
You may have read a few weeks ago about what happens when Chris gets bored with watching me teach. And what happens a day later when people share “advice” after said experiments. As far as I know, the bugs have not yet eaten what is now Roy Underhill’s Dutch tool chest. (And frankly, I’m a little offended that some of y’all think my dovetail joints aren’t tight enough to keep the bugs out….)
I didn’t bring the chest home, but we did bring home the test joint Chris made with Gummy Bear Glue. On Tuesday, I tried reversing the gummy glue using the same strategies one uses to reverse hide glue; both are gelatin, after all.
But first, I hit the snot out of it…again. We first tried to reverse the joint using nothing but force (a big hammer) the day after Chris glued the two pieces together. It didn’t work then, either. But you see can above that this time, the lump hammer produced the start of a split. Under extreme force, the wood is failing before the gummy glue. Just as it does with hide glue, PVA and other wood-appropriate mastics after they’ve fully cured.
I cut the test joint into three pieces before testing the gummy glue reversal with hot water, alcohol and a chisel.
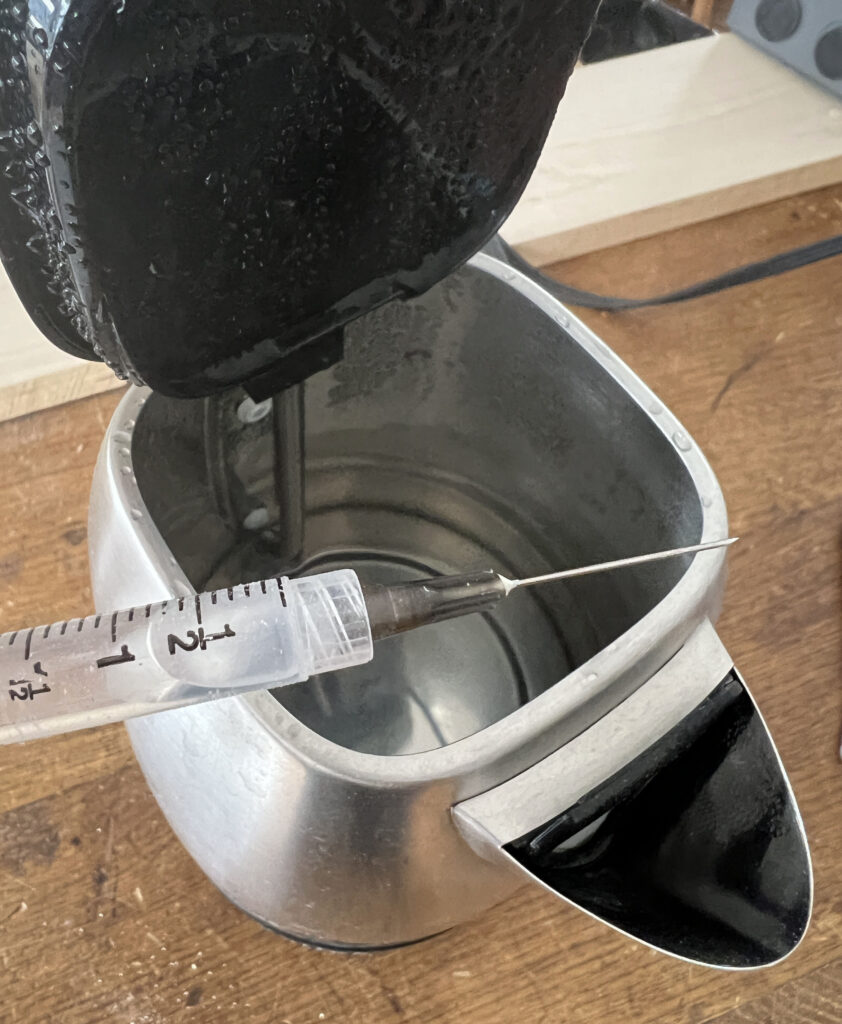
I boiled water, then as quickly as possible sucked it into a syringe with an 18-gauge needle and inserted hot water into the joint on all sides. After letting it sit for a few minutes, I was able to pop the joint apart with a sharp hammer blow. Just as I’ve done numerous times to hide glue joints treated with hot water.

As you can see, it’s an almost dead-clear reversal – no wood failure in the joint (that teensy bit of failure visible at the top of the above picture is where the split was starting from the untreated hammer blow).
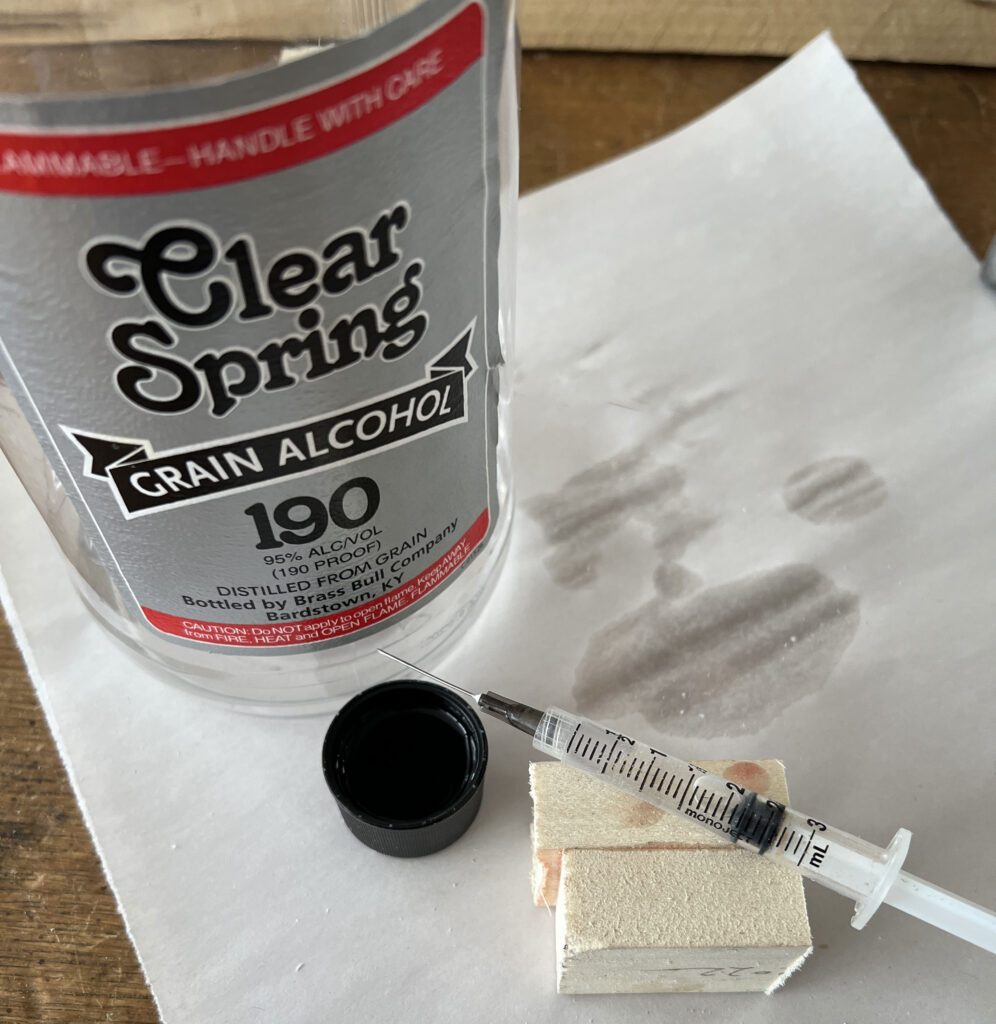
Next I tried inserting 190-proof grain alcohol into the joint. This crystalizes hide glue – and it did the same here. I waited two minutes or so before smacking the joint, and you can see below that the split isn’t quite as clear as with the water, with a few thin areas of wood failure visible (again, the obvious failure at the edge is the result of before-treatment beating).
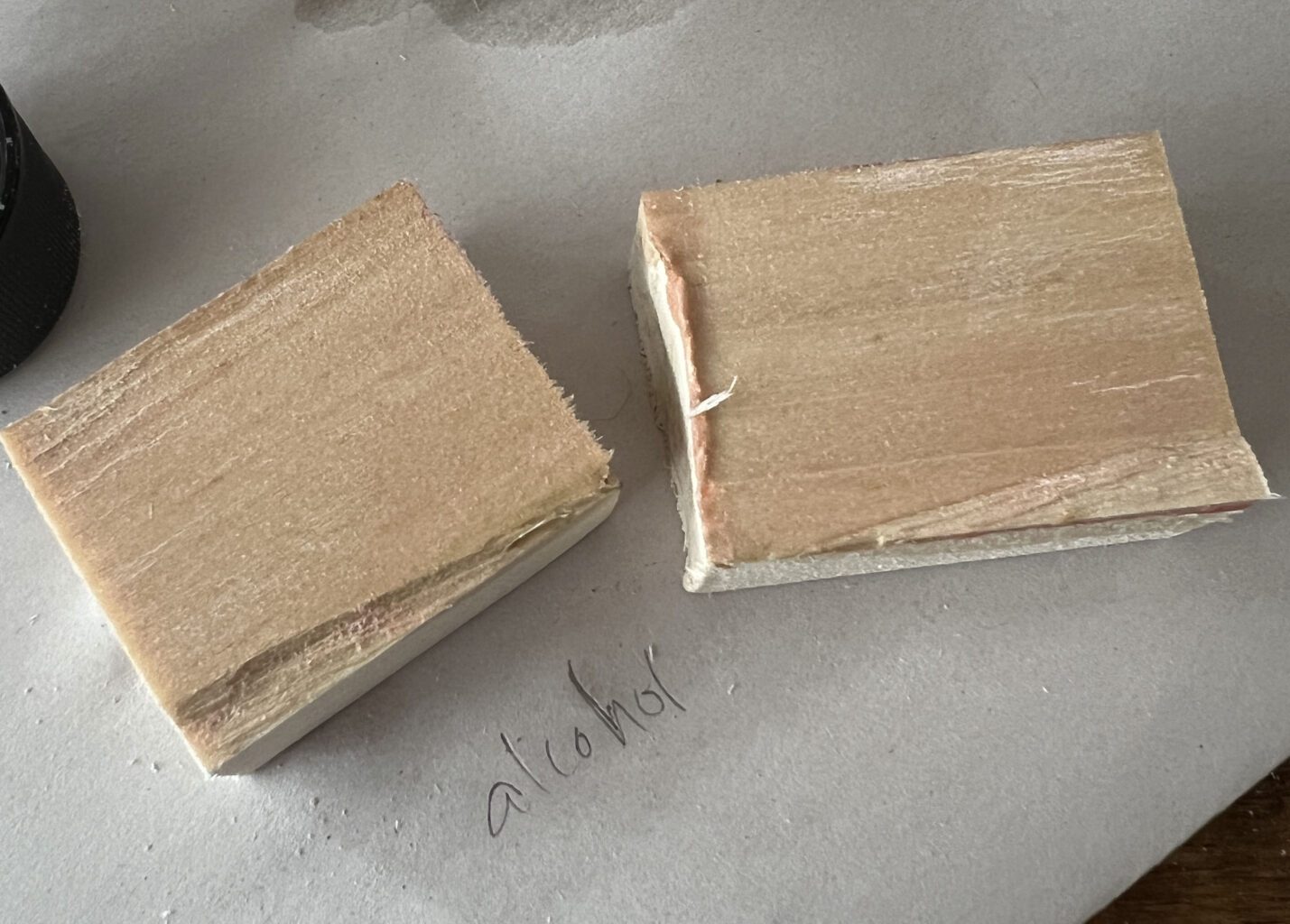
Then, I used a wide chisel to try to cleanly split the joint without water or alcohol. Same as with any wood glue, there is obvious wood failure – if not as much as I’ve seen with traditional hide glue.
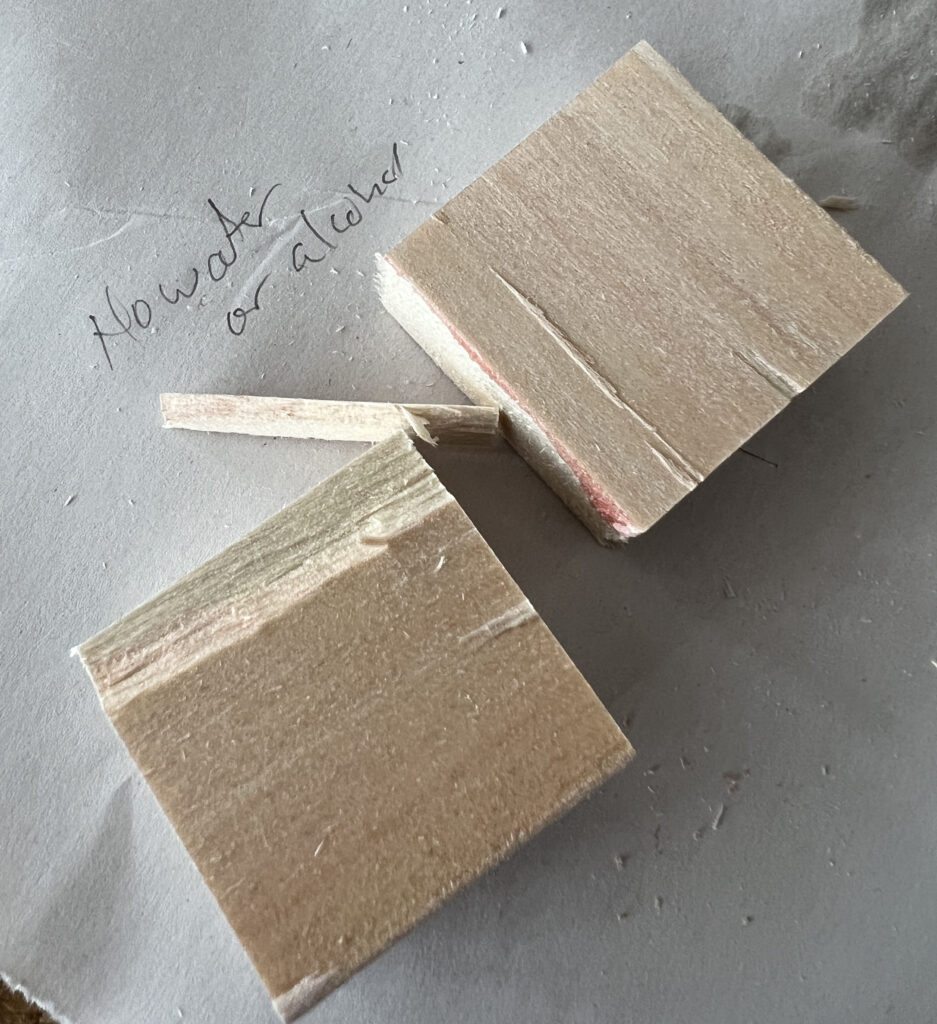
Is two weeks enough set-up time – and in winter, where it’s too cold for the bugs – for a proper test of the gummy glue? Maybe not. But clearly, it has some holding power. Regardless, I am 100-percent certain that Roy’s Dutch tool chest will not fall apart; have you seen the number of nails I use on those things?*
– Fitz
* Maybe you haven’t…but soon, very soon, you’ll be able to refer to a book on the subject. Just trying to head that question off at the pass…