
We just got our first working prototype of a kit that lets you build an Anarchist’s Square with less than an hour of work.
I’ve made dozens of these squares since “The Anarchist’s Tool Chest” came out. The square was originally a student project. Tool monger Patrick Leach said he has found many of them in the U.K. during his career, and he suspects it was part of a curriculum at a school.
When I teach students to make the square in a class, it takes two days. There are a lot of lessons involved, from sawing accurate half-laps to truing long edges to perfection to sawing perfect little beads.
But thanks to this kit, you don’t have to do all that.
The kit parts are made from 1/2”-thick Baltic birch. All the joinery and decorative details are already cut. All you have to do is a little cleanup with sandpaper then glue the parts together. The prototype turned out dead square with little effort.
Then you can finish up the square however you like. You can leave it unfinished or tart it up with paint, oil or a film finish. Because it’s plywood, it’s unlikely to ever go out of square.
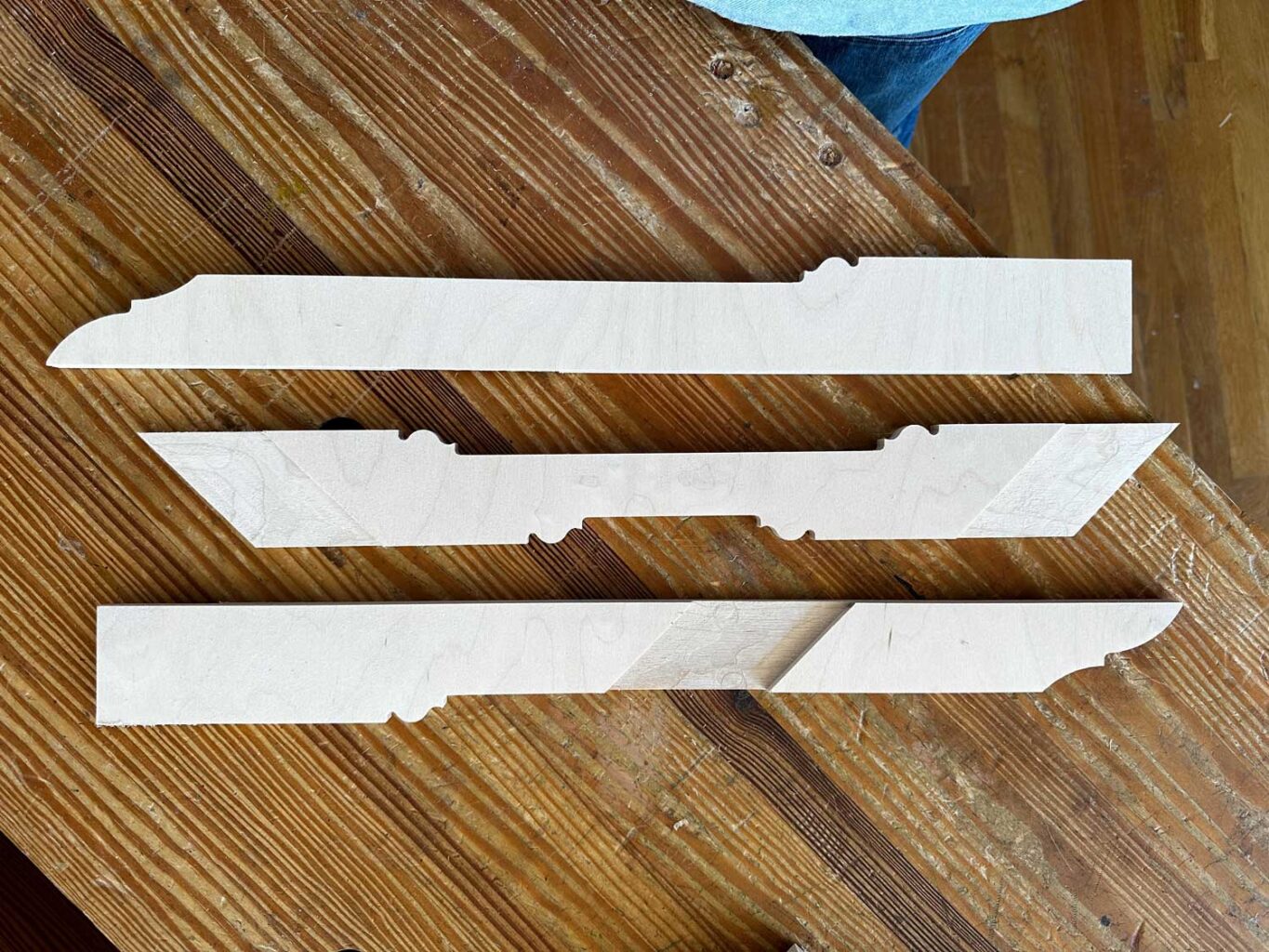
I am greatly looking forward to getting some of these kits in house because I don’t have any more of these squares. I sold most of them and gave away my personal one – the one I built for the book – to Anne Briggs (aka Anne of All Trades) as a gift.
I miss having some of the squares around and using them. I had some with accessory fences that made them even more useful. So I’m sure I’ll shoot some video of making, using and modifying the square.
When? I don’t know. Soon, I hope. How much? Again, I don’t know for sure. Less than $50 I hope.
They’ll be made in Ohio and shipped out by Mark and Gabe.
— Christopher Schwarz