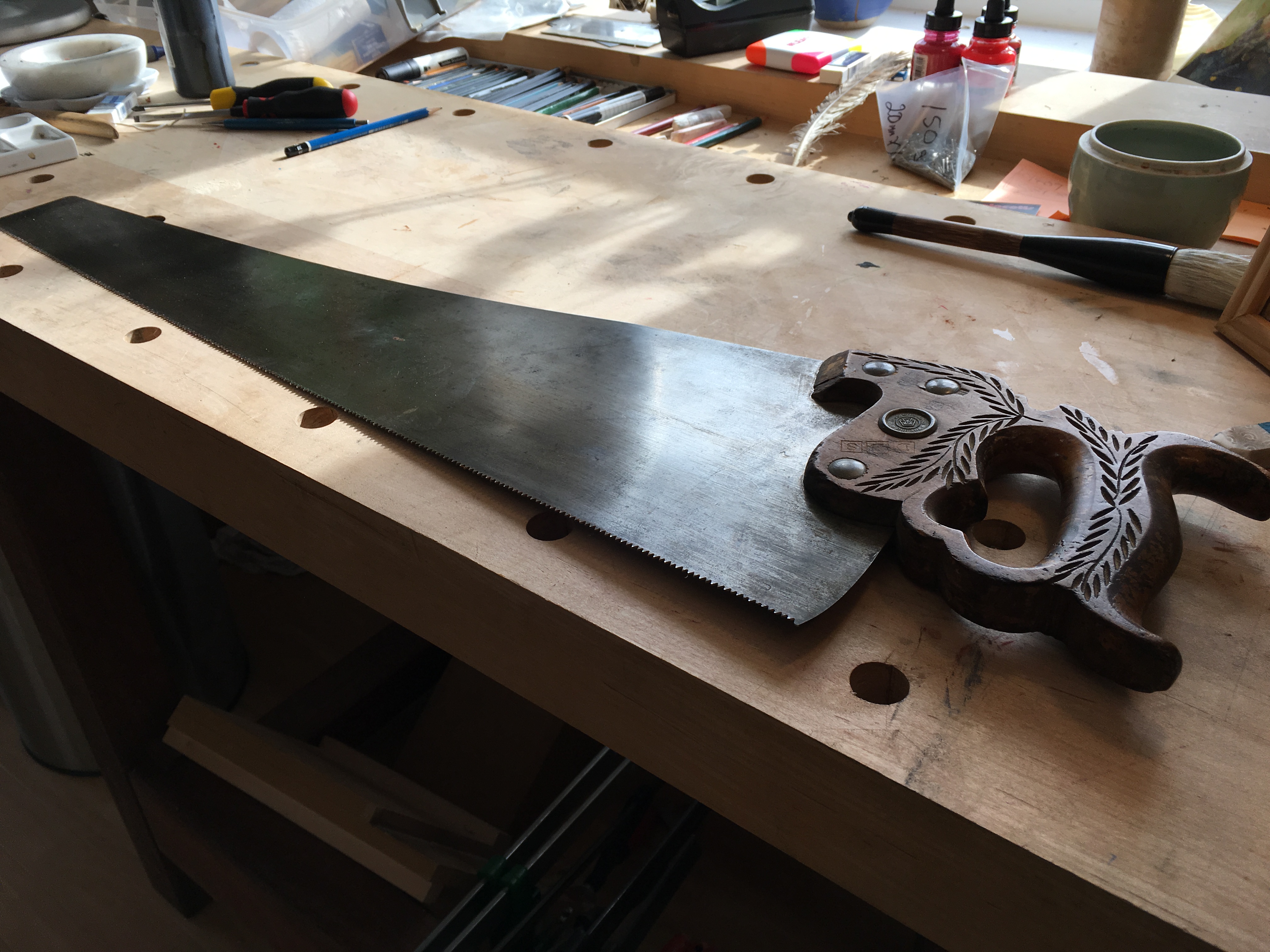
Panel saws, huh? Well I have got a few handsaws. A superb old Disston 10 point hangs on my wall gathering dust. I just got out of the habit of using it; lazy really. The dovetail and tenon saws see a quite a bit of daylight as they are bench saws. I could go to the table saw rather than pick up a tenon saw but I am probably quicker with a tenon saw. And I avoid the shlep. I have a nice, big, well-equipped machine shop just behind the studio here. But it’s a bit of a shlep. So a small panel saw seems to be getting more and more use as I get more confident in using it.
That’s an alarming admission. Yes, I have not used a panel saw as much lately as I did when I was younger. You forget a lot in 40-odd years of furniture making. That is the effect of the machine shop. The band or table saw are just too good, too reliable to not be used in this role every day. And the panel saw takes effort, work, sweat. All of which is pleasant to avoid on a warm sunny day – unless really necessary.
But it’s nice cutting down a line with a small panel saw using a sawhorse properly. No screaming router, just argh, argh argh. I wish I had had one years ago. My old Disston is great, but somehow too big, a small panel saw can become a bench tool, like a tenon saw. Saves a lot of shlepping about.
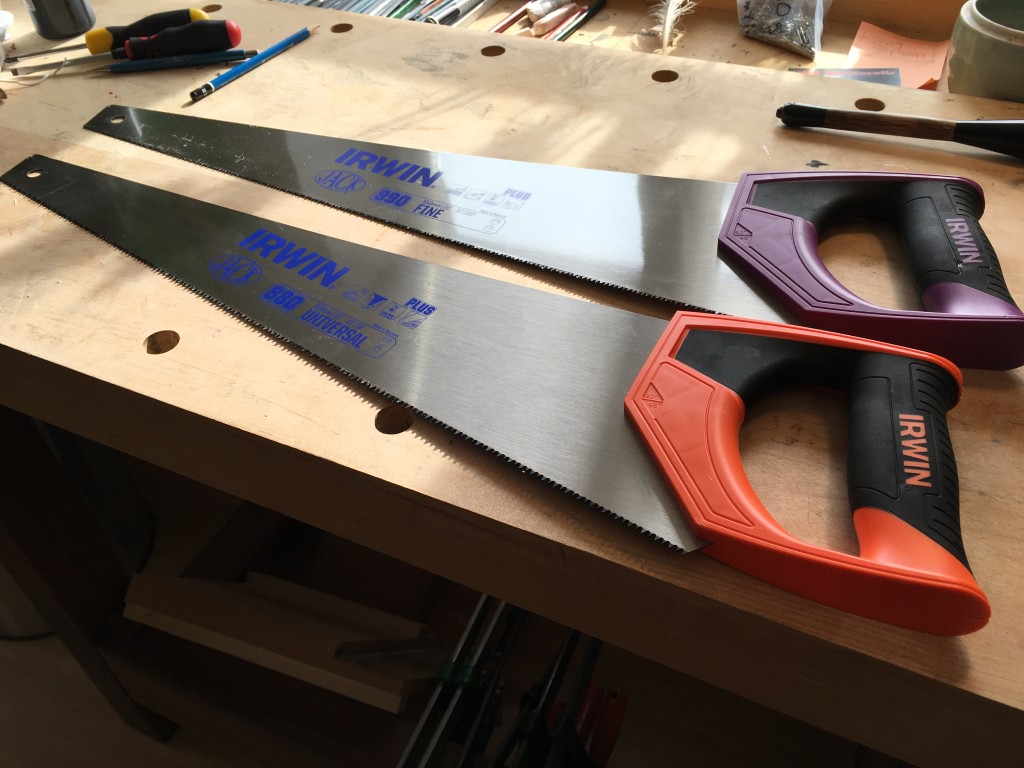
So what have we got for this young person’s tool chest that will make any sense? The biggest change in saws that I have seen is the arrival of the cheap, throw-away saw. These we have all over the shop; they hang on hooks behind almost every door. These are board saws. They usually have a Japanese tooth pattern and get loads of use quickly ripping up board material or crosscutting the odd bit of solid.
It’s hateful, but we buy them, use them and chuck them away. It’s a scandalous waste of resources that we should be ashamed of, as my daughter would tell me. But saw doctors are getting older and not being replaced. Our saw doc, Brian Mills, is retired now; thankfully he still does all our hand saws and planer blades. Getting them back into shape after we have mutilated them. Don’t tell him, because he would put his prices up, but he is invaluable. I don’t think Brian has trained a replacement, and when he stops, which will never happen, we are in trouble.
First up are the two cheap throw-aways: the Irwin 990 Fine with a 10-point toothline and a disgusting purple plastic handle. There is also an Irwin 880 Universal 9 point with a disgusting orange plastic handle. They are both razor sharp to a state that they can easily cut you very badly. Both these do a great job, and I will not dwell upon them. Our experience is that the toothline holds up so well that you don’t chuck them away as soon as you should. This means you find yourself working much harder with dull saw than you should. Was that not always the way?
I will keep the purple one; it goes with my purple tool chest. So the orange one goes to our winner. What winner? You must have heard? Well, we are gathering tools to fill this tool chest. One Chris Schwarz made when he was here with us at Rowden in the summer. And we are giving it to a young maker under 25. Application details are here.
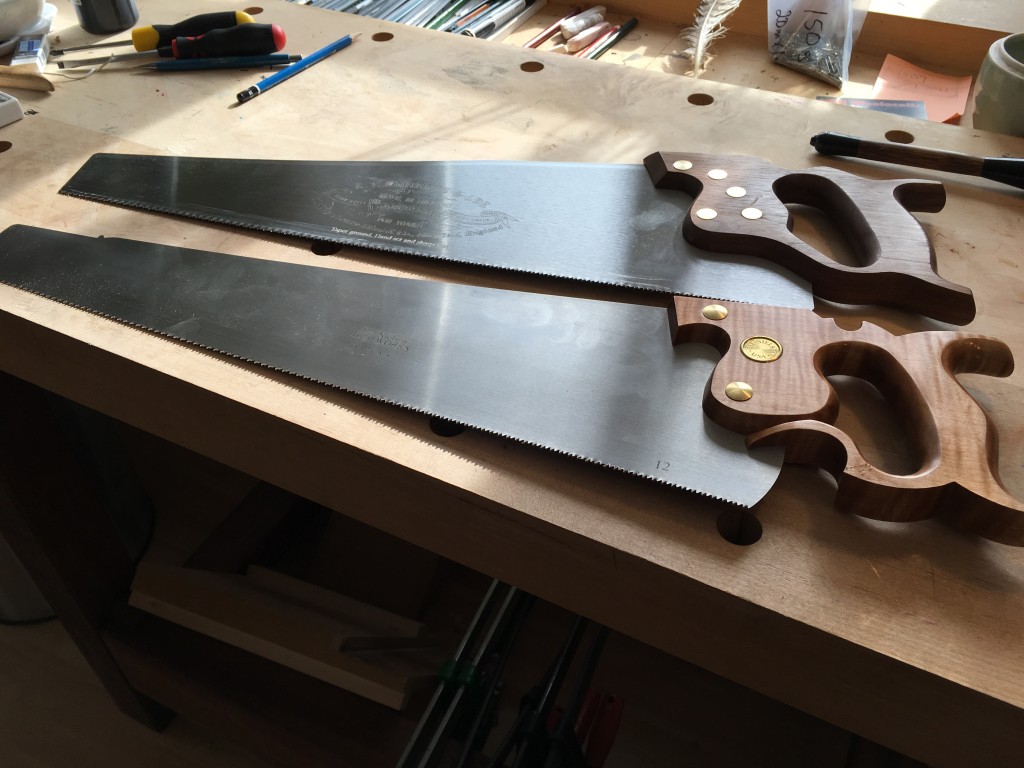
Now we come to the meat. Two of the best panel saws I could lay hands on. If I missed your saws I am sorry but I can only look at two. These are not “review” saws; I bought these and paid a pretty penny for the Lie-Nielsen 12-point crosscut saw at £174.46 from Axminster Power Tools. The best British saw I could find, and I can’t avoid wanting to support British tool makers, was from Roberts and Lee. Their Dorchester range made now by Thomas Flinn and Co. of Sheffield. This is another 20”, 10 pointer crosscut but at £100.31. Alan Peters had Roberts and Lee saws; my first dovetail saw was Roberts and Lee. So they have history with me. Not all of it good.
These are very different saws apart from the price. One is a stiffy one a floppy. Both are taper ground, meaning the plate of the saw is ground thinner near the top of the saw to give clearance. Both claim to be hand sharpened and indeed both cut very well. The differences come with the handle, the plate and the toothline.
The handle of the LN saw is beautiful, a ripple maple piece of work clearly inspired by Disston. Handles matter. It’s the bit YOU engage with. The junction of handle to the blade matters. This fit on the LN saw is pretty near perfect. The Dorchester saw handle is pretty crude in comparison without the decorative embellishments of the LN. But it fits my hand OK. The fit of the blade to the handle of the Dorchester is tight with five fixings, but the kerf of the cut the plate fits into is still a deal wider than the saw plate. The LN saw seems to be perfectly matched, kerf in the handle, to plate held in place with three brass fitttings.
The plates of these saws are fundamentally different. The Dorchester is a stiff saw with a thicker blade The Lie-Nielsen saw a floppy thin bladed saw in the Disston tradition. You could play a good tune on the LN saw. This is a personal preference thing. Common wisdom was, stiffies for board stuff and floppies for solid, but I don’t think that is totally true. I like the stiff blade of the Dorchester in this small saw, and it seems to cut well for me. Not that the Lie-Nielsen panel saw doesn’t do a great job.
The last difference which makes me sing with happiness is the breasted tooth line of the Dorchester. If you look down the line of the teeth they are not straight but slightly domed. Not much, probably a quarter of an inch. But that for me makes a difference. It’s to do with the geometry of my arm swinging away and the teeth engaging in the timber. Missed a trick there Tom.
Beautiful though the Lie-Nielsen 10-point panel saw is, I am going to put that saw in the prize winning box and keep the Dorchester for myself.
— David Savage, finefurnituremaker.com
Like this:
Like Loading...