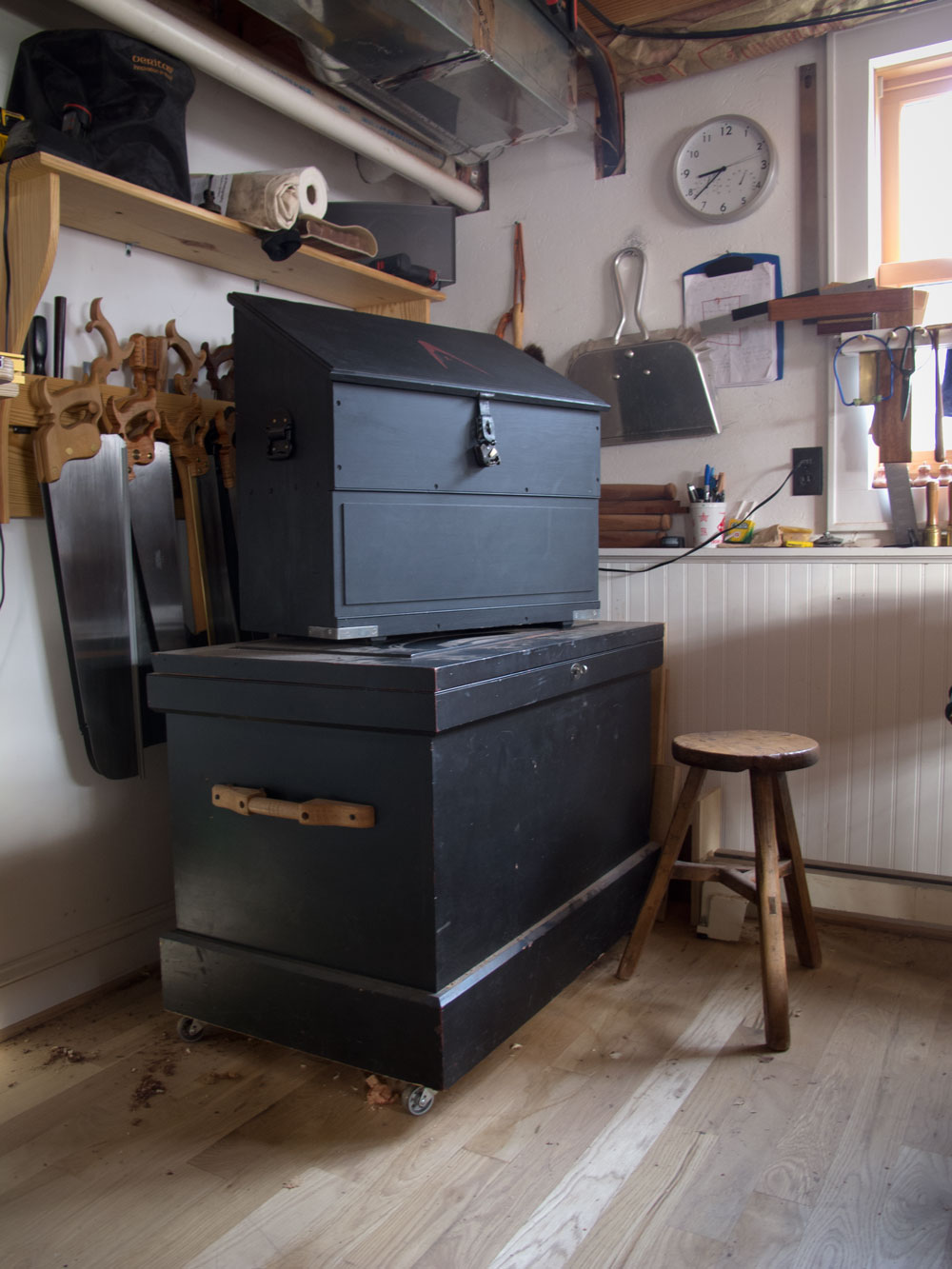
Question: What made you decide that you liked the Dutch tool chest design in favor of the one in “The Anarchist’s Tool Chest?”
Answer: I don’t prefer the Dutch chest.
This Q&A was repeated at least 20 times on Friday and Saturday during the Lie-Nielsen Hand Tool Event in Cincinnati, Ohio. I had brought the Dutch chest so people could examine it and get a feel for how it works. I’d also brought an English-style chest, which was filled with Lost Art Press books.
So here is a list of the advantages and disadvantages of each style of chest.
Portability: The Dutchman Wins
With an overall size of 27” wide x 13” deep x 26” high, the Dutch chest fits on the backseat of almost any vehicle and can be strapped in with a seat belt. I can easily lift and carry the chest myself. The full-size English chest is 40” wide x 24” deep x 26” high. It takes two people to move it, and you have to have a truck, utility vehicle or station wagon to transport it.
My smaller traveling English tool chest can be handled (barely) by one person and fits in many cars. But it is still not as easy to move as the Dutch.
Ease of Construction: Point, Dutchman
The Dutch chest takes me about 16 hours of shop time to build (including the paint). It has only two dovetailed corners. The rest of the joinery is dados, tongue-and-groove, glue and screws. It can be built with dimensional pine and requires only one panel glue-up (for the lid).
The English chest takes me about three times as long to build because there is so much more wood and everything is dovetailed and nailed. It’s a major project that requires a lot of wood and considerable time to complete.
Durability: One for the English
Though I haven’t tested either chest into the ground, past experience tells me that dovetails will last longer than screws. The English chest really is designed to last forever. The bottom bits are designed to be replaced when they rot out. The orientation of the joints on the skirts are designed to hold the chest together even if the glue fails.
The Dutch chest is solid enough, but it’s not designed to take the same level of punishment as the English chest. If the bottom rots out, I’ve got to rebuild the chest. If the screws rust and the glue fails, lots of things are going to come loose.
Looks: I Like the English
The Dutch chest isn’t ugly – several people at the Lie-Nielsen show said they preferred the looks of the Dutch chest. But to my eye, the English chest is beautiful. I like the shadow lines created by the skirts and raised-panel lid. I’ve experimented with adding more visual interest to the Dutch chest with some success, but it still looks like a grain bin to me.
Utility: Tie
While the English chest holds more, the Dutch chest holds enough and makes it easier to move your stuff around. Getting to all the tools in the Dutch chest is easy if you put the chest on a sawbench. You don’t have to prop up the English chest, and its lid is another working surface in the shop.
And so this morning I brought my Dutch chest into the shop and removed every tool. I wiped them down with a woobie and put them back into place in the English chest. I know some of you out there are going to say this is an onerous task task, but it’s not. Whenever I travel, I have to clean all the tools and put them back in order. (I allow all my students to use my personal tools, and so they get a lot of use.)
So the bottom line is that I’m glad I have the Dutch chest because I am on the road teaching for about 13 weeks out of the year. And the Dutch chest makes travel easy. But when I come home, I’m always happy to see my English chest with its open lid, waiting to get back to work.
— Christopher Schwarz
P.S. Megan Fitzpatrick, the editor of Popular Woodworking Magazine, says my story on Dutch tool chests should be in the October 2013 issue of the magazine. There are no promises in the magazine world, but that’s the word today.
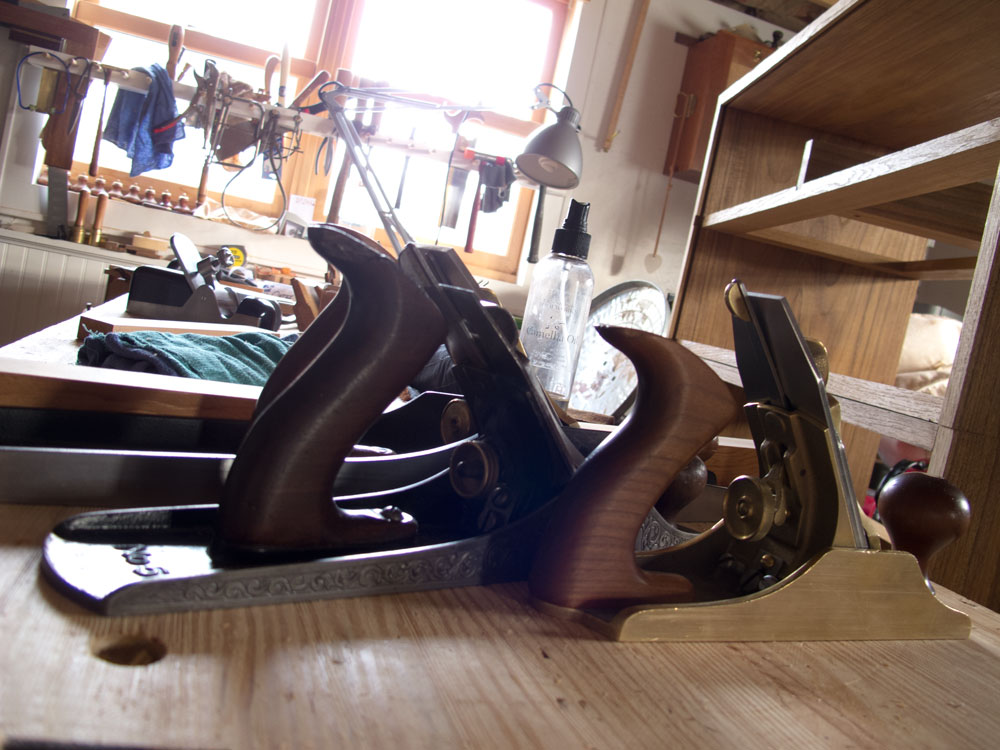
Like this:
Like Loading...