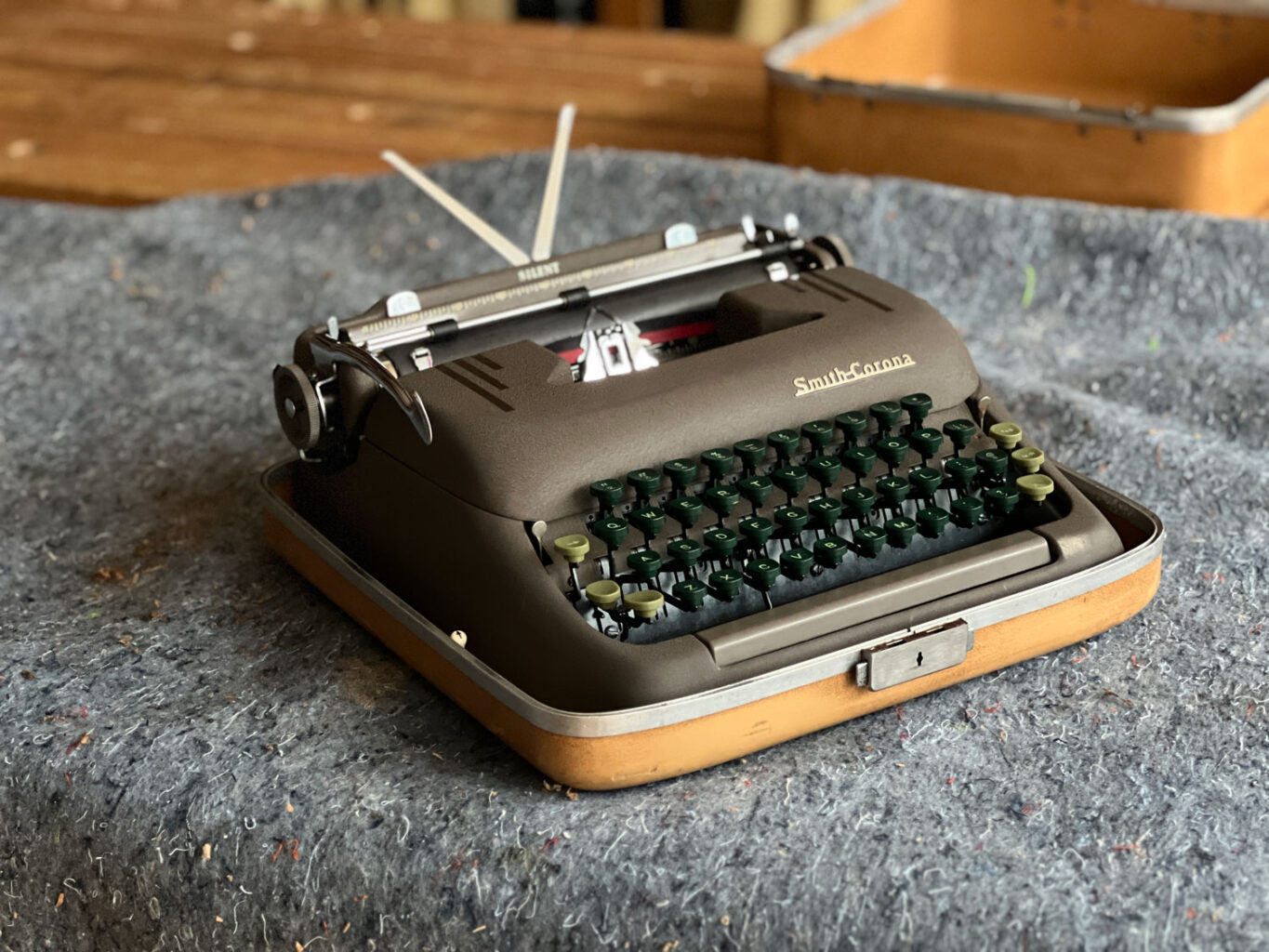
The first writing class I took at Northwestern’s journalism school – “B-01 Basic Writing” – was intended to weed out about one-third of the students. You had to make a “B” in the course or you were thrown out.
The class was intentionally boot camp-ish. And there were a variety of infractions that would result in an “F” on your day’s work, such as misspelling a proper noun. (I will never misspell “Nicaragua” again.)
Perhaps the most dastardly detail of the class was that you were required to type everything on manual typewriters in the writing lab. It was Spring 1987 when I took that class. And electric (even Selectric) typewriters were common, and dedicated word processors were in the writing labs for the advanced students.
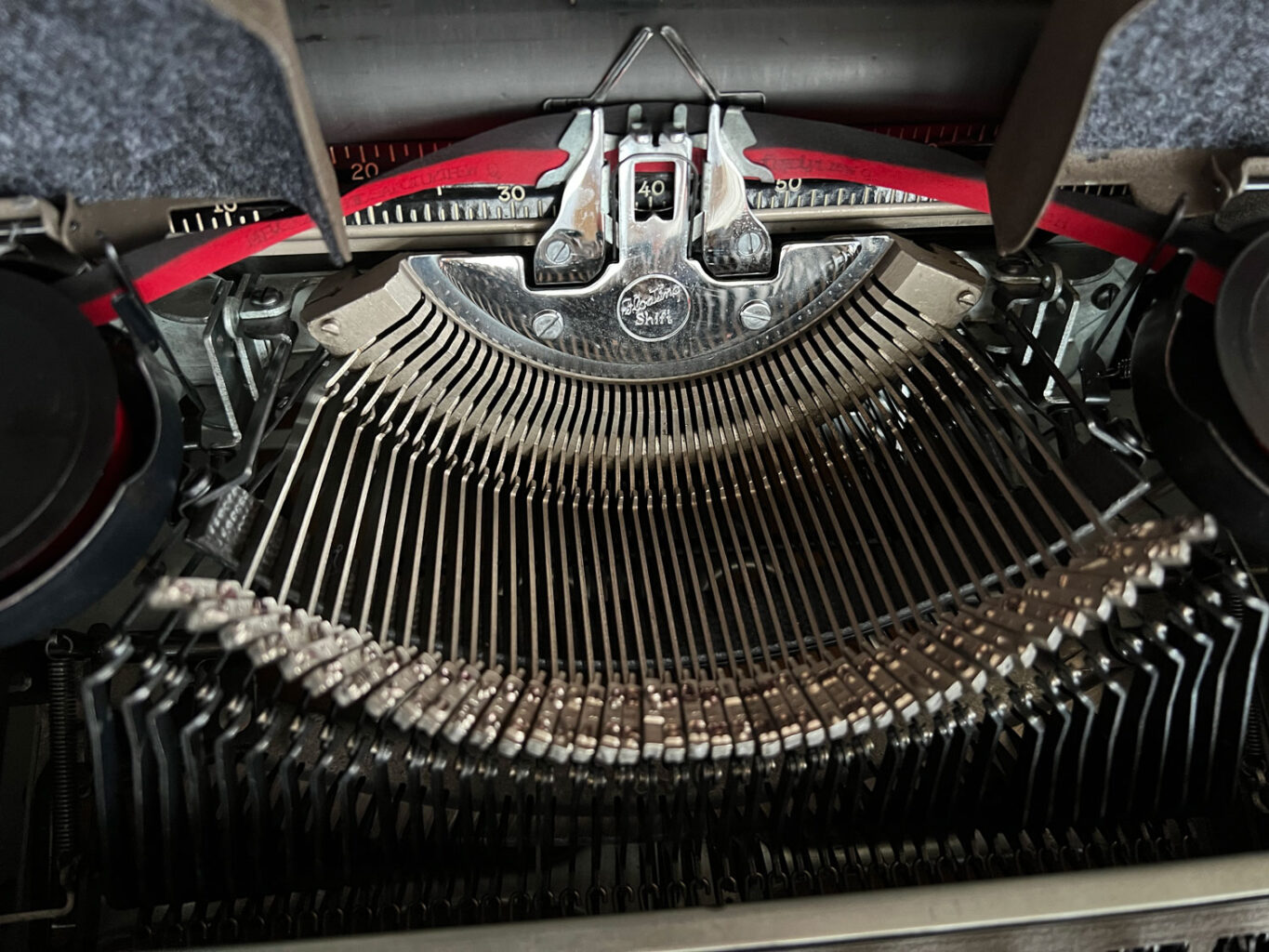
A lot of my fellow students were freaked about the manuals. Plus how to use correcting fluid. And moans such as, “Where is the ‘1’ key? My machine is missing that key!”
Working on a manual was the only advantage I had in the class. For the first 20 years of my life, everything I wrote was on my manual typewriter, which had been handed down to me by my mother. I knew the machine inside and out. I had to repair the thing, oil the thing. Clean it to keep it working, especially the platen. And change the ribbon, of course.
I didn’t like electric typewriters. They made a hum like a bug zapper, and every time I brushed a key accidentally I’d jump in my seat. I needed a typewriter that required effort to use. And was quiet.
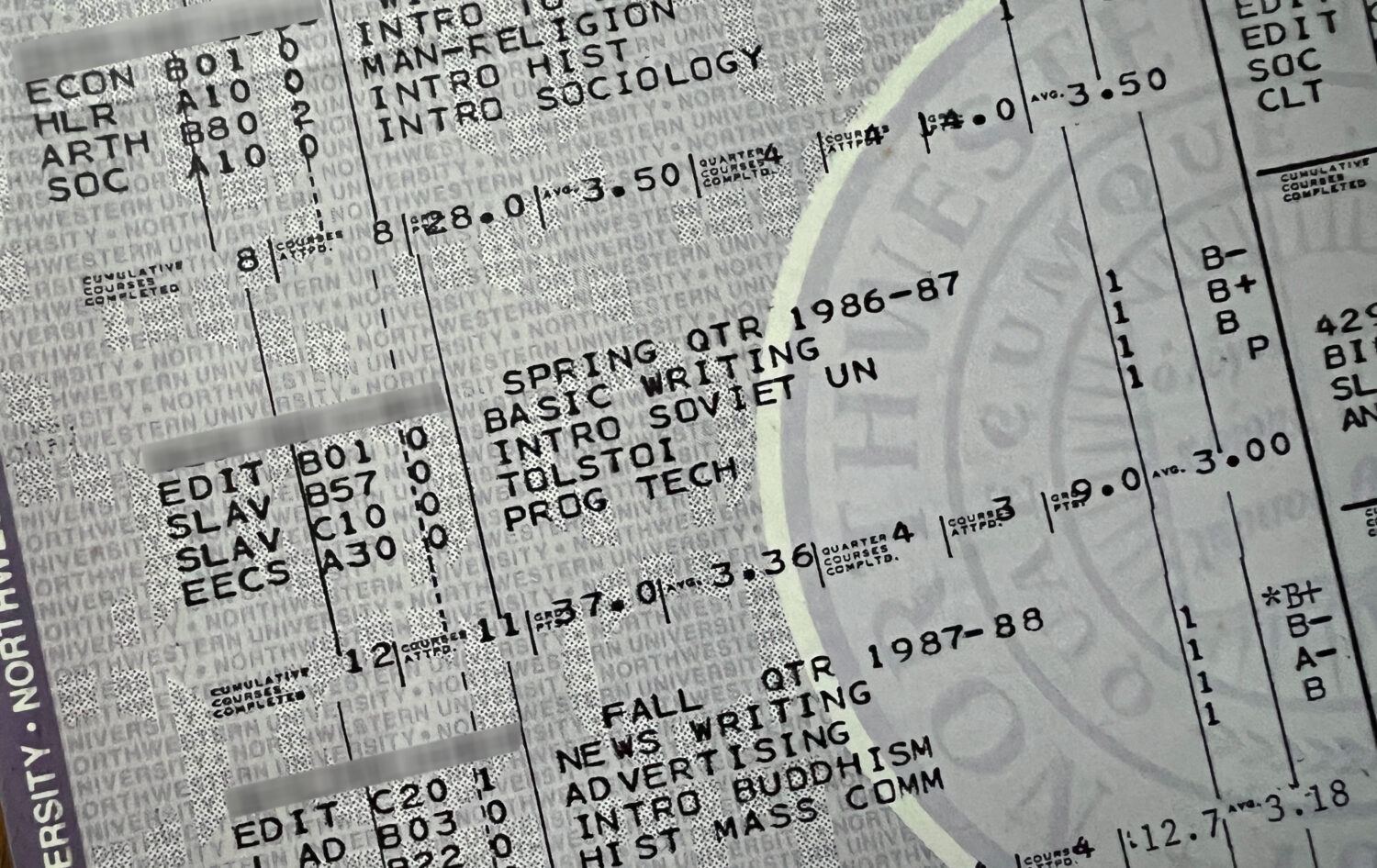
I barely passed Basic Writing with a B-, the absolute lowest grade that allowed me to continue in school. And I often attribute my love of manuals to be the reason I didn’t get a C or worse.
This week I took delivery of an amazing piece of work that has brought a lot of emotions to the fore. It’s a completely restored 1949 Smith-Corona Silent. A beautiful and compact piece of insane engineering.
The machine was completely rebuilt by Meagan Syata of the Unplug Typewriter Co. I have been following her work on Instagram for a while. And at some point our paths crossed. Her husband is a woodworker, and they live in Hope, Arkansas, my home state. We worked out a trade (I think I got the best part of the deal) – one typewriter in exchange for a huge pile of books.
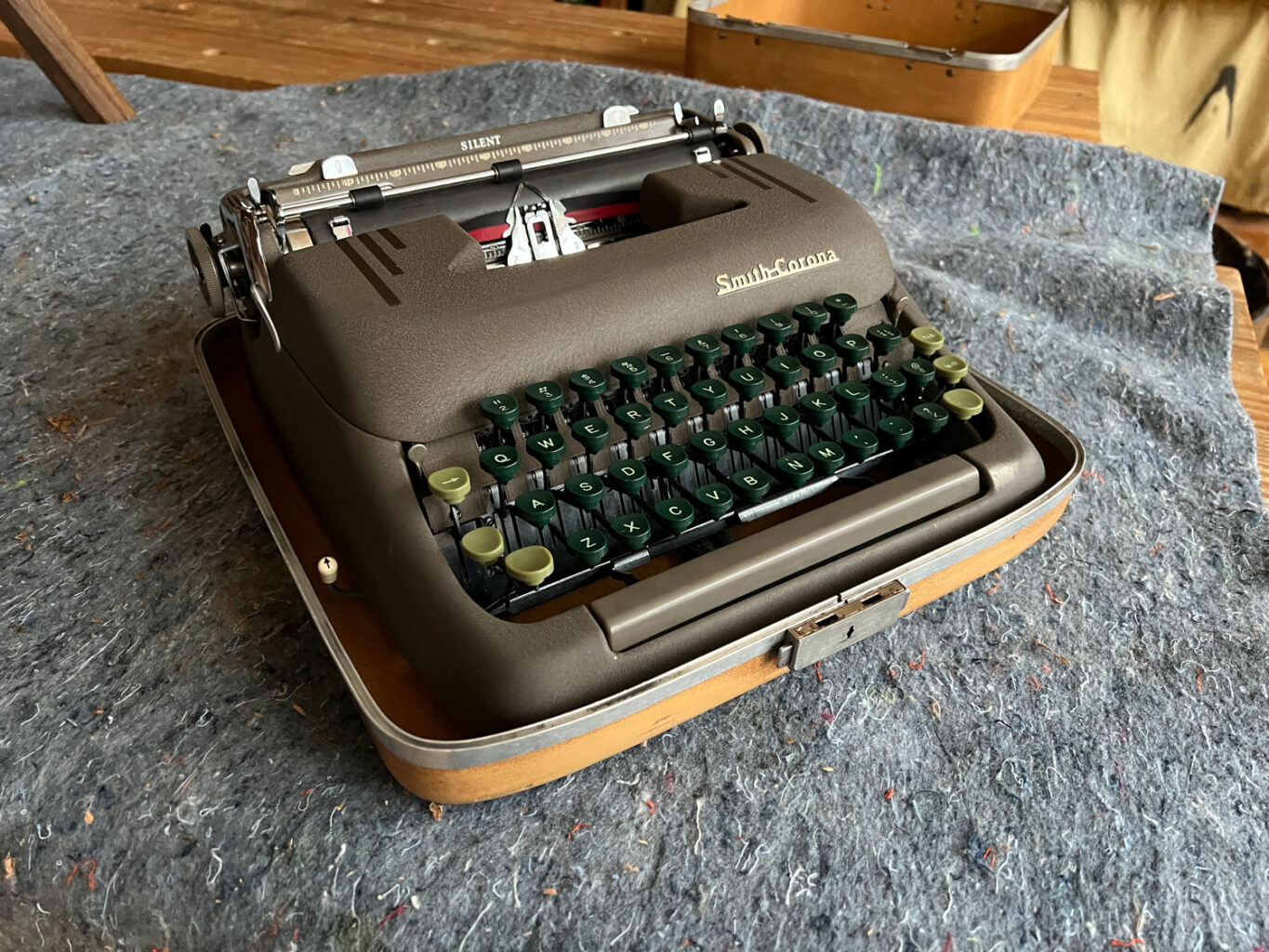
The typewriter showed up yesterday, and I cannot take my eyes or hands off of it. It looks and works like it is new from the factory. And after reading about and watching everything that Meagan does to these machines, I am not surprised.
This typewriter is going to get used. I hate writing notes and short letters by hand. My handwriting is terrible. I’m a much better typist.
I doubt I’ll ever write a book using it. But who knows? I’ve done stupider things (such as our letterpress version of “Roman Workbenches.”)
To be honest, I don’t have romantic notions about using a manual typewriter. I don’t do detective cosplay, and I’m not a “His Girl Friday” reenactor. Like my handplanes and saws, this is a tool. And knowing how to use all the tools is part of my DNA.
As a writer with a long history with these machines, it’s nice to have one of these back in my possession.
If you have any interest at all in these old machines, do check out Meagan’s store. I am incredibly impressed. Plus, if you buy one, you might just save an old typewriter from getting cut up so its keys can be turned into jewelry.
— Christopher Schwarz
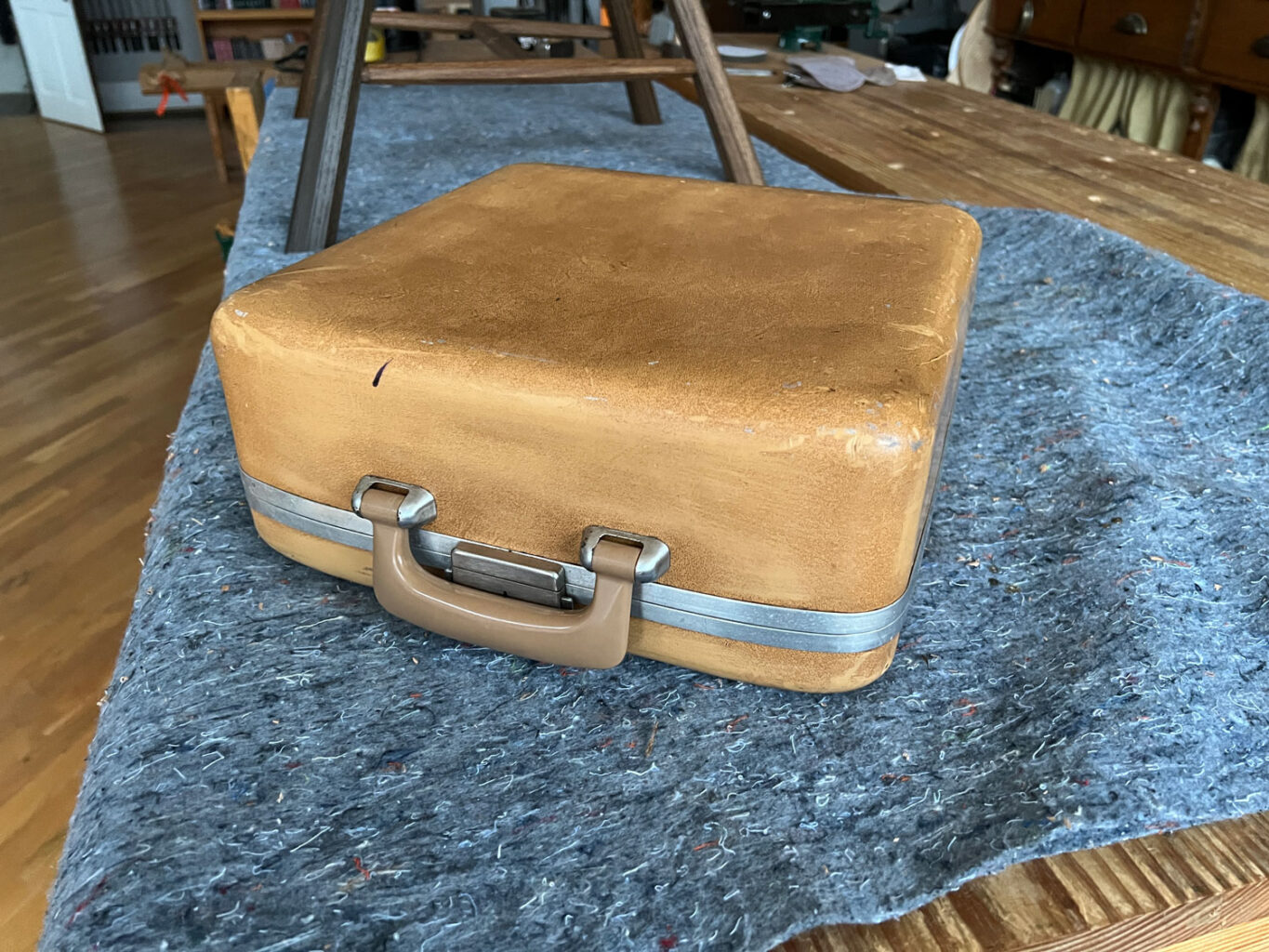