Editor’s note: The third edition of “Cut & Dried” should arrive in February. You can sign up to be notified when it arrives here. In this post, author Richard Jones explains his update to Chapter 6.
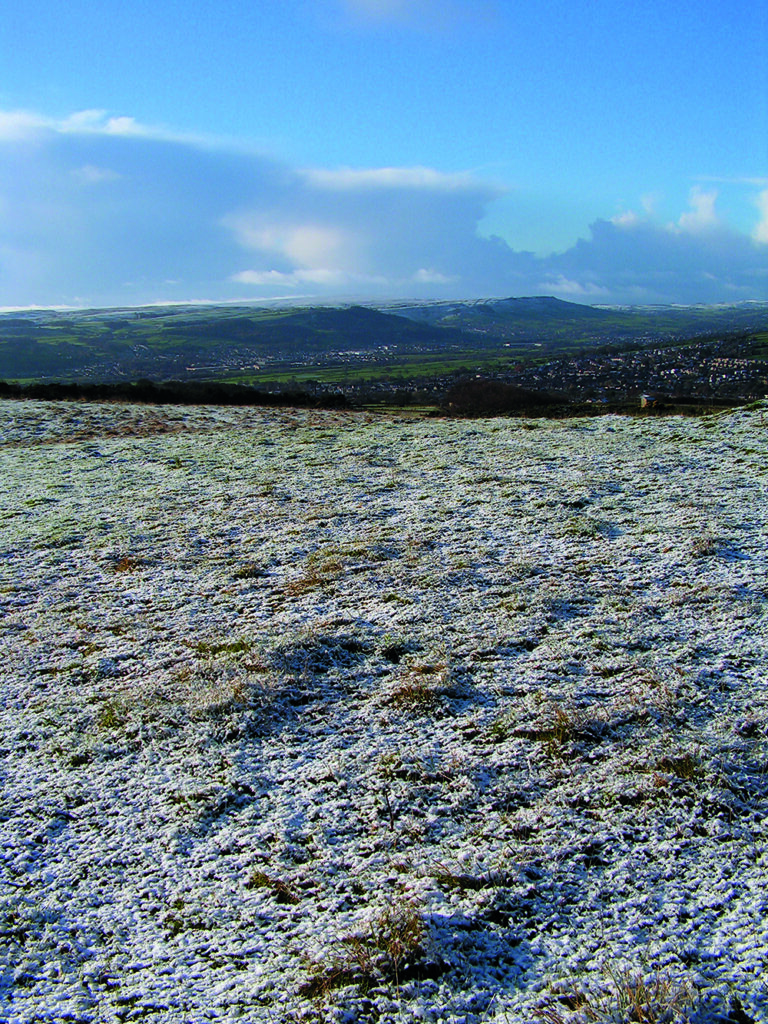
In 2021, I decided I ought to update “Cut & Dried,” and the third reprint of it at the end of 2024 was a good opportunity to do so. For a long time I had been aware of two ways to determine wood moisture content, i.e., the “dry basis” (db) and the “wet basis” (wb). In Section 6.6 Measuring Wood Moisture Content in the already printed book, I emphasised we woodworkers use only wood’s dry weight as the base weight to assess wood moisture content. This dry basis methodology wasn’t actually named in the book and nor was the alternative wet basis methodology named or described except the wet basis was hinted at in an exchange I had with a furniture student at the end of page 76 and into page 77.
However, since the last printing of “Cut & Dried” in 2019, things have evolved and environmental issues are ever more pressing. The drive is on to reduce carbon emissions, reduce particulates and pollutants etc. I am not here to proselytise on these issues but burning biomass fuel in the form of logs, wood chips, pellets etc. is one potential source of particulates and pollution. Many people and organisations around the world burn biomass fuel for heating homes, cooking, industrial boilers etc., and burning wet fuel is both inefficient and pollutant. The U.K. government, for example, created legislation to regulate the supply of biomass fuel, including setting the maximum moisture content levels for biomass fuel suppliers, and putting in place organisations to verify that such suppliers meet required government standards.
Crucially the authorised method of determining wood moisture content in the biomass fuel sector is the wet basis. It’s the case that the biomass fuel sector might be considered peripheral to us woodworkers with our focus on making things out of wood, and where we want to know its moisture content, but the biomass fuel sector, like use, require felled trees, so there is an environmental impact which deserves some discussion in “Cut & Dried.”
To illustrate the difference between dry basis and wet basis calculations for wood moisture content I’m including some text from the latest iteration of section 6.6 of “Cut & Dried,” but modified slightly for this blog post’s purposes.
A learner approached me with the following figures for a piece of wood both before and after oven-drying:
- Wet Weight = 20 grammes
- Oven-Dry Weight = 15 grammes
This learner questioned the calculated moisture content result. Using the formula already provided she calculated: ((20 – 15) / 15) X 100 = 33.3%MCdb. This learner, in trying to grasp the basis of the calculation, changed the formula to calculate thus: ((WW – ODW) / WW) X 100 giving the sum ((20 – 15) / 20) X 100 = 25%wb. We discussed the different results, i.e., 33.3 percent and 25 percent, and it is easy to mentally visualise a 5 gramme weight loss is a quarter of the 20 gramme wet weight of the sample, i.e., 25 percent. Similarly, it’s quickly apparent that a 5 gramme weight gain is one third (33.3 percent) of 15 grammes, the sample’s oven-dry weight. As soon as the learner understood the base line for the dry basis calculation is the dry weight of the wood, not the pre-dried wet weight, all was clear to her. She was then able to comprehend how, using the dry basis methodology of assessing wood moisture content wood MC figures such as 100 percent or greater were possible, e.g., wet weight, 200 grammes and oven-dry weight of 100 grammes.
This learner’s confusion had led her to unknowingly stumble upon the methodology for assessing wood moisture content referred to earlier, i.e., the “wet basis” (Forestry Commission, 2011). To calculate the wood moisture content percentage on the wet basis (wb) the formula given by The Forestry Commission (2011, p5) is:
“The MCwb = (the weight of water in a sample/ total initial weight of the sample) X 100.” MCwb as indicated earlier, means Moisture Content Wet Basis. Results are expressed as a percentage.
Further reading, if so desired, can be found at the following links:
Forestry Commission: Testing moisture content (simple method)
— Richard Jones