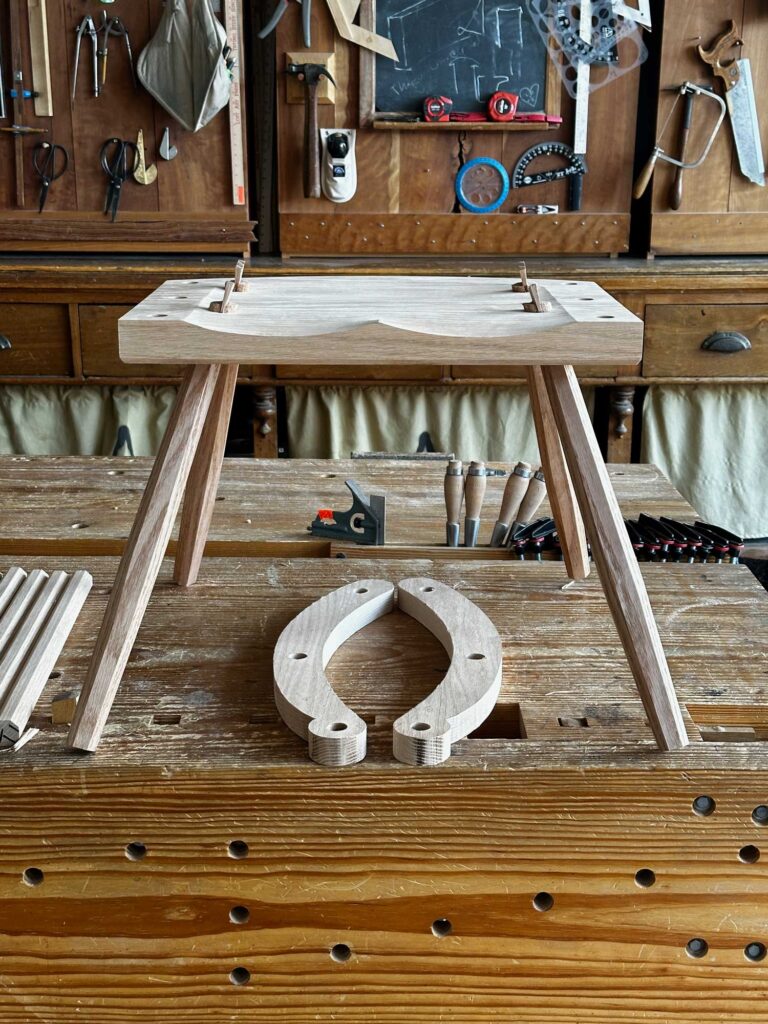
Megan is finishing Matt Cianci’s book “Set & File: A Practical Guide to Saw Sharpening,” and I’m polishing “The American Peasant.” Both books will go to the printer within the month, and then we will turn to our next publishing projects.
Here’s what is coming up.
Megan is (still) working on her Dutch tool chest book, and she’ll also take the reins on Jim Tolpin and George Walker’s next book, “Good Eye.” Their early drafts have convinced me this will be their best book. For this book, George and Jim are deconstructing pieces of furniture to show their underlying patterns and language.
Also in the works: Kale and I just began filming a long-form video on building and using a Roman workbench.
And I will dive into the next issue of “The Stick Chair Journal.” I have been working on the second issue off and on, and I promise it will be out before the end of 2024. The delay on “The Stick Chair Journal” has not been due to a lack of enthusiasm. Quite the opposite. My list of stories for the second (and third) issues grows every week.
Mostly, I have been stalled by our 11-month-long restoration of the Anthe building, our new fulfillment center. Finally, work on the Anthe building is winding down. This week we’re repairing the basement stairs and waterproofing the second-floor doors over the loading dock. These little projects are much easier to tackle than say: pay for a new roof, sunlight, gutter and reconstruction of the rear masonry wall.
Aside from the Anthe building, one of the obstacles to the next issue of “The Stick Chair Journal” is which chair plan we will publish in issue two. I have seven designs I’ve been working on:
Comb-back with a plywood arm and comb
Settle/Settee
The Shortback
Irish writing chair
Peasant chair
The Stout Lad chair (a chair for larger body types)
Hobbit chair
I want to build them all. And given enough time, I will. Since writing “The Stick Chair Book” (a free download), I have been moving chair-by-chair to a particular chair form in my mind. The two chairs on my bench right now (shown above) are a significant step forward to that chair – both in form and the natural dye I’m cooking up.
Or maybe I’m just fooling myself and “that chair” will always be on the horizon.
— Christopher Schwarz