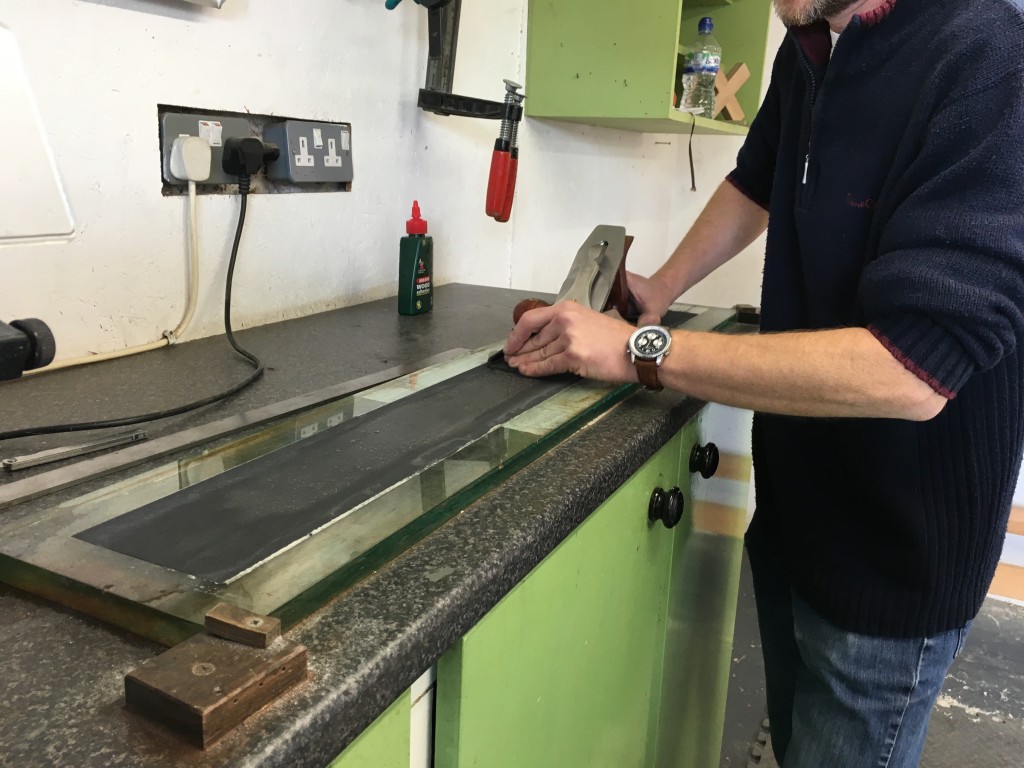
This will be Political. Bench planes always are.
I have, I must admit, asked Matthew at Workshop Heaven to donate here. I will, where I can afford it, buy tools in, like the panel saws and see if I can upgrade my own tool box. I will then pass one of my saws on to the young person who will get this tool chest. (They only have one more month to apply.) I wanted a No 6 bench plane; what Matthew sent me very kindly was a 5-1/2 Quangsheng. My aim was to look at these planes again. When they first came on the market I reviewed them and was less than happy. They have since revised these planes and they seem to be getting a good place in the market. I am delighted by this. From the point of view of the young maker with shallow pockets, I hate it that good tools are shiny and rosewood decorated, and expensive.
I have got a Lie-Nielsen No 7 in one of the many student tool boxes here that is a strong candidate. It’s in use at the moment so Jon’s No 6 is showing in my images. My comparison is between the Cheap Chinese and the really good Yank.
First a credit to the work of one man. Tom Lie-Nielsen has done more to enable good making to carry on, in my lifetime, than anyone I know. Quite simply he has put tools out there that give you a chance. For years in the 1980s and 1990s I wrestled with steel bananas. Tool-shaped objects created by marketing departments and accountants that challenged anyone attempting to learn to make. What was wrong you, or the tool? That they were patently not fit for function took us some years to establish. I vividly remember one student flattening a Record No. 6 eight times in 12 months and the damn thing was still moving! Tom gave us flat planes, and publicly, I thank you. Veritas followed behind often with “that’s a great solution but what exactly was the problem?” Their contribution should also be applauded. Alan Reid at Clifton gathered the remnants of a destroyed Sheffield tool industry and heroically attempted to enable good affordable bench planes to be made available to us. His forged steel Victor blades were in all planes at Rowden that could be modified to take them. I am desperately sad that these blades are no longer being made and not offered by the new management at Clifton.
The Western bench plane is a precise and complex version of a chisel stuck in a block of wood.
When any bench plane comes into the workshop at Rowden we check the perimeter flatness on a ground granite slab that has been certificated for compliance to almost atomic flatness. I remember it cost me an eye-watering amount of money. They go on this slab and our finest now rather crumpled feeler gauge is tested around the edge. Most planes these days get past this test (or they go back!!). It’s what is going on in middle of the plane surface that concerns us next.
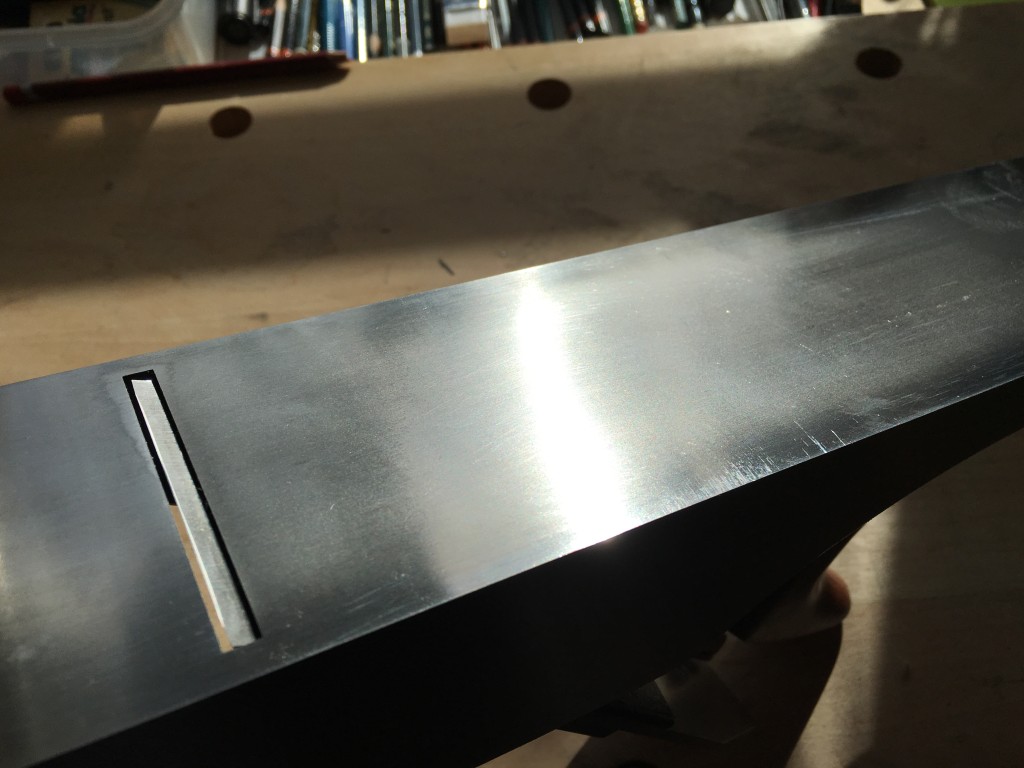
Putting a straightedge across the plane sole from side to side now slip that feeler gauge under the blade in the centre of the plane sole. Tom’s planes generally come out quite well with half a thou being the worst. This we remedy in the time-honoured way with thick sheet glass, checked for flat, well-supported as a surface to work on. We use double-sided tape rather than spray adhesive and #180-grit wet and dry paper and a little water. There should no need to do too much work on the sole to get most of the hollow out. Wearing the abrasive unevenly is a challenge that good technique just about overcomes.
The LN No. 7 was pretty well spot-on, needing a very short dressing, but the Quangsheng showed a good three quarter thou hollow that I told Jon not to spend more than half an hour working on.
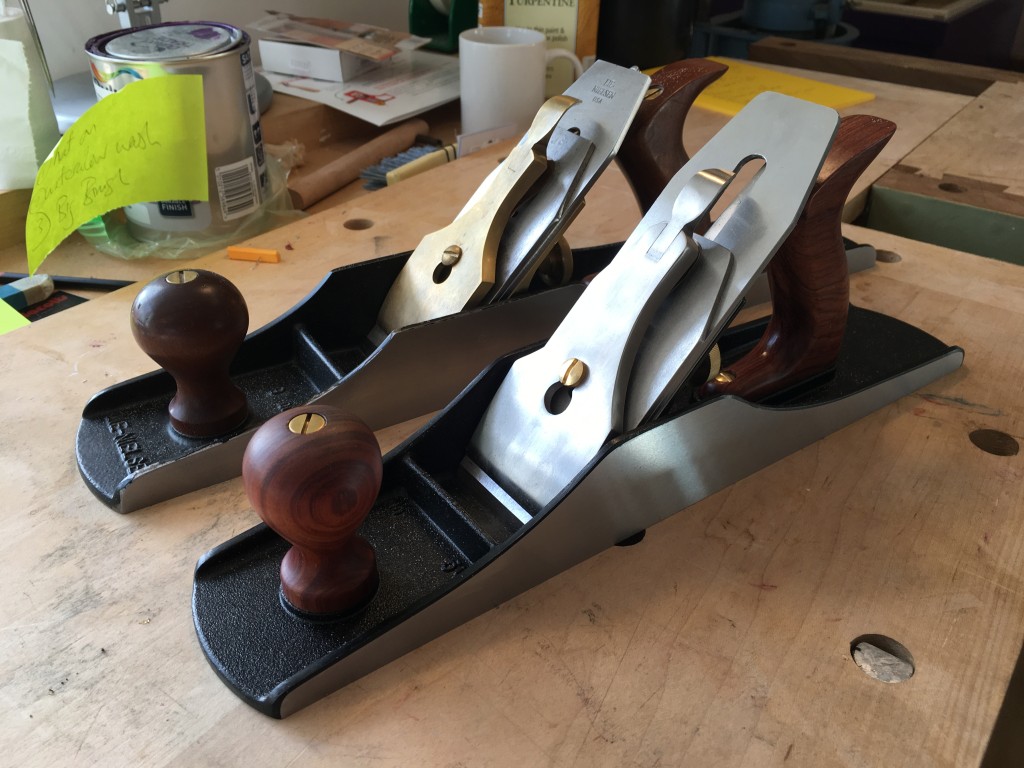
The LN No. 7 has a blade and back iron that does a great job. It’s A2 steel, which holds a decent edge for a long time. For stock removal and general work this is a good blade. For final shaving it’s is a little lacking in sharpness. But you would probably not use this plane for that purpose anyway.
The Quangsheng 5-1/2 is a potential finishing plane being small and fitted with a carbon steel O1 blade. I didn’t go and check this plane out as I have a walnut table in my studio being polished. But Jon set it up and got some pretty fine shavings.
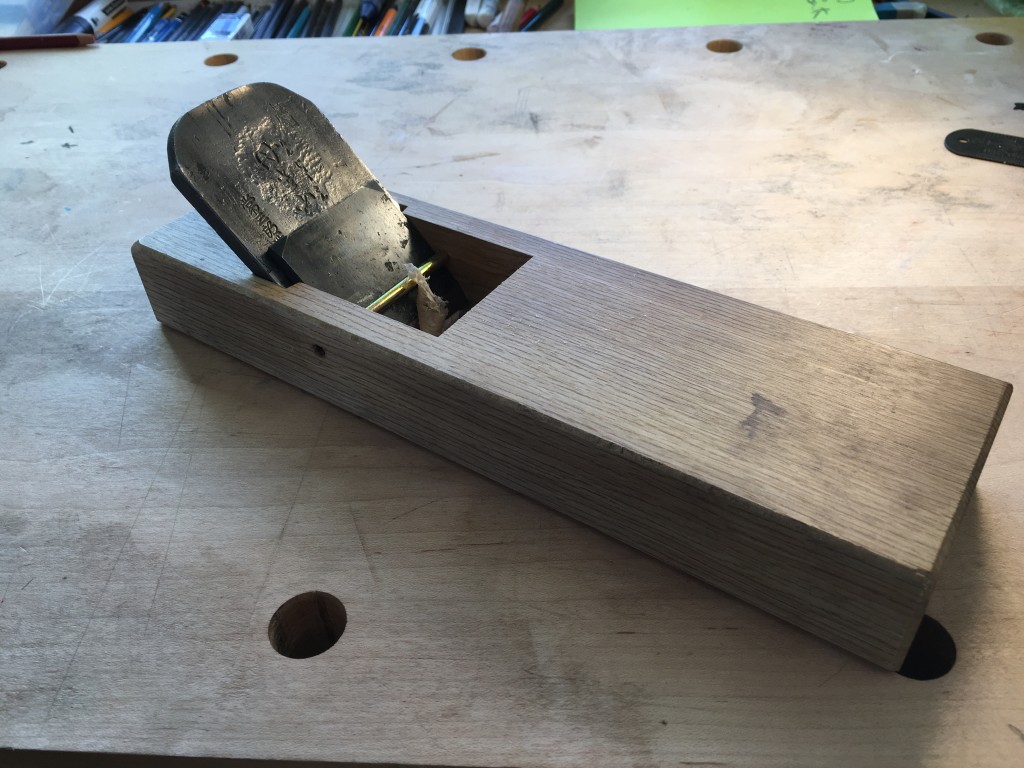
In winding this up, to complicate a simple problem. I offer an image of my current bench plane. Chisel in block of wood, but it’s the most sophisticated version of a simple concept. I would not suggest this for the beginner. It’s like driving a Ferrari, you have to be good enough or it will kill you. But I offer it as an idea to those of you who are older and wiser and needing to conserve energy. These light, incredibly sharp tools can be very effective in the right hands. In Summer School I glued up my chest half day after my fastest students, but was able to catch up, by the afternoon, even allowing for glue to set up, as my planes were that much better at final finish.
Thank you Tom, thank you Matthew. Both planes are going in the tool chest for our young furniture maker.
Hurrah, that’s a tricky one done….
— David Savage, finefurnituremaker.com
Like this:
Like Loading...