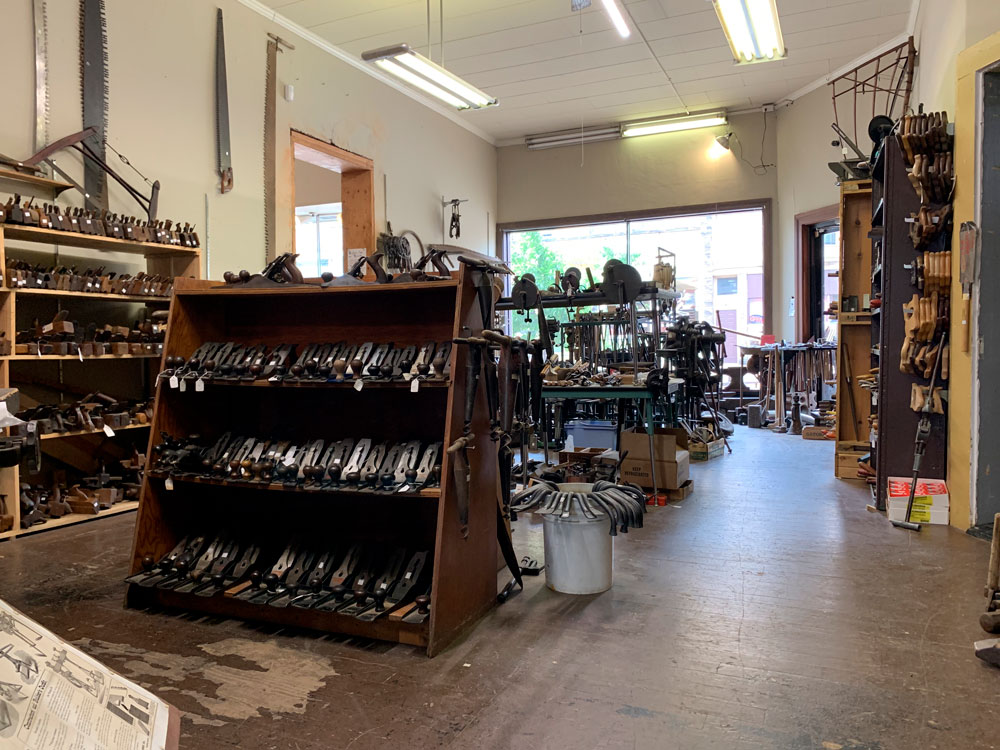
When people start venturing into hand tools they struggle mightily with what tools to buy and where to get them. As far as what tools you need, I’ve tried to cover that with “The Anarchist’s Tool Chest.”
When it comes to the question of where to buy the tools, my usual response is to attend a Mid-West Tool Collectors Association meeting. Or a meeting of the Early American Industries Association. I’m a member of both organizations and am so glad they exist. The tool tailgating at these meetings is epic.
But not everyone can plan their lives around these meetings. Or they can’t wait for a meeting to roll around to get started. Or something something something don’t wanna.
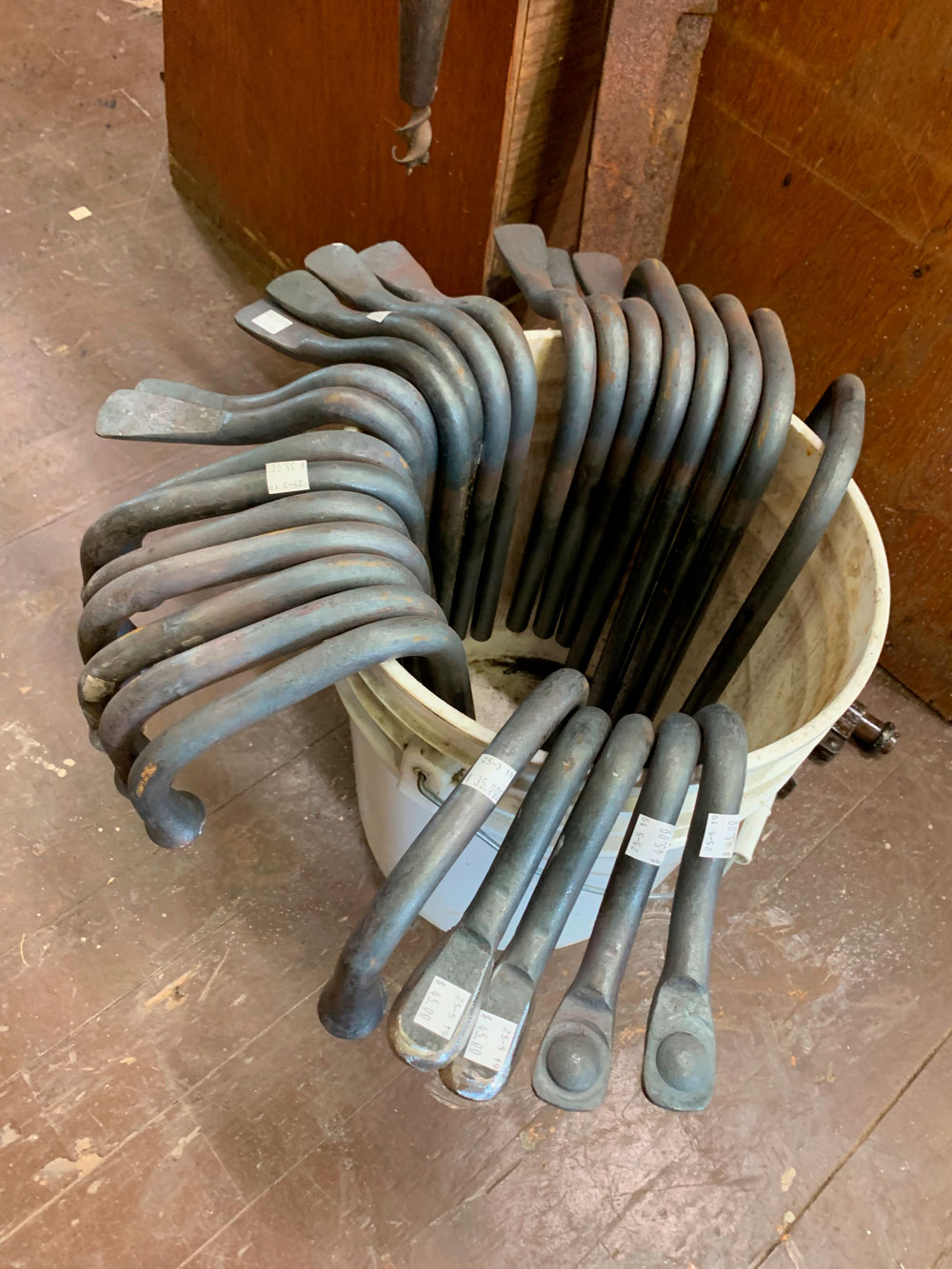
If you live in America’s Great Middle, I suggest you plan an excursion to Colonial Homestead in Millersburg, Ohio. I’ve written about Dan Raber’s tool store before for Popular Woodworking and discussed their classes yesterday on the blog.
But I just want to say here, on this blog, one more time, that Colonial Homestead is a Midwestern jewel.
What is so good about this place? The depth and quality of the stuff on his shelves. He has more woodworking and metalworking vises for sale than I’ve seen anywhere. Need dividers? There’s a whole section of them. How about a tool chest? Yupper. He’s got a bunch with prices starting at $275. There are drawers filled with spokeshaves, beading tools and Perfect Handle screwdrivers. A glue pot section. Boxes of complete sets of auger bits (in the bit section). So so so many saws. A wall of chisels, arranged by size.
After years in the craft, I’m pretty jaded by tool stalls in antique malls, which are usually filled with stuff that should be melted down. Buying stuff on eBay isn’t much better (unless you know the seller). And amassing a kit from people such as Josh Clark at Hyperkitten or Patrick Leach at Supertool can take a long time as you wait for the right stuff to come up for sale.
Colonial Homestead is a way to get a good working kit in one long visit.
To be honest, I haven’t bought much from Dan. I already own a complete kit of hand tools. During my most recent visit I bought a bunch of blacksmith-made rosehead nails (yes, they sell those). And I found a gorgeous cast-iron Defiance utility knife to replace the crappy zinc one in my chest. But I love to look over his wares when I visit. He’s got great taste in tools.
As always, I’m compelled to mention that this enthusiastic post isn’t sponsored. I am simply an admirer of what Dan has built in Millersburg. And I think you will be a fan as well.
— Christopher Schwarz
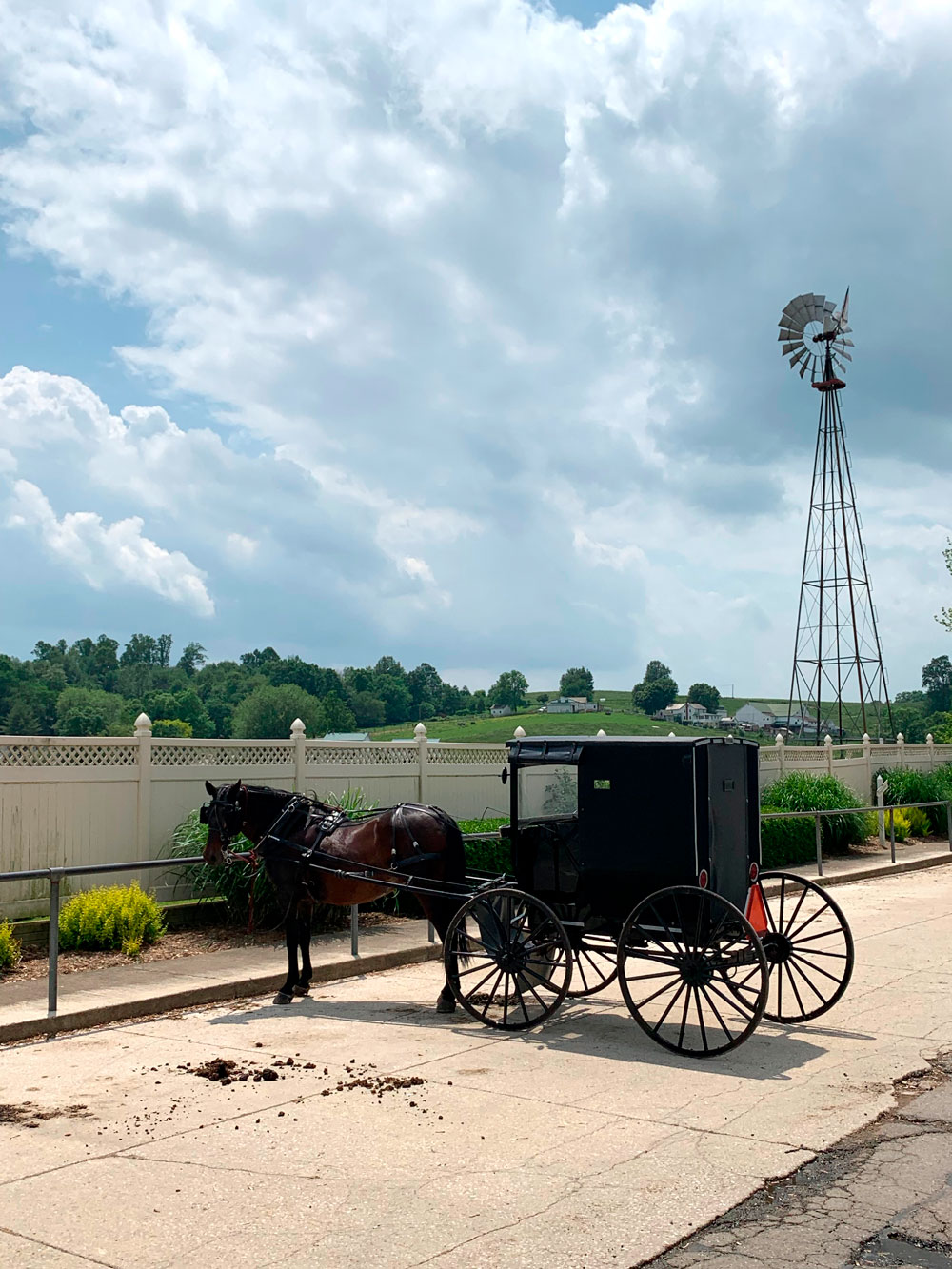
Like this:
Like Loading...