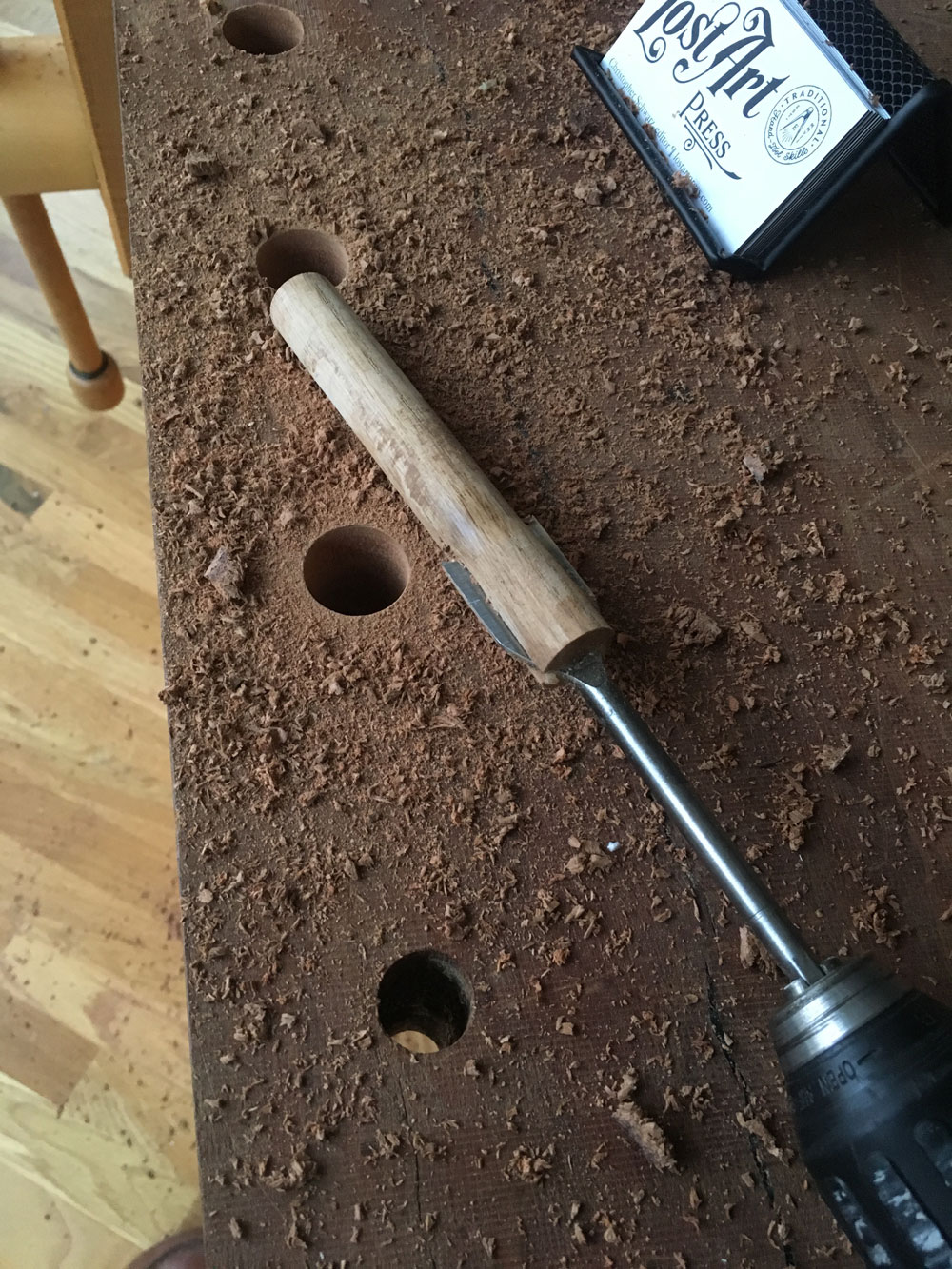
During the last 20 years, most woodworkers have adopted 3/4″ as the standard size for holdfasts, bench dogs and other workbench accessories. So why the heck are we making holdfasts at Crucible Tool that have a 1″ shaft?
Simply put: The larger holdfast has more mass, it doesn’t ream out your bench’s holes as fast and we think it just works better.
During the last couple weeks, I’ve written a series of blog entries on the Crucible Tool website that explain our reasoning. Despite this, we continue to get a lot of questions, and so I’ve consolidated all the answers here.
(Side note: We are working on offering a way for you to subscribe to the Crucible Tool blog so you can get updates via email. In the meantime, if you use an RSS reader, you can subscribe to it via this feedburner link: http://feeds.feedburner.com/Crucibletool-CrucibleNews.)
Q: Why did you choose 1″ instead of 3/4″?
A: We do have a good answer. Really. It’s here.
Q: OK, so if I do switch over to 1”, how do I enlarge the 3/4″ holes on my bench?
A: There are many ways to do it. Here is a quick and inexpensive way.
Q: Hmmm. So I use my dog holes for holdfasts sometimes. So I would need to switch to 1″ dogs. That sounds expensive.
A: It’s really not. Here’s how to make an entire set of 1″ dogs for about $11. Wooden dogs are gentler on your tools.
Q: I’m building a new workbench, where should I locate my holdfast holes?
A: We have a map of what we prefer here.
Q: So why does your holdfast fit so tightly in the hole? Other brands just drop in?
A: There is a very good reason for that. Here’s why. And here’s some more.
Q: How do you make your holdfasts? And where?
A: They are ductile iron and made at the Erhart Foundry. You can read all about it here.
— Christopher Schwarz
Like this:
Like Loading...