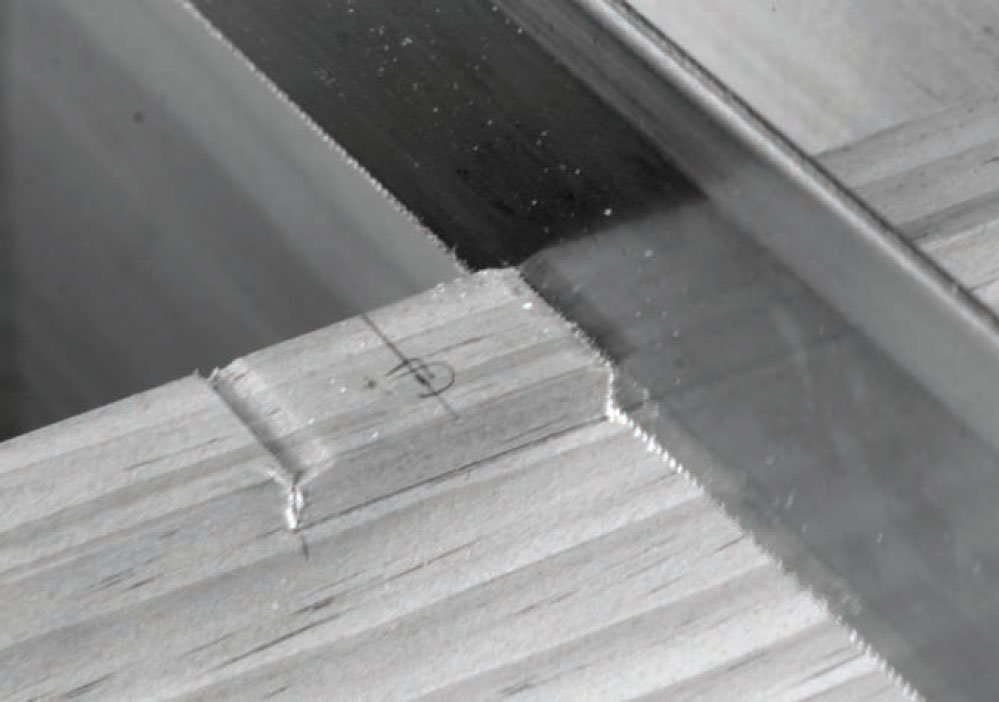
This is an excerpt from “The Joiner and Cabinet-Maker” By Anonymous, Christopher Schwarz and Joel Moskowitz.
Good luck finding steel hinges for this project that have the right look and bend in the right place to fit in the partition. I was unsuccessful in finding some off-the-rack hinges to make this part easy. But altering your hinges to fit is easy work – the barrier for most woodworkers is that hinges are made of metal and that can sap your confidence.
Don’t let it. There are lots of cool steel strap hinges out there that are sold with straight-as-an-arrow leaves. Bending them is simple work with just a metal-jawed vise and a hammer. If you still have some trepidation, purchase an extra hinge to practice on.
These hinges are placed using the same rules for placing the crossstrengtheners on the Packing Box. First calculate the overall length of the box. Position the hinges so their centerlines are half this distance apart.

The hinges are recessed into the top edge and face of the back of the Schoolbox. First, cut away the notch on the top edge of the box for the hinges. Install the unbent hinges into the mortise using the screw hole that is nearest to the hinge pin. Then mark where you want to bend the leaf. Mark your bending line underneath the hinge, right up against the back of the box. Remember: It’s not like folding paper. You need to allow for the thickness of the leaf when bending.
Secure the leaf in a metal-jawed vise so that the leaf you want to bend sticks up from the vise. Clamp the jaws right below the line you marked. Use a hammer to tap the leaf to shape. You want to bend the leaf so that the leaf needs to be recessed into the back.

Hold the hinge in its mortise again. Then trace around the hinge to mortise the hinge flush to the inside of the case (this will allow the partition to be removed). Waste away the area where the leaf should go.
Screw the hinges to the carcase of the Schoolbox and get ready to attach the lid. The lid should be slightly oversized because things might shift around during installation. Plus you never know how the slop in the hinge barrels will affect how the top fits.
Set the Schoolbox on its back and elevate it on some spacers. Position the lid on the benchtop and let the hinges fall onto the lid. Drive one screw into each hinge and see how things work.
Once the lid is positioned where you want it, let the lid fall onto the workbench and drive the remainder of the screws. Now you can trim the lid so there’s about 1/16″ of overhang all around. That should be enough for most environments. If you live in an area with wild humidity swings, give yourself 1/8″ of overhang on the front.
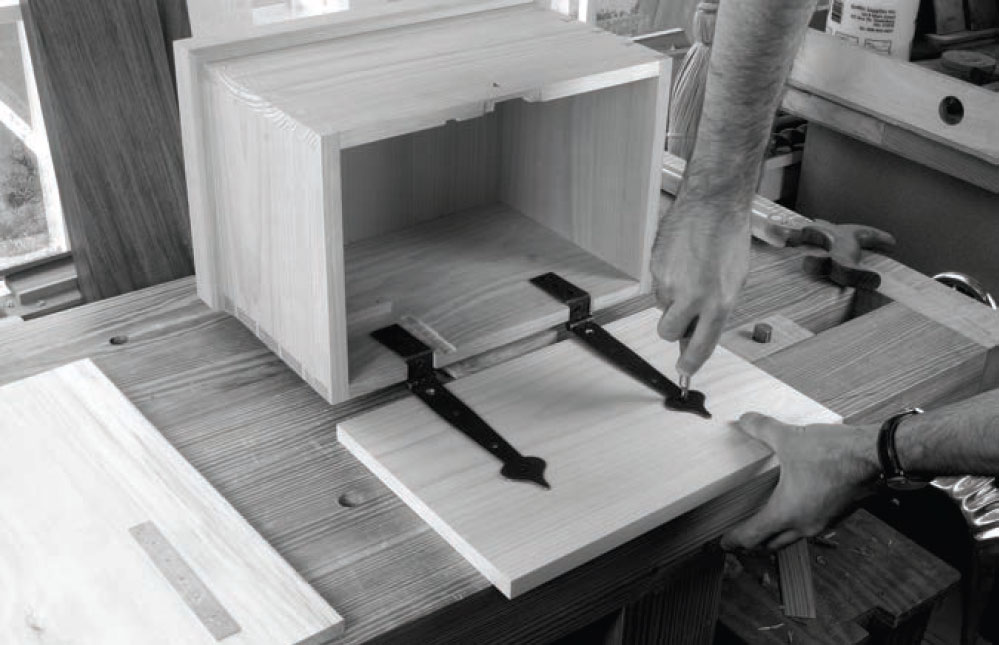
Now you can fix the lock’s hasp into the lid. This is a Friday job (meaning it’s easy). Lock the hasp onto the lockset. Then drop the lid onto the hasp. The hasp has two nibs on it. Strike the lid right where the hasp is. This dents the lid right where these two nibs are.
Unlock the hasp, nestle it into the nibs and trace around the hasp. By this point you should know the drill: Score the waste with a chisel. Remove it with a router plane or a chisel. Then screw the hasp to the underside of the lid.
As far as woodworking goes, you’re almost done. All that is left is to install the moulding around the lid. This moulding receives a chamfer or a bevel that is identical to the one you planed onto the skirt moulding.
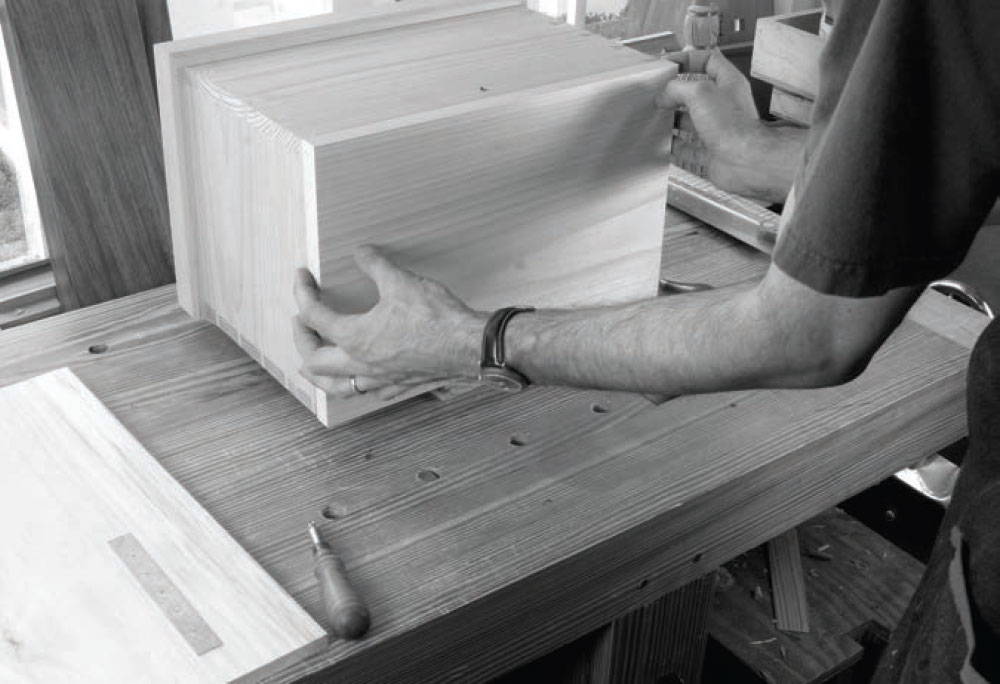
You also can cut the moulding and miter it just like you did the skirt moulding. However, there is one small difference when installing the lid moulding. You have some cross-grain problems that you didn’t have with the skirt moulding. The lid’s return moulding has its grain running at 90° to the grain of the lid.
Here’s how you deal with it: Glue and nail the front piece of moulding just like you did on the front piece of skirt moulding. When you install the returns, glue the miters in the same way you glued the miters for the skirt moulding. But when you glue the back of the lid moulding to the lid, glue only the first few inches up by the miter. Leave the rest of the moulding dry.
Nail the entire moulding, however. Nail through each miter and into the lid. The glue at the front will keep the miter tight. The nails at the unglued area at the back will allow the lid to move without things splitting or blowing apart. Well, that’s the plan at least. And it’s a good plan if you used Eastern white pine for this project. It moves little in service. If, however, you used flat-sawn red oak for your Schoolbox, then keep your fingers crossed.
— Meghan B.