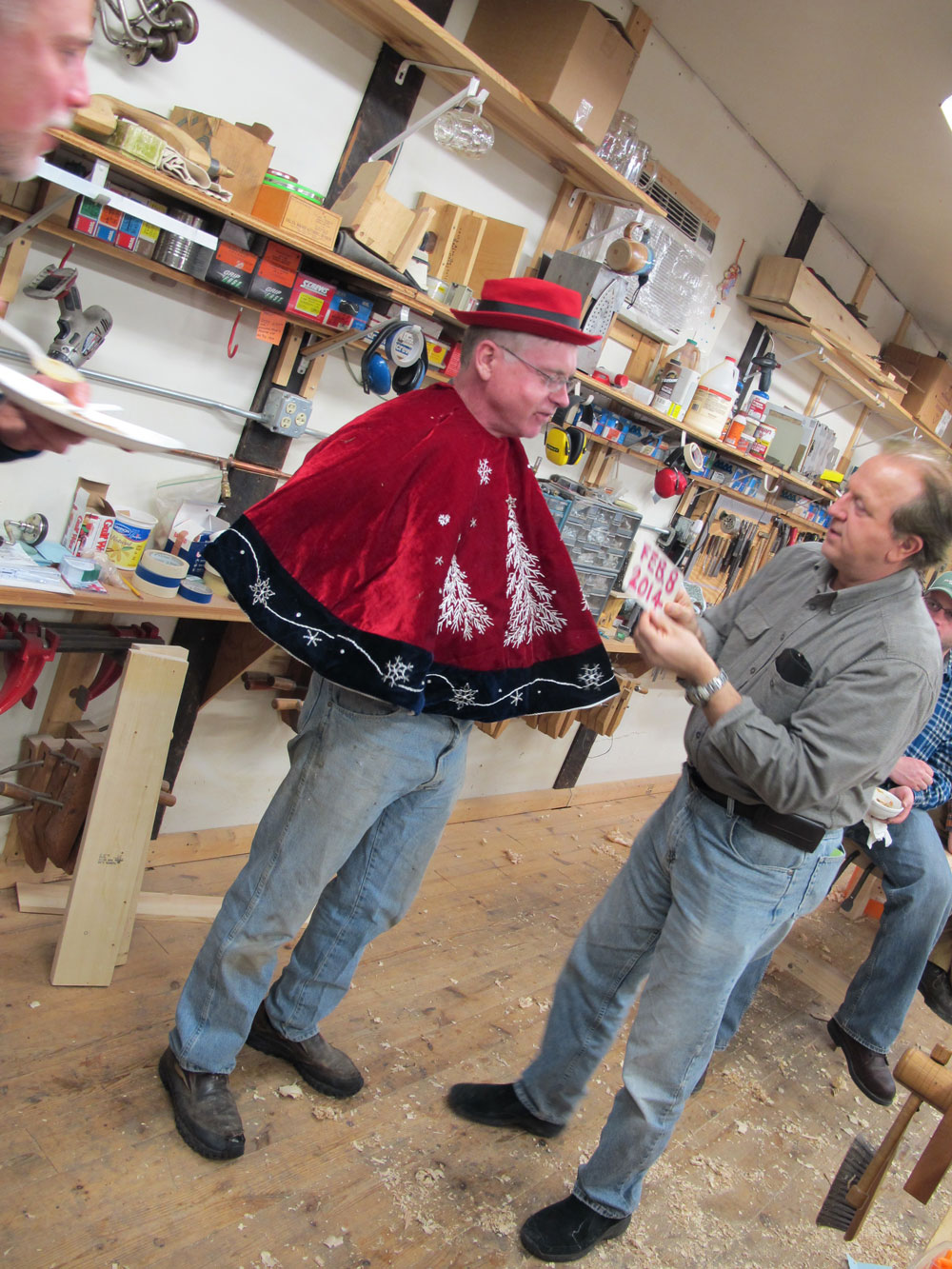
In this segment, we visit The Naked Woodworker, the oracle of east-central Minnesota, to ask his advice on the following important questions.
1. Oh Naked Woodworker, tell us the truth about safety advice. It’s mostly legal, cover-one’s-behind stuff, no?
The Naked Woodworker speaks: Avoid injury! There is no greater loss to a woodworker than an injury; while most injuries are small cuts that are fairly easily taped over, you still get blood on your work and have an annoying sore spot to take care of until it heals. The bigger wounds might require stitching, which involves time away from your shop to get sewn up, time lost to heal if the wound is in a bad place, and money out of pocket to pay the doctor. We won’t talk about more severe wounds, which have more severe repercussions, such as the loss of the ability to count to 10 or pick your nose. Be careful, read instructions, follow them, wear safety glasses and dust masks, listen to your “gut” if the voice in your head says, ”Don’t do that.”
2. Oh Naked Woodworker, where will I find tools and wood to make things? For we are naked and have no such objects.
The Naked Woodworker speaks: You will need tools, wood and a place to work and store your tools and materials. Be creative. Perhaps you’ll have to work outside and store everything in a garden shed; if you don’t have a shed, that could be a good project. Figure out how you want to work; both hand tools and power tools can be found on Craigslist. Be patient and watch for a good deal.
It is a good idea to have a small trailer for getting materials and machines. Small trailers can be found on Craigslist as well. If all you have is the back seat of a Miata or a bicycle, you will be severely limited in your ability to jump on deals when they arise. Though I have been able to pick things up via motorcycle as well. Many items will easily fit in the trunk of a car, but lumber can be tricky. Roof racks are good but be sure to tie things down well; be creative.
Keep it simple at first. Build a sawhorse and a workbench of the type that suits you and your method of work. I find the English joiner’s bench to be inexpensive, very functional and easy to make. Workmates and sheets of plywood on sawhorses work as well.
3. Oh Naked Woodworker, what is the most important tool in the shop?
The Naked Woodworker speaks: Without knowledge of your tools and material, you will be lost. Learn the basics, put down a solid foundation of how tools work and how wood behaves, or misbehaves. Learn to sharpen and maintain your tools and equipment quickly and efficiently. Your brain is your true power tool, make sure it is turned on before you enter the shop. You don’t want to say, “I knew better” or, “I just wasn’t thinking.” Your mind is where you keep your most important tools, make sure it is full and well maintained.
Take a class and try other people’s tools. Learn how to sharpen and tune any tool you own, power or hand tool. Buying tools will not give you skills! Skills come with training and practice; they are earned! Many machines are very dangerous; learn how to operate them safely by reading the manuals that come with them. Know what makes a tool or machine “good.” Price is not always an indicator of quality. Buy the best tools and machines you can afford.
The broom is the second-most most important tool in the shop. Keep your shop clean, and when you drop a tiny screw or break a chip off of a dovetail you might be able to find it. When you hit a tough spot in a project and don’t know how to progress, or you had an upsetting phone call and are stressed out, sweep the shop to music. Put things away and tidy up. Soon you feel better and can get back to work. You may even come up with a solution to your tough project. You will get far more work done and have fewer tools fall off the bench and break in a tidy shop. If you can’t find a tool in the shop, start putting things away until it turns up. Don’t simply search for it. When you go into your shop, always put 10 things away.
4. But Naked Woodworker, we did not ask about the second-most important tool, for we are slovenly. But where can we purchase such knowledge and skills?
The Naked Woodworker speaks: Take classes to gain skills. Create or join a group of like-minded people, SAPFM, M-WTCA, PATINA, or local guilds and learn together. Bring in a teacher and create your own class. Knowledge is your best tool for saving money. Learn, practice, learn some more and improve by practicing. Do not practice poor technique.
The Naked Woodworker has spoken.
— Mike Siemsen, Mike Siemsen School of Woodworking
Like this:
Like Loading...