Order in the House!
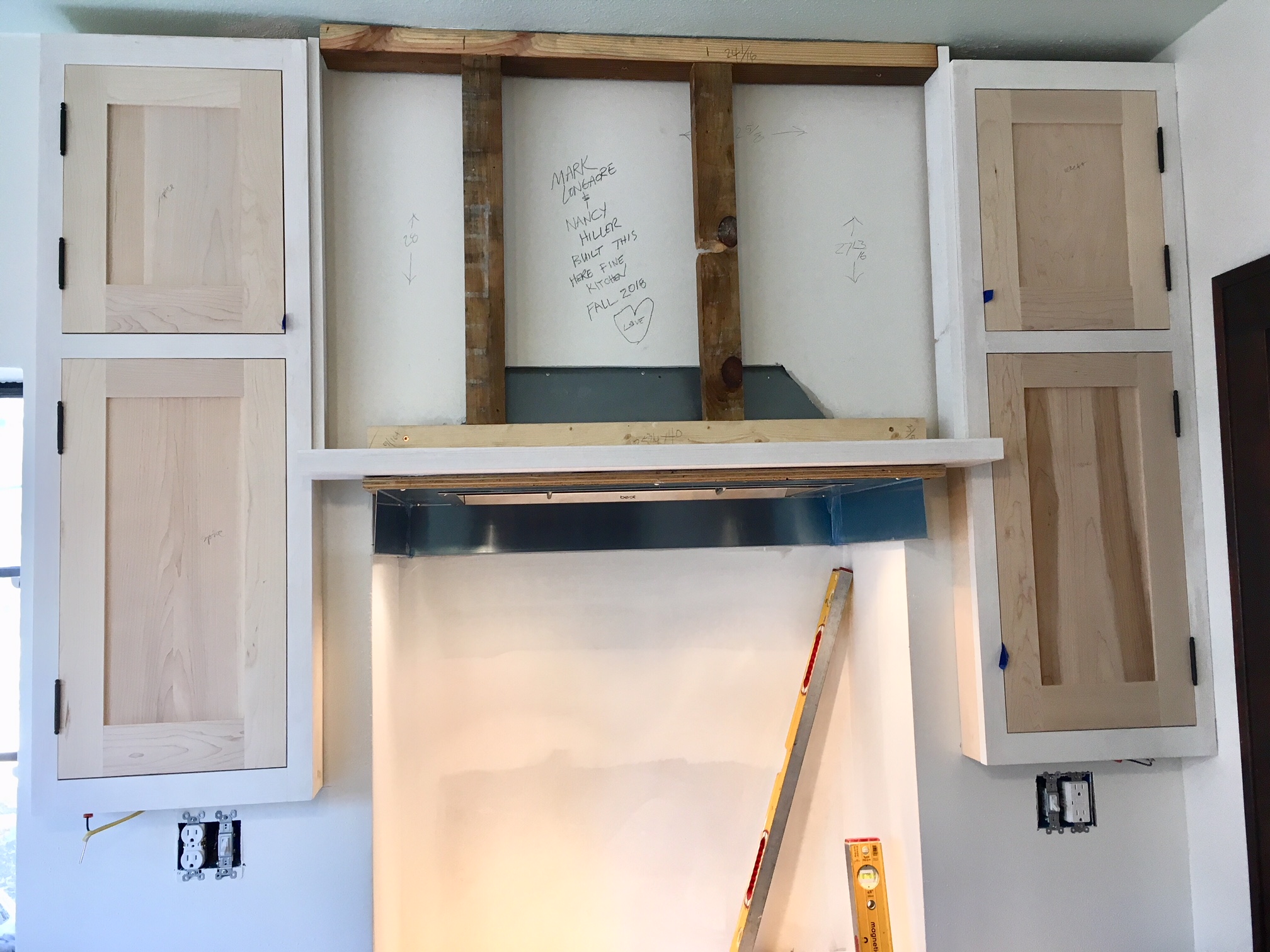
As a woodworker trained in furniture making, I’ve designed and built many a kitchen over the past 39 years. Blame the first guy who employed me in 1980; he taught me a lot about business and design, but one of the most valuable gifts he gave me was an appreciation of making kitchens.
Until I started my own business in 1995, my work for kitchens never really took me into the rooms my work would furnish. In almost every case, I was working to plans drawn (often on the backs of envelopes) by others. After I’d built the cabinets to spec, someone picked them up and drove them away for installation. Beyond a dim awareness that the scribe rails I built into face frames would somehow allow the cabinets to be fitted to the walls around them, I had no inkling of what transpired at the job site.
Things are different when you’re the one responsible not only for building the cabinets, but designing the room and putting the whole thing together. You soon realize that there’s an order in which the different pieces of the puzzle should fall into place.
Writing a book about kitchens is a daunting task. (The book related to this post is planned for publication in the summer of 2020.) We all know that the hardest subjects to write about are those with which you’re most familiar. Where to start? With writing, as with building a kitchen from scratch (or remodeling one for people who will be living in the house while the center of their home undergoes an inevitably disruptive transformation), a systematic approach helps ensure a high-quality result.
So here’s a quick list of the order in which such work is typically done.
1 Demolition
2 Insulate exterior walls as appropriate. If you have gutted the room to the studs, joists and rafters, shim or plane down framing parts to make ceiling, walls and floor level and plumb. Add blocking for cabinet (and other) installation.
3 Rough plumbing (sink supplies and drainage, gas for stove) and electrical wiring (lighting, appliances, dishwasher, fridge, stove, undercabinet lighting, switches, etc.)
4 Patch or replace ceiling, walls and subfloor as necessary. Tape and finish joints.
5 Prime and paint at least one coat of color
6 Floor finish (lay tile or sheet flooring; sand wood floor and finish)
7 Install cabinets. (With the overwhelming majority of contractors, this means the whole shebang. Numbers 9 and 10 below aren’t relevant.)
8 Measure and make templates for counters
9 Fit doors and drawers
10 Remove doors and drawers for finishing in shop
11 Install counters
12 Install backsplash or tile
13 Install sink and faucet
14 Finish electrical—install the light fixtures, disposal, appliances, switches, etc.
15 Final painting.
Sure, you can mess around with the order of work, depending on circumstances and materials. But in general this is a reliable guide.
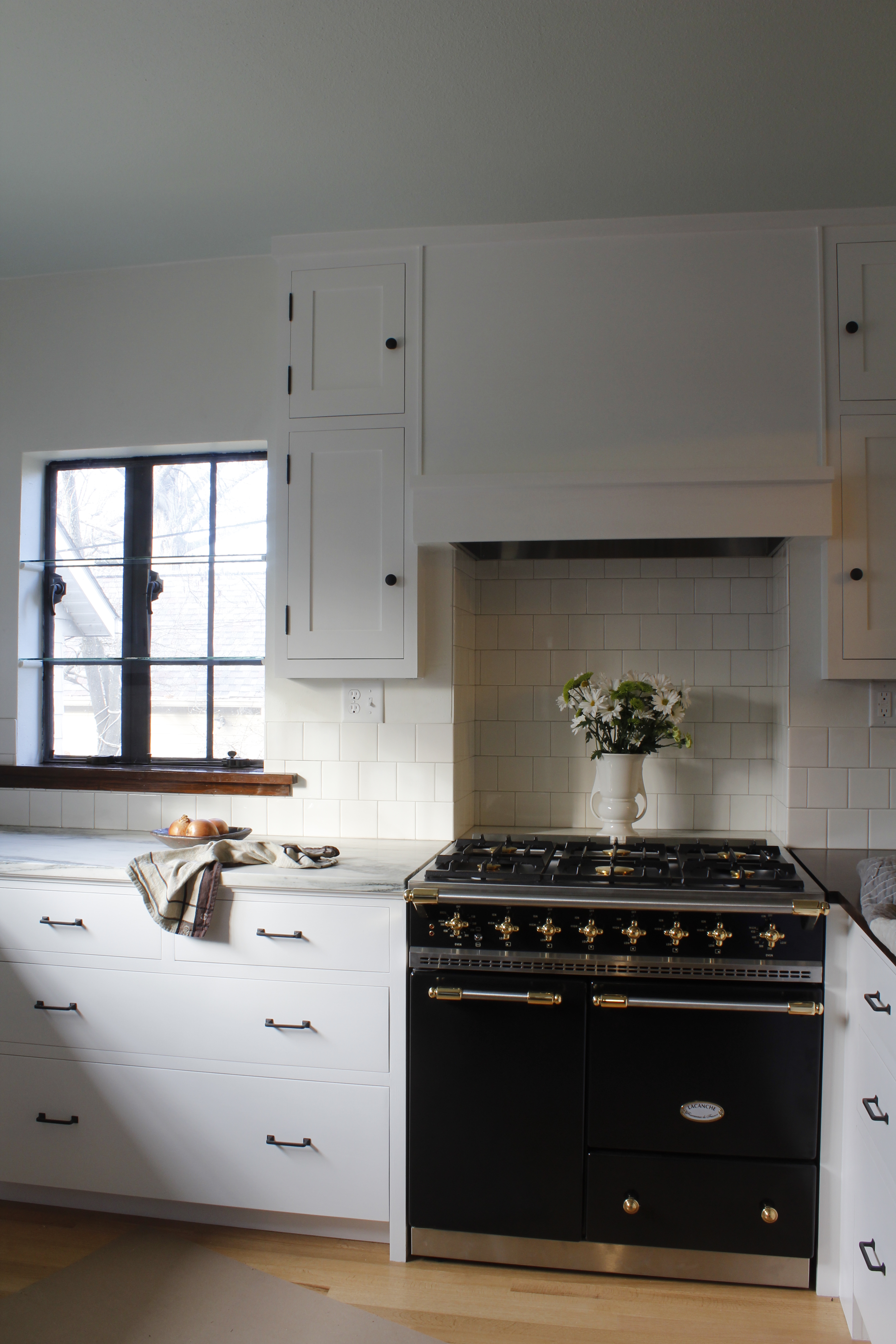
Nancy Hiller, author of Making Things Work
Like this:
Like Loading...