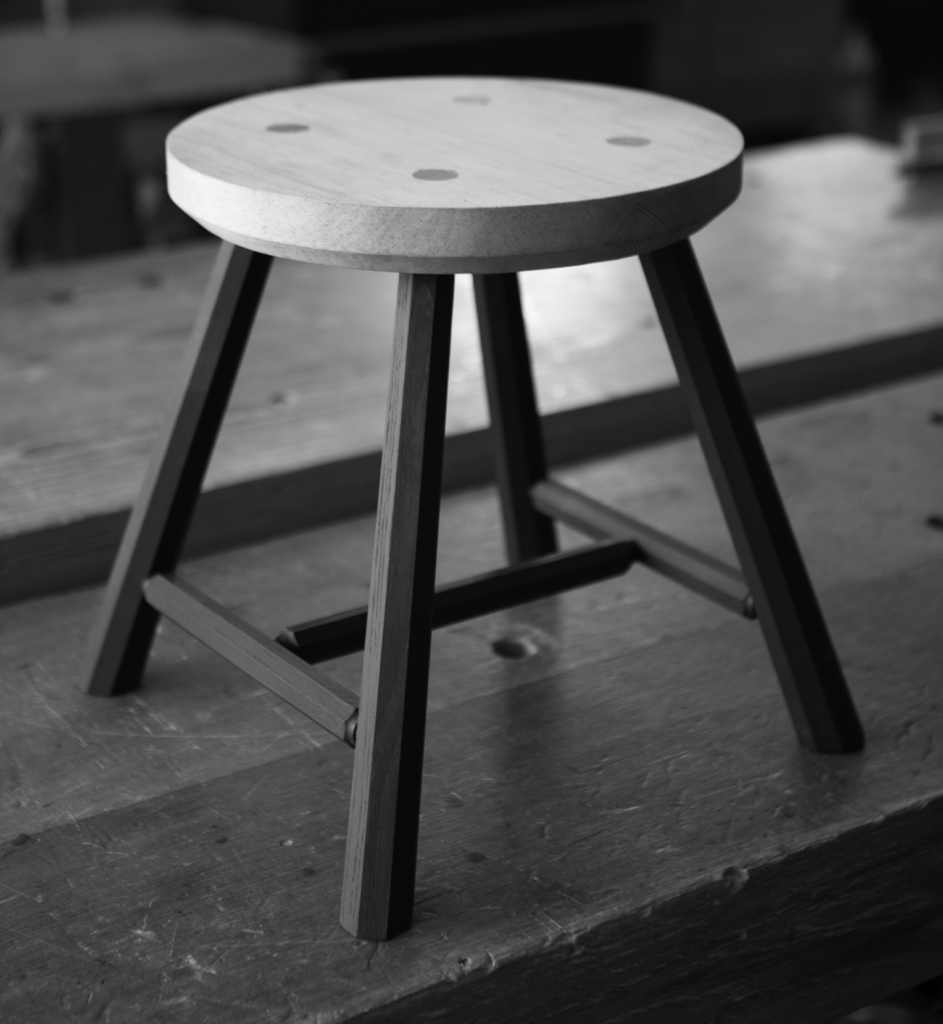
The following is excerpted from “The Anarchist’s Design Book,” by Christopher Schwarz, an exploration of furniture forms that have persisted outside of the high styles that dominate every museum exhibit, scholarly text and woodworking magazine of the last 200 years.
There are historic furniture forms out there that have been around for almost 1,000 years that don’t get written about much. They are simple to make. They have clean lines. And they can be shockingly modern.
This book explores 18 of these forms – a bed, dining tables, chairs, chests, desks, shelving, stools – and offers a deep exploration into the two construction techniques (staked and boarded) used to make these pieces that have been forgotten, neglected or rejected.
Here’s a simple stool design that represents a lot of false starts, research and prototyping. It’s not perfect, but it is a nice, stout stool. The stool is based on 18th-century low stools from American homes. This stool is also an excellent introduction into building the seat and undercarriage of a full-blown chair.
This stool has a pine seat and hardwood legs – ash in this case. The seat is 13″ in diameter and the legs hold the seat about 16″ off the ground – a good height for a low stool. The H-stretcher is a bit of overkill. But I think you should include it. It will teach you how to add stretchers to any of the chairs in this book – or from other people’s books. So let’s go.
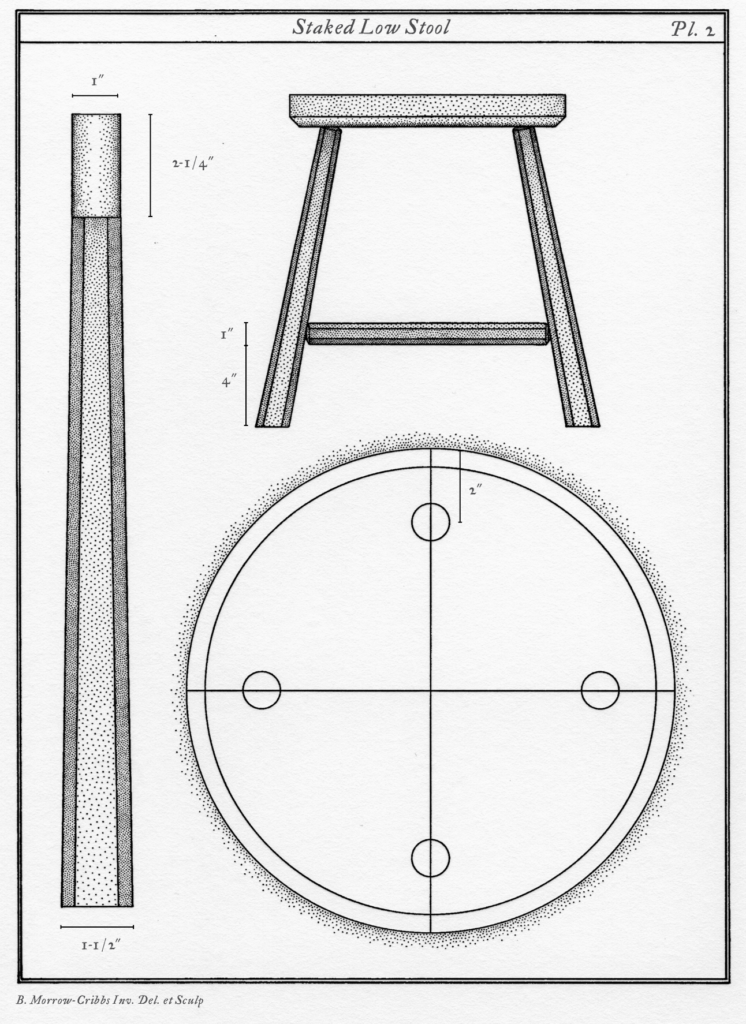
Make the Seat
The seat is a softwood that is about 1-1/2″ to 1-5/8″ thick. You can glue up the seat from two bits of wood (that’s what I did) and put the seam in the dead center of the seat. Keep the leg joints away from this seam; you don’t want the legs levering the seat apart. (Yes, a long-grain-to-long-grain joint is stronger than the wood itself in a perfect world. But that is not where we live.)
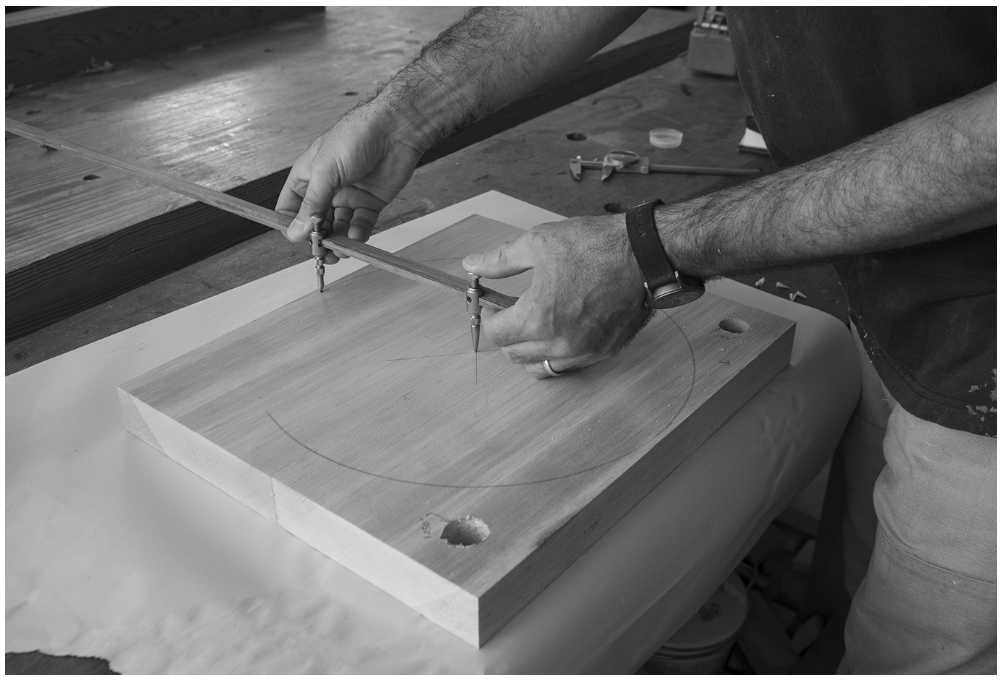
With the seat blank glued up, use a compass or trammel points to lay out the 13″-diameter seat.
Cut the seat to shape. Then cut a 1/2″ x 1/2″ bevel on its underside. This bevel lightens the look (and the weight) of the stool. You can do this on the band saw or do it with a block plane or spokeshave.
Now you can mark out the location of the joints. Here’s the easy way. On the underside of the seat, draw a line through the centerpoint of the circle. Make this line parallel or perpendicular to the glue seam in the seat (if you have a seam).
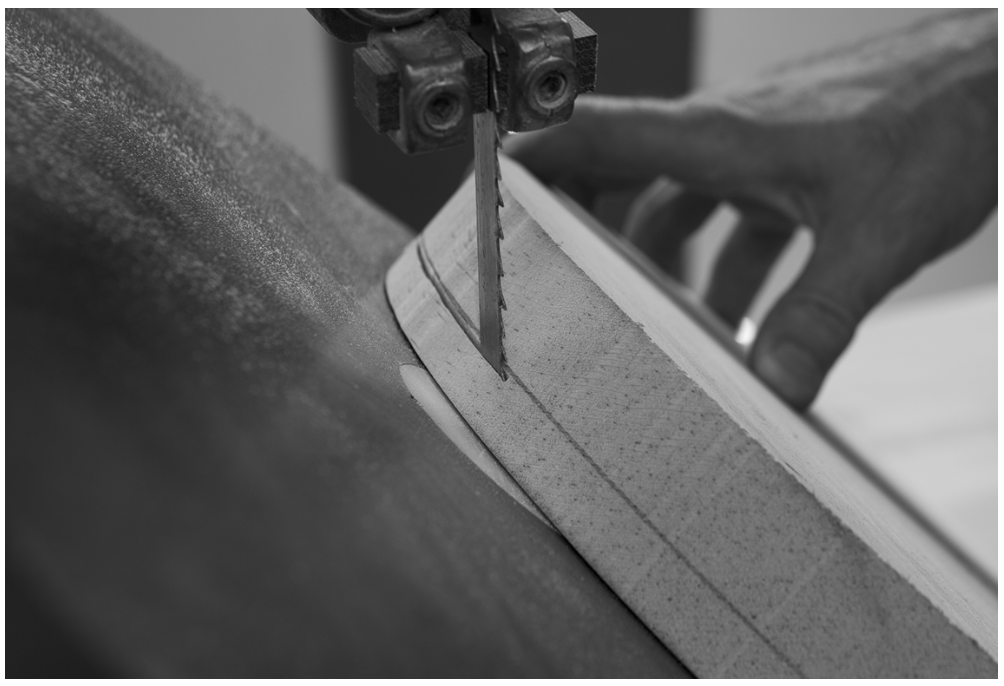
Place a protractor on your pencil line and mark the seat at 45° on both the left and right sides of 90°. Connect the marks with the centerpoint and you will have a perfect “X” on the underside.
Now take a ruler and mark out the location of the four leg mortises 1-1/2″ in from the edge of the seat’s bevel. (It’s all shown in the photo [below] if you look closely.)
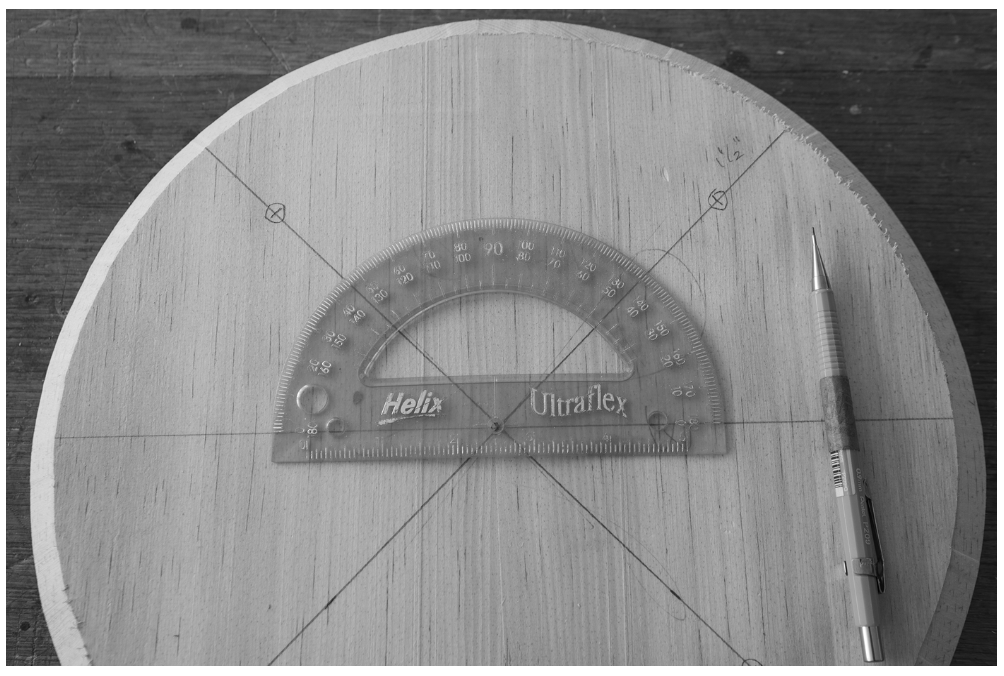
Make the Legs
The legs are 1-1/2″ x 1-1/2″ x 18″ and are made from a dead-straight hardwood such as oak, maple, ash or hickory. Knock off the edges until the legs are octagons. Then taper the legs so they taper to 1″ at the top.
For this project, I decided to use cylindrical tenons. While I prefer tapered tenons, cylindrical tenons are far more common in the historical record and are easier to make, especially if you own a lathe.
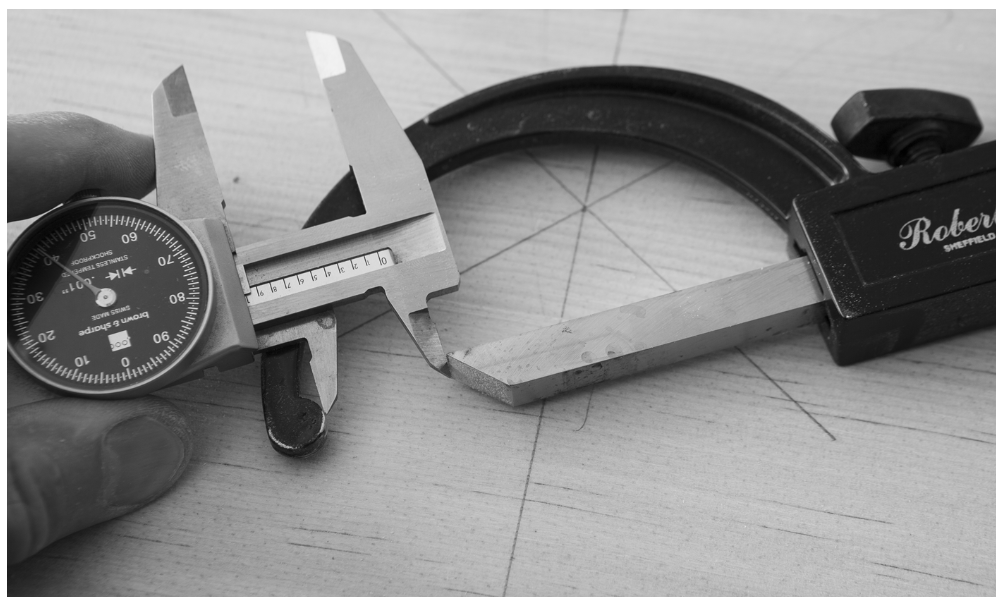
The tenons for this stool are 1″ in diameter and 2-1/4″ long. Turning them on the lathe is straightforward. If you want your tenons to be dead-on accurate, I recommend you purchase a bedan tool with a sizing attachment. A bedan tool is basically a wide parting tool with its sides relieved (like a traditional mortise chisel) to allow it to maneuver in the cut without binding. The sizing tool is an attachment that clamps to the tool and allows you to set the diameter of the cut.
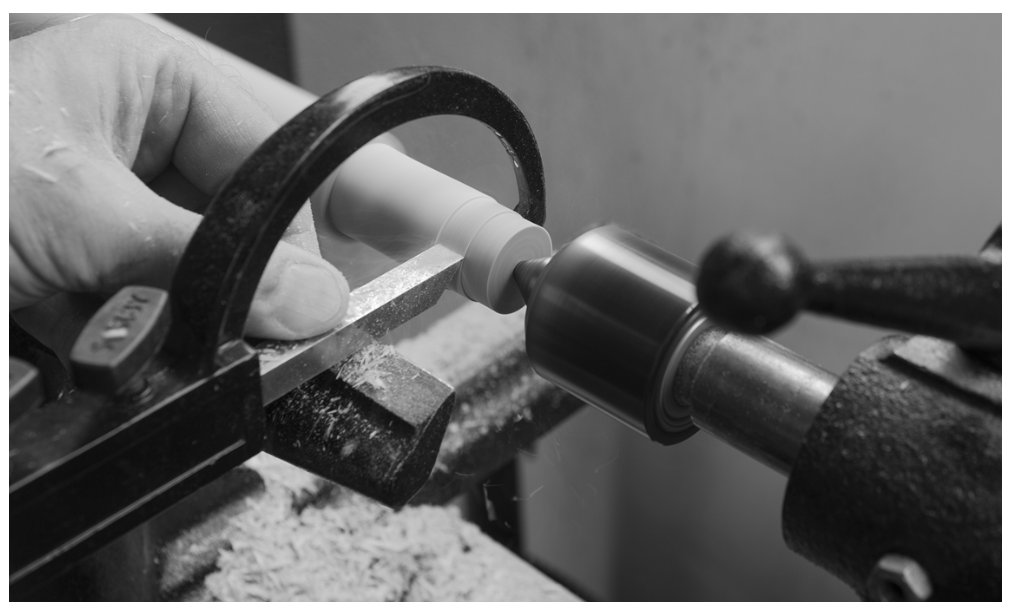
To use the bedan tool and sizing attachment, first drill a test mortise and gauge the exact diameter of the bit that will drill your mortises. Set a dial caliper to that measurement (lock it) and use the caliper to set the bedan tool and its sizing attachment.
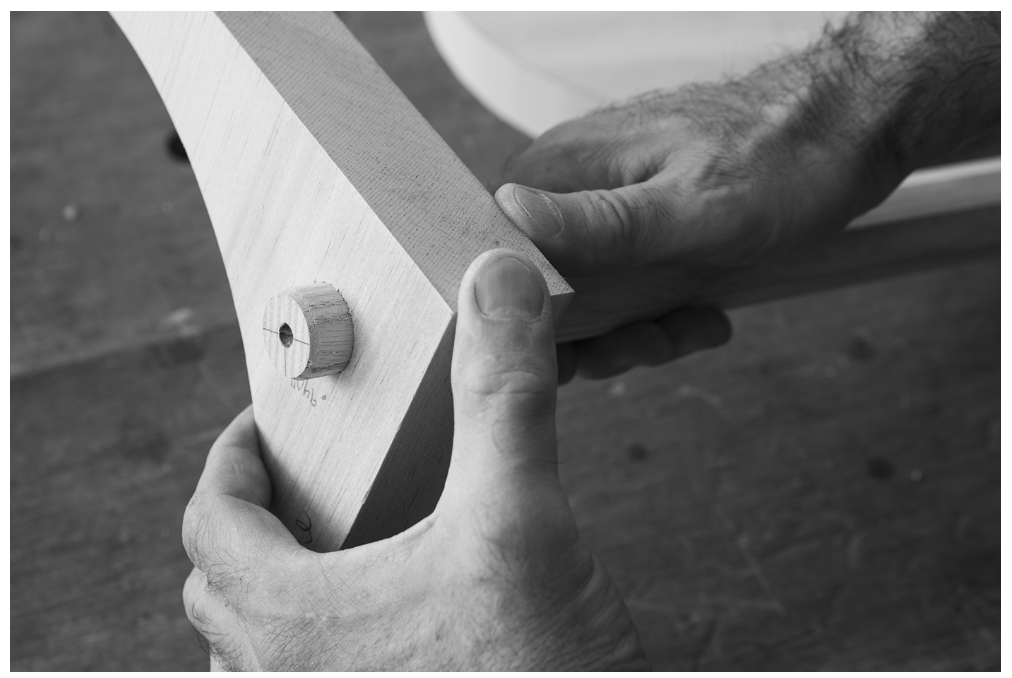
Bore the Mortises
The leg mortises are bored at an 21° resultant angle. The sightline is 0° and runs directly into the centerpoint of the seat. Set a sliding bevel to 21° and tape it to the sightline. Clamp a backing board below the seat to reduce (but probably not eliminate) any splintering.
With this stool, I’m using a 24 mm bit from WoodOwl that is supposed to leave a clean exit hole without splintering. It does a pretty good job, though no bit is perfect (hence my backing board). These particular bits work best in an electric drill.
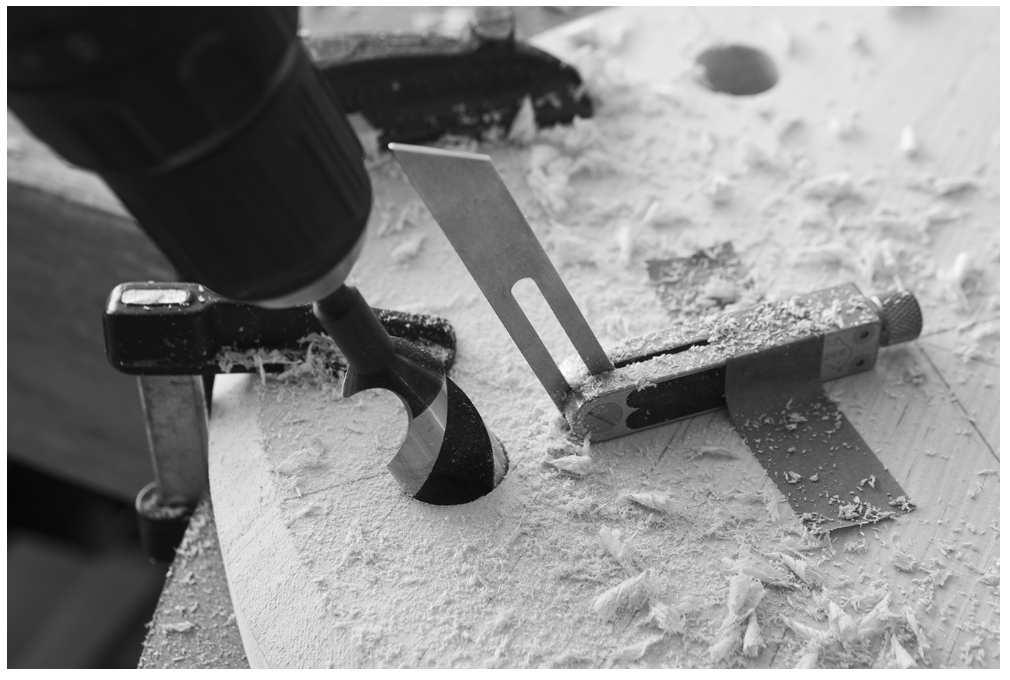
Drill the four mortises. Then put the legs into their mortises and have a gander at how accurate you were.
Rotate the legs in their mortises and orient them so their attractive surfaces face out. Then meaningfully mark the legs and the seat so you can get the legs back into this ideal arrangement.
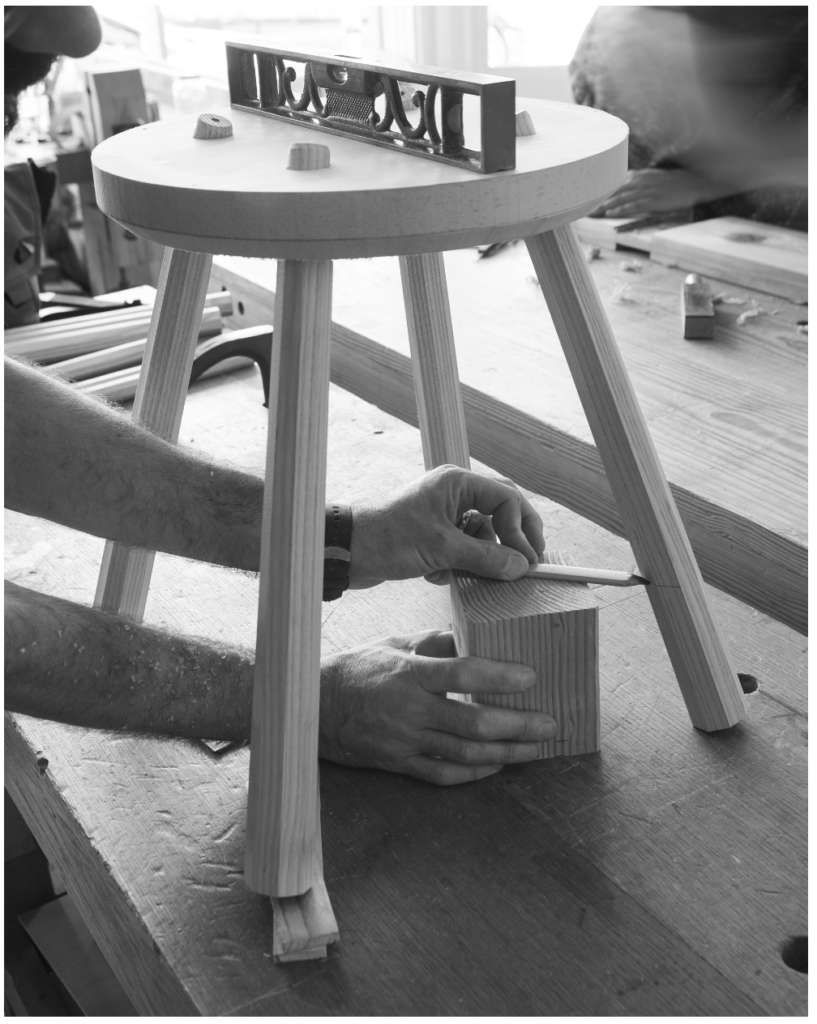
Now it’s time to bore the mortises for the side stretchers. These are positioned about 4″ to 4-1/2″ up from the floor. Here’s how to mark them out. First, level the stool like you are preparing to cut the legs to length. Shim the feet until the seat is level all around. Then cut a 4×4 block of wood to 4-1/2″ long and place it on the bench. Fetch the half-pencil (it’s a pencil planed to half its thickness). Mark the location of the mortises for the side stretchers on the legs.
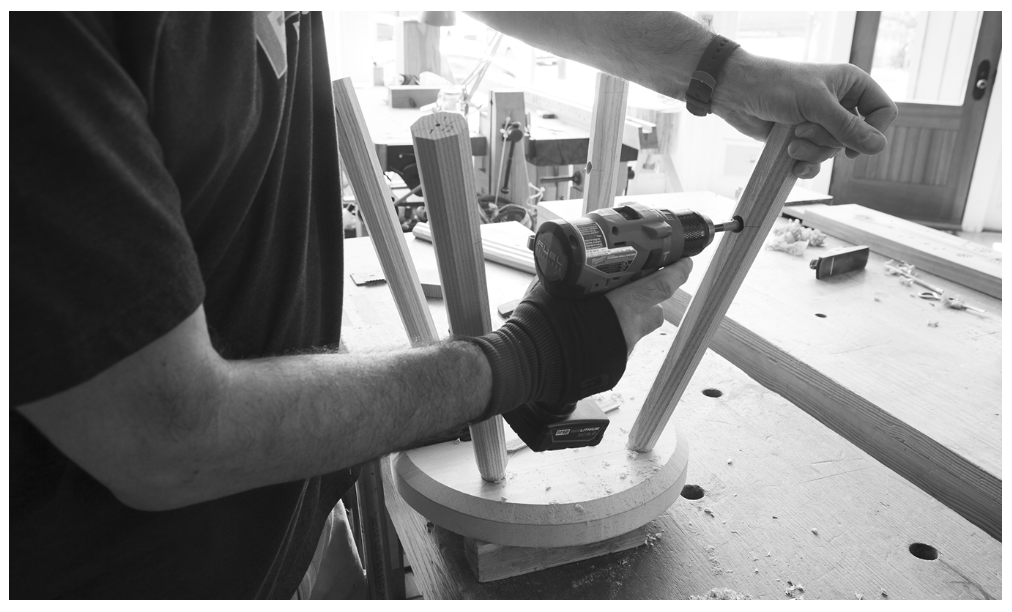
To bore the mortises, flip the chair upside down so the seat is on the benchtop. Place a couple sticks between the seat and benchtop to let the tenons poke through the seat. Then take an awl and mark the centerpoint of each mortise on each leg. I do this by eye. Measuring always seems to make it worse.

Chuck a 5/8″ Forstner bit into a cordless drill. I drill the 7/8″-deep mortises in the legs entirely freehand, using the seat and the marks on the legs as a guide. Rotate the leg in its mortise so you can get the drill and the bit in position in line with the leg. The drill and bit should be aligned with the mortise on the opposite leg. The photo [“On the tip of disaster”] shows how this works.
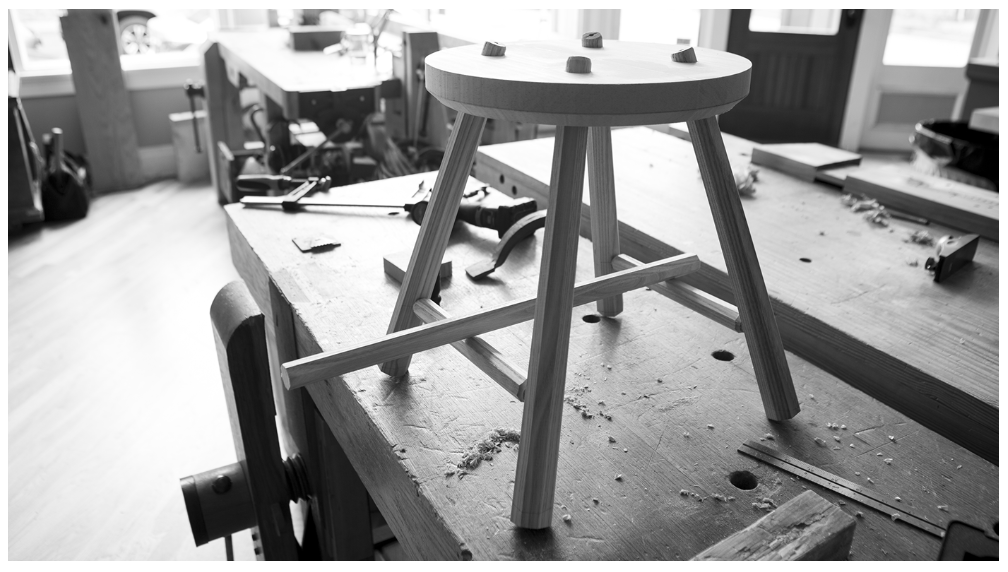
If you lack confidence because this is your first rodeo, have a spotter give you some directions. They should be able to tell you if your drill bit is in line with both mortise locations in the legs. Drill the blind mortises, stopping before the bit explodes out the backside.

Make the Stretchers
The stretchers are 1″ x 1″ material that has been planed octagonal. After preparing the overlong stock for the stretchers, you need to determine how long they should be for your stool. To do this, fetch two skinny scraps. Pinch them together and press the ends into the bottoms of the mortises. Make a pencil mark across the two scraps. Remove them from the mortises. Reassemble them with the marks aligned. Measure the overall length, and that’s the finished length of the stretcher.
Do this for both stretchers. Mine were slightly different lengths. If you are cutting the tenons on the lathe, then add 2″ to the calculated length to give you some room to work without running your tools into the headstock and tailstock of the machine. (I wrote this sentence to remind myself to do this next time.)
Cut the 5/8″-diameter tenons on the side stretchers using the same techniques outlined for the legs. Yup to the bedan tool and the sizing attachment. After turning the tenons, saw the stretchers to their final length and install them in their mortises.
The medial stretcher is easy. Mark the centerpoint on each side stretcher. Use the same 5/8″ Forstner bit to drill a 5/8″-deep mortise in each side stretcher. Once again, I drill these freehand. Keep the bit 90° to the stretcher and parallel to one of the facets of the octagonal stretcher.
You know what to do next. Get the skinny scraps and use them to determine the finished length of the medial stretcher. Cut the stretcher 2″ overlong. Turn the tenons on the ends with the bedan tool. Cut the medial stretcher to finished size and fit everything. If the stool doesn’t explode, you are ready to glue it up.
Assembly
Before you disassemble the dry-fit stool, mark where the wedges should go in the legs’ tenons. I use a Sharpie for this to avoid confusion. Disassemble all the parts and mark them up so you can assemble them in the same orientation with glue in the equation.
Kerf the legs to receive wedges. Use a band saw or a handsaw for this. You want the kerf to be of significant thickness. Make some 1″-wide wedges for the legs.
Right before assembly, clean up all the tool marks left on the legs, stretchers and seat with planes and spokeshaves. This is quick work with sharp tools.
Here is the sequence for assembly. Learn this and you’ll be ready for a full-on chair in your future.
Glue the medial stretcher to the side stretchers. Twist the parts until the assembly sits flat.
Put glue in the mortises in the legs. Wipe off any excess and put the stretchers’ tenons into the legs in the mortises. This will be an ungainly thing, like a baby goat. Rotate the legs until the assembly is stable. Set it on the bench.
Paint the interior of the mortises in the seat with glue. Do not skimp or get in a hurry.
Take a deep breath.
Navigate the legs into their mortises. This might require some grabbing and bending. That’s OK as long as the seat doesn’t split. The goal is to get the tip of each tenon into its mortise.
Tap the legs down, working around the stool’s four legs until the legs are seated. Small taps are better than big ones.
Flip the assembled stool over. Paint the wedges with glue and drive them in with a hammer.
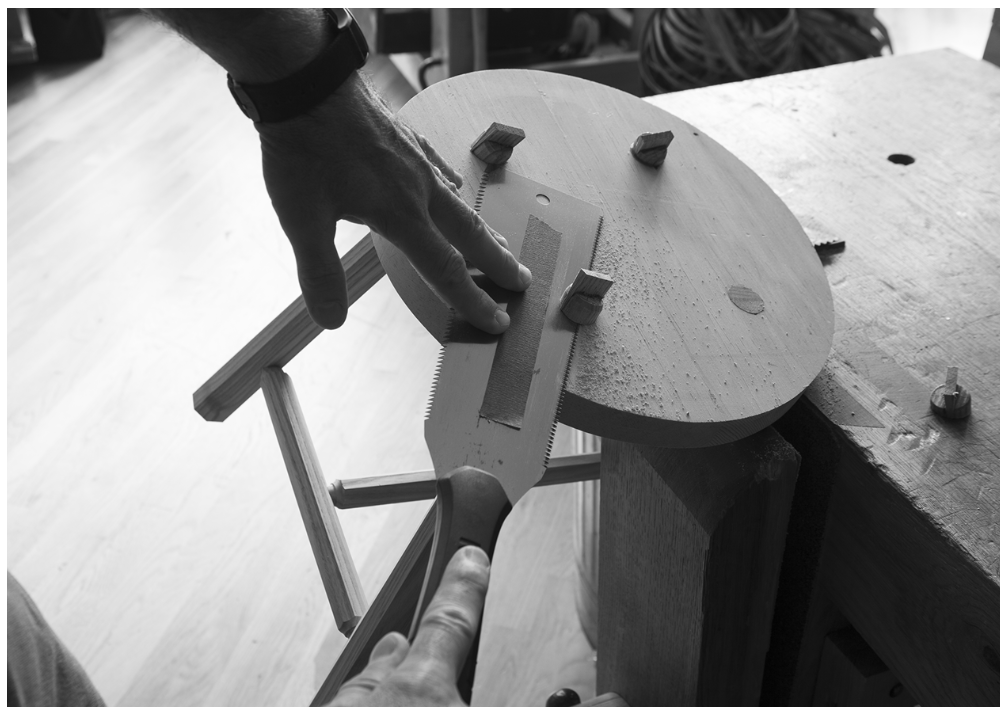
Let the glue dry overnight. The next morning, saw the tenons flush to the seat. There are (at least) 50 ways to level your tenons. When your seat is flat and not saddled, the fastest way is with a Japanese ryoba saw. We took a hardware-store saw and stoned the sides of its teeth with a diamond plate to remove the set of the teeth. It now barely scratches the seat in use.
After sawing off the tenons, plane the seat to remove any toolmarks.
Level the Feet
As shown in other sections of this book, there are lots of ways to level the feet. Picking one method depends on how your head works. Here’s how I did it for this stool. I first leveled the seat using wedges underneath the four legs.
Then I determined the final seat height (16″) and made a block of wood to guide a pencil. The height of the block represented the amount of leg I needed to saw off to achieve the final seat height. In this case, the block was about 1″ high. I placed this block on the benchtop and used a half-pencil.
Then I sawed off the legs to their finished lengths. I then chamfered the feet to prevent the feet from splintering out when the stool is dragged across a floor.
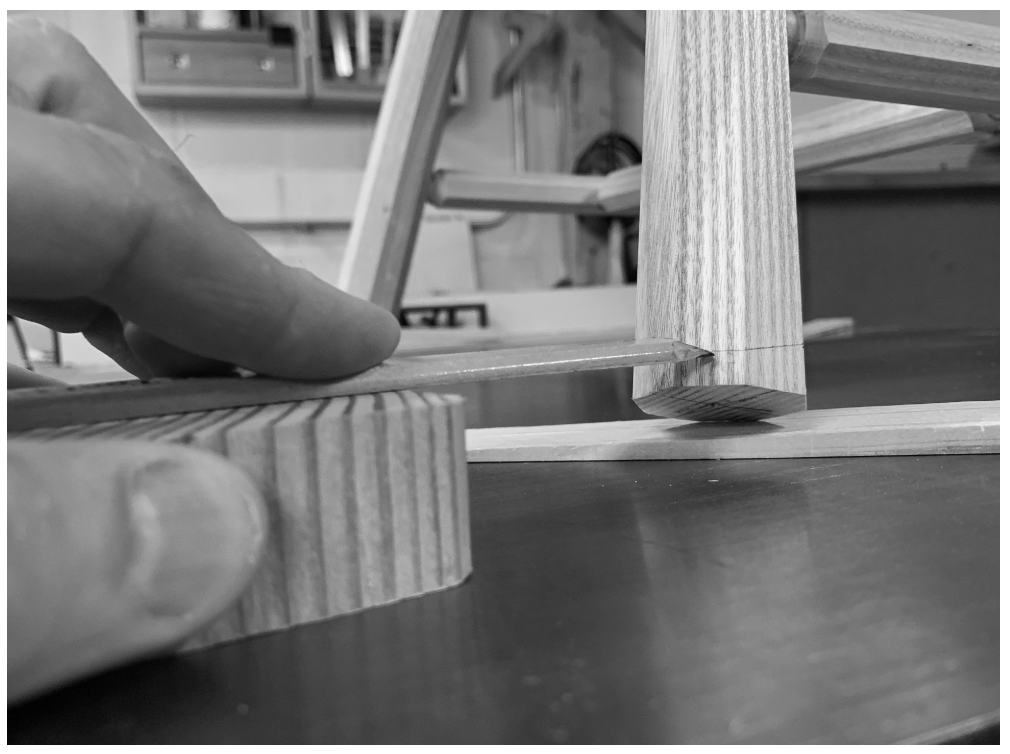
And then you are done with construction. Finishing these stools can be as simple as a coat of linseed oil and wax. Or you can dive into milk paint, soap finishes or the Wild World of Wiping Varnishes. Do your best work – you don’t want to be accused of polishing a turd. (And you thought you’d get away without a single stool joke.)
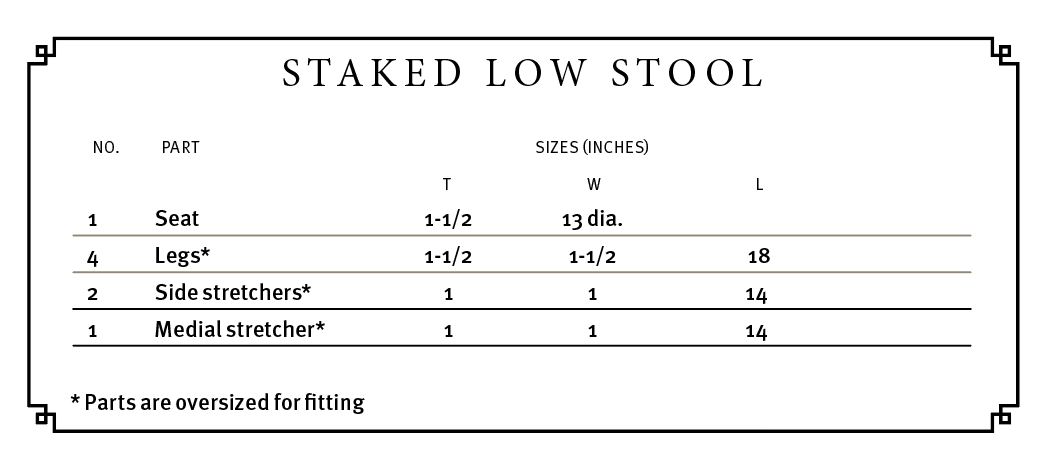