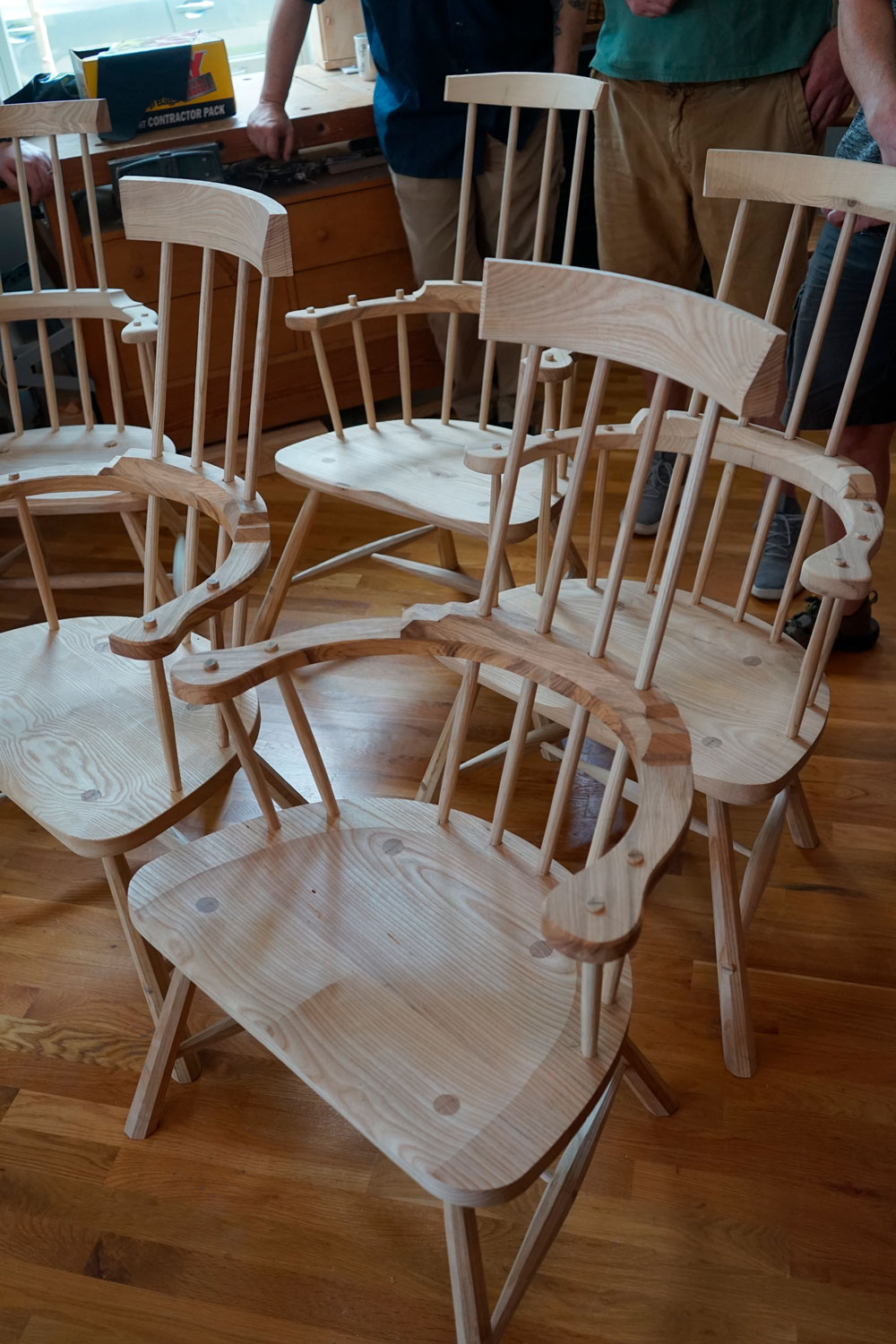
Today I dropped Chris Williams off at the airport for his journey home to Wales, and I cannot believe how quickly the last three weeks have rushed by.
In addition to Chris teaching two classes on making Welsh stick chairs, Chris and I spent a lot of time working on his forthcoming book, “The Life & Work of John Brown.” The book has – like all books – taken some hard left turns as it germinated below the soil. And Chris and I have spent many evenings sorting out the important chapters.
But the biggest discussion has been over whether or not to include detailed plans of a chair in the book.
After much thought, Chris concluded that adding plans to the book would go against the spirit of how John Brown made chairs during his life (and how Chris makes chairs now). John Brown and Chris contend that no two Welsh stick chairs should ever be identical. Instead, each chair should be built to suit the materials at hand, the skills of the maker and the tools available.
Don’t worry. You’ll be able to build a Welsh stick chair after reading Chris’s book. But your chair will start from a personal place instead of from an established pattern.
That’s how Chris built his first chair. He’d read John Brown’s “Welsh Stick Chairs,” and then figured out his own way by observing the chairs in John Brown’s book.
It’s not an easy way to make a chair. But it is satisfying. I built my first chair in a class, but my second chair went in a different direction than the first one. Even today I don’t expect my chairs to end up how I envision them in my mind or on paper. Each has a life of its own.
Chris tries to imbue his classes with the same spirit. His students were encouraged to go their own direction with their chairs. There are, of course, limits to what you can do during five days. But I was impressed by how some students took this idea to heart.
All of the chairs in the classes had four back sticks, but that’s where the similarities ended.
In the real world, Welsh stick chairs have enormous variations – in the number of back sticks (three sticks up to 11 or so). The shape of the seat (circle, rectangle, D-shaped etc). The construction of the arm. The undercarriage (if there even is an undercarriage). The comb. Plus the length of all the long stocks and short sticks, and the rake and splay of every component.
So when you look at Chris’s chair, or mine, or one of the thousands being built, know that your chair shouldn’t look like that. Exactly. Or at all. But it should look Welsh. And that is something you have to develop an eye for and will definitely be covered in Chris’s book.
— Christopher Schwarz
P.S. When will this book be out? Chris plans to have the writing done this fall. I’ll design it in November and December. And we hope it will be in your hands in February or March 2020.
Like this:
Like Loading...