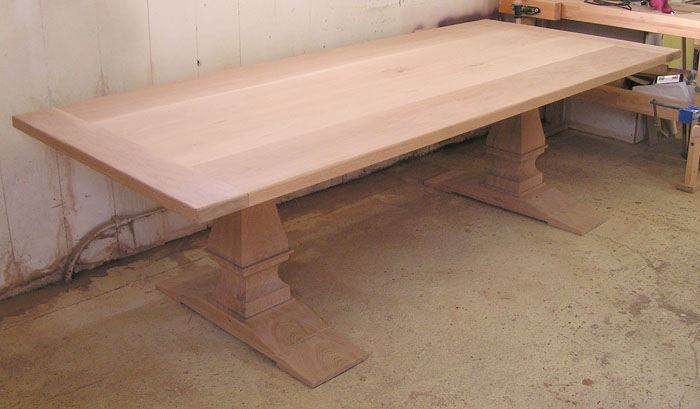
Editor’s Note: This is the second in a series of blog posts by Richard Jones, who has written a detailed book about timber technology. The book is scheduled to be released in early 2018.
— Kara Gebhart Uhl
I didn’t set out to write a book on timber technology. Doing so was an accident of circumstances. In 2003, I closed my furniture business in Texas, moved home to the UK and started teaching furniture undergraduates at Rycotewood, which I mentioned here. I was given the task of introducing the students to the craft furniture maker’s primary material of wood in the Timber Technology module. I possessed a relatively good expertise in the subject but I’d never prepared and delivered learning materials on it. It was a challenging sink-or-swim moment for me – well, more of an ongoing fight against drowning throughout a 12-week term. But it got easier with practice and as the years passed.
In 2005, I started creating illustrated Timber Tech PowerPoint presentations as learning tools. From that, I converted the PowerPoints into articles to sell to woodworking magazines, a sideline of mine. At some stage in this article production I decided the topic was too involved to be covered adequately in a series of articles in several magazine issues. So, being a bit bloody minded, I decided to create a manuscript covering the key issues relevant and of interest to me as a woodworker. Further, I decided to write it in such a way that non-specialists could understand some of the more challenging elements, and my students were the model non-specialists. Of course, this meant I was writing speculatively, without having a publisher on board – but more on that in a later post.
Most books on timber technology are written by timber technologists for wood scientist colleagues, or students of the topic. They’re consequently a difficult read for the general reader, something probably true of most woodworkers, myself included. Wood science authors assume a certain background knowledge in their expected readership. And why not? They’re generally singing to the choir, or at least aspirant wood scientists. It doesn’t really help the non-scientific woodworker who wants a better understanding of their material as simply as possible. In creating my manuscript I took pains to try and make some difficult science accessible and useful to all woodworkers – carpenters, joiners, furniture makers and so on.
An oak tabletop, such as the one shown above, 1100 mm (~43-1/4″) wide with end clamps (aka breadboard ends) needs allowance for expansion and contraction on the main panel across the grain. A tongue and groove, incorporating three tenons worked in the main panel fit motices in the clamps. The central tenon is glued, and the two end tenons are free to move side to side in extended mortices, but held tight in the main panel with dowels passing through slots in the tenons.
– Richard Jones