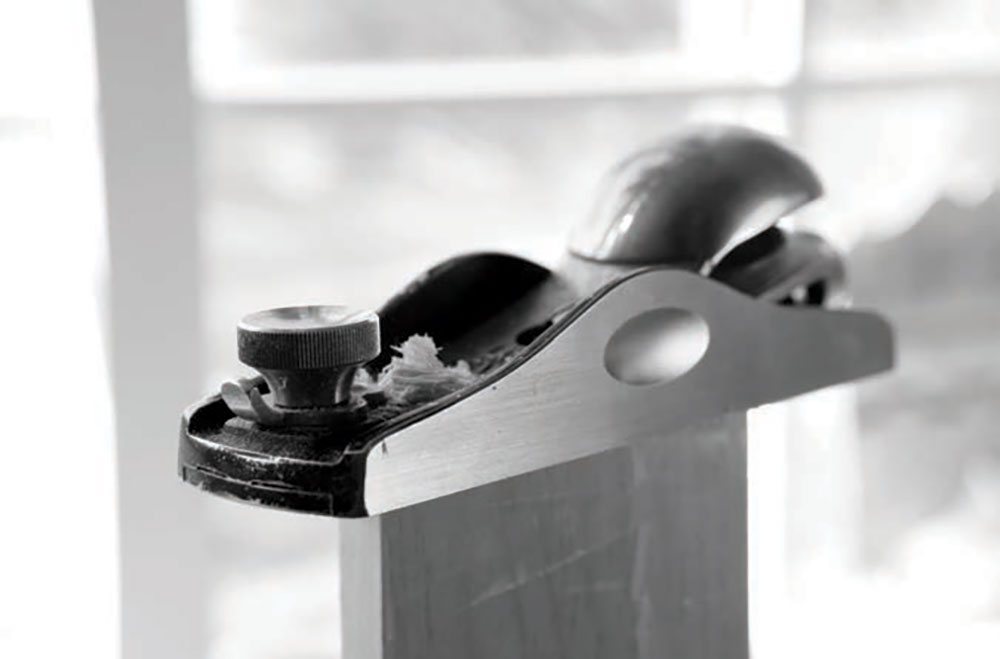
This is an excerpt from “The Anarchist’s Tool Chest” by Christopher Schwarz.
You can build furniture without a block plane. But why should you? The block plane is one of the greatest hand-tool inventions of the Industrial Revolution, in my opinion. With a block plane and a little skill you can accomplish almost any task. These tools trim end grain, face grain and whatever else you ask of them – and they do it even if the iron is a mite dull (thanks to their lower pitch). They are the most flexible plane ever manufactured. You can change the pitch of the tool with great ease and close or open the mouth with no special tools. And they are simple to set up.
Woodworking purists scoff at the tool, but I think that this is only because it doesn’t fit into their narrow tool list. If block planes had been invented in the 18th century, you can dang well bet that every re-enactor would be spouting off about how the block plane was the savior of the age.
In fact, I have to say that the block plane is one of my favorite planes because it was the first hand tool I ever used with great success.
When making my very first piece of handmade furniture, a sitting bench, I realized that I needed a way to trim the bench’s front and back pieces to the seat of the bench. I didn’t have an electric sander – much to my chagrin – so I decided to go to Walmart and buy a block plane. I don’t know where I got this idea; probably from my grandfather.
They had one block plane. It was a “Popular Mechanics” brand and was cheap and blue. I bought it, took it home and put it to work. It was not sharp. I did not sharpen it. It cut the pine surprisingly well. I can remember being amazed at the curly shavings that emerged from the mouth. I knew at that moment how powerful hand tools could be, even if wielded by a moron.
If you look at the history of block planes, you should be prepared for some enormous diversity and confusion. It seems that toolmakers made more kinds of block planes than any other kind of tool. I’m going to try to boil down the major features here for you, but be aware that I cannot cover every kind of block plane ever made.
Low Angle or Standard?
Block planes come in two flavors: low-angle or standard-angle. Low-angle tools have the iron bedded on a ramp that is 12° off of the sole. Standard planes have a 20° bed. Low-angle planes make it easier to achieve lower planing angles, which are nice for end grain. Standard-angle planes make it easier to achieve higher planing angles, which are nice for reducing tear-out.
The reason I always use a low-angle block plane is two-fold.
- The lower angle makes for a more compact tool that fits better in my hand. Your mileage may vary here.
-
With the low-angle plane you have a wider variety of planing angles available to you. You can achieve angles as low as 37°. Standard-angle planes can only go as low as 45°, if you want the edge to last more than a few strokes. Both planes can achieve high-planing angles. So the low-angle tools are more versatile.
So I see no reason to even own a standard-angle block plane. And I don’t.
Adjustable Mouth or Not?
Low-rent block planes generally have a fixed mouth, though there are some nice small block planes with fixed mouths. I prefer an adjustable mouth. Why? When I am using a block plane to true end grain, I don’t want the leading corner of the work diving into the mouth aperture. When I work in tricky grain, I will use every weapon available to me to attempt to reduce tearing – including an adjustable mouth.
And when I need to hog off material, I simply open the mouth as wide as it will go. Easy. If you have only one block plane, I recommend a low-angle tool with an adjustable mouth.
Lateral Adjustment or Not?
All block planes have lateral adjustment – you can tap the blade left or right to tweak the position of the cutting edge in the mouth. The question here is whether you need a lateral-adjustment mechanism, which can be as simple as a plate that shifts left or right to move the blade left or right, all the way up to a Norris-style adjuster that will control both the depth of cut and the lateral adjustment.
I find that all lateral-adjustment mechanisms that are supplied on a plane generally offer only coarse adjustments. The fine adjustments come from tapping the plane’s iron with a hammer. So to me, it doesn’t really matter if the plane offers some sort of formal lateral-adjustment mechanism. That’s because of the way I adjust a block plane:
• Sight down the sole and extend the iron until it appears as a black line against the shiny sole.
• Use your fingers to shift the iron left or right until the black line protrudes consistently from the mouth.
• Retract the iron to take up the screw-feed mechanism’s backlash. Then extend the iron a bit and use a small hammer to tap the iron left or right into its final position.
So do what you want to here. You don’t have to have a lateral-adjust mechanism. But it won’t hurt your efforts either.
— MB