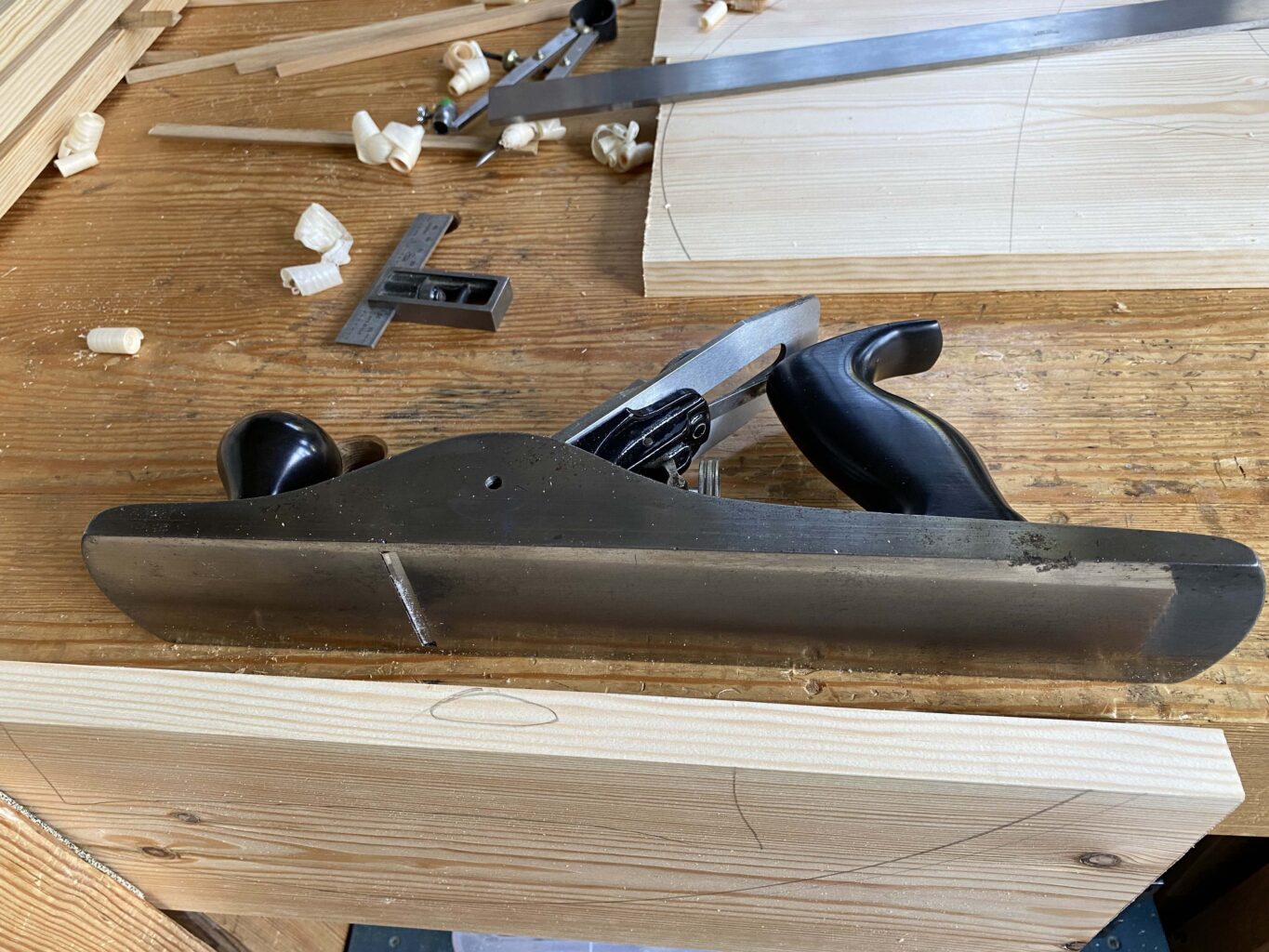
When Derek Jones was planning for his summer trip to teach at Lost Art Press, he asked if we had a No. 6 he could borrow. A No. 6? Really? I thought it was a typo. I’ve been fully inculcated into using a No. 7 (or No. 8, if I must – and I’ve eaten my Wheaties) as my jointer, but Derek has good arguments for using a shorter plane. I was working at the computer and heard snippets of his teaching his class why (as he instead used a No. 5 – of which we have several), but I didn’t pay close attention.
Now, as I edit his forthcoming book on cricket tables (which we hope to have out in the first quarter of next year), I’ve came across the No. 6 lesson in writing. In Chapter 5, he’s writing about the tools and techniques he uses, and shares his history with struggling to get a good edge joint in panel glue-ups (a decent-sized cricket table will need a panel glue up for the top).
The No. 6 was not a typo; it is Derek’s answer to how he achieves panel-prep success.
– Fitz
Two things come into play when you “go large” in the plane aisle. The first is linked to the size of the user and the second is more to do with the scale of work. I’ve read hundreds of how-to texts on planing and I don’t think I’ve ever come across a specific mention of the suitability of a tool in respect of it’s size in relation to the size of the user (notwithstanding advise for children). As far as I could make out, it was a given that larger planes are better for leveling larger boards and the science was often quoted to back the theory up. I like science, I like maths and I like it when they come together, but unless they take into account the human factor, they’re not really much help.
So in context let’s say for example I buy a No. 7 jointer for truing the edges of long boards. It wouldn’t be out of the ordinary; after all that’s what is generally recommended and therefore accepted as good practise. If we accept that advise (the science) but now ask “how long is a long board?” (the maths) we’re starting to get close to what an appropriate size plane might look like. My vital statistics (the human factor) are height 5′ 5-3/4″, weight 140 lbs. Do you honestly think I’m going to be in complete control of a lump of cast iron weighing in at around 8-1/4 lbs. when I’m trying to remove a sliver of wood 0.001″ thick from an edge measuring 3/4″ across? The short answer to that is no, but you’d be surprised how long I persisted with that set-up before finally addressing the problem.
The secret to many things in life is good communication. I learned this lesson on a visit to a well-established tool auction to meet up with a friend who had a sideline in trading old tools. Always willing to share his expertise, he singled out a Stanley Tape and Rule Co. No. 6 bench plane with rosewood handles as being good value. I hadn’t come to the auction to buy a plane but made a note of it anyway.
After sitting through dozens of lots and being outbid on everything on my list, the No. 6 came up. I figured I’d either been too cautious so far to win anything or the room had become stale. I left my seat in the second row and relocated to the back of the hall, acknowledging my friend on the way. My tactics paid off and I came home with a new-to-me No. 6.
Some time later while I was demonstrating at a woodworking show, my friend dropped by my booth and picked up the No. 6, now tuned and performing like new. I told him where it came from and what I’d paid for it. “You’re joking” he said. “I was bidding on that, you should have said.” That No. 6 has become my go-to jointer for boards of any length and my two (yes two) No. 7s are now part of someone else’s collection. The No. 6 is shorter than a No. 7 by 4″ and about 3/4 lbs lighter, making it something I have complete control over – and that’s the key.
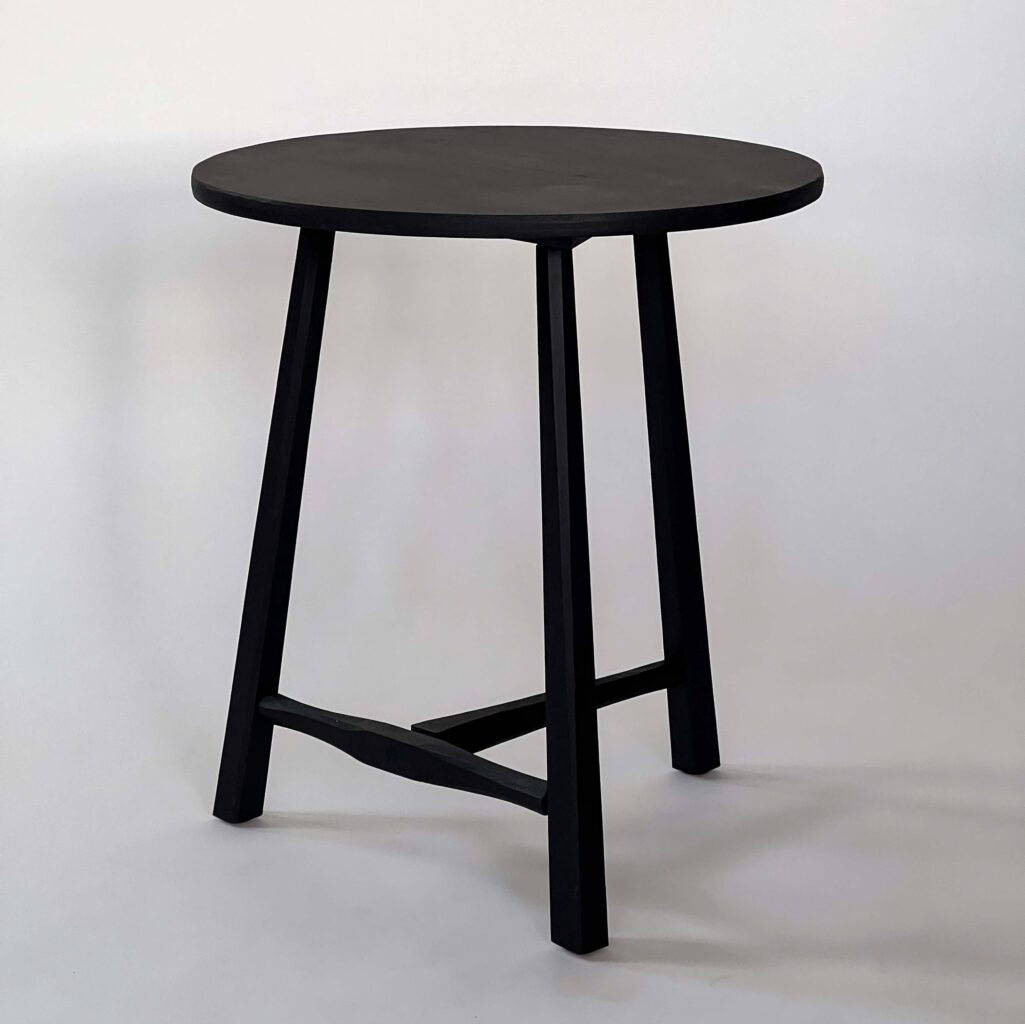