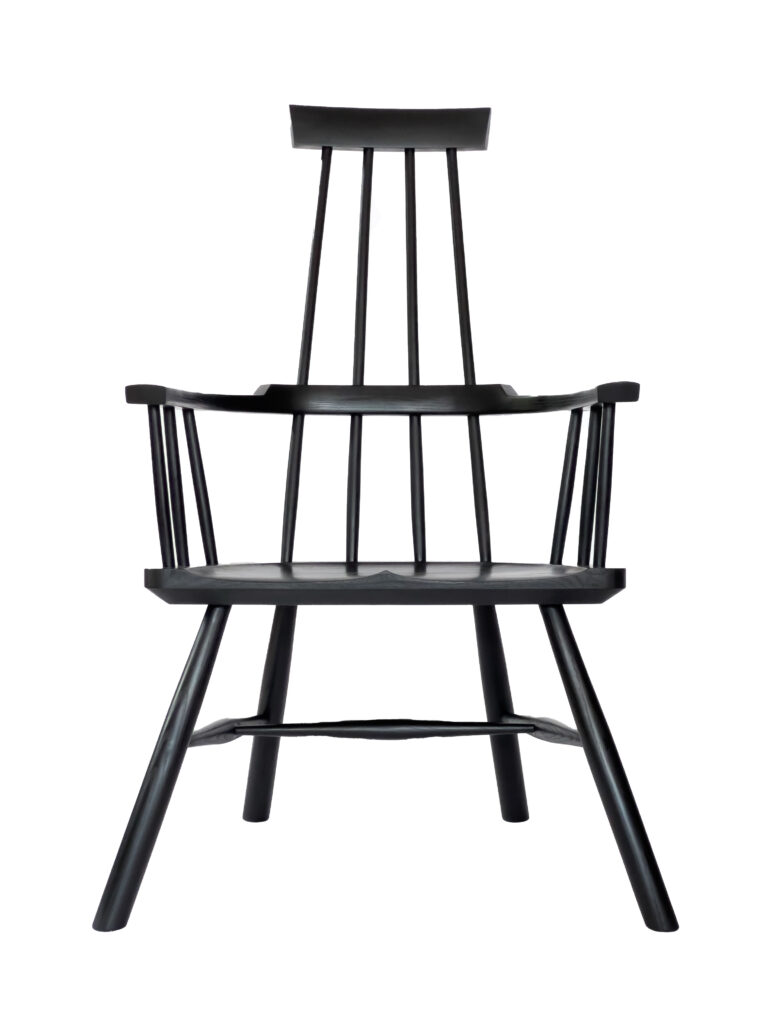
Welsh chairmaker Chris Williams is teaching classes in our storefront this month and has brought over one of his truly remarkable Welsh stick chairs, made from Welsh woods in the old tradition by a 100-percent Welshman.
Chris is, quite simply, the best stick chair maker alive. He’s the one we all look up to, and he’s always pushing the design of the chair forward in terms of design and backward in terms of using armbows made from curved branches – the traditional way that the best chairs were made.
In fact, I would put up his work against any fine furniture maker in terms of fit and surface finish. Chris absolutely tortures himself to get it right. And it shows in the results.
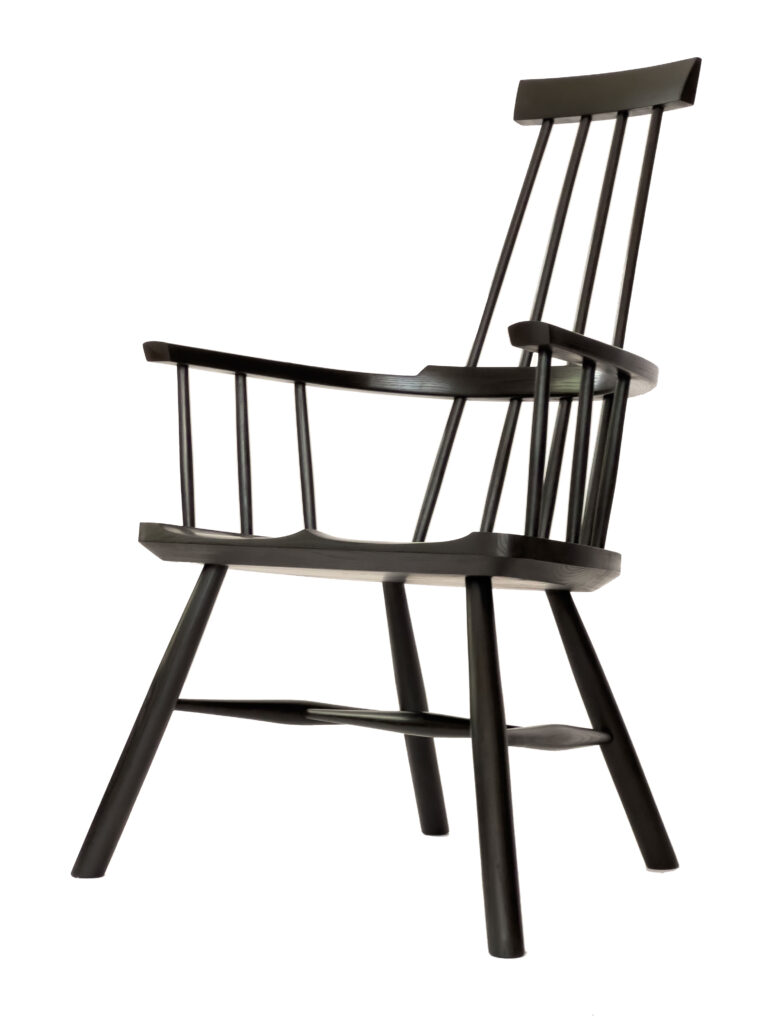
Chris, the author of “Good Work,” was shown how to make Welsh stick chairs by John Brown, and Chris worked with JB for many years, making these chairs.
Here’s a little about the chair from Chris:
Dimensions:
Overall height: 41”
Seat height: 17-1/2”
Seat depth: 16-1/2”
Seat width: 24”
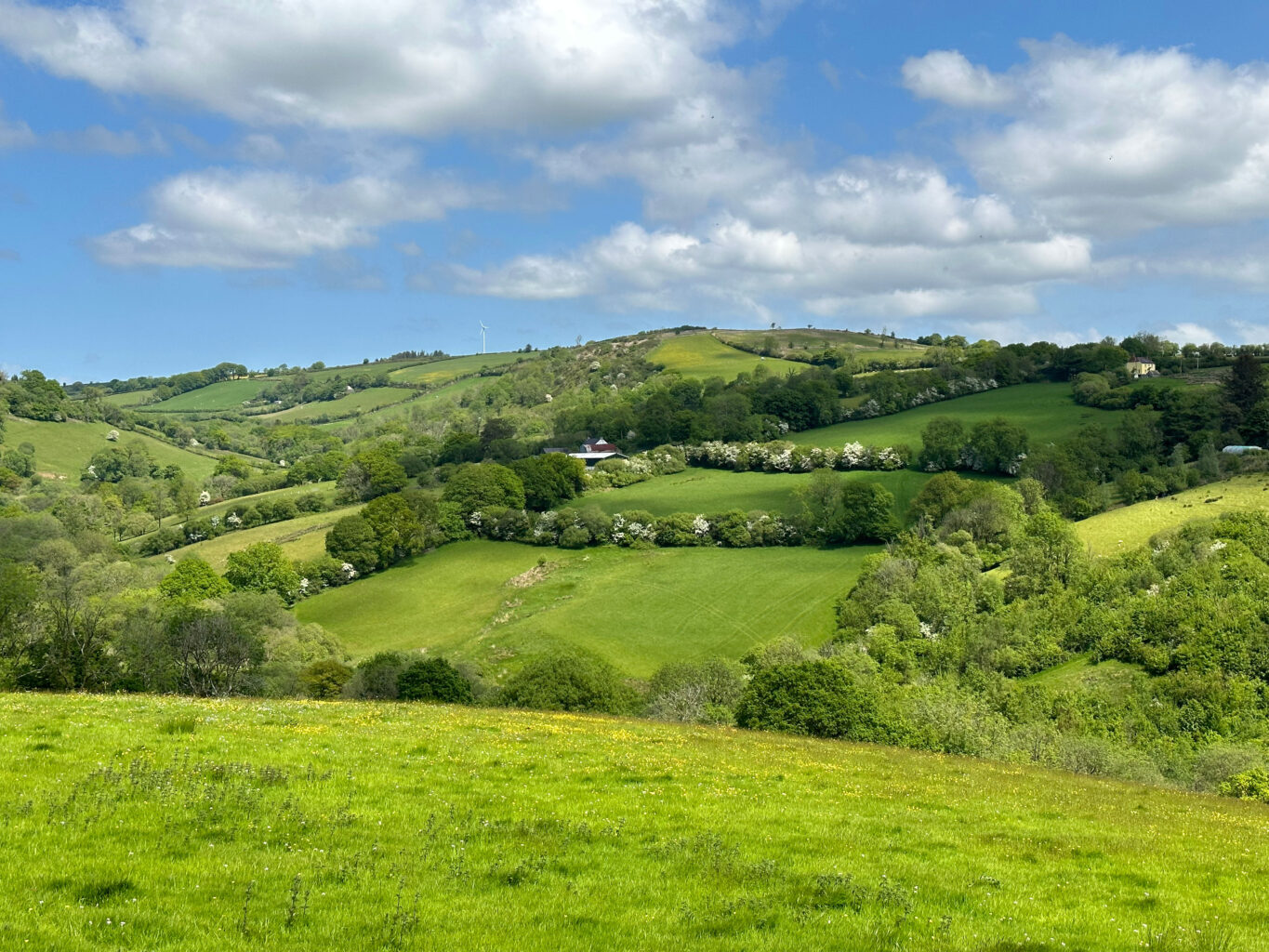
The chair is made from timber I source myself from around my home village of Llanybri in Wales. Small-diameter ash logs are split by hand and are used to construct the legs, stretchers and sticks. The three-piece ash arm bow is made from naturally curved ash from the hedgerows, which is cut in winter and seasoned for a few years before use. I follow the tradition that the armbow dictates the shape of the seat, which in turn makes Welsh chairs visually and uniquely distinctive from other chair forms. The two-piece elm seat is jointed with loose tenons and the oak pegs which are used in this construction technique form a pattern on the seat which is visible when a raking light casts across it. The chair is stained with a black dye and topcoated with a linseed oil finish. The open grain of the timbers is clearly visible through the matte/satin finish.
Typically, Chris has a buyer for the chairs he brings over. But for this one we decided to offer it up in a silent auction here on our blog. All the proceeds go to Chris. (We never take a cut when we sell other people’s work.)
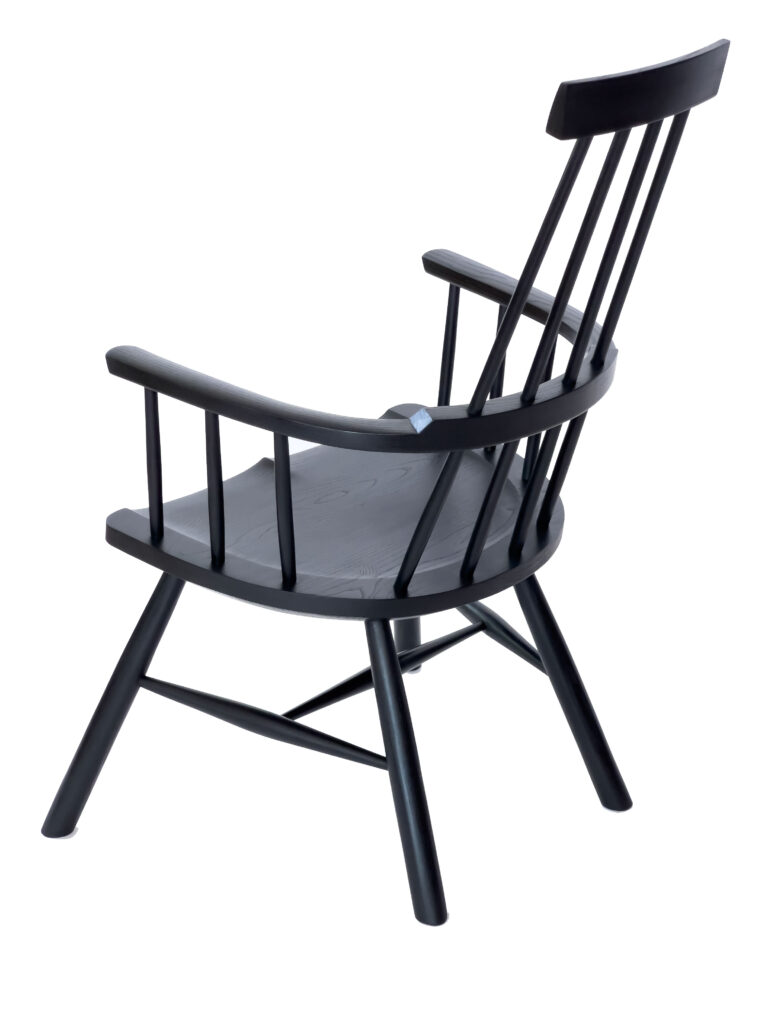
Purchasing the Chair
This chair is being sold via silent auction. (I’m sorry but the chair cannot be shipped outside the U.S.) If you wish to buy the chair, send an email to lapdrawing@lostartpress.com before 3 p.m. (Eastern) on Thursday, June 15. In the email please use the subject line “Welsh Chair Sale” and include your:
- Your bid
- First name and last name
- U.S. shipping address
- Daytime phone number (this is for the trucking quote only)
This chair has a reserve. The sale price will include shipping to anywhere in the lower 48 states. Or you are welcome to pick it up in our storefront here in Covington, Ky.
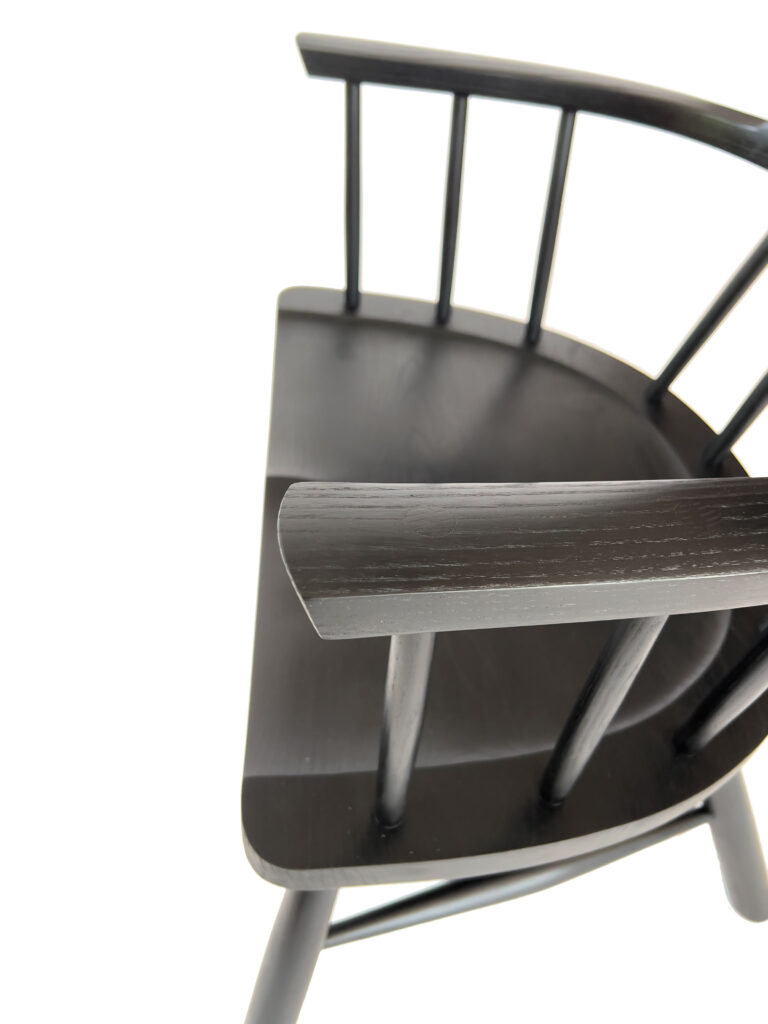